BTMA Receives Award From China State Textile Industry As part of its preparations prior to Chinas
anticipated accession to the World Trade Organization (WTO), the Chinese State Textile Industry
Bureau (STIB) is taking steps to improve the overall quality of its textile production in
anticipation of greater demand from overseas.As part of these preparations, STIB has extended its
award system to include not only domestic producers, but also overseas organizations that have
played a substantial and long-term part in the development of Chinas textile industry. The British
Textile Machinery Assocation (BTMA) is the first recipient of this award, which was presented to
Eric France, director, BTMA, by Chinese Minister Du Yuzhou during the Grand Meeting of the National
Conference on Textile Development, which recently took place in Shanghai.
January 2001
BTMA Recieves Award From China State Textile Industry
CeramTec Offers Custom Traverse Guides
CeramTec North America, Laurens, S.C., has introduced its custom traverse guides, which can help
improve quality and consistency in the manufacture of most fiber and yarn types. The guides, which
are made up of a ceramic guide insert molded into a body, enhance performance on most machine types
and at various take-up speeds.The guides are available in a variety of ceramic compositions and
nylon resins, including standard, conductive and toughened aluminas; and zirconias. The diversity
of materials allows frictional characteristics to be controlled through wear properties, surface
texture, hardness, grain size, dimensional tolerances and porosity.Rapid prototyping of traverse
guides is available through CeramTecs Fast Turnaround Prototype Group. The company says it can
deliver small quantities of finished prototypes for testing in as little as three to four weeks.
January 2001
National Textile Center Receives 9 75 Million Federal Grant
WILMINGTON, Del., Jan. 3 /PRNewswire/ — The National Textile Center will receive $9.75 million
from the Department of Commerce. The United States Congress recently appropriated these funds to
support university research in textiles, apparel, fibers and retailing. This is the tenth
consecutive grant to the National Textile Center to continue its mission of enhancing the knowledge
base of the US textile and related industries. The National Textile Center has over 50 active
research projects and is currently developing new projects for the increased level of funding. The
new projects will start May 1, 2001. Current projects are underway at over 20universities across
the USA and around the world. All projects not only address important industry problems, but also
provide the research topics graduate students. The new grant funds will seek to expand the research
basis to a larger number of universities. The Congress has invested over $82 million in the
far-reaching and important effort. The results have been impressive, with over $170 million in new
business and $80 million in new centers of academic. To date over 700graduate students have been
involved in the research, resulting in 134 these and numerous patents. The full research program
will be presented to the industry at the upcoming NTC Forum. The forum will be held in Myrtle
Beach, SC, February11 – 13, 2001. Complete information is available on the web
at:http://www.ntcresearch.org The National Textile Center is a university research consortium owned
and managed by six universities: Auburn University, Clemson University, Georgia Institute of
Technology, North Carolina State University, University of Massachusetts Dartmouth and Philadelphia
University. The institutions sharehuman resources, equipment and facilities. Serving the
USAFiber/Textile/Fabricated Products/Retail Complex, the NTC vision, mission andgoals are realized
through innovate research and links to other institutions. SOURCE The National Textile CenterWeb
Site: http://www.ntcresearch.org Copyright 2001 PR Newswire
ACIMIT Says Machinery Orders Fell During First Half Of Year
