-I Exhibitors 3M Abrasive Systems Division, St. Paul, Minn., will exhibit drive and pull roll
coverings made from engineered polymers and available in smooth, textured and bristle surfaces;
unique methods that do not use glues or chemicals to attach coverings to drive and pull rolls; and
abrasive solutions featuring 3M bristle technology for maintenance repair operations. Primary
contact in booth: Jim Kessinger. Booth No. B-1411.AC Corp., Greensboro, N.C., will exhibit the
Z92000, a complete HVAC system to keep precise environmental control of temperature, humidity and
cleanliness at a low cost. Primary contact in booth: Ron Howerton. Booth No. A-228. Air Relief
Inc., Mayfield, Ky., specializes in remanufactured parts and services for Ingersoll-Rand Centac Air
Compressors. Primary contact in booth: Kerry Williams. Booth No. B-1421.Albatross USA Inc., Long
Island City, N.Y., will be displaying its full line of Mistral® Spot Cleaning Chemicals and
equipment. Albatross will demonstrate Mistral XS Textile Cleaning solvent that has been
reformulated without 1,1,1 trichloroethane. Primary contact in booth: Jay Margulies. Booth No.
A-113.American Cutting Edge, West Carrollton, Ohio, will display blades and knives for all types of
cutting applications. Primary contact in booth: John Ramantanin. Booth No. B-1222.American Filteco
Machinery Corp., Marietta, Ga., will exhibit BCF extrusion equipment and winders for the carpet and
textile industries. Primary contact in booth: Larry Hummer. Booth No. B-1316.American Linc Corp.,
Gastonia, N.C., will show the CV-35 frieze yarn/coiled yarn conversion system for processing spun
yarn, BCF, nylon, polyester and polypropylene. Other equipment to be displayed includes the EFT-900
even feed tensioner and the MVS-600 mechanical yarn sensor, which is a low-maintenance replacement
for traditional photo eyes. Primary contact in booth: Ryan Hoover. Booth No. B-1302.American
Moistening Co., Pineville, N.C., will exhibit humidification systems including space, air-assist,
high-pressure and custom-designed humidifiers. Primary contacts in booth: Hal Wilson and Dave
Kelsey. Booth No. D-2219.Amsler-Tex AG, Switzerland (Symtech Inc., Spartanburg, S.C.), will display
yarn-effect devices for ring-spinning and open-end frames as well as core-yarn devices for
ring-spinning frames. The company also offers software and hardware for all types of fancy yarn
creation and visualization. Primary contact in booth: Peter Egli. Booth No. D-2100.Argus Fire
Control, Charlotte, N.C., will have among its exhibits automatic fire-protection systems,
metal-detection systems, and building fire alarm and security systems, as well as card access
systems and the Odyssey Intelligent Fire Control system. Primary contact in booth: Mike Viniconis.
Booth No. D-2619.Ashworth Card Clothing Inc., Greenville, S.C., will be exhibiting metallic wire
for cotton and nonwoven carding. The company also supplies card parts and offers card roll repair
and card clothing installation. Primary contact in booth: Carlton Reeves. Booth No. C-1700,
C-1701.ATI (Americas Textile Industries), Atlanta, will offer copies of the magazine (including
Fiber World and Knitting/Apparel), which features extensive reports and information on ATME-I 2000.
Primary contacts in booth: James M. Borneman, Editor In Chief; James C. Phillips Jr., Executive
Editor; Eric Vonwiller, Senior Technical Editor; Marcella Nacmias, Associate Publisher and Vice
President, International Operations; and Denise Buchalter, Advertising Business Manager. Booth No.
C-1625.Atkins Machinery, Spartanburg, S.C., will exhibit used textile machinery and Schlafhorst
open-end parts. Primary contact in booth: Greg Atkins. Booth No. D-2531, D-2540.Autefa GmbH,
Germany (Fi-Tech Inc., Richmond, Va.), will offer solutions for complete package automation
including doffing, transportation, storage and packing. Also featured will be automatic
staple-fiber bale presses and bale storage solutions. Primary contact in booth: Udo Teich. Booth
No. D-2617.Awa Spindle Co. Ltd., Japan (Izumi International Inc., Greenville, S.C.), will show
twisting spindles, covering spindles and interlacing nozzles. Primary contact in booth: Ken Overly.
Booth No. D-2604.Bahmer Machine Works, Germany (W. Fritz Mezger Inc., Spartanburg, S.C.), will show
a spiral can coiler that is adaptable to any type of carding machine. Primary contact in booth:
Fritz Mezger. Booth No. B-1426.Bamco Belting, Greenville, S.C., will present nylon and leather
belting for conveyors and various other types of applications. Primary contact in booth: Don James.
Booth No. A-202.Barco Automation, Charlotte, N.C., will present equipment for the detection and
elimination of contaminants in the spinning plant. This includes the Cotton Sorter for the blow
room, Sliver Watch for drawframes, and ABS foreign fiber detection on open-end spinning machines.
The company will also highlight its Barcoprofile optical yarn-measurement systems, which can be
used on air-texturing machines, air-entangling machines and sewing-thread machines. The Opti-Spin
detection system for ring-spinning machines, Opti-Twist speed-control system for twisting machines,
KIT sliver information system for cards and drawframes and Sycotex system for spinning plants are
other equipment that Barco will emphasize. Primary contact in booth: Joe Essick. Booth No.
C-1926.Barmag AG, Germany. Booth No. C-1740.Louis P. Batson Co., Greenville, S.C., will show
textile accessories and supplies. Primary contact in booth: Marie Cox. Booth No. B-1335.Bay
Controls Inc., Maumee, Ohio, offers advanced compressed-air system management solutions. Bay will
introduce the new BayWatch performance enhancement service that includes 24-hour-a-day efficiency
monitoring and web-based reporting for flexible access to key information. Primary contact in
booth: Gary Thaxton. Booth No. A-414.Befama, S.A., Poland (Wise Industries, Kings Mountain, N.C.),
will exhibit an edge-trim opener for nonwovens. Other products offered by the company include
carding machinery, opening and blending machinery, textiles recycling equipment and ring-spinning
frames. Primary contact in booth: Piotr Fialkowski. Booth No. A-322, A-324.Belmont Textile
Machinery, Mount Holly, N.C., will show an air-entanglement machine, take-up winders, accumulators
and yarn coilers. Primary contact in booth: Jeffrey T. Rhyne. Booth No. C-1936.Belt Shop Inc.,
Belmont, N.C., will showcase flat power-transmission and conveyor belting as well as spinning and
twister tapes, ID bands, crosslapper belts, and screen and mesh belting. Primary contact in booth:
Jim Mull. Booth No. D-2225.BettariniandSerafini, SRL, Italy (Stellamcor Inc., Larchmont, N.Y.),
will emphasize various machinery and technology for yarn production. Some of the machines on
display include carding machines, opening machines, fiber openers, metering machines, card feeding
systems and weighing control systems. Primary contact in booth: Giovanni Bettarini. Booth No.
D-2925-A.Binsfield Engineering Inc., Maple City, Mich., will display rotary temperature
transmitters used to accurately monitor temperatures on heated godet roll sheets. New products to
be featured are the RT300 Rotary Temperature Transmitter System, the RT220 Rotary Temperature
Transmitter and the DS220 Digital Stator. Primary contacts in booth: Michael Binsfield and Mike
Kawiecki. Booth No. B-1230.Adolf Bockemuehl GmbHandCo. KG, Germany (Symtech Inc., Spartanburg,
S.C.), will exhibit special accessories for spinning machines, including condenser tapes, aprons
and bobbins, rubbing and combing aprons, cots, texturing aprons and high drafting aprons. Primary
contact in booth: Bobby Patrick. Booth No. D-2101-A.Bombi Meccanica, Italy (Stellamcor Inc.,
Larchmont, N.Y.), will exhibit spray, low-melt fiber, powder and foam bonding technologies; hot and
cold calenders; computerized foam generators and foam applicators; various ovens and dryers; and
air-cleaning towers. Primary contact in booth: Tancredi Bombi.Booth No. D-2927.Bowman-Dunn Mfg. Co.
Inc., Charlotte, N.C., will display aprons, belting, flexible card clothing and wire cylinders for
yarn formation processes. Primary contact in booth: Russ Bowman. Booth No. B-1522.Brer Ltd.,
Switzerland (Graf Metallic of America Inc., Spartanburg, S.C.), will introduce its new Titan finish
spinning rings and the latest developments in traveler design and finish for high-speed, quality
ring spinning. Brer will also show Rapid, equipment for semi-automatic insertion of travelers.
Primary contact in booth: James Mauney. Booth No. B-1301.Briggs-Schaffner Co., Winston Salem, N.C.,
will highlight its new and used beam maintenance programs for tricot, section and loom beam
repairs. Primary contact in booth: Steve Hagood. Booth No. C-1818.Bunting Magnetics Co., Newton,
Kan., will exhibit permanent and electro magnets. Primary contact in booth: Dale J. Thortsen. Booth
No. D-3029.Christoph Burckhardt AG, Switzerland (Fi-Tech Inc., Richmond, Va.), will feature its
patented fibrillating system using replaceable pin bars. In addition, Burckhardt will highlight its
extensive capabilities for hot and cold perforation. Primary contact in booth: Christoph Ulmer.
Booth No. D-2506.Burckhardt America Inc., Greensboro, N.C., will show rotor spinning components
including rotors, navels, twist traps, combing rolls and wear coatings. Primary contact in booth:
Robert Mackey. Booth No. B-1436.BVO Corp., Monroe, N.C., will exhibit roll-shop equipment including
cots, aprons, rollers and spare parts for the spinning and yarn industry. Primary contact in booth:
Don Bump. Booth No. D-3016.CandD Robotics, Beaumont, Texas, manufactures material-handling gantry
robotic systems that palletize and depalletize. CandD will showcase its specialty multi-line
palletizers, order picking, and packaging-material handling equipment. Other equipment in the
companys product line includes conveyors, pallet dispensers, rail cars and a zip-coded bundle
palletizer. Primary contact in booth: J. C. Caraway. Booth No. A-312.C. B. Mfg.andSales Co., West
Carrollton, Ohio, is a manufacturer of custom and standard blades for the textile industry and also
provides blade coatings for longer life. Booth No. B-1222.Caraustar, Fort Mill, S.C., will display
yarn carriers for filament and spun yarns, various tubes for texturing drawtwist, and paper tubes
used in the packaging and windup of nonwoven fabrics. Primary contact in booth: Richard Massey.
