A
fter the first and very successful International Exhibition of Textile Machinery (ITMA)
Asia in Singapore in 2001, many so-called opinion leaders predicted the traditional ITMA in Europe
would be out of favor. However, recent textile machinery association presentations suggest European
textile machinery suppliers did their homework and are ready for a successful ITMA 2007 in Munich
this September.
The European Committee of Textile Machinery Manufacturers (CEMATEX) was founded on Oct. 20,
1952, to concentrate the textile machinery market at one trade fair venue. The first attempt to
hold an international textile machine exhibition had been in Lille, France, in 1951. The show had
floor space of approximately 12,000 square meters (m2), and some 280 exhibitors took part. Since
that time, ITMA has been held at different sites in Europe every four years
(See Table 1).

the venue for ITMA 2007.
Most Important Textile Machinery Show
Over the years, ITMA has gained importance and today is the most important meeting place for
the textile machinery industry. ITMA gives an overview of innovative technology and the latest
information available. It is owned by CEMATEX, which in turn hands over responsibility for
organizing each trade fair to one of its member associations. ITMA has very strict rules: It is one
of the few machinery exhibitions in the world that demands exhibitors bring a new exhibit. This
rule guarantees a high standard of new technology at ITMA shows.
In view of the booming markets in Asia, ITMA inaugurated its sister show, ITMA Asia, in
Singapore in 2001. This venue was chosen for its easy access by visitors around the globe. The
event became an instant success. After two consecutive shows in Singapore in 2001 and 2005, the
next ITMA Asia will be held in Shanghai in 2008. CEMATEX made the decision to change the show’s
venue, and also to combine it with the biennial China International Textile Machinery Exhibition
(CITME) show held in Beijing, to underline the importance of the Chinese market.
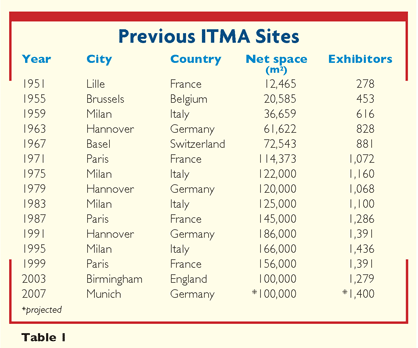
Munich: The Place For Innovation
aim is to show new exhibits that answer upcoming challenges in the textile chain — from fiber
preparation to apparel. More than 1,400 exhibitors have already booked more than 100,000 m2 of
exhibition space, an increase compared to ITMA 2003 numbers. Of great value for the show and the
visitors is the fact that producers of knitting and warp knitting machinery — totaling more than 70
exhibitors — are back at ITMA.
The net exhibition area of Asian companies already surpasses the value of 2003 by 19 percent
with more than 11,500 m2. Suppliers from China, India and Japan have booked substantially larger
areas than at ITMA 2003. Registered exhibitors from Turkey have increased approximately 10 percent.
Seventy-five percent of total floor space is booked by companies from Italy, Switzerland and
Germany.
As the textile industry grows and changes, European textile machinery manufacturers face an
increased demand for high-performance machines and systems. Substantial need for replacements and
modernization, especially in newly industrialized and developing countries, strengthen this trend.
On the other hand, energy costs have a significant impact on production costs and
competitiveness in the textile industry. Energy savings, reduced consumption of water and
chemicals, low maintenance, and recycling are just a few key concerns. These issues are at the top
of the priority list for European textile machinery manufacturers. In this context, CEMATEX member
countries Switzerland, France and Germany recently invited journalists to press conferences with
the purpose of unveiling ITMA highlights. Italy’s Association of Italian Textile Machinery
Manufacturers (ACIMIT) also shared information about Italian exhibitor innovations that will be
displayed at ITMA.
Switzerland To
Showcase A Wide Array At ITMA
Traditionally, Switzerland has been among the leading global producers of textile machinery.
Forty-three suppliers are members of the Swiss Mechanical, Electrical and Engineering Industries
(Swissmem) Textile Division, a founding member of CEMATEX.
President Christian Kuoni opened Swissmem’s recent pre-ITMA meeting, which was organized by
General Secretary Dr. Lukas Sigrist and his team. Swiss textile machinery means innovation to
Kuoni, and not only because this is the slogan for ITMA 2007. He mentioned that all important
developments in the last 40 years were made in Switzerland. “ITMA is the place for innovations,” he
said. “And today and tomorrow you will see a lot of innovations.”