ACIMIT SAYS MACHINERY ORDERS FELL DURING FIRST HALF OF YEAROrders for Italian textile machinery fell sharply for a second consecutive six-month period, according to figures released by ACIMIT, the Association of Italian Textile Machinery Producers.The general index for orders has fallen by 18% compared to the same period for the previous year, ending at 87.9 points (base year 1995=100). The drop was mainly in the foreign market, where the index for orders, 83.7 points, fell by 21%. The drop in orders in the internal market was 12% and the relative index 97.5 points.”We are not only dealing with the inevitable natural downturn in the sector,” explains Dr. Alberto M. Sacchi, president of ACIMIT. “Another element which has had a negative influence on the orders received by producers is the difficult economic situation of many economies. The U.S. and Turkey, for example, important markets for Italian textile machinery, are undergoing an economic downturn. The results of this are reductions in investments in the textile industry and reductions in the purchasing of machinery. In Europe, on the other hand, there are countries to which our exports continue to grow (Spain, France, Switzerland) and markets (mainly Germany) where Italian textile machinery is struggling to repeat the successes of last year.”Sacchi says there are considerable worries about the situation in the U.S. market following the recent tragedy there. The American textile industry, already undergoing restructuring, may now be further weakened by the probable drop in consumption, already felt before the terrorist attacks in the U.S.In relation to the competitiveness of the sector, Sacchi also says “ACIMIT will continue to fight for the elimination of all the bureaucratic constraints which block extraordinary operations which can provide real added value to Italian companies in terms of competitiveness. It is increasingly necessary to provide Italian companies with valid instruments so they can compete with the international competitors in all the foreign markets. This must be ensured over the short term because in our age it is rapid change which can ensure leadership in any given market”.However, the speed of change is also subject to constant research and innovation activities. This is why ACIMIT recently signed an agreement with CPI (Consorzio Politecnico di Milano Milan Polytechnic Consortium) to put companies and research centers in contact with each other. “Often, says Sacchi, “there is nobody to bring demand and supply together. The agreement signed with CPI aims to satisfy this basic requirement. The Consortium will identify, within the Milan University field or using third-parties, the skills and know-how required to provide a solution for the technological and scientific problems of textile machinery companies.”November 2001
New Nylstar Plant Aims At NAFTA Markets
FibersBy John W. McCurry, Managing Editor New Nylstar Plant Aims At NAFTA MarketsNylon yarn facility helps boost economy in beleaguered southern Virginia. A joint venture between Rhodia and Snia, Nylstar was looking for a manufacturing platform to serve the NAFTA region when it found Amfibe in Martinsville, Va., in April 2000. A nylon monofilament plant, Amfibe was founded by a group led by manmade fiber veteran Larry McDorman and began operations in 1998.Eager to expand, Nylstar began construction of a plant now known as Amfibe 2 in August 2000 and a year later it began operations. Construction crews and equipment installers worked 16-hr days to bring the new plant online. The opening of the $50 million facility is welcome news to the Martinsville area, which has been hit hard by the closing of Tultex and layoffs in the furniture industry.The plant employs about 100 and Nylstar officials expect it to reach capacity this month. The plant is capable of producing 25 to 30 million lb/yr of nylon yarns depending on the product mix.”I commend Rhodias engineering groups ability to build a nylon facility,” says Larry McDorman, now vice of manufacturing for Nylstars U.S. operations. Products range from 15 to 220 den. The plant also produces POY and FOY 6,6 nylon.
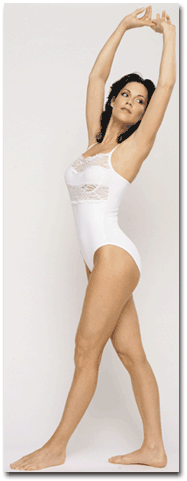
Nylstar yarns are used in a variety of applications, including women’s intimate apparel. Meryl is Nylstars “signature” brand for its yarn products. Meryl includes several sub brands for various niche markets. Yarns made of Nylstars new Elite fiber will also be manufactured in Virginia. Nylstar says Elite gives fabrics “remarkable” hand and drape.”
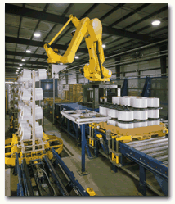
The new plant has four 20,000 sq. ft. floors with processes beginning on the top floor. Production processes began with nylon chips supplied by Nylstar facilities in Europe. Three large silos store the chips until ready for transport for extrusion into polymer. Each silo contains different lusters of chips to allow for maximum flexibility. “We can make any product on any machine,” McDorman says.Plant equipment includes the latest Barmag machines. Robotic equipment supplied by Fanuc doffs yarn and transports it to an automatic packing station.”Our customers are happy to see someone investing in new equipment in the U.S.,” McDorman says.