Booth No. D-2119.Cardan Design Corp., Maplewood, Nev., will have among its exhibits tungsten
carbide tow-cutter blades. Various other types of blades will also be on display. Primary contact
in booth: Charles Sears. Booth No. A-125.Carico Systems, Fort Wayne, Ind., will exhibit wire
container models 15102, 15403, 15406 and 15739 as well as roll cart models RC-4, RC-5, RC-9 and
RC-11. Primary contact in booth: Lori Graves. Booth No. B-1507.Carolina Brush Mfg. Co., Gastonia,
N.C., will show custom design and special application brushes for use in the textile industry.
Primary contact in booth: Fred Spach. Booth No. D-2629.Meccanica Carresi, SRL, Italy, will show a
video highlighting its machinery for the opening, cleaning, oiling, storing, blending and feeding
of textile fibers destined for woolen spinning, worsted spinning, nonwoven production lines and
rag-tearing lines. Primary contact in booth: Alessandro Badiali. Booth No. D-3023.A. B. Carter
Inc., Gastonia, N.C., will introduce a mag-feed traveler installation tool for improving spinning
productivity; the Resch in-line steaming machine to steam bobbins for the purpose of relaxing yarn
twist and controlling residual moisture; and the neps and trash indicator tester (NATI), which is
designed to monitor sliver quality at the carding, combing and drawing machines. Other laboratory
testing equipment will be on display. Primary contact in booth: Fred Rankin. Booth No. B-1326.Cary
Mfg. Corp., Charlotte, N.C., will exhibit blowers and vacuum pumps, vacuum accessories and the Cary
Super Vac portable and stationary vacuum systems. Primary contact in booth: Gil Millsaps. Booth No.
D-2505.Cason, SPA, Italy (Fi-Tech Inc., Richmond, Va.), will exhibit an extensive line of manual,
semi-automatic and fully automatic bobbin/pirn stripping units. The company will also promote new
fine-denier polypropylene turnkey spinning plants. Primary contact in booth: Giovanni Cama. Booth
No. D-2508.Ceramco Inc., Charlotte, N.C., is a source of roll manufacturing and reconditioning
technology and will have on display ceramic and metal coatings that offer wear resistance and
engineered surface properties. Booth No. A-206.CeramTec North America, Laurens, S.C., will
introduce conductive alumina pins and eyelets that can dissipate static and have good wear
resistance. The company also offers technical ceramics including eyelets, applicators, air-jets,
stationary guides and traverse guides. Primary contact in booth: James Satterfield. Booth No:
B-1505.Cezoma BV, The Netherlands, will show various tube, cone and bobbin winders as well as
accessories. Primary contact in booth: A. W. F. Ceelen. Booth No. B-1218.Chase
MachineandEngineering, West Warwick, R.I., will display a cut-to-length machine and a two-box
festooner. Booth No. B-1219.Chemineer-Kenics, North Andover, Mass., will highlight its mixing
technology, which has been developed to offer in-line processing with a minimal drop in pressure.
The Kenics mixing element can blend and disperse fluids in-line, eliminating the need for batch
processes. Primary contact in booth: Steve Willis. Booth No. D-2728.Clarkson Industrial
Contractors, Spartanburg, S.C., will offer information on installation, erection or relocation
services for equipment and machinery. Primary contact in booth: Rick Smith. Booth No.
D-2524.Clemson University, Clemson, S.C., will be promoting textile and fiber education at Clemson
with information on majors and services available to industry. Primary contact in booth: Bob Bowen.
Booth No. B-1133.Cognetex, SPA, Italy (ZTM, Ashville, N.C.), will exhibit stretch-breaking
machines, drawframes, roving frames for worsted yarn and ring-spinning frames for worsted spinning.
Primary contact in booth: Paolo Campagnoli. Booth No. C-1932.Component Resources, Spartanburg, S.C,
will highlight open-end spinning parts. Primary contact in booth: Greg Atkins. Booth No.
D-2430.Conitex Sonoco, Gastonia, N.C., will feature high-performance paper cones and tubes for the
spun-yarn market. Primary contact in booth: Leary Cloer. Booth No. C-1836.Corghi, SPA, Italy (Louis
P. Batson Co., Greenville, S.C.), will show cone-to-cone winders, hank-to-cone winders and
dewinders. Primary contact in booth: Marie Cox. Booth No. B-1432.Custom Industries Inc.,
Greensboro, N.C., will exhibit automatic yarn-packing systems, laser marking for yarn packages and
cones, replacement parts for Schlafhorst and Murata winding and spinning machines, and Electrotex
sensing and monitoring devices. Primary contact in booth: Mike OConnor. Booth No. C-1922.Cutrite,
(Louis P. Batson Co., Greenville, S.C.), will display scissors and shears. Primary contact in
booth: Marie Cox. Booth No. B-1335.Dalmec Italia, SPA, (Symtech Inc., Spartanburg, S.C.), will be
exhibiting Speedyfil, its miniature Manipulator, which is equipped with specific pneumatic grippers
for handling textile bobbins. Also on display will be the Partner Industrial Manipulator, which can
handle carton boxes with the use of special vacuum grippers, enabling operators to move any product
effortlessly. Primary contact in booth: Daniel Martin. Booth No. D-2115.C. R. Daniels, Ellicott
City, Md., will show material handling solutions including shipping containers, tilt trucks and
conveyor belting. Primary contact in booth: George Frazier.Booth No. D-2413, D-2415, D-2417.Datapaq
Inc., Wilmington, Mass., will showcase the Oven Tracker System for monitoring the temperature
profile in a tenter oven. The system combines the latest data-logger technology with thermal
protection and analytical software to ensure the process is kept within specified tolerances.
Datapaqs 9000 data logger has the fastest sampling rate in the industry, the company claims.
Primary contact in booth: Connie Wood. Booth No. B-1409.Datatex TIS Inc., Greenville, S.C., will
demonstrate its software for textile manufacturing applications. The systems are fully integrated
and offer everything needed to operate a plant. Datatex will also introduce Java-based
applications. Primary contact in booth: Jim Watters. Booth No. B-1526.Davis-Standard Corp.,
Pawcatuck, Conn. (Lawson-Hemphill Sales, Spartanburg, S.C.), will show various extruders and
controls, feed screws, film lines and lab lines for staple and synthetic fiber. Primary contact in
booth: Mark A. Reese. Booth No. B-1236-A.Day International Inc., Greenville, S.C., will feature
various cots and aprons for spinning and texturizing yarn. Primary contact in booth: Marsha Marsh.
Booth No. C-1820, C-1832.DellOrcoandVillani, SAS, Italy (Stellamcor Inc., Larchmont, N.Y.), will
have information on opening and blending equipment, pneumatic transport systems and presses.
Blending boxes, reclaiming machinery, hopper feeders, bale openers, fine openers, apron feeds,
condensers, automatic control systems and horizontal presses are included in the machinery and
technology that DellOrco has to offer. Primary contact in booth: Sergio DellOrco. Booth No.
D-2925-B.Dent Inc., Huntersville, N.C., will exhibit optical yarn-break detectors and software
systems for data monitoring and processing. Primary contact in booth: Andrew Dent. Booth No.
D-2410.Diamond Wire Spring Co., Taylors, S.C., will show various compression, extension and torsion
springs, as well as wire forms. Primary contacts in booth: Gene Coyle and Frank Fazio. Booth No.
A-403.DietzeandSchell GmbH, Germany (American DietzeandSchell Corp., Piedmont, S.C.), will have an
information booth displaying pictures and catalogs of winding and texturing machinery. Primary
contact in booth: Christian Iyer. Booth No. D-3033.Dilo System Group, Germany (Dilo Inc.,
Charlotte, N.C.), will have among its exhibits a special airlay Turbo-Card system fed by a
Trutzschler FBK feeding unit followed by the Hyperpunch ultra high-speed needler. This line aims
for high-speed needling of lightweight hygienic or medical material as well as special filtration
products. Other Dilo technology to be shown includes a Di-Lour double-structuring unit for the
production of velour for auto interiors; and the high-speed patterning machine, Di-Loop DYSXB, for
floor coverings; along with Dilo Di-Sign software. Booth No. C-1829.DMandE Corp., Shelby N.C., will
exhibit tow cutters, crimpers, cutter reels, winder cams, tension stands and a cutting-load
indicator for diagnostic measurement. Primary contact in booth: Phil Love. Booth No.
D-2829.DO-Ceram Engineered Ceramics, Co. Ltd., Germany, will present its line of ceramic thread
guides made from alumina, titania and zirconia, and will also introduce Cerazur, its brand-new blue
ceramic with an extremely high impact resistance and hardness. Primary contact in booth: Thomas
Krause. Booth No. B-1506.Dover Flexo Electronics Inc., Rochester, N.H., will exhibit WebHandler, a
low-cost automatic tension controller; the TrueTension series of tension indicators; tension-roll
transducers, roll-shell transducers and narrow-web transducers to measure tension on textile
machinery; and heavy-duty dual-disc pneumatic tension brakes to control tension on any rewind.
Primary contact in booth: Mark Breen. Booth No. D-2227.Dukane Corp., Ultrasonics Division, St.
Charles, Ill., is a leader in ultrasonic equipment for the bonding, slitting, laminating and
cutting of synthetic wovens and nonwovens. The company will show an Ultrasonic sewing machine,
slitter, hand-held mini slitter and press system. Primary contact in booth: Joe Re. Booth No.
