New Book HighlightsCotton Fibers’ Impact On U.S. EconomyCottons Renaissance A Study in Market Innovation, a new book by George David Smith and Timothy C. Jacobson published by Cambridge University Press, is now available from booksellers. The book tells the story of the struggle by U.S. cotton growers to grow, compete and survive for more than two centuries through a series of challenges to their markets. The book also traces the rise of Cotton Incorporated, Cary, N.C., from its establishment in 1968.In 1960, cottons share of the U.S. textile fiber market was 63 percent; by 1973, that share had fallen to an all-time low of 33 percent. Today, cotton holds a 60-percent share of the U.S. market.The authors were given full access to our records and reports, said Hugh Malone, vice president of administration, Cotton Incorporated. We let them see everything. Otherwise its merely an ego piece, and we werent interested in that.For more information, contact Thomas Pendleton, Cotton Incorporated, (212) 413-8316.November 2001
Fasturn Initiates Operations Network For Apparel Trade
Fasturn Inc., Los Angeles, has launched its Operations Network (OPN) to enable apparel retailers
and manufacturers to facilitate and streamline supply-chain management. The OPN software solution
combines advanced process management techniques with electronic communications for any business
function.Fasturn developed OPN after identifying the primary challenges that have led to industry
profits being reduced by one-half to two-thirds over the last several years. The company visited
key countries in the apparel sourcing chain and interviewed apparel retailers, manufacturers and
suppliers. Upon defining the problems and causes, the company collaborated with Accenture, PwC,
KPMG and Kurt Salmon Associates on various projects to determine the aspects of an effective
solution.The industrys supply chains are complex, multi-layered and subject to change with each new
season and style, according to Fasturn. Not surprisingly in an industry that has focused primarily
on design, promotion and site selection to gain market share, the problem was found on the
operational side of the business, said William Seagrave, CEO. Our Operations Network was designed
to help solve these challenges.By using the Internet and other such technologies, OPN users can
plan and view the entire supply chain for each style to be ordered. Internet use eliminates the
need by each supplier for investment, an advantage that Fasturn claims is particularly important in
light of the number of suppliers in the chain and the frequency with which they change.OPN features
include: coordination of schedules and tasks; two approaches management by exception and management
by key criteria; proactive monitoring of activities; and executing the supply plan.
November 2001
DuPont Teflon Unveils Let Life Happen Concept
The Wilmington, Del.-based DuPont Teflon® business has introduced Let Life Happen, a new lifestyle
concept for its Teflon fabric-protection products. DuPont wants to add value to garments and make
consumers feel comfortable eating spaghetti or allowing the kids to jump on the sofa.The concept
will be introduced globally in 2002 with an advertising print campaign, a new retail hangtag design
and a comprehensive set of promotional materials. The use of advertising in the Yellow Pages next
to listings for pizza or mechanics, for example, is an idea that will be implemented.We are
committed to raising awareness and interest in garments and home fashions which are enhanced with
stain protection, bringing value to both our trade customers and consumers, said Teresa Kleinhans,
global textiles manager, DuPont Teflon.
November 2001
GretagMacbeth GE Launch CCM Programs
CCM Silver, CCM Gold and CCM Platinum are three new corporate color management (CCM) programs
launched jointly by Switzerland-based GretagMacbeth and General Electric (GE) ColorXpressSM
Services, Pittsfield, Mass.The programs are designed to help customers reduce costs and
time-to-market issues by collaborating with industry experts to manage and improve color
communications throughout the supply chain.Key elements offered by the CCM programs include:
standards development; standards ordering and distribution via a customized Web page;
pre-production and production part auditing; color consulting, training and education; controlled
lighting and measurement devices; Root Cause and Corrective Action (RCCA) consulting, a GE Six
Sigma program; and monthly reporting and communication to the supply chain. Customers may also
select items a carte to create specific programs to fulfill general needs.
November 2001
Safe And Sound
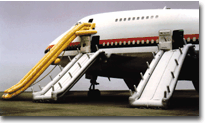
Safe And Sound
Reeves Brothers, LINQ Industrial Fabrics and Hexcel Schwebel produce textile products for
safety and performance-related applications.
