S
täubli Corp.’s open house – held recently at the company’s US headquarters in Duncan,
S.C. – was well-attended. The company exhibited its latest warp-preparation systems including the
Opal automatic warp leasing machine, Delta 110 automatic warp drawing-in machine and Topmatic
automatic warp tying-in machine; and shedding-motion systems including Rotary Dobby 2881 and
jacquard machines DX 110, LX 3202, and Unival 100. The DX 110 and LX 3202 are equipped with a new,
improved patented M6 module and a new JC6 electronic controller. The Unival 100 also is equipped
with a JC6 controller.
.
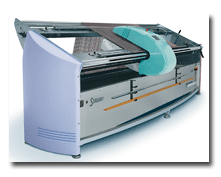
speeds of up to 100,000 threads over an eight-hour period.
Warp Leasing
The leasing process prepares the warp yarns with a desired sequence and maintains that
sequence for the automatic drawing-in or tying-in process. The Opal automatic warp-leasing machine
– introduced at ITMA ’03 in Birmingham, England – processes up to eight single- or multiple-color
warp sheets usually prepared by direct warping process into a single leased sheet. The Opal,
capable of handling single or plied spun yarns and flat or twisted continuous filament yarns, can
lease warps up to 230 centimeters wide.
One operator is required to set the warp on the Opal’s frame, program the required warp
color sequence and yarn type for each color, and run the machine to start leasing. Then the
automatic leasing begins, and operator presence is not required until that process is completed.
Observing the programming of the Opal through a user interface via a color screen indicated easy
operation and full user color identification control. The machine displays a magnified color image
of good resolution for individual yarns so the user can recognize color and yarn type. The user
identifies a yarn color to the machine by touching one of up to 10 different colors available on
the user-defined panel.
The machine is equipped with two cameras to check for double yarn and color. The foremost
yarn in the warp is picked up by an air suction nozzle. The color recognition ensures correct
desired sequence of the yarns in the lease. If a yarn with a different color than that programmed
is picked, the yarn will not be leased, and the machine continues the leasing process until the
yarn of such color is required in the sequence. Depending on the application, the leasing speed of
the Opal is up to 100,000 threads per eight hours. If the warp contains single and plied yarns, and
thus yarn type recognition is required, the leasing speed range is 30,000 to 60,000 threads in
eight hours. The highest speed of 100,000 threads per eight hours can be achieved when leasing a
single-sheet warp. The range of yarn linear density that the machine can handle is 10 to 50 tex.
The Opal enables weavers employing direct warpers to produce striped warps as easily as
those using sectional warpers. Other recognized advantages of the Opal are the significant
reduction in labor cost; removal of a bottleneck in warp preparation, as it replaces the manual or
semi-automated warp leasing systems; capability of manufacturing intricate woven fabric designs;
and response in quick mode to short orders and frequent style changes.
Jacquard Machines
Stlis new DX 110 and LX 3202 jacquard machines are equipped with the M6 module and JC6
controller. The DX 110 also features a capacity of 1,408 or 2,688 hooks, easy access to centralized
lubrication points, and vacuum cleaning of the fan filter without the need for disassembly. The LX
3202 is available in a broad range of capacities 6,144, 8,192, 10,240, 12,288 and 14,336 hooks. The
filter and fans in the LX 3202 are mounted vertically to avoid lint accumulation, and the
maintenance program is automatically managed by the JC6 controller.
M6 Module
Stäubli’s new DX 110 and LX 3202 jacquard machines are equipped with the M6 module and JC6
controller. The DX 110 also features a capacity of 1,408 or 2,688 hooks, easy access to centralized
lubrication points, and vacuum cleaning of the fan filter without the need for disassembly. The LX
3202 is available in a broad range of capacities – 6,144, 8,192, 10,240, 12,288 and 14,336 hooks.
The filter and fans in the LX 3202 are mounted vertically to avoid lint accumulation, and the
maintenance program is automatically managed by the JC6 controller.
JC6 Controller
The new jacquard machines are provided with an improved, more compact JC6 controller. The
user interface is accomplished via a color touch screen. The JC6 is provided with a flash disk as
opposed to the hard drive used with previous controllers. It allows pattern loading via universal
serial bus, external drive, and/or networking for compatibility with the latest computer file
communications and storage. The realized advantages for networking include weaving-room management
locally or remotely from anywhere via Internet access.
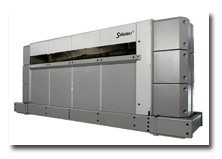
to reach never-before-seen jacquard weaving machine speeds.
The Unival 100
A prototype of the Unival 100 jacquard machine was unveiled at ITMA ’99 in Paris. The
machine was shown at ITMA ’03 in commercial form, and several machines have been sold since then.
In 2003, the Unival 100 was demonstrated running on a Picanol Omniplus-6-J 250 weaving machine
producing mattress ticking and table cloth fabrics at a filling insertion rate of 2,460 meters per
minute – the highest speed in jacquard weaving history. The reason behind such a high speed is the
control of each harness cord by a stepping motor, termed Jactuator, which eliminates the
electromagnets, movable and retaining hooks, and pulleys. The Jactuator raises or lowers a harness
cord, or warp end, by rotating its pulley. The module in the Unival is the assembly of 16
Jactuators.
The Unival design permits easy-to-set features including formation of different sheds –
symmetrical, asymmetrical, shifted, venturi and multiple – and shed height. All settings can be
conducted electronically through a user interface with the JC6 controller. Another significant
feature of the Unival is its independence from the weaving machine drive because it has its own
drive without mechanical coupling to the weaving machine. The Unival modular construction enables a
jacquard capacity range from 6,144 to 20,480 hooks.
The new developments in shed-formation and warp-preparation systems enable weavers to
explore new opportunities, weave industrial and intricate designs at the speed of commodity
fabrics, respond quickly to style change and produce short runs economically. These innovations
also set the stage for weaving machine manufacturers to increase weaving speed to new levels..
Editor’s Note: Abdel-Fattah M. Seyam is a professor in the department of textiles and apparel,
technology and management at North Carolina State University’s (NCSU’s) College of Textiles,
Raleigh, N.C.