D-2427.Eldon Specialties Inc., Graham, N.C., will show ceramic yarn and thread guides, tension
devices, creel caps, rollers, air-assist suction guns and various other parts for textile
machinery. Primary contact in booth: Don Foster. Booth No. D-2618.Electric Systems Inc.,
Chattanooga, Tenn., will demonstrate drive controls manufactured by ABB, Reliance, Siemens, Allen
Bradley and MagneTek, integrated into a singular drive enclosure powering a center winding
application. Primary contact in booth: Mike Mauney. Booth No. D-2908.Electro-Jet, S.A., Spain (PSP
Marketing Inc., Charlotte, N.C.), will show cleaners, bobbin strippers and material handling
systems. Primary contact in booth: Mireia Rovira. Booth No. C-1734.Electromatic Equipment Co. Inc.,
Cedarhurst, N.Y., will highlight tension-measuring instruments and systems, which include hand-held
mechanical and digital tension meters, in-line tension sensors and indicators, tachometers,
yarn-speed indicators and durometers. New equipment offered by the company includes the Check-Line
models ZEF and ZED for the accurate measurement of running-line tensions on a wide variety of
yarns, fibers and fine wires. Primary contact in booth: Andrew Kaner. Booth No. B-1221.Elitex
Machinery SRO, Czech Republic (Epic Enterprises Inc., Southern Pines, N.C.), will showcase a
two-for-one twisting machine. Primary contact in booth: Peter Magie. Booth No. B-1207.The Elliott
Co., Jeannette, Pa. (Ron Whites Air Compressor Sales, Anderson, S.C.), will show centrifugal air
compressors. Primary contact in booth: C. David Gibson.Booth No. B-1511.Eltex U.S. Inc., Greer,
S.C., will exhibit yarn-break detectors for winding, spinning, weaving, warping, heat-set and
air-entanglement machines, as well as various tension monitors. Primary contact in booth: Jonathan
Bell. Booth No. B-1435.Enka Tecnica, Germany (Fi-Tech Inc., Richmond, Va.), will highlight its
ability to manufacture spinnerets for all fiber processes and will exhibit a line of fiber-quality
devices and components. Primary contact in booth: Iris Ross. Booth No. D-2603.Epic Enterprises
Inc., Southern Pines, N.C., will have among its exhibits parts for Volkmann, Verdol and Elitex
two-for-one twisters and cablers, as well as parts for Superba and Suessen heat-setting machines.
Primary contact in booth: Herman Harris. Booth No. B-1206.Edmund Erdmann GmbHandCo. KG, (Edmund
Erdmann Enterprises, Charlotte, N.C.), will feature a draw winder. Primary contact in booth: Daniel
Troutman. Booth No. C-1817.EREMA GmbH, Austria (EREMA North America Inc., Topsfield, Mass.), will
have an information booth displaying materials on plastic recycling systems, PET recycling systems,
automatic backflushing screen changers, size-reducing machinery and WAREMA wash lines. Primary
contact in booth: Karl Maas. Booth No. D-2221.eSASA.com, Atlanta, will promote the new global,
multi-lingual, full-service Internet marketplace for textile machinery. Primary contact in booth:
Don Cotney. Booth No. C-1830.Excel Inc., Lincolnton, N.C., will display material handling
solutions, which include spring-bottom trucks, doff trucks, roller-deck trucks, tray trucks, pin
and cone trucks, and shelving. Primary contact in booth: Charles Eurey. Booth No. D-2302.Exim Ltd.,
Greenville, S.C., will present cone and tube adapters, anti-vibration machinery mounting pads and
ceramic thread guides. Booth No. C-1629.Exxon Lubricants, Burnsville, N.C., will highlight textile
lubricants and lubrication engineering solutions. Primary contact in booth: Ed Siles. Booth No.
B-1516.FandT Products, Greenville, S.C., will feature rubber cots and aprons, spinnerettes, weaving
parts, separator rolls, hot knives and acrylic tow stretch-breaking equipment. Primary contact in
booth: Michael Alexander. Booth No. D-2521.F.O.R. Ing. Graziano, SPA, Italy, (McKittrickandAssoc.
Inc., Charlotte, N.C.), specializes in the construction of cards as well as machines for fiber
opening, blending and feeding. This includes cards for nonwovens, woolen cards, worsted cards and
cards for semi-worsted yarns. The company will introduce a patented Y.M.2+1 woolen card that is
equipped with the most modern drives available. Primary contact in booth: R. Bacchio. Booth No.
D-3013.Fadis, SPA, Italy (J-Tex Corp., Troutman, N.C.), will exhibit Syncrotex electronic doubling
winders and electronic soft winders. Primary contact in booth: Harry H. de Jong. Booth No.
D-3019.Far44; SPA, Italy (Carolmac Corp., Greenville, S.C.), will have a large information booth
with samples of fiber and drawings of machinery. The company has been a pioneer in designing and
manufacturing compact staple fiber machinery and is now entering the market with machines for
producing spunbonded nonwovens and meltblown fiber webs suitable for PP, PE, PET, PA and their
copolymers. New machines to be highlighted will include Superstaple III and Superstaple IV for
carded webs in staple fibers, Superspun spinning system for spunbonds in continuous filaments, and
the Supermeltblown spinning system for spunlaid webs in meltblown material. Primary contact in
booth: Marco FarBooth No. C-1600.Fehrer AG, Nonwovens Machinery Division, Austria (Batson
YarnandFabrics Machinery Group Inc., Greenville, S.C.), will have samples and information regarding
Fehrer machinery and technology, which includes the latest in nonwoven and needle-punching
developments. Primary contact in booth: Peter Schoeffer. Booth No. C-1741.Fehrer AG, Spinning
Machinery Division (DREF), Austria (Symtech Inc., Spartanburg, S.C.), will introduce the DREF 2000
6/E12 friction spinning machine. Primary contact in booth: Norbert Ziebermayr. Booth No.
D-2108.Fiber and Textile Services Inc., Lewisville, N.C., will exhibit spare parts for take-up
winders, ceramic eyelets, traverse guides, ceramic and polyurethane friction discs for false-twist
texturing, and breaker plates. Primary contact in booth: Jim Arrington. Booth No. D-2308.Filatech
GmbH, Germany (FranklandThomas Inc., Greenville, S.C.), will highlight cleaning systems for polymer
filters, spin packs and melt pumps. Primary contact in booth: Thomas Mueller. Booth No.
D-2523.Fillattice, SPA/OMM, Italy (Fillattice Inc., Charlotte, N.C.), will present covering
machines for double and single yarns; and for fine, medium and coarse yarns. Also on display will
be spandex fiber, synthetic and natural fibers for narrow elastic fabric, high-speed hollow
spindles and electronic bobbin winders. Primary contact in booth: Davide Monti. Booth No.
C-1628.Fi-Tech Inc., Richmond Va., will be on hand to discuss spinpack design, polymer filtration
solutions and its spare parts program. Primary contact in booth: Jeffrey G. Bassett. Booth No.
D-2609.Fleissner GmbH, Germany (Fleissner Inc., Charlotte, N.C.), has developed five new
technologies in the field of spunlace hydroentanglement. At the show, Fleissner will be exhibiting
an Aquajet hydroentangling unit with a 5.0-meter working width. Other offerings include a jumbo
crimper, a godet unit and a sunflower reel plaiter for conjugate fiber. Primary contact in booth:
Don B. Gillespie. Booth No. D-2600.Formall Inc., Knoxville, Tenn., will exhibit reuseable,
returnable plastic yarn packages for both shipping and in-house handling. Primary contacts in
booth: Bryan Yarnell and Bob Stovall. Booth No. B-1519.Fortechnology Inc., Norwood, Mass., will
demonstrate the Fort760 Moisture Analyzer with a network-ready Windows N/T Operating System. The
company says the system instantly and nondestructively determines the moisture regain percentage
and commercial weight allowance of yarn packages. Primary contact in booth: Rose Murphy. Booth No.
D-2314.Fortress Technology, Canada, will feature metal detectors for the textile industry, and web
and blown fiber applications. Primary contact in booth: Steve Mason. Booth No. A-213.Foster Needle
Co. Inc., Manitowoc, Wis., will show a complete range of felting and structuring needles and
needle-removal tools. Primary contact in booth: John Foster. Booth No. C-1931. FranklandThomas
Inc., Greenville, S.C., will exhibit rubber cots and aprons, spinerettes, acrylic tow
stretch-breaking equipment, separator rolls, hot knives and weaving parts. Primary contact in
booth: A.W. Thomas III.Booth No. D-2422.Freudenberg, Germany.Booth No. D-2717.H. Talleres Gal#44;
S.A., Spain (PSP Marketing Inc., Charlotte, N.C.), will feature ring doubling and twisting machines
as well as precision winders. Booth No. D-2218, D-2226, D-2319,D-2327.Gaudino, SPA, Italy (Dawson
Textile Machinery, Greensboro, N.C.), is a supplier of automated ring-spinning frames for the
carpet, worsted, semi-worsted and short-staple synthetic markets. Information will be available on
specialty frames that can be custom-made to fit the needs of the spinner. Primary contact in booth:
Claude Dawson. Booth No. D-2124.Giesse, SRL, Italy (OTEX Inc., Lyman, S.C.), specializes in
machinery for the production of chenille yarns. The company will highlight the new SL 2000 machine,
which was developed with flexibility, quality and productivity in mind. The SL 2000 features
computerized controls and a redesigned diagnostic system. Primary contact in booth: A. Maier. Booth
No. C-1800.Gip Exports, India, will show precision spare parts for draw texturizers, cone-winding
machines for the man-made fiber industry and spare parts for weaving machines. Primary contact in
booth: U.V. Shah. Booth No. D-3031.Giudici, DavideandFigli, SNC, Italy, (PetreeandStoudt Assoc.
Inc., High Point, N.C.), will introduce the RG.6 BE electronic air-covering machine for the
air-entangling of elastomers with synthetic fibers. The machine has central electronic controls,
high-speed take-up, easy threading, and electronic yarn sensors among its many features. The
company will also showcase the RGT A model electronic air-texturing machine for nylon, polyester
and polypropylene. Primary contacts in booth: Domenico and Paolo Giudici. Booth No. C-1716.Gneuss
Inc., Matthews, N.C., will present RSFgenius, the new top product of its rotary filtration systems.
The RSFgenius can be used for the ultra-fine filtration of high-viscosity and low-viscosity plastic
melts. The filter has a fully automatic mode of operation with constant pressure consumption across
the filter. Primary contacts in booth: Monika Gneuss and Daniel Gneuss. Booth No. C-1640.Goulston
Technologies Inc., Monroe, N.C., produces specialty lubricants for manufacturing and processing
synthetic fibers including fiberfill finishes, spandex finishes and spin finishes for fibers made
from PTT- and PLA-based polymers. Primary contact in booth: Gordon Magee.Booth No.
