DuraTech™ by Microban® is a new antimicrobial treatment specifically developed for cotton products.
By Yihong Li and Xiuzhu Fei
Cotton is the most extensively grown non-food crop in the world,1 and makes up a significant part of the global textiles market, accounting for a revenue share of greater than 39 percent in 2021.2 Fabric manufacturers choose this organic material for its longevity, absorbency and color retention, while consumers appreciate its softness, breathability and comfort. However, the properties of cotton that make it well suited to use in clothing and home textiles also make it susceptible to the build-up of odor-causing bacteria.
Susceptibility To Microbes
Natural cotton fibers are made from cellulose with a permeable, hydrophilic structure, making them accessible to moisture, dead skin cells, food residue, airborne dust and other contaminants from the environment. The large surface areas of sheets, towels and other cotton products can easily trap environmental contaminants, making them vulnerable to colonization by a diverse community of microorganisms. Bacterial growth on cotton fabrics causes multiple undesirable outcomes — such as discoloration, odors and degradation of the fabric — worsening product performance and increasing laundering requirements. One solution to these problems is to incorporate antimicrobial technologies during the manufacturing process, enhancing the cleanliness of cotton products and extending their lifespans.
Current Antimicrobial Technologies
Antimicrobial treatments can be applied during the exhaustion or finishing step of fabric manufacturing to provide a wide range of benefits, including improved fabric durability, odor-causing bacteria prevention, a decrease in water- and energy-intensive laundry requirements, and a reduction in the quantity of chemicals required for fabric care. Cotton materials are often treated with metal-based antimicrobial agents, such as zinc- and silver-based products, some of which may pose potential environmental concerns3 or regulatory challenges. Alternatives like quaternary ammonium compounds are more sustainable than heavy metals, but may have reduced compatibility with other additives used during the cotton manufacturing process because of the presence of cationic ions within their chemical structure. In addition, some conventional cotton finishes can suffer from poor wash durability, as many antimicrobials are water-soluble, so the treatment can be easily stripped from textiles over time during washing.4
Durable Antimicrobial Finishes For Cotton
Huntersville, N.C.-based Microban International recently released a new product line — DuraTech™ by Microban® — as a durable, effective antimicrobial solution for cotton products. DuraTech uses an antimicrobial compound that is odorless and colorless. Though it is also water soluble, it can bind to cellulose via permanent covalent bonding, resulting in wash durability. The compound has been widely used in the cosmetics industry where it acts as a sustainable preservative to prevent the harmful build-up of bacteria in cosmetics and personal care products. The technology works by integrating into cotton fabric during the manufacturing process and penetrating bacteria, inhibiting the ability of microbes to reproduce.
Efficacy And Durability
The antimicrobial efficacy and wash durability of the DuraTech antimicrobial technology has undergone stringent validation following industry standard testing methodologies. These procedures involved testing multiple types of cotton — including 100-percent cotton knits for apparel, 100-percent woven cotton sheeting and 100-percent terry cotton fabrics — in line with the ISO 20743, JIS L 1902, and AATCC TM 100 standard testing methods. During testing, DuraTech-treated cotton underwent laundering and tumble-drying using a representative commercial detergent. Antimicrobial efficiency was tested by comparing quantities of bacteria known to cause cotton degradation on treated and untreated cotton samples, and relevant fabric properties were also measured before and after laundering.
DuraTech technology was assessed for its antimicrobial efficacy after multiple washes, following the AATCC LP1 washing protocol on various cotton materials. Fabric pH, color fastness and crocking fastness also were evaluated following AATCC TM 81, AATCC TM 61-2A, and AATCC TM 8 protocols, respectively. The reduction of odor in DuraTech-treated cotton products compared to untreated products was tested with the AATCC TM211 Drager method, providing real-time and visual depictions of ammonia levels using two ammonium-producing, odor-causing bacteria.