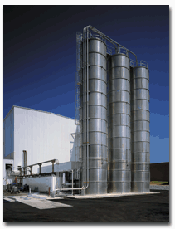
There is room for expansion at Martinsville. In fact, there are tentative plans for an “Amfibe 3” plant should business conditions warrant.During the plants construction, Nylstar sent 38 production employees and nine supervisors to its European facilities for a month of training. Of the production employees, 22 came from Amfibe 1 and 16 were new hires. These employees trained all new employees.The new plant has been a blessing for some displaced textile workers in the Martinsville area. These include Alice Tucker, who spent 11 years in the cutting and sewing department at Tultex before it closed in December 1999. Tucker, who works in the inspection and packing department, says she has “found a new home at Nylstar.” Yarn produced at Martinsville finds its way into end products ranging from velcro to womens intimate apparel. Customers include weavers, warpknitters and circular knitters. Nylstar also sells POY to texturing companies.”Having a strong presence in North America allows Nylstar to participate in all these markets,” McDorman says. “A lot of our customers are insisting that yarn be NAFTA and CBI approved. We look for niches where we can compete best.”Dina Dunn, Nylstars U.S. vice president, marketing, says the company is seeing a lot of success in a difficult textile and apparel environment. “Were in a startup mode, so its been all growth for us. Weve had lots of positive comments from customers.” Dunn says Nylstar approaches business with a consumer focus, particularly in the intimate apparel and activewear markets. Seamless garments are beginning to catch on with consumers and swimwear and outerwear markets offer much potential, she says.”Were a worldwide player,” Dunn says. “We offer the advantages of sourcing on this continent. While Asia has comparable pricing, we reduce delivery time by three weeks. Mexico is all growth for us now. There is heavy competition on pricing, so we compete where we can.”We have steady business in Canada. In the U.S., brands like the Victoria Secrets and the Vanity Fares drive the business. Theres a lot of promise in all three countries.”A Quick Look At NylstarNylstar formed on Jan. 1, 1994 when French firm Rhone Poulenc (now Rhodia) and Italian company Snia Fibre (now Snia SpA) merged their fiber manufacturing operations. Nylstar produces 270 million lb/yr yarn and employs about 5,000 worldwide.In addition to Martinsville, Va., Nylstar has production facilites in:o Freiburg, Germanyo Neumunster, Germanyo Arras, Franceo Blanes, Spaino Gorzow, Polando Ying Long, Chinao Cesano/Varedo, Italyo Pisticci, ItalyOctober 2001
Great American Knitting Mills To Acquire Certain Ridgeview Assets
NEWTON, N.C., Jan. 25 /PRNewswire/ — On Friday January 19, 2001 Ridgeview entered into a letter of
intent with Great American Knitting Mills to sell certain assets, including the Ridgeview name and
other trademarks. The intent of the proposed transaction is to continue Ridgeview’s sport sock
business inthe sporting goods market and to provide the resources necessary to build thebrand going
forward. The agreement has a closing date of February 1, 2001. Ridgeview continues to operate and
meet its customers’ needs at the present time. Both companiesexpect the transition to be a smooth
one for Ridgeview’s customers. It isun clear at this point exactly what the transaction will mean
to Ridgeview’s operations. Hugh Gaither, President and CEO of Ridgeview, said, “the transaction
provides an opportunity for our Ridgeview sport sock business tocontinue in the market place.” Jim
Williams, President and CEO of Great American Knitting Mills added, “We are excited about this new
business opportunity and very encouraged by informal customer reaction to the business
combination.”SOURCE Ridgeview, Inc.Copyright 2001 PR Newswire
ITMA 2003 News
New eight-day format: Circular knitting machinery WILL be shown The first ITMA of the 21st Century
will set a precedent: it will be staged over 8 days, instead of the traditional 10.Organisers of
ITMA 2003, to be held at The National Exhibition Centre (NEC), Birmingham, England, have announced
that the show will run from October 22 to 29 inclusive. The shorter duration is in response to
feedback from both exhibitors and visitors, who want to cut down on expenditure and reduce the
out-of-office time commitment for key personnel.Another vital boost for ITMA 2003 comes with the
news that the leading circular knitting machinery manufacturers have confirmed that they WILL take
part in ITMA 2003, instead of attending another show being organised at the same time in Italy.
Their decision underlines the appeal of ITMA as the world’s premier textile machinery exhibition
for all sectors of the textile industry.Officials at The NEC venue, which will stage ITMA for the
first time in 2003, say they are delighted with these two positive announcements. Maria Avery,
Exhibition Director of the ITMA 2003 Organising Committee at The NEC stated : “Representatives of
several leading knitting machinery companies have visited The NEC recently, and have been impressed
both with the facilities and the cost-effectiveness of the overall package we can offer.”We are
pleased that this has corrected some of the unfair and unfounded criticism that has been stirred up
in some quarters, and we are delighted to welcome circular knitting machine producers as an
important exhibit group.” The NEC and Cematex – the pan-European machinery body which stages the
four-yearly ITMA shows – are also confident that the switch to the more compact, eight-day format,
will be a winner. This decision, which will apply to all future ITMAs, recognises the changing
business environment and the influence of the internet and e-mail.Maria Avery added:
“Overwhelmingly, feedback has confirmed that a 10-day show is too long. We have acted accordingly
and reduced ITMA 2003 to eight days, ensuring that the popular busy weekend is still embraced.