C-1939.GrafandCie., Switzerland (Graf Metallic of America Inc., Spartanburg, S.C.), will feature
the latest technology in metallic wire for clothing high-speed cards and opening and cleaning
rolls. Primary contact in booth: James Mauney. Booth No. B-1300.Gualchierani Textile Automation,
SAS, Italy (Dawson Textile Machinery, Greensboro, N.C.), will have information on the GSA bale
press that was introduced at ITMA as well as information on spinning automation and filament
production. Primary contact in booth: Claude Dawson. Booth No. D-2130.Habasit Belting, Chamblee,
Ga., will demonstrate a wide range of high-performance Armid® tangential drive belts featuring the
first open-end spinning belt with a performance guarantee. Habasit will also introduce the AS-250H,
a new abrasion-resistant tangential belt. Primary contact in booth: Gary Paradise. Booth No.
B-1232.Hacoba Spultechnik GmbH, Germany (Symtech, Inc., Spartanburg, S.C), will display the Thread
King and Thread Master series of automatic and semi-automatic winders for sewing threads.
Electronic gears, slit drum systems and newly added traverse systems guarantee highest package
quality and gentle yarn treatment. Other equipment on display includes the NSA-U underbobbin winder
and the FSA braider bobbin winder.Booth No. D-2300. HDB Houget Duesberg Bosson 1823, S.A., Belgium
(Symtech Inc., Spartanburg, S.C.), will have an information booth emphasizing its manufacturing
program, which includes opening, blending, carding, spinning, gilling, crosslapping and
web-drafting machinery for woolen, semi-worsted and nonwovens manufacturing. Primary contact in
booth: Bobby Patrick. Booth No. D-2101-B.Heany Industries Inc., Scottsville, N.Y., will show
Heanium industrial solid ceramic eyelets, guides, tension assemblies, pigtails and bushings, as
well as ceramic pulleys designed for wire, cable and fiber optics. Various coatings for wear
resistance will also be on display. Booth No. D-2318.Heberlein Fiber Technology Inc., Switzerland
(Heberlein North America Inc., Greenville, S.C.), will exhibit key components and system solutions
for effective processing and finishing of yarns, which includes PolyJet, SlideJet and ACV-Jet
air-interlacing jets and the Pulsar-Fancy-Yarn-System. Primary contact in booth: A. Weber.Booth No.
D-2802, D-2903.H. Hergeth GmbH, Germany, will introduce a plucker for long and staple waste, as
well as a high-production plucker and condenser and a blending system. Primary contact in booth:
Hubert Hergeth. Booth No. C-1640. Heritage Cutlery, Bolivar, N.Y., will display more than 80
models of textile-cutting scissors and shears that are configured to cut a wide array of synthetic
and natural materials. Primary contact in booth: Chris Olix.Booth No. D-2231.August Herzog, Germany
(August Herzog U.S.A., West End, N.C.), will show braiding machinery, winding machinery, unwinding
and rewinding machinery and a computer-aided design program. Primary contact in booth: John Owen.
Booth No. B-1515.Hills Inc., West Melbourne, Fla., will show bicomponent fibers and related
products. The company will highlight 100-islands-in-the-sea nanometer fibers and a 1-micron
meltblown fabric made using a 100-holes-per-inch die. Primary contact in booth: John Hagewood.Booth
No. C-1933.Himson Ind. Ceramic Ltd., India, will feature ceramic thread guides, brakes for yarn,
and wire guides and assemblies. Primary contact in booth: P.G. Rave. Booth No. A-204.Hi-Tec Plating
Inc., Statesville, N.C., will highlight tdC-1® thin dense chrome plating. Also on display will be
conventional, flash, matte and industrial hard chrome platings. Primary contact in booth: Buddy
Bray.Booth No. B-1135.Hi-Tech Products Inc., Greenville, S.C., will show ceramic yarn guides and
tension assemblies. Primary contact in booth: Rick Lankford.Booth No. D-2916.James
HoldsworthandBros. Ltd. England (Redman Card Clothing, Andover, Mass.), will exhibit flexible and
metallic card wire in addition to mounting, grinding and cleaning equipment for all card wire.
Primary contact in booth: John Murray.Booth No. D-2312.John D. Hollingsworth on Wheels Inc.,
Greenville, S.C., will introduce Mastersteel, new metallic card clothing. The company also offers
standard and enhanced-point metallic card clothing for nonwovens, yarn spinning and worsted yarn
applications as well as various carding accessories. Primary contact in booth: Carl Martin. Booth
No. C-1618.HSGM GmbH, Germany (HSGM Inc., Duncan, S.C.), will demonstrate hand-operated and
tabletop heatcutting and sealing equipment, soldering guns and styrofoam-cutting equipment.
Visitors are invited to bring samples of fabric and other materials to the booth for test
cutting.Booth No. D-2626.Hydradyne Hydraulics, Charlotte, N.C., will showcase pneumatic components
and systems. Primary contact in booth: Gary Grussing. Booth No. A-314.ICBT Inc., see Rieter ICBT
Greensboro Inc.Booth No. C-1812.Igus® Inc., Rumford, R.I., will be displaying its Iglide®
self-lubricating polymer plain bearings, DryLin® linear bearings and linear guide systems, and
Igubal® polymer rod end bearings and spherical bearings. Igus will also introduce a new cable
carrier for advanced noise reduction and a new compact, self-lubricating linear guide system.
Primary contact in booth: Cate Keefe. Booth No. A-120.Industrial Air Inc., Greensboro, N.C., will
present a system that allows coordinated, interactive control of air-conditioning, refrigeration,
air-filtration, waste-handling and other process equipment. Features include centralized monitoring
with customized color graphic displays; selectable trending; alarm reporting; on-line operating,
maintenance and parts data; and off-site diagnostics of all systems via modem connection, including
control program modifications. Booth No. C-1732.International Baler Corp., Jacksonville, Fla., will
show a double box as well as raise
ATME-I Exhibitors
NAFTA Six Years Of Fibers
NAFTA UpdateBy John E. LukeNAFTA: Six Years Of Fibers
NAFTA shows mixed results for U.S. manufacturers, but opportunity for cross-border,
intra-industry trade. Economists have a habit of reviewing results and predicting the
future in five-year increments. These professionals notwithstanding, it is now past time, six years
and 40 percent through complete implementation, to review the performance of the U.S. fiber
industry in world trade with a specific focus on accomplishments with Mexico and Canada under
NAFTA.NAFTA has been good for the U.S. fiber industry. This is not to say that the industry shipped
all it could make or that fiber prices reflected adequate investment returns. It also is not to say
that the industry was not hammered by cheap fiber and manufactured product imports from all areas
of the world. It is to say, however, that facing the inexorable advance of world/free trade as
evidenced by NAFTA and WTO passage, U.S. fiber producers found new markets in the fabric-producing
industries of our immediate North American neighbors and have turned the tri-country poundage trade
balance from a negative to a positive figure. Accurate cross-border prices are not available, but,
based upon the current border-crossing product mix, the dollar balance of trade is still somewhat
negative, although significantly improved from pre-NAFTA levels.World Fiber TradeIt is important to
note that the negative trade balance in fibers results more from increased imports than from
decreased exports. Since NAFTA, new international capacity particularly in polyester and acrylic
has lusted after the worlds largest market, and U.S. fiber imports surged from a 1995-1996 average
of 1.1 billion pounds to over 1.3 billion by 1999. Simultaneously, U.S. fiber imports from NAFTA
countries remained virtually constant at approximately 480 million pounds. This means that NAFTA
countries share of U.S. fiber imports dropped from approximately 45 percent of total to under 38
percent in the most recent year.
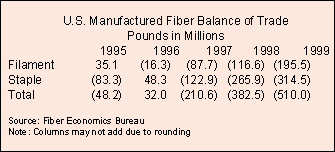
In exports, a contrary story has developed. Between 1995 and 1997, U.S. fiber industry
exports held steady at slightly over 1.1 billion pounds. Since that time, with world polyester
prices tanking and foreign producers offering the output of new polyester and acrylic capacity at
almost any price, domestic manufacturers pulled back; 1998 and 1999 exports dropped to under 900
million pounds. It must be noted in these figures, however, that U.S. fiber manufacturers responded
to NAFTA in the spirit in which it was created. In 1995, at 326 million pounds, U.S. fiber exports
to NAFTA countries represented 31 percent of total fiber exports. By 1999, fiber exports of 501
million pounds an increase of 11 percent per year represented almost 62 percent of total fiber
exports. NAFTA provides the economic essentials to allow and encourage U.S. producers to compete
close to home. This has brought us to a positive poundage trade balance with our NAFTA
partners.Table 1 details total U.S. fiber trade since the onset of NAFTA. Regular readers of this
space will recognize the abrupt change from an industry contributing a positive balance of trade to
one mired in seemingly eternal negative balances. In a word, the pattern is ugly and speaks loudly
to changes in fiber manufacturing and distribution brought on by the political and economic
turmoil, particularly in Southeast Asia, of the 1990s.In mid-decade, American fiber producers were
struggling to maintain the positive balance of payments historically provided by the industry. The
effort was for naught, however, as economic and political forces, particularly in Asia, unleashed a
frenzy of exporting to generate hard currencies and balance overstretched economies. In fibers, as
has been noted in this space several times in the past, the forces of King Polyester descended on
the U.S. market, resulting in a 160-million-pound positive balance of filament trade in 1995
turning to a 38-million-pound negative by 1999. Similarly, polyester staple swung 100 million
pounds negative to finish 1999 at almost 400 million pounds net imports. Some backing and filling
occurred in other fiber categories, most of which, save acrylic, amounted to little more than
normal variances in trade reporting. Acrylic manufacturers, traditionally an industry sector that
exported a substantial proportion of its fiber production, suffered from recent building of
capacity in Asia, and from customer lack of hard currencies with which to pay for traditional
imports. The first negative balance in memory of acrylic trade occurred in 1999. Considering the
amount of production capacity added in acrylic and polyester in Asia in the 1990s, it is highly
unlikely that the U.S. total manufactured fiber trade balance will ever again be positive.NAFTA
Fiber TradeA recent report from the El Paso Branch of the Federal Reserve Bank of Dallas (El Paso
Business Frontier, Issue 2, 2000, hereinafter called the El Paso Report) reviewing NAFTA trade
patterns provides an interesting perspective on the current shape of cross-border trade engendered
by the treaty. According to the report, at NAFTAs inception, an amusement in the United States
centered on identifying which industries or sectors would be winners and losers in the treaty. A
winner was identified as a sector in which exports would rise as a result of the treaty; a losing
sector would see increased imports. Generally speaking, the U.S. fiber/fabric/apparel complex
designated itself as losers, a title that unfairly groups several winners into the losers category.