Seamless Incorporation Into Manufacturing
DuraTech consists of two water-soluble parts — the active compound and a catalyst — allowing for seamless mixing and incorporation into padding manufacturing processes without the need for polymer binders that can cause unexpected buildup on process rollers in the mill. Because of its water solubility and the absence of binders in its composition, DuraTech covalently bonds with the cellulose structure of cotton under certain conditions to impart long-lasting wash-resistant antimicrobial properties to the textile without impacting its physical properties.
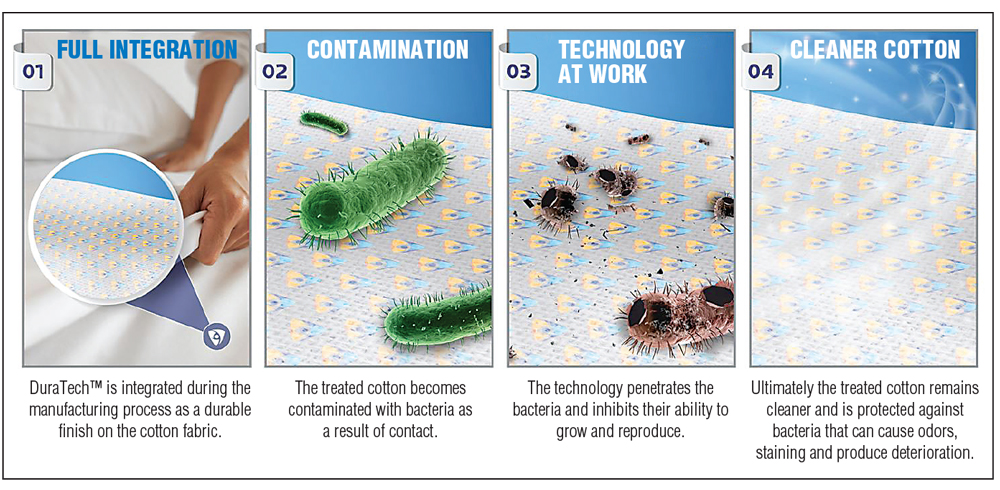
Benefits And Applications Of Antimicrobial Cotton Technologies
The expected lifespan of cotton fabrics depends on their intended use; cotton knits for seasonal garments will undergo up to 50 wash cycles, while domestic-use items like sheeting and terry towels — which are more frequently exposed to human skin and humidity — will require more regular washing. Reported findings demonstrate that DuraTech-treated cotton maintains up to 99.99-percent bacterial inhibition after 75 wash cycles compared to untreated controls. In addition, treated samples achieve up to 99-percent odor reduction after 75 washes, without compromising on other essential fabric properties.
Microban reports that DuraTech is compliant with industry standards and regulations, compatible with sustainable manufacturing processes, and safe for handlers and users. The non-heavy metal-based formula is biodegradable, and is not an aquatic hazard according to OECD test guidelines 301A, 111, and 209.5 The technology is registered with the United States Environmental Protection Agency (EPA), and Microban also is pursuing textile-specific certifications for DuraTech — like Bluesign® and Oeko-Tex® — as part of an ongoing commitment to making textile manufacturing processes more sustainable.
Built-in antimicrobial technologies can be a key tool in the cotton textile industry, seamlessly integrating into the production process to extend the usable lifespan of fabrics and enhance the end-user experience.
References
1 Cotton: Industries: WWF. World Wildlife Fund. https://www.worldwildlife.org/industries/cotton.
2 Grand View Research. Global Textile Market Size & Share Report, 2022-2030. https://www.grandviewresearch.com/industry-analysis/textile-market.
3 Roy Choudhury, A. Finishes for protection against microbial, insect and UV radiation. Principles of Textile Finishing 319-382 (2017).
4 Tessier D. Surface modification of biotextiles for medical applications. Biotextiles as Medical Implants 137-156 (2013).
5 Qian, L. & Sun, G. Durable and regenerable antimicrobial textiles: Improving efficacy and
durability of biocidal functions. J Appl Polym Sci 91, 2588-2593 (2004).
Editor’s Note: Yihong Li is senior technical manager and Xiuzhu Fei is senior formulations chemist for Textiles at Microban International, Huntersville, N.C.
November/December 2022