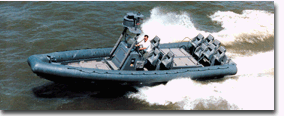
Globalization. Diversification. Innovation. Specialization. Important words all, especially
for the future of the U.S. textile industry. While still a neophyte to the concept of a world
marketplace, the U.S. textile industry is making inroads and nowhere is this more evident than in
the arena of technical and industrial fabrics.Technical fabrics create a wide range of
opportunities for textile manufacturers and capitalize on the U.S. industrys ability to make
high-quality fabrics to the most exacting specifications.From geotextiles to armor, from aerospace
fabrics to automotive airbags, from filters to truck covers, U.S. companies have few peers in this
growing segment of textile production. Reeves Brothers Diversifies Into High-Tech
MarketsReeves Brothers Inc., Spartanburg, S.C., is known for the production of its famed Vulcan®
brand of printing blankets, but the Engineered Fabrics Division of the company has diversified into
high-tech markets that maximize its production capabilities. Among the many fabrics woven and
coated with specialized treatments at the companys facilities in Spartanburg and in Rutherfordton,
N.C., is a material for the escape slides in commercial aircraft.These slides, obviously, must be
manufactured to very stringent safety requirements because of the safety factors involved, said Tom
Layton, director of sales and business development, Reeves Air Safety group. The slides are
manufactured from multiple fabrics that work together to form a single product. Flooring fabrics
are mounted to a tubing material that can inflate and stay inflated for a specific amount of time.
The base fabric for the slide is a multiple-denier nylon substrate woven using Dornier rapier looms
at the companys Spartanburg plant. A special urethane coating is applied at another Spartanburg
facility.The escape slides are manufactured to very exacting specifications, Layton said. They must
meet certain deployment standards that is, they must deploy in the same fashion every time,
maintaining specific distance from parts of the aircrafts structure. Additionally, the fabric must
have strength and elongation properties, and the coating must be able to maintain specific pressure
for a given time.Special attention is given as well to abrasion resistance and non-conductive
properties. Obviously, the most likely use of an evacuation slide is in an emergency, and it cannot
be the source of sparks that could ignite fuel, Layton said.Reeves is the leading supplier of
urethane-coated fabrics for the aerospace industry, according to Layton. The company supplies both
Boeing, the worlds largest manufacturer of commercial aircraft, and Airbus Industrie, the European
consortium that is the worlds other major manufacturer of jetliners.Reeves urethane-coated fabrics
are also used for other aviation applications including life rafts, life vests, fuel cells, deicers
and acoustical insulation. Automotive Airbags
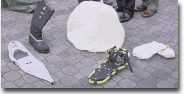
In addition to being the largest supplier of fabrics for certain aviation applications,
Reeves Brothers is also among the worlds largest suppliers of automotive airbag fabrics.Reeves
pioneered engineered, coated airbag fabrics and is the leading supplier in the North American
market, Layton said. As in aviation, quality and reliability are critical in the deployment of
airbags, he said. Reeves vertically integrated weaving and coating operations give the company the
ability to meticulously control all quality standards and ensure that all products are manufactured
to the most rigorous standards, he said.The company offers products used for driver-side airbags,
passenger-side airbags and side-impact airbags, and is working on a new, one-piece, woven
side-curtain airbag that would protect during a rollover event.In the event of a side impact, the
rollover curtain would deploy and remain inflated for the duration of the roll. The curtain covers
from the A-pillar to the C-pillar, meaning that both windows are covered during a roll. The product
has been designed initially for vans and sport utility vehicles, but, Layton said, it will
eventually be available for all cars.No doubt, automotive and aerospace applications are associated
with the glamour side of technical and industrial fabrics. But there is a more basic side one that
involves interaction with the day-to-day lives of nearly everyone.Frank Hannas, director of sales
and business development for the Engineered Fabrics group, said the company is a market leader in
the mechanical rubber-parts industry and supplies fabrics for gas meters, gaskets, diaphragms and
seals.For example, we make a rubber-coated nylon fabric that measures gas in gas meters. It used to
be that leather was used in the bellows in these meters, but we developed a fabric specifically
designed to replace the leather. It is now used in 98 percent of the meters in place today. Gas
meters are guaranteed for 30 years and, to this point, there has never been a failure of Reeves
fabric in one, said Hannas.A coated silk fabric from Reeves goes into the diaphragm of two-stroke
gasoline engines, such as those used in chain saws and weed eaters. And for military applications,
Reeves has developed a rubber-coated fabric for hovercraft skirts. This is a heavy-weight nylon
fabric coated with rubber that can be used as a replacement for skirts on Navy craft, Hannas
said. Military ApplicationsAdditionally, the company at the request of the military is
developing a fabric for flexible fuel tanks. These tanks are bladders that have capacities from