As cross-Rio Grande trade has unfolded, it appears that apparel manufacturing accurately falls in
the loser category. Fabric manufacturing rides a middle ground, less impacted by NAFTA than by
expanded Southeast Asian garment production that reduces the overall need for U.S.-produced
fabrics. The El Paso Report notes that in 1999, the states of North Carolina (No. 6), South
Carolina (No. 17) and Alabama (No. 22) were among the top 25 states exporting to Mexico. North
Carolina and Alabama made the list for having apparel and other textile products as their top
export, and South Carolina made it for rubber and plastics products. Together, these three states
in 1999 represented more than 3.5 percent of all exports to Mexico. In the same year, textile yarn
and fabrics and articles of apparel and clothing represented more than six percent of total U.S.
exports to Mexico.The description hints at the shape of Mexican-U.S. bilateral trade. The El Paso
Report, rather than looking for winners and losers, views trade as two positives. Imports create
opportunities for consumers to broaden purchasing patterns, often at reduced prices; exports
provide opportunities for industry to expand markets and potentially operate factories at efficient
levels. In effect, U.S.-Mexican trade is raw materials and work-in-process in and finished goods
out. Trade is moving both ways, and, in the textile complex, it is intra-industry trade with
manufacturers on each side of the border that is adding value in specialty areas. This matches the
El Paso Report description of the U.S.-Mexican macro-trade as 80 percent intra-industry. Mexican
wages are a fact, and trade has changed under NAFTA to reflect their attractiveness. It now becomes
the responsibility of raw material suppliers to optimize opportunities for business south of the
border by combining the capital advantage of U.S. manufacturing with the labor attractiveness of
Mexico.In marked contrast to the world experience and moving toward the intra-industry description,
fiber trade among the three NAFTA partners has moved from a distinct negative position in
mid-decade, soon after NAFTA implementation, to a positive balance by the end of 1999. From a
negative 165-million-pound balance in 1995, the fiber industry has fought back to a positive
10-million-pound balance in 1999. Impressively, as U.S. man-made fibers reversed negative trade
trends and fought to a positive balance, they waged a losing battle with other geographic areas.
Table 2 outlines the balance of trade in fibers among the NAFTA partners. As the U.S. position in
world fiber trade deteriorated to a 510-million-pound negative balance in 1999, the NAFTA position
continued the positive trend first exhibited in 1995. By adding the data in Tables 1 and 2, one can
calculate the size of trade with non-NAFTA world areas can be calculated. In 1995, it was positive
116.7 million; 1996, positive 108.9 million; 1997, negative 202.9 million; 1998, negative 397.2
million; and 1999, negative 520.9 million. It certainly appears the U.S. fiber industry should be
thankful for the apparent positive benefits of NAFTA trade. NAFTA trade has a distinct geographic
slant, with the United States historically running positive trade balances with Canada and
negative, but decreasingly so, balances with Mexico (See Table 3). Canada apparently has focused
its fiber manufacturing in non-apparel markets, particularly in nylon. In total fiber trade between
the United States and Canada, except for a small negative trade balance in cellulosic filament,
only nylon filament runs a negative trade account, one approaching 100 million pounds annually.
This position reflects a regional approach by producers to fiber production, with much nylon
industrial filament production transferred to Canada since 1990. In polyester, the 800-pound
gorilla of trade, the United States maintains with Canada a small positive trade balance in
filament, while dancing around a zero balance in staple. At the southern end of NAFTA geography,
the trade picture with Mexico is significantly different from that with Canada. Consistent with the
difference in apparel industry wages between the United States and Mexico, Mexican trade in fibers
focuses on apparel-type items, and, not surprisingly, the major emphasis is on polyester. Mexican
polyester filament trade has run a consistent deficit approximating 22 million pounds in the past
five years. Once falling below 100 million pounds, staple has settled into a negative balance of
approximately 75 million pounds. This negative balance may grow as DuPont participates with its
Mexican Alpek alliance in building new capacity and faces issues of productivity in old U.S.
facilities vis-a-vis new operations in Mexico.
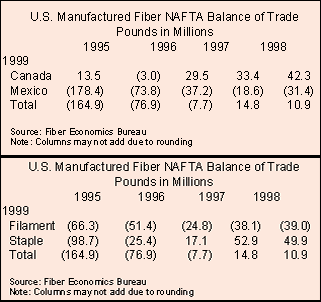
ConclusionAccording to the El Paso Report, since NAFTA opened the U.S. market to Mexicos
textiles and apparel goods, overall textiles and apparel exports to the United States have
increased 419 percent. In fact, Mexico surpassed China as the top supplier for the United States
for these products. That is the gauntlet. Mexican wage rates will rise, but so will those in the
United States. The U.S. fiber and fabric industries are as efficient and productive as any in the
world. Creativity, marketing and design abound in the United States. If industry marries the
competencies admits that the United States is a capital-sensitive, large-quantity manufacturer of
fibers and fabrics, and supports Mexicos management of its labor competencies then the natural
forces of cross-border intra-industry trade can be ridden to new records.
Editor’s Note: John E. Luke is owner of Five Twenty Six Associates Inc., Bryn Mawr, Pa., a
consulting firm specializing in strategic marketing and operations facing textile fiber and fabric
manufacturers. He is also a professor of textile marketing at Philadelphia University.
September 2000
Open-End Vs Ring-Spun Pricing
Yarn Market ResearchBy Erin Dodd and William Oxenham, Ph.D Open-End Vs. Ring-Spun Pricing
A new progam underway at N.C. State’s College of Textiles uses ATI pricing data to analyze and
forecast production and pricing of open-end and ring-spun yarns. There have been several
comments recently in the textile press regarding the differential pricing of ring-spun and open-end
(rotor) yarn. Further concern has been expressed about the difference in yarn pricing associated
with yarn count, and how this difference is influenced by the yarn type (ring-spun or
open-end). Identifying Pricing TrendsA project currently underway at N.C. State Universitys
College of Textiles, Raleigh, N.C., is investigating possible approaches to predicting future
trends in yarn production in the United States. Various sources of data are being utilized,
including data associated with yarn pricing, some of which has been obtained from back issues of
ATI. Based solely on data from ATI, it is possible to clearly identify certain trends that are
apparent in the figures that follow.Figure 1 shows a comparison of the prices for ring-spun and
open-end yarns of the same count (18Ne) from 1984 to the present. The difference in yarn prices is
also included (ring-spun yarn price/open-end yarn price), and it is clearly shown that the price
difference has increased almost linearly over time.Indeed, while the price difference in October
1984 was 13 cents, the difference in January 2000 was 51 cents. This trend is also shown for other
yarn counts for which prices were available.The reason for the increasing difference in prices is
that while ring-spun prices showed a general increase (up to 1997), open-end prices either remained
static or fell more rapidly than their ring-spun counterparts.Figure 2 compares the prices of 18Ne
and 10Ne ring-spun yarns (again from 1984 to the present), with the difference in yarn price due to
count also included. While there is considerable variation in price over time, it appears the
difference in price between the finer and coarser yarn is increasing slightly.
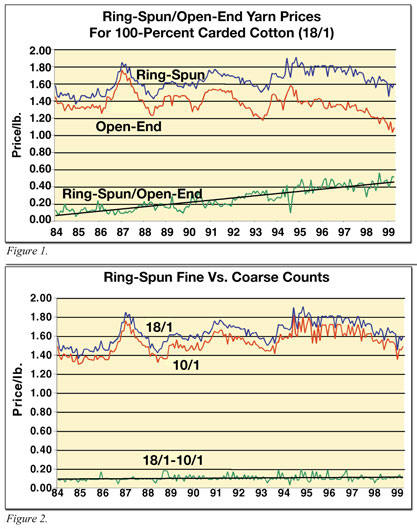
Figure 3 shows a similar exercise (comparing prices for 18Ne and 10Ne) for open-end
yarns. While the effects are small, the data indicates that for open-end yarns, the difference in
price between finer and coarser yarns is diminishing over the time period studied.While the
analysis is based on historic data, making it risky to extrapolate to make future predictions, the
findings are summarized as follows: The price difference between ring-spun and open-end is
increasing. The price difference between finer and coarser counts is increasing for ring-spun
yarns.The price difference between fiber and coarser count open-end yarns is decreasing.
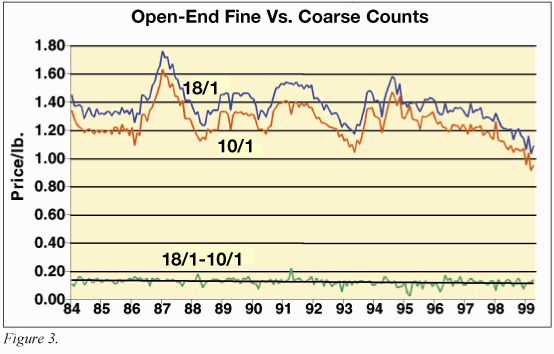
Editor’s Note: William Oxenham Ph.D, is professor, associate department head and graduate
administrator in the Department of Textile and Apparel Technology and Management in the College of
Texiles at N.C. State University.Erin Dodd is a graduate student at N.C. State’s College of
Textiles. She is completing her Master’s degree and preparing to enter the Ph.D program in Textile
and Apparel Technology and Management.
September 2000
TrendWatch Introduces Report On Textile Apparel Market
TrendWatch, Harrisville, R.I., has developed a new report for aiding technology firms in strategic
analysis of the textile and apparel industry.Published annually, the report will help executives
shed light on this industry and identify market segments, competitors, investment trends and market
opportunities.While design professionals may use similar tools, each market has a unique structure,
workflow, economic factors and expectations about how those resources are best used, said Dr. Joe
Webb, TrendWatch partner.Information is detailed by marketing and type of business, size of
business, geographic region and major investment categories.Discussion and analysis of the
challenges facing these businesses, their investment plans and technology threats will be included.