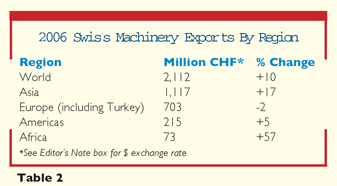
Tables 2 and 3 show the importance of Swiss textile machinery exports in 2006 — the export
share is 99 percent.
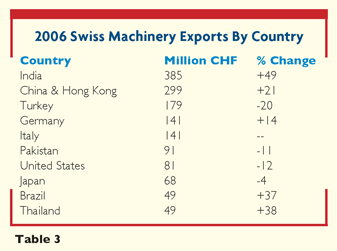
Asia is still the most important market for most Swiss companies. China and — more and more —2
2 s s 2 s s 2 s 2 s s 2 s 2 s 2 s 2 2 s 2 I ndia are playing very big roles as contributors to
turnover. However, for technical textile applications, the United States and Europe remain the main
markets.
Swiss textile machinery manufacturers’ exports rose by 10 percent in 2006 compared with
2005, and reached a total volume of CHF 2,112 million
(See Editor’s Note for $ exchange rate). Forty percent of all exports go to Asia. While
exports in the first half of the year already were 8 percent above 2005, this positive result was
topped by another 11 percent in the second half. The most significant impact again came from the
Asian markets, which enjoyed a gain of 17 percent, resulting in a market share of 53 percent.
Added-Value In Demand
To remain cost-competitive, mainly in Asian markets, most Swiss manufacturers have their own
production sites in China. What was considered to be a negative aspect in the past is today
communicated as a price advantage.
The rising market share of machinery for technical textiles and nonwovens was apparent in
most of the Swissmem presentations. Some companies already achieve 40- to 50-percent of turnover in
the technical textiles sector. Also featured in many presentations was the goal of reducing energy
costs and waste. With rising raw material costs, almost every ounce of material needs to be
reclaimed and brought back into the production process. Swiss companies will show some new
developments at ITMA that aim to save on raw materials.
Another key point brought up at the Swissmem meeting: The markets are requesting more and
more turnkey installations, driving each machinery manufacturer to become a system supplier.
Strategic alliances on all levels — and cooperations between companies to supply and build turnkey
installations — are in demand. Many acquisitions in the past few years were executed based on this
market need.
After company presentations at the Swissmem event, the trends were very clear: quality,
flexibility and service are no longer sales arguments, but prerequisites for success. Included in
the service package is the possibility to conduct extensive trials for new products in the
supplier’s laboratory. This is very important; the market is constantly demanding new products,
mainly for industrial applications. All Swiss suppliers are expecting a lot from ITMA, and all
agreed and are convinced that the European textile industry is strong and will remain strong. The
actual positive sales trends underline this fact and will support the Swiss manufacturers’ market
share.
Textile Machinery À La Française
France is a country with a long-standing textile tradition. Today, it ranks fifth on the list
of the world’s top exporting textile machinery manufacturers. On the occasion of a presentation at
this year’s Techtextil in Frankfurt, the French ITMA exhibitors declared themselves to be ready for
the trade show in Munich.
The French textile machinery builders are integrated in the French Association of Textile
Machinery Manufacturers (UCMTF). Approximately 8,000 people are directly or indirectly active in
this industry. Bruno Ameline, UCMTF president, said French textile machinery manufacturers spend 8
percent of their turnover on research and development. In 2006, the 35 French producers achieved a
turnover of 1.2 billion euros
(See Editor’s Note for $ exchange rate). This is a global market share of approximately
6.5 percent that continues to rise. The export breakdown in regional markets is shown in Table 4.
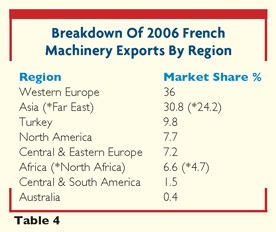
Japan, with 11.4 percent of market share, is the largest market; followed by Belgium, 10.8
percent; Turkey, 9.7 percent; Italy, 9.1 percent; China, 7.5 percent; the United States, 6.5
percent; and Germany, 6.2 percent. Ameline mentioned that many machines become re-exports to Asia.