10,000 to 50,000 gallons. The objective is for the military to be able to drop the fuel tanks from
an airplane and enable helicopters in the field to land and refuel.Previously, fabrics tended to
disintegrate in the desert heat. Reeves is working on a rubber-coated fabric that withstands both
the impact of being dropped from an airplane and the heat inherent in a desert operation. This same
material must also be able to withstand extreme cold environments.Yet another military application
from the company is a rapid air decelerator product that would slow down missiles fired from
helicopters and enable the craft to get clear of the damage area. The fabric is earmarked for
anti-personnel/tank missiles and those that would be used to destroy runways.Other fabrics by
Reeves include those for dock seals, oil booms, truck tarps and rafts. Polyproylene From
LINQWhile companies such as Reeves concentrate on developing coated fabrics for technical
applications in automotives, aerospace and material handling, other companies, such as LINQ
Industrial Fabrics Inc., Summerville, S.C., focus efforts on polypropylene fabrics for geotextiles
and flexible bulk containers.Formerly a division of Exxon Chemical Co., LINQ is a global supplier
of woven and nonwoven polypropylene-based fabrics for a wide variety of textile applications.The
companys woven geotextiles feature a combination of high tensile strength and water flow. The
fabrics have been used in projects ranging from parking lot stabilization to retaining walls. LINQ
also offers a line of nonwoven geotextiles that provide high tensile strength and superior
hydraulic properties. StabilizationThe company used its GTF 200 woven geotextile, for example,
to stabilize the Miami Dolphins football stadium parking lot. Improvement was needed to meet the
increased demand for parking at the stadium. A field was selected to serve as an additional parking
area near the stadium. The original field consisted of unstable muck soils, from 6 to 20 feet deep,
which had to be stabilized to support suitable fill material. The expensive alternative, said Jay
Wilson, Technical Services Engineer at LINQ Industrial Fabrics Inc., was to excavate all of the
unstable soil and replace it with suitable fill.
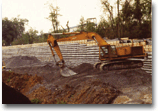
LINQs GTF 200, a high-survivability, general-use woven geotextile, was placed directly over
the soft subgrade and then covered with sandfill. The muck soil was covered with 25,000 square
yards of GTF 200. The geotextile was covered with 3 to 4 feet of fill, which was graded and
compacted. Grass was planted to complete the project. After six years, the parking lot is in
excellent shape, so plans were delayed to pave the lot.The contractor specified GTF 200 be used for
stabilization. This fabric meets the separation specifications in many states, as well as Class 3
separation requirements set by the American Association of State Highway and Transportation
Officials. Floodwall SolutionsLINQ also supplies fabrics used in floodwalls. In Kentucky, the
Environmental Protection Agency (EPA) proposed a concrete structure to protect a waste site from
floodwaters up to the 100-year storm elevation. The waste site is 300 feet from a nearby river. The
compressible subsoils made this concrete approach unfeasible. A second approach was a compacted
clay structure; however, with a maximum wall height of 38 feet and a minimum top width of 14 feet,
the required side slopes would make the base so wide that it would encroach on adjacent properties
and take up valuable landfill capacity.To overcome these problems, an engineer proposed a
geotextile-reinforced wall with near-vertical sides. This wall would also be compliant to
accommodate any settlement due to the compressible subsoils. There were some concerns because this
was to be a permanent structure, and the EPA had never installed this type of geotextile wall
before. Said Wilson: There was a substantial amount of coordination between LINQ and the designing
engineer to make sure the right geotextile was used in this application. LINQ has a full-time civil
engineer on staff to aid in all design applications and answer any questions concerning
installation, as well as helping get the right geotextile for the job.Using acceptable geotextile
design methodology, the engineer developed a double-sided structure consisting of layers of
permeable backfill reinforced with LINQ geotextiles. Each layer of geotextile was folded over and
secured beneath the next layer of backfill. The bottom 12 feet of the wall has 12-inch nominal
backfill layers reinforced with LINQ GTF 375N. The upper layers are 18 inches thick, reinforced
with LINQ GTF 300.The GTF 375N is a stronger fabric than the GTF 300 and was required to support
the weight of the higher layers. The final design called for an impermeable geomembrane and a
toe-drain system to be installed on the landfill side. The entire structure would be covered with a
puncture-resistant, nonwoven geotextile to protect the reinforcing fabric against physical damage
and ultraviolet degradation.The 1,735-foot-long wall, finished more than 10 years ago, is still
stable and meets all design objectives.LINQs manufacturing plant in Summerville is capable of
manufacturing up to 200 million square yards of fabric per year. Filling A NicheWhat each of
these companies Reeves and LINQ share in common is a flair for innovation, of meeting specialized
demands in markets in which few other companies have either the desire or the expertise to compete.