This report will collect the basic data that has been unavailable, as well as add insight to the
changing industry dynamics, said Alison Hardy, owner of FabriCAD and collaborator with TrendWatch
for this report.Bringing this kind of research to the textile and apparel markets will also result
in a Demographic Atlas and Market Segmentation Guide, which will provide managers with the
necessary statistical background and market sizing information to make strategic and tactical
decisions. The number of design businesses by zip code or major metropolitan area as well as
estimates of annual shipments will be included.
August 2000
Ring-Spun Yarn Sales Fantastic
A
brief comment from a respondent involved in raw cotton markets will be encouraging to
spinners: “The cotton crop looks beautiful this year, even with the drought. A large crop is
anticipated and the quality is good. Prices, however, don’t look good.” In other words – bad
news for farmers, good news for spinners. As with just about everything in this business, it’s not
over ’til it’s over. So we’ll see how it looks a couple of months from now.
The markets for ring-spun yarns are causing exuberance, to say the least, among spinners. One
spinner said, “Ring-spun markets are fantastic in all counts and all market segments.” Another
whole-heartedly agreed saying, “Ring-spun markets are excellent – really tight!” Now, the
question is, how long will it be until everyone moves to these markets and saturates them as we
have done in the open-end (OE) markets?
Spinners of ring-spun yarns are confident that the market is strong enough to see an
improvement in pricing. A spinner commented, “We will start moving prices up – the market can
take it. We are running full, but are still far behind. We have no inventory, and we are booked
solid through the third quarter. I wish we could have run through the fourth.”
Several factors have contributed to the continued excellence of markets for ring-spun yarns,
according to spinners. As one said, “Denim is back. Docker twill is back.” As you know, both of
these markets use tremendous quantities of yarn.
Opportunities Abound
“Open-end yarns, however, give us many opportunities in outerwear, underwear and T-shirt
markets,” commented one such spinner. Despite the lackluster market conditions, most OE spinners
are running full and booking ahead. One spinner informed the Yarn Market that he was booked solid
for the rest of the year and was beginning to book first quarter 2001. He said, “Of course, we are
quoting higher prices for next year, but we will never see inflated prices again. All we want to do
is make a reasonable profit – something we haven’t done in several years.” He also said that
once they got through the current contracts, prices will probably improve.
Many spinners feel the OE markets will always be tough because no one is getting out of it.
Therefore, the oversupply of OE yarns will continue. “It’s funny,” said one spinner, “the spinners
who complain most loudly about pricing in the OE markets are the same ones who are selling low.” In
spite of it all, volume remains good for these markets.
Inventories are strictly controlled, according to virtually all spinners. As if to justify
more than their standard of two-week inventory, one spinner said, “Of course, when you run so many
products, you have to maintain a stock of your basic items.”
South Of The Border
The Yarn Market received some interesting comments from spinners concerning the Carribean and
Mexico. One spinner observed, “While spinners will probably benefit, those textiles which are
labor-intensive will move offshore.” Yet another spinner commented, “I think the CBI will be good
for us as long as it lasts, but a couple of large producers could eat up the quotas. Also, a
company must get positioned beforehand and be able to identify the players. The logistics could be
a problem, such as credit and freight. Those who capture the market will profit the most.” This
same spinner (discussing NAFTA) said, ” Those manufacturers already involved in Mexico are
beginning to question their position, feeling they must supply the local market rather than ship
the goods back to the USA.” Shipping costs are apparently part of the problem.
Weavers are having real problems with synthetic fabrics. As one weaver said, “It’s a struggle
every day.” In cotton and poly/cotton goods, volume is good, but margins are terrible. Doesn’t that
sound familiar to you spinners?
The Good Old Days
A spinner reminisced, “Way back yonder, we had peaks and valleys in our earnings report. Today,
it is all valleys. We need to climb a peak and start making a profit for a change. Seriously, I
think the future for spinners looks good, at least for the near future.” He was reminded that back
in the old days, we came out of the mills covered in so much lint that we never had a problem with
dry hair days. Who wants to go back to the good old days?
August 2000
Textile Institute Creates Strategy Marketing Group
The Textile Institute, England, has strengthened its network of industry-focused Special Interest
Groups with the creation of a new body to promote strategy and marketing for textiles, apparel and
related industries.Chaired by David Rigby, a strategy and marketing consultant to the global
textile industry, the new group aims to provide services to members associated with the commercial
issues they face in day-to-day business strategy.Increasingly, companies in textiles and related
industries have to think more clearly about business strategies and market focus, said Rigby.
Having efficient operations is not enough if the strategic focus is wrong. Rapid changes in the
global market, and its supply chain, mean that overall business direction and marketing strategies
need to be constantly under review.The group will be based on the Internet so that advice, support
and information can be quickly shared worldwide.
August 2000
Quality Fabric Of The Month: Tactel® Fuses Fashion And Performance
The 2000 International Hosiery Exposition (IHE), held in Charlotte, N.C., was the venue for the introduction of new products made using Tactel®, DuPont’s family of innovative specialty, fine denier per filament nylon yarns. With Tactel, fashion and performance are fused in a variety of seamless applications including swimwear, activewear, lingerie and support garments, as well as the complete spectrum of legwear. Tactel and Lycra® are used in combination to offer softness, luster, texture and visual interest as well as comfort, fit and freedom of movement.
Seamless Concepts
Tactel and Lycra are leading players in the growing market for seamless fashions. “The current uses of seamless have only touched the surface of what is possible with this innovative technology, as more women look for innovative ready-to-wear fashions,” said Kathy Smith, intimate apparel marketing manager for DuPont Lycra. “It is our partnership with key industry leaders that has made this growth possible.”
In the category of seamless apparel, Tactel has developed a multifunctional concept collection which presents possibilities for a variety of garments from intimate apparel to bodywear to ready-to-wear. New silhouettes, patterns and textures are available using jacquards, tone-on-tone, color blocking, striated effects and combinations of sheer/opaque and bright/matte.
“We are seeing a growing awareness of fashion, style and embellishment in the seamless category,” said Ida Corraggio, intimate apparel marketing manager for DuPont Tactel. “The fluid designs of seamless garments help to redefine the silhouette, while trends such as romantic florals and control tops and bottoms softened with ornamentation offer the perfect combination of functionality and allure.”
New Fashions In Legwear
Some of Tactel’s new legwear products combine fashionable new textures and bold colors with softness, breathability and durability. Among these new products is Hue’s new fashion sock, Sport Shell, made of Tactel Aquator™, a double-sided fabric that keeps feet dry and comfortable by wicking moisture away from the skin.
Also new on the legwear scene is Nine West’s So Strong line of 20-denier sheer hosiery made of Tactel Duo™.
“We are thrilled to be a part of the solution in creating products that consumers are looking for,” said Sharon Cook, DuPont’s retail marketing manager for Legwear. “Our Tactel family of yarns can help our customer’s brands stand apart with our offerings of different lusters, shimmers and color vibrancy. We allow the consumer more fashionable options, helping turn hosiery into a contemporary accessory.”
Tactel Soft Black
Tactel Soft Black, the newest offering in DuPont’s line of Tactel products, is solution-dyed to give the black a softer appearance than is achieved in package-dyed yarns. When blended with other yarns, it can be overdyed to obtain a uniform, deep color. The integrity of the companion yarn is maintained, while Soft Black enhances the styling capabilities of the blend. Particularly well-suited for jacquards and other patterned effects in seamless apparel, Soft Black is available
with a variety of yarn effects including air-jet-textured marls, false-twist combinations, covered and fancy yarns, organzines, metallic looks and soft-as-cotton natural looks.
For more information on DuPont’s new Tactel products, contact Eleanor Walsh, DuPont, (212)
255-1081.
August 2000
Growth Fiber Polypropylene
Arguably, the growth fiber of the 1990s is polypropylene. Total production of polypropylene
filament, staple and film was 1.8 billion pounds in 1990 and rose at a compounded rate of 5.5
percent to the 2.9-billion-pound level in 1999, easily besting the 2.7-percent rate posted by its
nearest competitor, polyester fibers
(See Table 1).Filament fiber shipment growth through the 1990s averaged a compounded 5
percent per year while staple averaged 7.2 percent per year. To be sure, the U.S. fiber industry
ships more polyester than olefin, nearly 3.6 billion pounds for polyester filament and staple in
1999, but olefin wins the battle for growth rate hands down and is catching up fast in the total
shipment category.Faced with this growth despite a stagnant domestic market deluged by imports, it
becomes important to pose several related questions. First, is polypropylene technologically and
marketing-wise ready to move up into the class of 3-billion-pound fiber Second, are fiber suppliers
prepared to invest in fiber development to sustain/increase the current rate of growth And third,
are fiber producers prepared to adopt sufficiently creative marketing strategies to balance the
pressures expected from the combination of existing domestic competitors and importers In this
article, we first will review statistics to set the stage, and then reveal marketing and product
strategies planned or in execution by several major players in polypropylene distribution. These
activities are not all that is going on, but we suggest that they are admirable examples of
creative marketing and product strategic thinking found among polypropylene producers and
processors. Setting The StageA closer look at Table 1 suggests that growth in shipments of
total polypropylene fibers has slowed, a pattern consistent with maturing product lines. The data,
particularly in filament, hints that shipments to carpet end uses, representing almost two-thirds
of all filament shipments, gained a substantial boost in 1994 as spending on housing responded to
Federal Reserve-activated lower interest rates and recovered from the early-decade recession. This
was followed naturally by a slowing as current interest rate upticks exacted a toll on housing.