India, with 3.2-percent market share, and Russia, with 2.1-percent, also are promising markets. The
breakdown by sectors in 2006 is shown in Table 5.
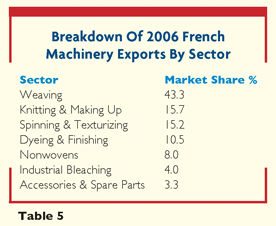
Sustainable Growth, Changing Needs
Ameline also referred to rising energy costs and growing concerns about the environment.
Registration Evaluation and Authorization of Chemicals (REACH) regulations of the European Union,
adopted in December 2006, are still the talk of the town. In accordance with a German study, the
energy costs from 1998 to 2006 roughly doubled from 5 percent to 10 percent.
The French machinery manufacturers also see a rising demand for technical textiles. “Also in
this sector we have specialists who operate in very successful ways,” Ameline said. “For many
years, NSC nonwoven and Rieter-Perfojet have been producing machines and lines for the production
of accurate nonwovens. And on recycling lines from Laroche, nonwovens are produced for all types of
technical textiles for applications such as felts, mats and geotextiles.”
The French manufacturers have invested a lot of effort in the forthcoming ITMA in Munich.
“We want to show the world that we can offer high-tech machinery for high-tech markets,” Ameline
said. “In France, we don’t have any large machinery groups, but there are very active and
specialized small and medium-sized enterprises that operate very successfully in the global
markets. We are ready, and are looking forward to ITMA 2007 with great expectations.”
The German Perspective
The German Engineering Federation (VDMA) Textile Machinery Association held a lively
discussion among the VDMA committee and journalists present during a pre-ITMA meeting. One thing
became clear: One can see a lot of new products from German companies. Those present at the meeting
gave some hints, however, that most companies aren’t ready to unveil their new machinery until the
show.
Germany has been the world’s number-one supplier of textile machinery for a long time. After
a weak year in 2005, the German textile machinery industry is back on the road to success. “With
exports worth 3.6 billion euros, the industry reached an increase of 6 percent compared to last
year,” said Johann Philipp Dilo, chairman, VDMA Textile Machinery Association’s Executive Board.
“We are also expecting an increase of some 13 percent for the current year.”
Approximately 310 German companies will exhibit at ITMA 2007. This represents an increase of
34 percent when compared to ITMA 2003. The area booked by German exhibitors totals 29,567.5 m2, an
increase of 25 percent over 2003. Everybody agreed that Munich is an ideal location for ITMA.
Top export markets for Germany are China, with a 28.6-percent share; and India, with 11.8
percent. China and Hong Kong accounted for shipments worth 929 million euros, leaving China as the
undisputed top market for German textile machinery. For additional 2006 VDMA textile machinery
export statistics by country, region and sector, please see ”
Textile World
News,” this issue.
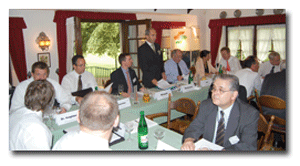
for organizing ITMA 2007 in Munich, held a lively discussion among its committee members and
journalists present during a pre-ITMA meeting.
The ITMA For Everybody
For the first time since 1991, Germany will host ITMA. “Our goal is that everybody can come
to ITMA in Munich,” said Thomas Waldmann, managing director, VDMA Textile Machinery Association.
“For this, we have prepared all information in 10 languages. Many people would like to see the
Oktoberfest after ITMA — that’s another challenge. Not to be forgotten is Ramadan. Many exhibitors
and visitors are Muslims, and we take this fact very seriously and will do everything to meet their
requirements. To make an easy access to Munich for everybody, we informed most of the countries
around the world that we are expecting a lot of visitors and we kindly requested all authorities to
issue visa applications in a very easy way.”
All companies at the VDMA meeting agreed that ITMA is still very important because visitors
can compare the machinery in one place. That’s why ITMA is still the top event for sales. “We show
three complete lines,” said Dilo, who is also managing director of ITMA exhibitor Oskar Dilo
Maschinenfabrik KG. “For this reason, our customers can see not only machinery, but also products.”
Producers of knitting machinery are back exhibiting at ITMA after their absence in 2003. “We
have had a very good response that the knitters are back at ITMA,” said Gerhard Berger, director,
advertising and communication, H. Stoll GmbH & Co. KG. “Many customers came back, from Europe
and Asia too. And we, as Stoll, must show our presence.”
