NEW YORK CITY — March 17, 2025 — Ultrafabrics, a global supplier of high-performance coated fabrics and leather alternatives, announces the appointment of the new Director of Merchandising, Kimberle Frost. With a rich background in textile design and color consultation spanning over 30 years, Frost has successfully collaborated with esteemed brands while receiving numerous industry awards for her innovative contributions.
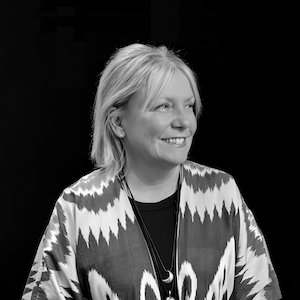
Frost’s impressive portfolio includes collaborations with notable companies such as Mayer Fabrics, Maharam, Designtex, and Robert Allen, among others. Throughout her career, she has received several prestigious awards, including the Best of Year Award from Interior Design Magazine and recognition from Metropolis Magazine. Prior to joining the Ultrafabrics team, Frost worked as an independent consultant for the brand, offering services in color consultation and product development. Her strong relationship with the team and deep understanding of the brand ultimately led her to join Ultrafabrics full-time.
“I joined Ultrafabrics because of the incredible people who truly care about each other and the products we create. Being part of a team with such a strong commitment to quality, innovation, and sustainability resonates deeply with my values,” Frost said. “I wanted to play a significant role in shaping the future of a company that sets the standard in our industry with its luxurious products and commitment to making a difference.”
In her new role as director of Merchandising at Ultrafabrics, Frost will act as a vital link between product development, marketing, and sales. She will ensure that the company’s products and colors align with its brand identity and business goals. By leveraging her creativity, strategic planning, and analytical skills, she aims to bring new products to market while enhancing business success effectively. Frost’s responsibilities will also include providing innovative product presentations to support sales, fostering deeper client interactions, and contributing to the development of both existing and new products and color palettes, all while aligning with Ultrafabrics’ brand values and mission.
“We are thrilled to welcome Kimberle to the Ultrafabrics team, as her expertise and passion for innovation will undoubtedly enhance our collaborative efforts and drive our mission forward,” says Jennifer Hendren, vice president of Product Development at Ultrafabrics. “Her extensive background in textile design and her holistic approach to merchandising aligns perfectly with our mission to deliver beautiful, sustainable products. We’re excited to have her insights and creativity driving our product development.”
Posted: March 17, 2025
Source: Ultrafabrics