Since 1997, the rate of growth in filament has slowed dramatically, dropping to 2.0 percent from
1998 to 1999.Staple, however, appears to be enjoying a renewed rise, energized by an almost
one-third rise in staple use in nonwovens. In the 1990s, staple has received two positive
market-share shots, all driven by improving fortunes in nonwovens, which represent approximately
three-fifths of all polypropylene staple sales. First came the significant bump from the 1991-1992
recession recovery, followed by a significant jump from 1998 to 1999 as major diaper producers
displaced some film layers with fibrous (staple or spunbonded) layers to diapers to make the
product seem more fabric-like and consumer-friendly (Authors Note: Part of mid-decade growth
represents the Fiber Economics Bureau fine tuning its database to include both captive fiber and
spunbonded/meltblown fiber capacities, which historically had been under-reported).Filament
polypropylene in carpet face fibers, the main driver of filament polypropylene market share, grew a
mere 1.5 percent from 1998 to 1999 and filament in carpet-backing fabrics, a barely better 2.2
percent (See Table 2). Other broadwovens incorporating filament, including items like geotextiles
and upholstery, increased an average of 6 percent per year, compounded for the 1996-1999 period, to
retain a 12-percent share of filament shipments. Rope, cordage and fishline grew more slowly than
the category average and watched market share deteriorate slightly. Other filament end uses grew at
the category average of approximately 4 percent and thereby held their own in market share.The
largest end use in the Other category is an amalgam of spunbonded and meltblown filament products
for such markets as carpet backing, interliners, medical disposables, etc. Also included are much
smaller miscellaneous markets for such products as backing/structural materials for sliver knit
products, miscellaneous apparel items like thermal underwear, sport-specific athletic garments for
biking, aerobics, scuba diving, running and the like. Together, all the miscellaneous end uses do
not consume nearly the amount gobbled up by spunbonded and meltblown, but these smaller uses appear
to provide opportunities for new specialized products that can lead to increased market share and
value-added potential.Staple shipments in 1996 grew 12+ percent over 1995 (See Table 1). It must be
noted, however, that 1995 lagged behind 1994 by 6+ percent as all major end-use areas carpet face,
broadwoven (largely upholstery) and nonwovens sagged from record levels. Secondly, 1996 staple
shipments recovered from the 1995 lethargy to scale the 500-million-pound mountain for the first
time, regaining all and more of the 1995 losses (See Tables 1 and 3).This growth has continued to
the present, driven in large part by double-digit gains in carpet-face fiber shipments, coupled
with a mind-boggling 34-percent increase in nonwovens consumption in the 1998-1999 period (See
Table 3). All of this increase is not yet understood, although a significant portion represents
changes in diaper construction.As filament polypropylene is beholden to carpet distribution, so
also must its staple cousin answer to a demanding master, nonwovens. To date in this market,
polypropylene successfully has bested polyester staple, which in its day bested rayon and cotton.
The question now becomes, what can polypropylene staple suppliers do to retain market interest in
the product Is the current product satisfactory or is newness mandatory for continued growth Are
there more diaper construction changes on the horizon to re-energize polypropylene fibers again
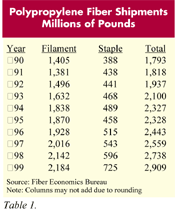
Going ForwardIt is quite apparent from the foregoing analyses that polypropylene fibers
enjoy dominant positions in several large markets. It also appears that these markets are
commodity-focused and often subject to the rawest of price and cost competition actions. These
pressures already have forced current polypropylene technology into efficient manufacturing
postures to fend off inter- and intra-fiber competition and market-share grabs from imports.So far
the campaign is successful in both filament and staple, but some industry observers suggest that
practical machine production/efficiency limits are at hand and a new efficacy paradigm is required
to continue growth patterns. The industry has been effective in providing low-cost materials. Now
it must build new product and marketing strategies and become effective at those endeavors.
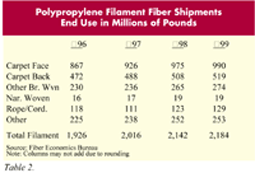
Marketing ChangesPolypropylene fibers are natural receptors for additives that bring
permanent market-specific characteristics to the material. Additives currently in use provide
anti-microbial, flame-retardant, higher heat resistance and higher strength characteristics to the
market. While these product innovation strategies find homes in a wide variety of end use markets,
it is important to note that new, innovative marketing strategies are an integral part of this
movement. The phrases solutions marketing and customer-focused are approaching hackneyed status,
but their impact is proving real in fiber marketing.Slimmed-down marketing organizations, created
by urgent needs for cost control or elimination, patrol customer plants looking for opportunities
to add value to existing businesses. For example, a two-year marketing initiative aimed at
improving carpet backing led Synthetic Industries, Chickamauga, Ga., to develop the secondary
backing, Softbac and the primary backing Patternloc. Both come from customer inputs, but this time
the customer was the installer, not the homeowner, who would be the ulitmate purchaser.Both
carpet-backing ideas came from installers. They save labor and material, making the overall cost to
the consumer lower than previous materials, despite a slight increase in per-square-yard expense
for the carpet because of the new technology.Polypropylenes environmental resistance and light
weight have long made the fiber a material of choice for geotextiles. As geotextiles have matured
into a science, fabric producers have adapted to and adopted specifications substantially more
detailed than predecessor materials demanded. Fiber development has played a small role in meeting
these new requirements. More importantly, however, has been the ongoing dialog with users and
installers that created an atmosphere of trust and gave fabric producers sufficient comfort to
justify the purchase of new processing equipment to meet the upgraded standards.Another example of
market-driven development comes from Coville Inc., Winston-Salem, N.C., which is creating fabrics
for scuba diving. Traditionally, divers like to leave the water and not remove their wet suits.
With traditional materials, this practice often results in rashes from microbe growth under a wet
suit. Coville decided to try using antimicrobial polypropylene in a line of diving fabrics. By
talking to divers, the company discovered that, particularly in warmer climes, diving garments dry
in the heat of the sun from the outside in. The challenge was to reverse this natural sequence by
creating a product that would dry from the inside out, thereby minimizing possible microbe growth
and promoting skin health. The answer lay in combining antimicrobial filament polypropylene with
spandex. The fabric is napped on the inside to create a warmth layer and brings with it the wicking
capacity of polypropylene plus a natural resistance to microbes granted by additive technology.
Individually, all the described technologies existed; it took diver input to group them into a
solution. Coville sells a premium fabric and develops opportunities to translate basic technology
into traditional bathing suit distribution. Fiber suppliers sell premium, performing yarns.
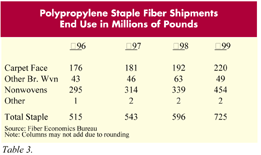
Technology DevelopmentsThe two cited marketing developments could not have worked
without advances in technology. Marketing is but one of the routes to added-value, niche markets.
Marketing has learned to work with development in an applied nature rather than as basic research.
Polypropylene producers are becoming increasingly adept at translating customer problems into
marketing opportunities incorporating marketing and technology advances.Lightweight filament yarns
are a small part of polypropylene distribution. Historically, the most successful filament olefin
markets have demanded heavy-denier fibers in the 200- to 1,000-denier range.Apparel has been the
holy grail for polypropylene marketers; polymer, fiber and fabric producers have searched for
apparel and home furnishings markets large enough to justify development of fine-denier products.
Until activewear developed around spandex in the late 1980s and early 1990s, polypropylene really
had little exposure in apparel.Following activewear, and development of antimicrobial polypropylene
additives, a natural marriage of two man-made fibers began to enjoy increased volume in the
traditional high-sweat markets of running, cycling and aerobics. Permanent color, wicking capacity
and antimicrobial advantages were wedded in a series of market-specific performance fabrics that
enjoyed vigorous growth among the Boomer and Gen X generation exercise fanatics.In addition to
diving and bathing suit materials, apparel fabric producers are modifying fabrics for running,
cycling and aerobics for a generation attempting to age gracefully, but still demanding hard bodies
and the visible trappings of success. Fabric developments continue apace to expand the fibers role
in activewear markets.Slow progress is being made in lightweight knitted and woven constructions
for apparel and home furnishings. Dyeable polypropylene has been the wish of fiber producers. It
currently is available in heavy deniers for woven rugs through KromaLon® polymer technology
developed by Equistar Chemical, Houston, but it is a long way from commercialization in fine
deniers for apparel and home furnishings. Considering the pressures from polyester and from
imported garments, we suspect that commercialization will continue to remain more a dream than a
reality. Fine denier, therefore, should continue to depend on marketing innovation and additive
technologies for growth.As might be inferred from the last paragraph, developments at the heavy end
of the polypropylene denier spectrum are much more active than those in fine deniers. For example,
the Clean Air Act and the Clean Water Act mandate levels of air and water cleanliness.
Polypropylenes low melting point often has prevented it from acting as a filter in hot-exhaust
environments. Copolymer research currently is providing higher-temperature materials to provide a
new growth market for polypropylene. Copolymers providing high strength are targeted for selected
industrial end uses like belts and geotextiles where tensile strength above current levels is
needed. In these markets, polypropylene will go head-to-head with polyester by bringing a
sufficiently strong material of considerably lighter weight at an anticipated lower
price. ConclusionsOur market background, always as a competitor to polypropylene, injected a
certain bias into this assignment. We are pleased to note, however, that completion of the work
convinces us that the polypropylene industry is populated with inquisitive managers who are
constantly peering around the next corner, not satisfied with the status quo. To be sure, in our
judgment, polypropylene always will depend on commodity-like materials if only because of the
fragmented nature of the supply chain. We are pleased, however, to have had the opportunity to
visit with some forward-thinking members of the industry and be convinced that they, and many of
their colleagues, are working hard to make sure that newness always is a hallmark of polypropylene
development and marketing.
Editors Note: John E. Luke is owner of Five Twenty Six Associates Inc., Bryn Mawr, Pa., a
consulting firm specializing in strategic marketing and operations facing textile fiber and fabric
manufacturers. He is also a professor of textile marketing at Philadelphia University.