As evidenced by the developments of fabrics with significantly enhanced properties Reeves fuel
tanks, for example, or LINQs GTF 200 this commitment is paying off in enhanced sales and greater
market share. Hexcel Schwebel Weaves For PerformanceIn the world of high-performance fabrics,
DuPonts Kevlar® brand enjoys perhaps the widest name recognition among the general population no
doubt because of its association with lightweight body armor for law enforcement and military
applications.Kevlar was developed in 1965 by DuPont research scientists who were looking to create
a fiber with exceptional strength, but which was also lightweight and flexible. It is an organic
fiber in the aromatic polyamide family, also known as aramid. General features include high tensile
strength at low weight; high modulus (structural rigidity); high chemical resistance; high
toughness; high cut resistance; low elongation to break; low electrical conductivity; low thermal
shrinkage; excellent dimensional stability; and self-extinguishing flame resistance.Kevlar is five
times stronger than steel, weight for weight. It provides excellent impact resistance and is one of
the lightest structural fibers available. The product is commercially available in a multitude of
fiber physical property balances for specific end-use performance benefits. Originally available as
either Kevlar 29 for ballistic applications or Kevlar 49 for structural applications, today Kevlar
technology is available with physical properties developed to deliver enhanced performance in a
myriad of targeted end-uses. Examples of this are stab and puncture resistance, enhanced products
for body armor, improved military fragmentation technology, performance increases in cut-resistant
and cyclical motion (fatigue) applications, and improved products for structural and aerospace
needs.
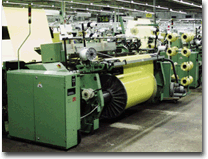
Despite the fact that Kevlar is used in a host of applications today, there was a point at
which DuPont was unsure exactly what it would do with the product. The fiber was originally
developed for use in automobile tires, but the emergence of a cheaper polyester alternative waylaid
that end-use. DuPont began to look for other applications for the product, and one of the companies
DuPont turned to for assistance was Hexcel Schwebel in Anderson, S.C.We were the first weaver in
the United States to weave Kevlar fabric for DuPont, said Ken Langford, marketing manager, Hexcel
Schwebel. We started weaving fabric specified for use in soft body armor in 1972.Today, Hexcel
Schwebel continues to weave Kevlar for a variety of applications, including ballistic protection,
safety apparel, recreation and aerospace.The company gets filament and a small amount of spun yarn
from DuPont and performs ring twisting and cable twisting in-house. The yarn is woven into fabric
on Sulzer rapier looms and is finished at the Anderson plant. We do scouring, water-repellent
treatment and some coatings here in Anderson, said John Leatham, North American sales manager,
ballistics.Because of Kevlars end-uses, the product must be handled with extreme care during
fabrication, Leatham said. Our challenge is to protect the properties of Kevlar as they exist when
the yarn comes in. It has to be handled very gently. Tension, abrasion, exposure to thermal cycles
all of those can impact the strength and performance of the fiber. We want to limit that impact
throughout the process and provide the opportunity to have a product that performs very well.As a
result, Hexcel Schwebel has improved each process preparation, weaving and finishing in order to
provide delicate handling of the fiber.We measure the properties of the product when it first comes
in, Leatham said, and then extract strands throughout the process to measure loss. Because of the
applications of Kevlar, our customers need process integrity, so we provide a substantial amount of
quality control testing on a lot-to-lot basis.Hexcel Schwebel keeps meticulous records of each
process so that traceability is never an issue. We begin with the certification we receive from
DuPont and then do our own random testing of incoming product, Leatham said. Then we have
traceability throughout our system from the bobbin to the finished roll. We can tell by roll number
everything that has happened to the product from the moment it comes in until the moment it leaves
the plant.In addition to Kevlar, Hexcel Schwebel produces a number of other high-performance
fabrics for various applications. The companys biggest market is fiberglass. Hexcel Schwebel weaves
fabrics for electronic, filtration and composites, as well as for general industrial use.