Significantly, eight days ensures that exhibitors do not have their personnel away from the office
for such a long period, while allowing the visitors plenty of time to see all the equipment they
are interested in. The reduced period also means reduced expenditure for both exhibitors and
visitors.”ITMA 2003 will occupy some 160,000 square metres of stand space, with an expected total
of 1,400 exhibitors from 40 countries attracting around 150,000 visitors from the world’s textile
industries. Further details can be accessed from the main ITMA website : www.itma.com and from the
dedicated hotel website : www.itmahotels.com, as well as a brand new site, www.itmatravel.com,
focusing on all aspects of transport to and at ITMA 2003.For further information contact – The ITMA
2003 Organising CommitteeThe NEC Birmingham B40 1NT England Tel – +44 121 780 2003Fax – +44 121 782
2003 email – info@itma2003.comwww.itma.com
ATME-I 2000 Exhibitor Overview
of the companies that exhibited at the American Textile Machinery Exhibition-International 2000
(ATME-I). Obviously, space does not allow a comprehensive review of every display. ATI selected a
representative list of companies to interview in order to provide its readers with a feel for the
offerings at the exhibition. Some major exhibitors are not listed here, such as Rieter, Suessen,
Saco Lowell and Murata; they will be covered in a separate article about spinning technology to
appear in next months issue. Other companies Dilo and Fleissner, for example will be covered in an
upcoming nonwovens roundup. Barmag AG/Saurer Group, Germany/Switzerland (American Barmag Corp.,
Charlotte, N.C.), presented for the first time the new Automatic Winder babyASW. This winder, which
will be used primarily for technical yarns, specifically targets the markets of Mexico and South
America. The dimensions of the babyASW are much smaller than those of the regular ASW winder. It
features a camshaft traverse system, a string-up device with package protection function and a
counter for current yarn capturing. Options include machine frame and unheated godets, yarn sensors
and yarn cutters, spin-finish and intermingling equipment, and a cradle.Belmont Textile Machinery
Company, Mount Holly, N.C., exhibited its new EW1000 winder for the carpet industry. By means of a
new traverse cam-and-dog assembly, winding speeds of up to 1,100 meters per minute (m/min) can be
achieved. A new overfeed system guarantees perfect tension control independent of speed and fiber
type. The EW-1000 is compact and features a modular design that is expandable up to 72 spindles in
12-spindle increments. An electronic touch-screen panel regulates winding speeds, displays
production efficiency and monitors winder operating parameters.The company also showed the new
Rototwist yarn twister that produces 2-, 3-, 4-, 5-, or 6-ply yarns in one pass. It is designed for
continuous operation to run up to 600 m/min, and it offers the feature of alternating S+Z twists
that are carefully tacked through a servo-controlled air jet. The machine can be installed in line
with existing heat-setting equipment, or as a stand-alone Rototwist system. Belmont Textile
Machinery also presented a new prototype of a package knotter and placement robot that was designed
for auto-doff winders.CMD Systems, Charlotte, N.C., provides consulting services to textile
manufacturing and distribution organizations in computerized Enterprise Resource Planing (ERP)
systems. The company assists small and large textile and apparel manufacturers and distributors in
the selection, design/ modification and implementation of software and hardware for ERP and supply
chain management systems.Datatex USA, Alpharetta, Ga., a supplier of specialized ERP systems for
the textile and apparel industries, featured its Textile Integrated Management (TIM) software for
network-oriented applications in AS/400 environments. Datatex announced that, to date, it has
implemented 250 systems in large- and medium-sized textile manufacturing plants in 30 countries.
Datatex provides software modules, designed specifically for the modern textile mills, for sales,
manufacturing, planning, and inventory and purchasing. Datatex claims its software will optimize
the use of manufacturing resources, continuously monitor contribution margins, provide basic
quick-response capabilities, improve customer service, reduce waste and reduce work-in-process and
finished goods inventories.
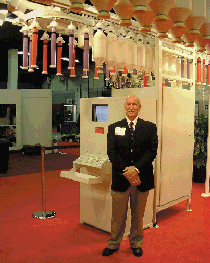
Electro-Jet S.A., Spain (PSP Marketing, Charlotte N.C.), introduced the new Roving Bobbin
Stripper for spinning installations. The machine uses compressed air to open and remove remaining
fiber and roving pieces from the bobbins. Since this is a modular system, there can be from one to
as many as required stripper heads installed. The system consists of the TAB-System for roving
bobbin transport, and the TAC-System for bobbin transfer. Fiber-optics sensors ensure all material
is removed, and other special sensors detect any misalignment to avoid damages that could be done
to the bobbins or the bobbin hangers. After the cleaning process, the bobbins are automatically
integrated into the clean roving bobbin supply.Electro-Jet exhibited for the first time in the
United States a manual system for ring-spinning bobbin cleaning, model MLB. An automatic version is
available that consists of a CT sorting unit; the MLB cleaning machine; and a JET-1, JET-2, or
JET-3 laying machine. The system works with any kind of bobbin without specific adjustments.
