Chemical TreatmentandFinishingBy William C. Smith, Consulting Editor Laminate Faster, More CompetitiveNew flat-bed laminating system uses special techniques to provide uniform bond strengths at much faster speeds.
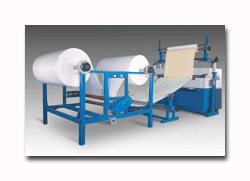
Fabrics bonded to foam have been used for many years for a variety of consumer and industrial applications to achieve bulk, soft hand, sound dampening and the like. A favorite method of bonding such fabrics has been flame laminating whereby polyester foam is passed by a flame, which literally melts the surface of the foam and a fabric immediately laid onto the melted foam and combined by pressure at the laminators nip roll. The melted foam acts as an adhesive for bonding the fabric to the foam for subsequent processing. A second pass may laminate the same or a different material on the opposite side, depending on the needs of the target end use. The process is fast, efficient and doesnt require an oven. But it has major drawbacks: The burning/melting foam produces heavy smoke and toxic fumes such as hydrogen chloride and/or cyanides which must be properly handled with ventilation and incineration or other pollution abatement equipment. Many places have banned or severely restricted further installations of flame laminating, and those in place have been forced to install expensive treatment equipment.Many other laminating systems use solvent-based adhesives, often to create a vinyl or urethane film-fabric-film sandwich, in the case of tarpaulin or signage fabrics, or two fabrics combined with an adhesive in the middle, such as for convertible tops. These solvent systems must also have the abatement equipment to handle the off-gases and by-products. Aqueous systems are available, and are successful for some applications, but for many others, they have inadequate performance properties of the laminates for the specified application or require more expensive processing techniques. New processes have been developed aimed at replacing flame laminating and solvent processing. They include the use of hot-melt adhesives, adhesive films and other non-solvent, environmentally friendly systems. These accomplish the task in many applications, but also have limitations. Slower line speeds are required for most systems, and uniform bond strength is often a problem.A new contender is on the horizon: flat-bed laminatingnot conventional flat-bed laminating, used successfully in many garment applications, but a newly developed flat-bed laminating system using special techniques that provide uniform bond strengths and speeds approaching those of flame laminating. It is more attractive economically than most systems now in use and can be competitive with flame bonding. Using separate heating and cooling chambers and a top and bottom belt transport system, with even pressure and heat through the oven, are some of the techniques that allow production at a comfortable speed of 30 mpm, up to three times the normal speed of in-place flat-bed laminators. Though flame laminating can approach 40 mpm, aside from the pollution problem, there are limitations on the types of foam or other substrates it can use. Among other things, they must be meltable. The new Bondtex flat bed laminating system can use many types of substrates, including the less expensive polyurethane or ether-based foam materials. Glenro Inc., a long-time leading supplier of process heating engineering and equipment, ovens and after-treatment equipment, fume oxidizers and now flat-bed laminating systems, acquired the Bondtex technology in the first quarter of 2001 from Textile SystemsandSupply of Los Angeles. Nick Pourmand, the Bondtex developer, has joined Glenro, designing laminating systems and working with customers on trial runs and developing specific techniques based on the end use.