November 2001
National Acquires Glen Raven39 S Open-End-Package Dyeing Business
National Spinning Co., Inc., a leading US-based supplier of yarns, and Glen Raven Yarn Co., LLC confirmed today the acquisition, effective November 12, 2001, by National Spinning of Glen Ravens open-end spinning and package-dyeing business, including two plants located in Alamance County, North Carolina. The former Glen Raven plants, which will immediately be integrated into Nationals operations, will become known as the Alamance Spinning Plant and Alamance Dyeing Plant of National Spinning. Over 200 associates will be added to Nationals base of 1,600 owner-associates.The added capacity will enhance National Spinnings ability to service its customers. Commenting on the acquisition, Jim Chesnutt, president and CEO of National, stated, “Despite being in an environment that has not favored domestic textile producers, National is fortunate to be in a position to expand its core business. Chesnutt added, “This move will emphasize our commitment to US-based manufacturing and North American/Caribbean markets. We will continue to support our customers with the highest quality products and service, to assure their success in difficult markets.”Brookwood Associates Inc., investment bankers, of Charlotte, NC assistedNational Spinning with this transaction.National Spinning Co., Inc., an employee-owned company, was founded in 1921. In addition to the Alamance plants, National operates plants in Beulaville, Warsaw, Washington, and Whiteville, North Carolina, and LaFayette, Georgia. National and its Caron International subsidiary provide high-quality natural and dyed yarns for apparel, home furnishings, industrial goods, hosiery, automotive fabrics, and home-crafting. Glen Raven, Inc. is a highly diversified textile marketing, sales, and manufacturing company producing yarn and fabric for the awning, marine, casual furniture, industrial fabrics, apparel fabrics, and automotive fabric markets, through various subsidiaries, with manufacturing facilities in North America and Europe. The company is headquartered in Glen Raven, NC.
IFAI Flash Report
Flash Report
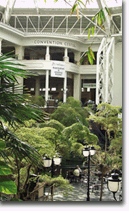
IFAI Expo 2001 was held at the Opryland Hotel and exhibit facility.
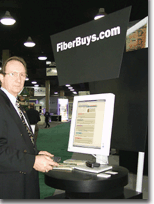
Honeywells Marvin Lewis represents Honeywell carpet fibers on FiberBuys.com.
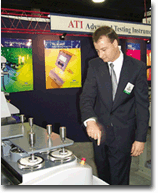
Reto Vogt, Advanced Testing Instruments (ATI), demonstrated latest testing
equipment. IFAI Expo 2001Exhibitors and visitors gathered in Nashville, Tenn., October 18-20,
at the Opryland Hotel and exhibit facility for the the Industrial Fabrics Association International
(IFAI) Expo 2001.Fridays keynote address by William McDonough, William McDonough + Partners,
Architects and Planners, focused on the eco-effective design agenda, which is revolutionizing
industries worldwide including the textile industry.The diversity of IFAIs membership was apparent
on the exhibit floor and also in the broad range of speakers invited to present during the
educational programs.
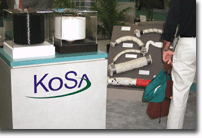
KoSa displayed its yarns and potential end-use products.
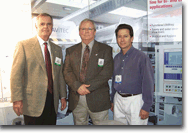
(left to right): Rick Horton, president, and Carroll Santos, sales representative – Cavitec,
both with American Santex Inc., visit with Scott Frisch, vice president, customer services,
Sclavos.
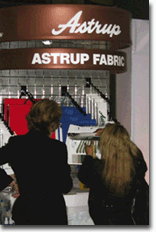
Astrup featured fabric and hardware for awning, sign, marine and other industrial markets.
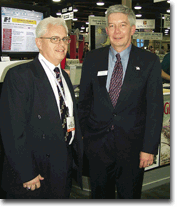
Opportunities for professionals involved in the military, safety and protective technical
fabrics industries. He is pictured with Stephen M. Warner, president, IFAI.
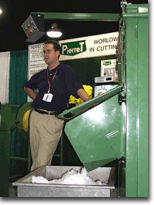
Todd Cooper, sales and marketing manager, Pierret, North American Division
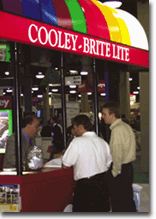
The Cooley Group designs, develops and manufactures high-performance materials for end-uses
such as safety clothing, medical products, truck tarps and illuminated signs.
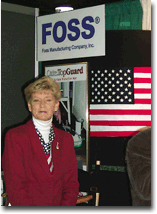
Trisha Mainella, customer service/planner, technical team, Foss Manufacturing Co. Inc.