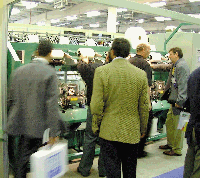
Fehrer AG, Spinning Machinery Division, Austria (Symtech Inc., Spartanburg, S.C.), promoted
its DREF 2000 friction-spinning machine with extended yarn applications. The machine expands the
scope of yarn-friction spinning in the medium-yarn-count range and the coarse count range. The
machine shown at ATME-I produced yarns for secondary carpet backings, filter cartridges, blankets,
cleaning rags and mops, and FR fabrics. The use of synthetic fiber waste materials was demonstrated
for use in combination with yarns for blankets, upholstery, filler yarns for ropes, carpets and
many other applications. FranklandThomas Inc., Greenville, S.C., a long-time supplier of
Nippon Nozzle Co. Ltd. spinnerets and manmade-fiber spinning accessories, has added Sue® Seki
separator rolls, HSGM heat cutters and Seydel stretch tow breakers to its offerings.Heberlein Fiber
Technology Inc., Switzerland (Heberlein North America Inc., Greenville, S.C.), exhibited a wide
range of its components for processing and finishing of synthetic yarns. The company builds core
elements for synthetic-fiber spinning machines. This includes high-performance interlacing jets
that enable todays high-process speeds in spinning, drawing and false-twist texturing. Heberlein
also offers air-texturing jets for the production of Taslan® textured yarns with spun yarn
character, at speeds of up to 1,000 m/min. The company offers friction discs made of special
materials that guarantee durability and a long life span at high texturing speeds.IKOS Inc.,
Charlotte, N.C., develops software for ERP and consults on the installation/implementation of its
software in a manufacturing environment. The company featured its Locator® software that gives
manufacturers a competitive edge in warehouse management through production automation, reduced
workforce, reduced rework, just-in-time (JIT) management, real-time information, Internet
connectivity, B2B communications and inventory accuracy. Additionally, IKOS demonstrated its
Resource Management Solution, software assisting management in resource allocation decisions; IKOS
Scheduler; and IKOS Logger all of which permit management to manipulate the schedule for and track
the material flow through a product or project management situation. Industrial Air Inc.,
Greensboro, N.C., presented filtration systems ranging from integrated air systems to air washers;
fiber and waste separators; custom HVAC systems; and bag, drum and roll filters. Among the newest
offerings from Industrial Air is the S series drum filter, which is constructed of steel perforated
panels bolted together to form a cylindrical, horizontal rotating drum. The arrangement allows even
air distribution across the fabric-filtering media. When bolted together in multiple sections,
these panels form a rigid cylindrical truss member that eliminates the need for a continuous center
support shaft, thus facilitating maintenance. The drum is cleaned by a series of vacuum nozzles
located on the outside of the cylinder, allowing convenient media inspection.Industrial Air has
also introduced a new Hi-Vac sleeve receiver that has 400 percent more screen area than standard
30-inch flat-screen receivers.J. D. Hollingsworth on Wheels Inc., Greenville, S.C., promoted its
metal clothing wires for opening, carding and yarn-spinning applications. The company claims that
the Mastersteel wire is the longest-wearing wire available for high production cards in 1-meter
(40-inch) width, with good performance for every fiber type. The other wire type, the Enhanced
Point Wire, allows for a wider setting between the doffer and the cylinder on high-production
cards, thereby reducing the risk of facing. It has controlled points that pick up fibers
efficiently from the cylinder and is available in non-serrated and serrated finishes and in a
variety of sizes.Jomar Software Corp., Charlotte, N.C., presented the Web-based e-TPF software that
offers textile-specific applications. It is suitable for controlling textile processes and tracking
from fibers to the finished fabric. The e-TPF software is integrated with JAVA and Web Server
technology. For example, the weaving and knitting systems software is designed for the assignments
of warp/section beams to a knitting or weaving schedule by individual beams, or number of ends. The
system allows warps to be matched by style, number of ends, weight and length. It also supports
process control for the width and length fabrics have to be cut, slit or rolled. The Jomar e-TPF is
available for spinning, warping, weaving and knitting, dyeing, finishing, cut and sew, and
converting processes, among others.

LTG AG, Germany (LTG Inc., Spartanburg, S.C.), showed the improved Versa Drum Filter VDF-16,
which now features 16 larger drums. A further improvement is that the filter medium can be changed
in approximately 15 minutes. All mechanical parts are on the clean side, which makes it easy and
clean to service the filter. The VDF also features continuous-suction cleaning of the internally
loaded filter drums. The capacity is up to 35,000 cubic feet per minute (cfm) for cotton-opening
and carding applications, and 60,000 cfm for general room filtration. The VersaDrum Filter is a
compact filter unit.LTG also had on display a large Tangential Fan that delivers a sheet of air
flow and can be used in a large variety of applications such as heating, cooling and drying, with
an even air flow over large surface areas.LTG promoted once again its diffuser systems type WDA/WDB
for direct conditioning of weaving machines. Company officials said the system is simple and,
therefore, very competitive in relation to installation and operating costs. A few months ago, LTG
Inc. changed its philosophy to turn away from providing complete turnkey projects in the United
States. The company now offers its technology to other vendors and fulfills orders for
customer-installed equipment.