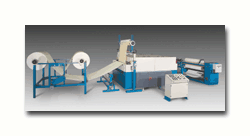
A full-scale demonstration line in Los Angeles enables customers to evaluate the new laminating system first hand.Jim Alimena, Glenro marketing manager, says the acquisition of Bondtex laminating technology provides the company a way to expand its offering to textile companies trying to add value to its products. “Many potential users of this laminating technology are already using (our) infrared and hot-air heat processing equipment. Many laminating lines require an infrared preheater to prepare the fabric for lamination. (We have) been applying infrared to fabric webs for over four decades.”Pourmand tried to work with flat bed laminating 11 years ago, importing a state-of-the-art machine to use powder bonding for textiles, leather and vinyl materials, but found it wonting. The heat and pressure was “just not right,” and he couldnt get the bonding he needed. So the machine was sent back. After 3-4 years more of working with other suppliers and trying to improve the process, he finally “found a solution.” A first step was to improve laminate bonding by heating the materials to be bonded prior to going through the oven in the transport belt. Time through the oven was too short, so he added continuous pressure to the material as it goes through the oven. But uneven heating was a concern. Pourmand found full-width top and bottom belts and multizone heating provided the uniform heating needed. But after heating and bonding, the materials have to be cooled. Most systems use a single transport belt, with a cooling section at the end, but still within the oven, thus, causing the heating and cooling cycles to “fight or compete,” resulting in having to run at slower speeds to properly bond and cool the combined materials. Thus the transport belt is heated then cooled, then heated, etc. The laminate in the Bondtex system is cooled in a separate section with an independent conveyor system. Since the same belt is not used for both heating and cooling, line speeds can be increased because the belt in the heating section does not have to be constantly brought back up to temperature. By placing the cooling unit outside the oven, with its own transport belts, speeds could be increased.Pourmand still needed more heat to further increase speeds. “One cant just increase the length of the heating chamber,” he says. “Its not cost effective.” Using infrared heaters on the substrate(s) before going into the heating was the solution. The flatbed oven doesnt have to do the melting of the adhesive used (web, film or other types) but only bonding. The infrared preheaters soften the adhesives and the two materials being bonded.
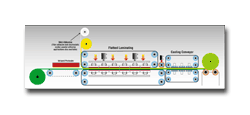
This diagram shows the components of the new flat-bed laminating system.“The primary purpose of the IR,” he says, “is to get the BTUs where you want themin the centerto heat up the surface of the substrates for introduction of adhesives.” A major reason of the success of the system is the unique use of IR technology, a Glenro specialty. Nip rolls are no longer needed in the system. Applying adjustable pressure control to the laminate, in the oven, with pneumatic cylinders on the top belt, is another key to good bonding. Others, says Pourmand, use floating flatbeds. Multizone heaters avoid edge loss. And, of course, extensive computer controls are an important key to accurate and reliable reproducibility. Each products parameters can be programmed into the computer and each run will be “exactly the same” as the previous ones.”Every good technology in the field has previously come from Europe,” says Pourmand. The Bondtex system is the only high-speed, high-end system developed and made in the U.S.Thomas Van Denend, product manager, Lamination, says, “The Bondtex system is high-performance bonding in a compact, clean process.” He points out a host of adhesives can be used, “just about anything” can be bonded. Dry adhesives store in powder, film or web form. There are no liquids involved, few regulatory concerns, little or no clean-up, quick turn-around times and often no venting requirements.Van Denend says Glenro is more solution driven rather than hardware driven. Theres a full-scale demonstration line in Los Angeles for customer evaluation. A small line at Glenros headquarters in Paterson, N.J., is being upgraded so customers can work directly with Glenro on the East Coast to run samples. EMS-Chemie, Sumter, S.C., an adhesives manufacturer, has a small lab type evaluation machine for its own trials as well as use by potential customers for trying their own products in the development process (EMS says they did blind testing and found the Bondtex machine to be the most versatile and superior in many processing areas). Glenro works with several major adhesive manufacturers to develop techniques for using their materials on the Bondtex line. The cost of “about a half million dollars” is competitive with other systems, especially considering no venting, pollution handling, regulatory or special adhesive storage problems are involved. Widths to 87 in. are available.Applications for fabrics from this system include automotive interior materials (long a critical and demanding end use for headliners and trim), medical fabric and film combinations, intimate apparel (fabric-foam-fabric combinations for bra molding, for instance), upholstery, aerospace (panel lamination for interiors of aircraft), moldable laminate panel office partitions and many more. The advantages of the machine drives development for even more demanding applications.Is this the “laminating system of the future” Only time will tell. To be sure, it is not the “do all, end all,” but, for many applications, it is superior to what is out there and may indeed replace flame lamination in many uses.
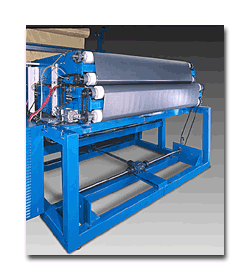
With the covers removed, you can see the inside of the exit end of the new flat-bed laminating system, which can compete with flame laminating systems.November 2001