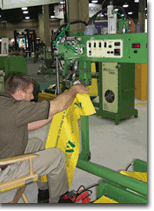
Mike Nastoff, Miller Weldmaster, demonstrated seaming technology for PVC, polyurethane,
polyethylene and polypropylene welding.
November 2001
Programmable Van Air Drain Valves Manage Any Fluid
Lake City, Pa.-based Van Air Systems Inc. has developed two Sentinel Series drain valves that can
manage any fluid by incorporating a clog-resistant, heavy-duty ball valve.The MDV-400L model valve
features a keypad for timing adjustments and a LCD cycle status readout to count remaining cycle or
drain open times. External test and valve fault functions are also included.The MDV-400I model is a
basic drain featuring a power on LED and test button. Cycle and open times are reset by adjusting
switches on the internal circuit board.Both valves run in programmable modes and can operate in
response to an optional liquid level sensor for zero-air-loss draining.Brass ball valves are
available in standard sizes of 0.5-, 0.75- and 1.0-inch narrow pipe thread (NPT). Sizes of up to 3
inches, stainless steel valves and electrical options are also available. Applications include
cooling towers, natural gas service, process tanks and more.
November 2001
Better Chemistry
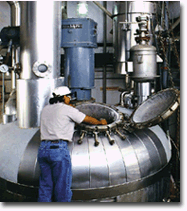
Better Chemistry
Textile chemical suppliers offer manufacturers value-added opportunities. Demand for
textile chemicals in the United States is expected to surpass $3 billion by next year, driven in
large part by the increased use of high-value formulations that increase production efficiency and
add value to fibers and fabrics.As the U.S. industry strives to compete in a global marketplace,
against odds outlined time and again in these pages, the industry is examining virtually every
facet of manufacturing to improve quality, efficiency and effectiveness.In this report,
Textile Industries looks at some of the chemicals and companies that provide the means for
more efficient manufacturing, whether in yarn and fabric preparation or in dyeing and
finishing.Bayer Corp., Pittsburgh, last year acquired Sybron Chemicals Inc., a U.S.-based producer
of polymers and specialty chemicals. This year, the company has announced significant worldwide
investment in its polymers and coatings business.Bayer plans to invest $1.6 billion globally in its
polymers segment, according to Werner Spinner, a member of the Board of Management of Germany-based
Bayer AG, the U.S. companys parent. Of this total, $1.3 billion will be assigned to new production
facilities, with the lions share going into expansion of polycarbonate capacities. The United
States continues to hold a key position for Bayer, he said. With a U.S. polymers market share
already totaling more than 30 percent, the company aims to invest another $250 million in the
polymers segment on top of a recent expansion program that totaled $2 billion between 1996 and
2000.Polymers are and will remain a core business for Bayer, Spinner said. We will continue to
build on our market leadership in the field of high-grade polymers. To this end, we will eliminate
capacity bottlenecks and exploit every opportunity for regional growth, while at the same time
analyzing and optimizing our portfolio and our cost structures.Among recent product additions for
the company is a low-temperature bleaching (LTB) system that produces results comparable to those
from conventional systems, but at lower temperatures and in less time. With conventional bleaching
systems, typical process temperatures range from 200°F to 230°F, depending on the substrate and
equipment used. But with Bayers LTB system, fabrics can be bleached effectively with hydrogen
peroxide at significantly lower temperatures. The most significant benefit associated with the new
LTB system is increased productivity, which is generated by significantly reducing the processing
time by as much as 1.5 hours, according to the company. It takes less time to heat the process
water, and the system has a neutral pH at the end of the bleaching stage, eliminating the need for
rinse and neutralization baths.The system can be used to bleach a variety of fibers and fabrics,
including cotton, viscose and nylon, as well as pH- and heat-sensitive blends. According to Bayer,
it eliminates the need for hazardous chemicals (hypochlorite and hydrosulfite) and has been proven
to improve fiber whiteness and fabric integrity.Bayer also offers Baysolex® RP and RP Assist, which
comprise a new generation of aftersoaping agents for reactive dyeings. A special enzyme system
removes color components from the unfixed dyestuff hydrolysate, saving water, energy and time,
according to the company. As well, the new products maintain or improve fastness properties. The
Baysolex enzyme system is primarily intended for deep shades, especially dyeings based on Reactive
Black 5 (black and navy). The system comprises Baysolex RP, an enzyme component, and Baysolex RP
Assist, a special process regulator. The products are generally added in the fourth or fifth rinse
bath after reactive dyeing, but the exact method depends on the customers operating
conditions.