Everybody wants to show faster and better machinery at ITMA. According to Peter Dornier,
owner of Lindauer Dornier GmbH, his company will show a so-called concept machine, which should be
a center point for discussions about the future for textile machinery.
It’s vital for Heinrich Trützschler, managing partner, Trützschler GmbH & Co. KG, that
the exhibition is taking place in a country where production is still an important factor of the
gross domestic product. “There must be an ITMA in Europe,” Trützschler said. “Europe is still the
place for innovation. All new developments are still made with European customers.”
“The finishing companies in Europe are very successful today,” said Regine Brückner,
managing director and co-owner, Brückner Trockentechnik GmbH & Co. KG. “With our new machines,
one can save up to 35 percent in energy. This is a lot if the actual energy costs are taken into
consideration.”
“All present companies here at this table are market leaders in their sector,” Dilo said,
wrapping up the VDMA event. “The machines become more powerful, and a lot of money is invested in
research and development. But there is still a lot of education needed. For example, we as a
manufacturer of needling machines know that needling is the most cost-efficient technology to form
a textile substrate. With an annual increase in our turnover of 6 percent, we can see that many
customers already know this fact. However, we have to keep the pace so ITMA and our companies
remain at the top of the list.”
The German Engineering Federation (VDMA) Textile Machinery Association, responsible for
organizing ITMA 2007 in Munich, held a lively discussion among its committee members and
journalists present during a pre-ITMA meeting.
Italy Ready For ITMA 2007
The number of Italian companies attending ITMA 2007 is approximately 355 — 13 percent more
than attended ITMA 2003. Italy ranks second in the world in exports of textile machinery,
outweighing countries that have a long tradition in the manufacture of textile machinery, such as
Japan and Switzerland.
Moreover, the Munich edition is taking place at a time that is expected to confirm the
recovery of the whole textile machinery sector worldwide — and, in particular, of the Italian
sector, which closed 2006 with quite positive results.
In 2006, Italian textile machinery production recorded an increase of 4 percent over 2005
figures, for a total of 2,680 million euros. A similar increase occurred in exports, which reached
a value of 2,100 million euros — 3 percent higher than in 2005. The Italian market saw a rise in
orders of 33 percent.
Export figures reported by ACIMIT confirm the consistency of the major Asian markets,
especially China and India. These two countries are the main destinations for Italian machinery,
accounting for about 30 percent of all exports. The year 2006 was also characterized by a global
increase in sales to Latin America and Africa.
Italy also saw a recovery in 2006 in its domestic market, where the demand for textile
machinery exceeded 1,150 million euros — an increase of 4 percent over 2005.
“The ITMA in Munich will offer the opportunity to display the Italian machine sector with
its highly competitive production, which succeeded in maintaining its leadership worldwide,
notwithstanding the difficult economic conjuncture, thanks to its appreciated peculiarities such as
quality, creativity, reliability, and to the high level of the offered technology,” said Paolo
Banfi, president, ACIMIT.
The Italian textile machinery industry is claiming a leadership position, partly because of
its constant cooperation with the Italian textile and fashion industry. This relationship plays a
particular role in the finishing machinery sector, which realized a turnover of some 560 million
euros in 2006 — 21 percent of total turnover. More than 78 percent of turnover is generated by
exports, which in 2006 totaled about 440 million euros. Main export destinations for Italian
finishing machinery are India, with 39 million euros; China, with 31 million euros; Turkey, with 31
million euros; Germany, with 22 million euros; and the United States, with 22 million euros.
“Within the sector of machines for processing semifinished materials, the open-width lines
manufactured in Italy in the last decade for the continuous washing of woolen fabrics are of
particular interest,” Banfi said. “These lines established themselves worldwide, and their
manufacturers attained the leadership in the field of solvent washing thanks to their sophisticated
technologies.
“Our sector underwent in the last years a deep transformation, but could find inside itself
the motivations and the resources from which to draw the strength for resuming a winning course,”
he added. “It is an irrefutable fact that the textile machinery industry, with a favorable balance
of trade amounting to 1,520 million euros, is the feather in the cap of the instrumental mechanics
of our country and is at the same time a sector of strategic importance for the future of our
economy.”
Editor’s Note: As of
Textile World‘s press time, exchange rates were as follows:
1 CHF = $0.83
1 euro = $1.38
July/August 2007