ADLINGTON, England — March 24, 2025 — In a strategic move designed to align their long-term vision, RTS Textiles Ltd. (RTS) announced is bringing together all of its operations and joint venture partners under one unified entity, RTS Textiles Group Ltd (RTS Group). This newly formed global powerhouse in the workwear and protective textiles markets will be led by RTS, with minority shareholdings held by TMG – Acabamentos Têxteis S.A. (TMG) and Sapphire Textile Mills Ltd. (STM).
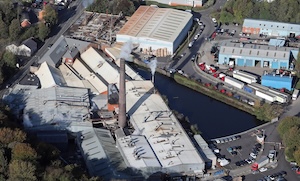
Effective March 24, 2025, this merger marks the next logical step in a partnership that has developed over years of collaboration between RTS, TMG and STM. Initially starting as supply chain partners, in 2017 TMG and RTS entered into a joint venture as MGC in Portugal, and in 2021 STM and RTS entered into a strategic partnership under CTI in Asia.
This new integrated strategic merger will further enhance the combined strength of all three companies. The merger will offer greater innovation and operational efficiency, positioning RTS Textiles Group as a leading force in the market.
The group will encompass RTS’ wholly owned brands and operations, including Carrington Textiles, Pincroft and Alltex, as well as full ownership of CTI, MGC and Melchior. The current management team at RTS will continue to lead the new entity, ensuring continuity and maintaining strong customer relationships.
Leveraging Expertise and Resources
The merger brings together the unique strengths of each organization:
- RTS: Known for high-performance flame-retardant (FR) fabrics for the PPE sector and rotary screen-printed fabrics for the military market.
- TMG: Experts in weaving, dyeing and finishing high-quality fabrics, serving a wide variety of applications in the workwear sector.
- STM: Specialises in vertical integration, with a focus on spinning, weaving, dyeing and finishing workwear textiles.
With more than 275 years of combined textile manufacturing experience, RTS Textiles Group is uniquely positioned to offer comprehensive global solutions, meeting the diverse and evolving needs of customers worldwide. The group’s manufacturing excellence spans three key centres, ensuring the highest standards across production, innovation and service.
A Vision for the Future
“We are thrilled to announce this transformative merger, which will reshape the future of RTS, TMG and STM,” said John Vareldzis, CEO of RTS Textiles. “By combining our expertise and resources, we are creating a dynamic and innovative entity that will set new standards in our industry, enabling us to better serve our customers and accelerate our growth.”
Meanwhile, TMG’s Board Member Manuel Gonçalves stated: “This merger represents a pivotal moment for our industry and for all our partners. By uniting the expertise, heritage, and innovation of RTS, TMG and STM, we are establishing a stronger foundation for growth and delivering unmatched value to our customers worldwide. Our shared vision for excellence and commitment to pushing boundaries in textile manufacturing will ensure that RTS Textiles Group sets the benchmark for quality, sustainability and innovation in workwear and protective textiles.”
Nabeel Abdullah, Sapphire Textile Mills’ COO, added: “At STM, we are delighted to embark on this new chapter with RTS Textiles Group and TMG. This strategic partnership brings a new era of collaboration, innovation and growth, creating a fully integrated textile powerhouse that enhances efficiency, drives innovation and meets the demands of an evolving global market. Together, we are positioned to redefine industry standards and deliver exceptional value to our customers.”
Benefits of the Merger
The RTS Textiles Group merger will generate significant benefits, including:
- Increased Innovation: The combined resources and expertise will accelerate the development of cutting-edge fabric solutions tailored to market needs.
- Expanded Market Reach: The new group will broaden its market presence, serving customers across a variety of sectors and regions.
- Enhanced Customer Experience: Customers will enjoy an expanded range of services, streamlined processes and improved global delivery capabilities.
The leadership teams of RTS Textiles, TMG and STM are committed to ensuring a seamless integration, maintaining high service standards and upholding strong customer relationships. Importantly, there will be no changes to ongoing projects or existing customer engagements.
Posted: March 24, 2025
Source: RTS Textiles Group Ltd