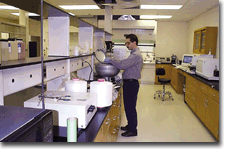
Seydel-WoolleyandCo. Inc., Pendergrass, Ga., has a full line of products for garment
processing and dyeing; preparation chemicals for knits and wovens; and dyeing auxiliaries for
indigo, cotton, polyester, acrylics, rayon, nylon, lyocell and blends. As well, the company
features a full line of finishing chemicals including resins, polyvinyl acetates, and many
hydrophobic and hydrophilic silicones. These silicones are used mostly as microemulsions, softeners
and bases, as well as lubricants, antistats and buffers.Seydel-Woolley has recently invested more
than $1 million in its laboratory to facilitate product development, according to Steve Adams,
president. We have the people, the technical support and the equipment in place to anticipate and
respond to the needs of our customers, he said.The companys Seycote SR-25R is a polyester
dispersing and antiredeposition aid designed to provide maximum dye antiredeposition properties in
garment wet processing and other washing and scouring systems. It can also be used as a
dye-leveling agent when used with disperse dyes on polyester and blends.Seyco Finish ESA Liquid is
a liquid film former based on a highly soluble and resoluble carboxilated starch of low viscosity.
It was designed to be applied as a hand builder for fabrics made from cellulosic fibers, especially
indigo-dyed denim. The product is used, as well, to stabilize elongation and shrinkage of finished
fabrics.Seyco Antizone is a complex cationic liquid softener specifically designed to provide
ozone- and ultraviolet (UV)-inhibition properties. According to Seydel-Woolley, it features
excellent antiozonate/UV inhibition on denim, is non-yellowing and does not alter shades. It
creates excellent hand and works well as a general-purpose softener for wovens or knits.A
microemulsion silicone designed to provide an extremely soft hand and increase color vibrancy,
Seyco Soft LM-5 will blossom dyed shades and make them appear darker. The product will not
adversely affect crockfastness and will not cause spots.Seyco Scour LFB is a low-foaming,
biodegradable wetter/scouring agent used for desizing, scouring, bleaching or dyeing. The product
can be used with alpha amylase or cellulose enzyme with decreasing enzyme
performance.Seydel-Woolleys Seyco Wetter 2EH provides detergent emulsification when used in
preparation dyeing and finishing. It is an effective scouring agent with penetrating properties
that make it useful for dyeing marginally prepared or difficult-to-wet-out goods. In continuous
indigo dyeing of denim, it has excellent wetting with low foaming, according to the company. The
wetter emulsifies wax and oils; is caustic-stable; can be used in exhaust or continuous dyeing;
features instant penetration for dyeing; can be used for jet-dyeing applications on all fibers and
most dyestuffs; and is excellent on indigo dye ranges in a sulfur dye mix or in finishing as a
wetter in the sulfur dye mix.Seyco Wetter IFR is a nonionic wetter and scouring agent designed to
remove loom oil from griege fabric. As well, the company says it performs well as an after-scour
for dyed goods. The product works on natural and synthetic fabrics, and is readily soluble in
water, resistant to hard water and metallic salts, and resistant to acids and alkalis.A one-piece
finishing system from Seydel-Woolley, Seyco Lube YLW, contains a nonionic wetter, an ester-based
sanforizing lubricant and a polyethylene softener. This combination enhances hand and provides
excellent wetting and fiber-to-fiber-to-metal lubrication.Seyco Lube SR is a nonionic-based
lubricant that prevents streaks in denim-dyed garments. It can also be used with fiber-reactive,
direct or acid dyes. The product can increase load size without streaking and can help prevent
broken stitches and nicks on heavily abraded garments.Seyco LEV HTP, a leveling agent for disperse
dyes, is widely used on polyester and polyester blends dyed on jet-dyeing machines at elevated
temperatures in the 240°F to 265°F range.Other offerings from Seydel-Woolley include Seyco HB-55, a
milky-white polymeric emulsion that builds hand and provides dimensional fabric stability to knits;
Seyco Fix Right, a non-formaldehyde fixing agent for direct and fiber-reactive dyeings that
increases washfastness, maximizes wetfastness and prevents migration during drying operations;
Seycozyme NEC, a buffered neutral enzyme blend designed to provide the same properties of liquid
acid or engineered acid cellulase enzymes without the deleterious effects on fabric strength
sometimes found with acid cellulases; Seycozyme L-2020, a high-strength, bio-engineered cellulase
enzyme system for both textile and industrial use; and Seycozyme HCE, a high-strength, acid-stable
cellulase enzyme effective on cotton and all natural and cellulosic fibers and blends.Additionally,
the company offers Seyco Sperse SPW, a concentrated mixture of low-molecular-weight polyesters and
other polymeric dispersing and antiredeposition agents; Seyco Defoamer 2341, which is a 40-percent
active non-silicone defoamer for textile dyeing; Seyco Defoamer AJA, a 100-percent active
non-silicone defoamer; Seyco Desize 2K, a 4X-strength thermal-stable alpha amylase effective in
removing starch; Seyco Buffer IDB, which is designed to provide the optimum pH for indigo dyeing to
give consistent shades in both rigid and wash-down shades; Seyco Buffer 480, a concentrated liquid
buffer that maintains pH from 4.5 to 5.0; Seyco Antimigrant 347, a liquid, sodium alginate-based
product for use in the prevention of dye migration; and Seyco Cat MC, a catalyst for thermosetting
glyoxal reactants based on magnesium chloride. Another company, Cognis Corp., (formerly
Henkel Textile Technology), Charlotte, N.C., offers chemical solutions that span the entire process
chain from spinning preparation for fiber and yarn production; through pretreatment, dyeing and
printing; to the finishing of the end product.