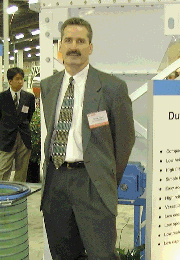
Luwa Bahnson Inc., Winston- Salem, N.C., displayed its new Dust Separator III, model DS-III.
The DS III reduces space requirements and improves ease of maintenance. It is the final element in
removing dust from textile and nonwovens processes. The vertical design of the filter cartridges
provides more efficient pulsing of dust. In extra-heavy fiber loading, an optional screen sleeve is
mounted around the cartridges. Extra-wide cartridge spacing prevents bridging of fibers. The
special cone in the center of the cartridge enhances the automatic cleaning by compressed air. This
provides a longer cartridge life and reduced service requirements. The discharge air can be
returned either to the room or to the central filtration system.Luwa also exhibited the latest
version of its Multi Drum-Vac® (MDV), the 9-foot-diameter MDV that supplies spinning-production
applications with up to 50,000 cfm of air, and ambient filtration up to 70,000 cfm.N.
SchlumbergerandCie, France (N. Schlumberger USA Inc., Fort Mill, S.C.), showed the latest version
of its CF-60 series double-sided ring- spinning frame that is specifically suitable for the
production of semi-worsted lines of carpet and rug yarns, upholstery yarns, knitting yarns and
technical yarns. It covers a yarn-count range from Nm 2 to 20/24 and can be equipped with an
automatic doffing system.NSC also exhibited the latest version of its tandem chain gill, the TM/GC
15 RE with an electronic autoleveller. It is designed for integration in compact spinning lines for
the production of carpet, upholstery and hand-knitted yarns. It features bi-directional control
through touch-screen dialogue, electronic draft adjustment and other advanced features that allow
production speeds of up to 550 yards per minute (500 m/min).Network Systems International Inc.,
Greensboro, N.C., offers the turn-key Net Collection, an enterprise-wide suite of ERP solutions
designed to enhance management planning and control in complex process and distribution centers.
The software includes modules covering enterprise demand management, time-phased resource planning,
supply-chain advisements and monitoring, distribution center authority and executive information
analysis broken down into task-specific sub-modules governing the major steps involved in producing
and delivering textiles, apparel and made-up items. At ATME-I 2000, Network Systems introduced four
new functions for its netCollection suite: netCashController, netSalesExec, Tracking Portal and
UltraClient. The first three apply to specific management areas, while the fourth allows access to
all functions of the complete software package over the Internet using a standard Web browser. This
allows away-from-home access and control over internal systems and provides remote sales personnel
and customers with ready access to sales order and delivery information without additional
connection costs or special software.Pneumafil Corp., Charlotte, N.C., presented the Everclean®
Rotary Pleated Belt Filter (RPB) that filters air more thoroughly than conventional tandem filters,
according to company officials. The RPB filter consists of a number of filter cells. Each cell is
comprised of an endless pleated filter-media belt, looped between two pulleys. Unfiltered air
enters the unit parallel to the filter cells and passes through the straight sections of the belt
loop. Larger fibers collect on the outer edges of the pleat, and smaller particles build up on the
media surfaces between pleats. The clean air continues between the two sides of the cell into a
plenum in back of the filter and then exits. Pressure drop across the media is constantly monitored
by a dual set-point Dwyer Photohelic gauge. When the high point is reached for a given cell, that
cells belt begins rotating around the pulleys, and a stationary suction plenum underneath the cell
is activated. As the belt moves around the lower pulley, the pleats open up and air flow through
the media is reversed, allowing the pleats to be easily vacuum-cleaned.Pneumafil promoted the
compact modular system utilized by its conditioning units. This system facilitates movement during
installation or relocation.OMM/Fillattice SPA, Italy (Fillattice Inc., Charlotte, N.C.), exhibited
the OMM type SPE covering machine for the production of Fillattice spandex yarn. The machine offers
several features, including the new SX spindle type, an electronically controlled take-up, and an
electronically controlled traversing device that assures excellent quality without any mirror
effects. The machine is available with a wide range of heads and a spindle gauge of 200 or 265
millimeters.
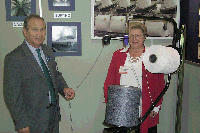
Otto Zollinger Inc., Spartanburg, S.C., displayed its full line of yarn controls. The O-Z®
Yarn Control System provides constant, uniform tension with no adjustments; reduces yarn breaks;
increases quality; increases production; reduces maintenance; allows easy package transfers; and
does not restrict speed, according to the company.Roberts, CurryandCo., Greenville, S.C., is a
management-consulting firm specializing in the textile and apparel industries. Its experience and
expertise cover all facets of textile operations with heavy emphasis on productivity improvements,
management systems, technology assessments, marketing, human resources development and total
quality management (TQM). Additionally, the organization is well-versed in many apparel operational
issues.
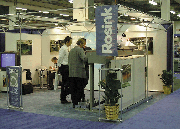
Rosink GmbH, Germany, exhibited the RK-W-235 rectangular can coiler with automatic can
changer. Rosink states that the RK can coiler is the worlds first self-contained rectangular can
coiler. Conveyor belt and calender rollers are independently servo-driven. The coiler operation is
synchronized electronically with the host machine. There is no mechanical interface, gearbox or
chain drive. A coiler-head dust-extraction system is included. Rosink RK can coilers are adaptable
to the Rosink can-transport system. The company also offers round can coilers, carriers and
can-changer systems for new cards and as retrofits for older cards.SAP America, Newtown Square,
Pa., teamed with its textile-industry specialist, Prescient Consulting, Atlanta, to introduce the
Prescient-designed textile-industry-specific version of SAPs R/3 ERP software. Building on the
recent success of SAPs Apparel and Footwear Solution (AFS), the partners are extolling the virtues
of the software, which is composed of modules specifically designed to address issues in management
of the textile supply/value chain. SAP has considerable experience in supply-chain management
controls and has partnered with Prescient to bring industry expertise to the design, installation
and implementation of the R/3 system for textiles.Savio Macchine Tessili SPA, Italy (American
Savio, Spartanburg, S.C.), showed the Orion Automatic Winder and the Geminis Twister. The Orions
key feature is its electronically controlled computer aided package (CAP) that prevents any
patterning of the yarn on the package. The Orion winder surpassed all early predictions for
incoming orders between the introduction of the machine at the International Textile Machinery
Exhibition (ITMA 99) and ATME-I 2000, according to company officials. Savio received the ATI Award
for Innovation in 1999 for this machine. Since then, the company has expanded the application and
model range of the Orion winder. Orion M is a model with manual feeding and doffing; Orion L
features manual feeding with automatic doffing; Orion E is a fully automatic version; and Orion I
is the linked version of the series.SML Lenzing, Austria (Tex America Inc., Charlotte, N.C.),
promoted its product line that includes extrusion technology for the plastics and textile industry,
BCF spinning technology and FDY spinning technology. SML is a member of the Starlinger Group,
Austria, which has more than 35 years of experience in developing, designing and manufacturing
extruders. SMLs Austrofil® BCF spinning system offers minimum floor space, high crimp contraction,
good crimp stability and low shrinkage. For Austrofil® FDY spinning, SML offers the MT version for
the production of continuous filament with medium tenacity, and the HT version for the production
of continuous filament with high tenacity of up to 8.5 grams per denier, both in the yarn- count
range of 200 to 1,600 denier.TextileWeb.com, Greensboro, N.C., featured its new relationship with
VerticalNet, the Philadelphia-based backer of 57 new economy enterprises. TextileWeb is focusing
its current efforts on expansion of its trading platform, which covers textile materials from
fibers to sewing supplies. The company is adding services to its website, which now features access
to databases for services in consulting, marketing and investment banking.The Dock, Los Angeles, is
introducing a website/database for trading textile machinery. Target customers are traditional
machinery dealers and individual companies looking to buy, sell or trade used textile equipment.
The Dock does not require it be included in all purchases/sales transactions. The site establishes
contacts and is willing to be involved in negotiations and financing, but The Dock also is willing
to allow the principals to conclude a deal without its involvement. Revenue is gained from
advertising, sale of home pages to active buyers/sellers and from the fee charged if The Dock is
included in a purchase negotiation.
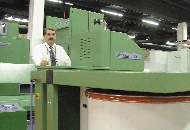
Truetzschler GmbH, Germany (American Truetzschler, Charlotte, N.C.), presented its newly
enhanced high-production card, the model DK 90. A new equipment kit specifically designed for
synthetic fiber applications has considerably improved productivity and efficiency for man-made
fiber processing. New also is the linking of the DK 903 with the integrated draw frame (IDF) that
was originally shown in Paris as a prototype. Depending on the final application, it offers the
possibility of bypassing one draw-frame passage and, in some cases, even two draw- frame passages.