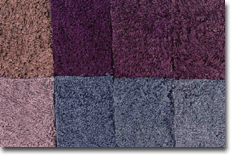
Chlorine fastness evaluation on 100-percent cotton towels.1.5-percent owb fixative (Cognis
Chromaset CBF) was applied. Towels were dried at 300°F4A Wash Test with chlorine was performed at
160°F.Courtesy of Cognis Corp.Among the specific products manufactured by the company is
Syntergent® APW, a low-foam scouring agent and penetrant designed for use on natural and synthetic
fibers and blends. It provides detergent emulsification and wetting properties when used in
preparation, dyeing and finishing. Syntergent SL CONC provides the same properties for use in batch
and continuous preparation of knit fabric. Syntergent TER-1, as well, is a scouring agent and
penetrant for use on natural and synthetic fibers and blends. During continuous indigo dyeing of
denim, the product imparts wetting properties without causing excessive foaming. Securon® 540
from Cognis is a bleaching and dyeing assistant designed specifically to prevent the formation of
silicate scale in alkaline bleach baths containing sodium silicate. In addition, it inhibits the
formation of insoluble fats and waxes from cotton and prevents their precipitation on the
manufactured goods. Stabilol® HCN is a multifunctional bleaching assistant for use in continuous
and batch operations in both cotton and polyester/cotton woven goods and knits. Stabilol HCN
eliminates the need for silicate in the system.Other products offered by Cognis include: Osimod®
CLD, a dyebath dispersant and leveling agent that can be used to disperse oligomer and prevent
redeposition on the fabric; Chromasist® 1487-A, a dispersant and leveling agent that minimizes dye
agglomeration without causing excessive foaming; Chromaset® CBF, a chlorine barrier that has
anionic ionicity and no reportable levels of phenol or formaldehyde compounds; Nonax® 1166, a
durable polymeric antistat; and Foamaster® 340, a non-silicone defoamer designed for use in jet- or
pressure-dyeing machines.CHT R. Beitleich (formerly Catawba-Charlab Inc.), Charlotte, has
introduced Sarabid LDR, a dispersing agent with sequestering and leveling properties for improving
the solubility of reactive dyestuffs. The product features low foaming and good salt stability and
is suitable for exhaust or continuous dyeing.CHT R. Beitleich also manufactures a variety of
softeners and lubricants; dyeing auxiliaries; printing auxiliaries, binders and block-outs;
binders; coatings; pretreatment products; and colors and pigments.
November 2001
Hartmarx Acquires Consolidated Apparel
Chicago-based Hartmarx Corp. has acquired the Consolidated Apparel Group, New York City.We are very
excited to have Consolidated Apparel Group as part of the Hartmarx family, said Elbert O. Hand,
chairman and CEO, Hartmarx. Its wide range of sportswear offerings are sold at price points and
serve distribution channels which complement our current sportswear lines. Consolidateds revenues
have been growing, now exceeding $50 million annually, and its results are expected to have a
positive impact on Hartmarx earnings.Perry Wolfman, principal owner of Consolidated, continues as
president. He reports to Homi B. Patel, president and COO, Hartmarx. Consolidateds management team
continues to report to Wolfman.
November 2001