The new production-ready equipment from Truetzschler helps to improve the economy of the yarn
preparation room.Also displayed in the booth was the HSR 1000 draw frame with rectangular
can-delivery system. Up to 50 kilograms (approximately 110 pounds) of draw-frame sliver can be
smoothly coiled into these rectangular cans, which are designed for use at roving machines. Also
new is the Securomat SCFO, which is a multifunctional machine for fiber preparation. It ensures an
intensive dedusting of the cotton through the use of an integrated camera system that detects and
separates foreign particles.U.T.I.T Textile Division, Wagner Automation, SPA, Italy, displayed
cone-cartoning automation systems. The U.T.I.T. line provides an example of a fully integrated,
automated packaging system. All stages of the process, collection of cones from the link-cone
winders, checking and labeling of individual cones, conditioning, carton placement taping and
palletizing are executed automatically without intervention by human operators. The line permits
the collection of cones from various cone winders that produce yarns of different counts. Dedicated
control software allows the simultaneous management of control, packaging and palletizing of
different yarn counts, while maintaining independent management of each count during the whole
cycle.Xorella AG, Switzerland (PSP Marketing Inc., Charlotte, N.C.), exhibited the Contexxor®
Compact Unit LTC-S for yarn conditioning. The rectangular shape of this new machine permits
optimized utilization of space for the yarns inside, lower space requirements for the mill and
shorter processing times. It also has low energy consumption because of the new ECO system. Xorella
received the ATI Award for Innovation after ITMA 99 for this technology.Zellweger Uster,
Switzerland, (Zellweger Uster Inc., Knoxville, Tenn., and Charlotte, N.C.), showed the Uster® Afis
Pro, Uster Tensorapid 4 and Uster Tensojet, the most technologically advanced fiber- and
yarn-testing equipment the company has available. With its new Windows-based software, Uster Afis
Pro offers up to 50-percent-faster testing speeds than its predecessor. It integrates new reporting
and diagnostic software for graphical comparison of fiber quality to Uster Statistics, thus
contributing to a more efficient use and control of the raw material in the production process.The
Uster Tensorapid 4 improves quality and process control with its increased yarn-quality evaluation
capabilities. New are sensors for denim fabrics and technical yarns; and warning and control limits
can easily be configured. The equipment facilitates new test procedures, especially in the areas of
strength testing and filament yarns.The new Uster Tensojet 4 is the latest generation of the
high-performance tensile testing installation for effective and mill-oriented yarn quality
control.New, as well, is the Uster HVI Spectrum, which represents the companys new generation of
bundle- fiber testing. Features include completely automated sampling, accurate and precise cotton
fiber maturity index, and drastically reduced sample and laboratory conditioning requirements.
Complete automation reduces operator influence to a minimum. Additional new features include
automated calibration checking, accurate short-fiber index, automatic moisture measurement of
samples and quality control tools.
Editor’s Note: Executive Editor Jim Phillips, Senior Technical Editor Eric Vonwiller, Fibers
Technical Editor John E. Luke, Spinning Technical Editor Dr. William Oxenham, and Nonwovens
Technical Editor Richard G. Mansfield contributed to this article.
December 2000
Radici Becomes Sole Owner Of FIM Textile
The previously announced joint acquisition of Italy-based FIM Textile by Picanol, Belgium, and the
Italy-based Radici Group has been called off. Radici is now the sole owner of FIM Textile.It
appeared that the expected synergies related to the double-shareholder structure by Picanol and
Radici would be difficult to materialize in practice. Therefore, both parties agreed that Picanol
will not enter the capital of FIM Textile.
December 2000
DuPont Combines Apparel And Textile Businesses
DuPont, Wilmington, Del., has announced the integration of its apparel, home textiles and related
businesses into a market-focused global organization. The name for the new organization is DuPont
Apparel and Textile Sciences.DuPonts Lycra® elastane-, nylon textile- and Dacron®-branded
specialties and fiberfill businesses will become a single unit effective January 1, 2001. The new
unit will capitalize on DuPonts global brand franchise, technical expertise, operational scale and
market knowledge to provide a more streamlined and competitive offering.Our vision is to create
consumer preference and loyalty to help grow our customers offerings by linking DuPont science with
the promise of our brands, said Steven R. McCracken, group vice president, who will lead the new
organization.DuPont Apparel and Textile Sciences will provide a world-class integrated market
platform that will allow better linkage between the marketplace and DuPont technologies. The
combined organization will have approximately 10,000 employees and marketing, technical and
manufacturing operations in every region of the world.We believe this centralized market approach
will provide economies of scale and scope, enable us to build stronger partnerships with our
customers and better deliver the constant flow of newness our global markets demand, added
McCracken.
December 2000