August 2000
Vision Innovation Are Keys To Viability
Supplier PerspectiveBy Jim Phillips, Executive Editor Vision, Innovation Are Keys To Viability
American Savio/Somet CEO predicts prosperity for strategically inventive
manufacturers.Those pundits ready to sound the death knell for the American textile industry
would be well-advised to speak to Harold Hoke before making any final proclamations.Hoke, the new
chief executive officer of American Savio Corp. and Somet of America Inc., both located in
Spartanburg, S.C., shared his thoughts about the U.S. textile and machinery markets with ATI during
an exclusive interview several weeks before the June open house for Savio and Somet
(See related sidebar, page 100. He is anything but pessimistic about the future of the
industry.This is an exciting time to be associated with this industry, he said. Is employment in
the industry going to continue to decline Very likely. Are the numbers of companies and plants
going to decrease Almost certainly. Is the U.S. textile industry in the sunset of its existence Not
a chance.The U.S. textile industry is going to continue to grow, he said, but differently than in
the past. Mergers, partnerships, acquisitions and closings will continue, and those companies with
dedication to vision and innovation will continue to prosper.I see companies looking intently
toward new product ideas, innovative manufacturing alliances and new technology that is different
than the current easy decisions sometimes made, he said.Ive been fortunate in my association with
this industry that Ive been able to watch a number of companies some of them very old and
traditional make the transition from product-oriented companies to marketing-oriented companies.
These leaders are the first to embrace new technology and the first to realize the cost savings and
productivity enhancements that this technology entails. These are the companies that are truly
competitive in the global market.Hoke issued a wry smile and declined to name specific companies
not, he said, for fear of offending those laggards that havent quite caught on to what its going to
take to prosper, but, instead, from reluctance to omit a truly outstanding company.
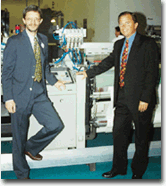
Dott. Fabio Mazzucchetti, president, Somet (left),and Harold Hoke, CEO, American Savio
andSomet of America, pose with the Mythos, Sometsrecent entry into high-speed air-jet
weaving. His resume indicates he has the credentials to both recognize and evaluate what it
takes to compete successfully in a worldwide textile market. Hoke holds a degree in textile
technology from Clemson University. Immediately upon graduation, he took a job with Burlington
Industries. For much of the past 20 years, he directed sales, marketing and service efforts for
Zellweger Uster, both in the Western hemisphere and worldwide, including sister companies in China,
Thailand, India, Germany, England and Brazil. He knows what it takes to establish a presence in
these countries and penetrate markets. As a result, he doesnt share the concern many American
textile leaders have expressed over the granting of permanent Normal Trade Relations (Ntr) with
China.Is this a potential problem for the U.S. industry he asks. Sure it is. But more than that, it
represents a real opportunity. China is, of course, a huge market, and not all of it is captured by
low-end products. There is demand in China an increasing demand for high-fashion products of
world-class quality. So in many ways, this could be a very good thing for those American companies
that will take advantage of it.I certainly would not be afraid of it, unless I didnt really
understand it and didnt have a plan to capitalize on it.Hoke continued: We hear so much about the
effects of the imbalance in world trade within the textile industry. But I think innovation comes
into play also. You dont see too many innovative third world countries when it comes to textiles.
They just produce cheap and sell cheap.On the other hand, every leading Italian and American
manufacturer is continually trying something new. I surely hope innovation wins this battle. If
not, the Paris, New York, and Milan fashion industry will surely suffer.As far as the textile
machinery industry is concerned, those companies that focus their resources and change the rules of
the game will thrive. The others, well, they can always just produce cheap and sell cheap. Its a
strategy, I guess, although not a very exciting one. As the captain of two major players in the
machinery market, Hoke is understandably more optimistic about the ramifications of Ntr status than
those mill owners who seem to be hammered year in and year out by trade imbalance and import
dumping. But his message is nonetheless clear. For the American industry to prosper to its
potential, more and more companies must make the transition to thinking in terms of global
marketing strategies. It is in hopes of capitalizing on such strategies that Hoke left his
comfortable position with Zellweger Uster after so many years to take the helm of American Savio
and Somet of America Inc. Both companies are owned by the Radici Group of Italy, with Savio being
the most recent acquisition. Savio manufactures yarn preparation/finishing machinery, while Somet
is a leading producer of weaving machinery.Both companies have been viable competitors throughout
the world virtually since their respective foundings, Hoke said. I think the answer to longevity
and tradition is innovation. Savio and Somet have truly presented, over many years, innovative
products and innovative, dynamic business strategies. For example, concerning marketing and
manufacturing leadership, Savio has developed strategic marketing and manufacturing partnerships in
India and China and, consequently, is a leader in both markets.Both companies have invested in new
product development and are now delivering the latest in winding and air-jet weaving technology.In
many ways, Hokes vision for the two companies parallels his assessment of the opportunities before
the American textile industry. His goal is to incorporate vision and innovation to maximize any
competitive advantage.Textile machinery companies, like our customers, have suffered financially in
the developed countries over the last few years, he said. You have already seen consolidations,
mergers, and, quite frankly, closings. This is where the financial strength and global marketing
strategy of the Radici Group has helped tremendously. The worldwide markets and successes of Somet
and Savio in developing markets have helped these companies maintain profitability even in these
past difficult several years.It is essential that we combine the technical strengths and
application knowledge of both companies in order to truly be capable of helping our customers solve
their business problems, he said. We are quickly moving to combine our sales, technical support and
service organization. Our company, with this broad knowledge base, will be the only one of its kind
in our industry. Our task is to clearly present the strong advantages of our equipment, especially
now that both Savio and Somet have unveiled technologically advanced new products
(See related sidebar below). Focus is critical, he said, for both Savio/Somet and the
textile industry in general. One of the most important aspects of success is listening to customers
and then acting. Research and development focus is critical. We must concentrate on fewer projects
those that yield the greatest return. If we cant do something as well asit needs to be done, we
will focus on what we do build better than anyone.My CEO at Zellweger Uster in Switzerland, Eddie
Bradley, practiced and implemented that, and it is easy to see the success Zellweger Uster had
because of such a philosophy. We at Somet and Savio understand where those areas of innovation
should be, we will invest heavily, and I am certain, if focused, we will be even more successful.
To be prosperous, innovation, risk, and dedication must not be strategic ideas only, but
implemented actions. Savio And Somet Showcase U.S. OperationsThe move of American Savio Corp.
to the location of its sister company, Somet of America Inc., has created new potential for the
U.S.-based subsidiaries of the Radici Group, according to Harold Hoke, CEO, American Savio and
Somet.The two companies are now combined in an expansive facility in Spartanburg, S.C., and are
merging sales, marketing and support staffs to capitalize on opportunities for new lines of winding
and weaving machinery.It is essential that we combine the technical strengths and application
knowledge of both companies in order to truly be capable of helping our customers solve their
business problems, said Hoke. Our task is to clearly present the strong advantages of our
equipment, especially now that both Savio and Somet have unveiled technologically advanced new
products.Those new products, the Savio Orion winder and the Somet Mythos air-jet weaving machine,
were on display at the companys open house and product demonstration in June.We are extremely proud
of these new products and fully expect the U.S. market to welcome such innovations in its search
for continued competitive advantages in its fight to battle the cheaper and increasing amount of
imported textile goods, said Hoke. If we do our job and can clearly present to the textile spinning
and weaving industries these advantages, Savio and Somet have a wonderful future. And there is much
more to come.Quite frankly, I couldnt be more excited about the future of both these Radici
companies.The Savio Orion winder, first introduced at the 1999 ITMA in Paris, is an innovation that
Hoke claims will change the rules of the game.The production and quality capabilities, if you study
the differences, are clearly superior to anything on the market at this point, he said. The
motivation behind development of the Orion series, Hoke said, was based on a thorough analysis of
customer needs. As a result, the company introduced a machine that would improve total quality of
the wound package, reduce overall process costs and increase manufacturing flexibility.The Orion is
available in two models, the Orion E, which is an independent winding machine, and the Orion I,
which can be linked to spinning frames. The frame for both is available in six- or eight-head
sections. The number of heads per machine ranges from a minimum of six to a maximum of 64 in steps
of two. Take-up speed ranges from 400 to 2,000 meters per minute.Somet is committed to developing
new technology in air-jet weaving. The Mythos, Hoke said, was tested for two years, 24 hours per
day, at 1,200 picks per minute.Somet conducted in-depth dynamic/behavioral studies to produce a
structurally strong loom that would be reliable at any speed. As a result, the Mythos requires no
anchoring, either mechanically or chemically. In addition, the Mythos can weave widths from 190 to
400 centimeters, and can accommodate up to six filling colors. The loom features automatic harness
leveling, a positive cam motion up to 10 harnesses and positive electronic dobbies up to 16
harnesses.In addition to the Orion and Mythos, the company displayed the Savio Geminis twister and
FRS open-end spinning machine and the Somet Super Excel HTP weaving machine.The Radici Group
worldwide forecasts sales in 2000 to top $1.5 billion. Combined revenues of American Savio Corp.
and Somet of America Inc. approach $25 million.Currently, Somet and Savio employ 33 people in the
46,000-square-foot facility.Savio moved from Charlotte, N.C., to the current location in January of
this year.
Below: Dott. Rino Morani, president, Savio, stands before the Orion, Savios latest-generation
winder.
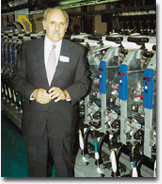
August 2000
People August 2000
EcomTextile.com, Fullerton, Calif., a newly formed Internet-based textile exchange, appointed
John C. Adams
CEO. Adams recently retired from his position of chairman, president and CEO, Russell Corp.
He also served as president of the American Textile Manufacturers Institute (ATMI), chairman of the
American Apparel Manufacturers Association (AAMA) and director of the National Cotton Council
(NCC), and on the Executive Committee of the American Textile Partnership.
N.C. State University, Raleigh, N.C., appointed
Dr. A. Blanton Godfrey
dean of the University’s College of Textiles. Godfrey, formerly chairman and CEO of Juran
Institute Inc. and an adjunct professor at the College of Textiles, was also named the Joseph D.
Moore Professor of Textile and Apparel Management Technology.
Cargill Dow, Minnetonka, Minn., appointed
Randy Howard
president of the company. Howard formerly served as director of growth and technology,
polyurethanes, Dow Chemical Co.
Buffalo Color Corp., Buffalo, N.Y., named
Jack Cabrey
president and CEO. Cabrey formerly was president and general manager of Sequa Chemicals
Inc./Sun Chemicals.
Rieter Textile Systems, Germany,
appointed
Uwe Teek
sales and marketing director, Synthetic Fiber Machinery. Teek has been with Rieter for many
years, both in Germany and in the United States.
Uwe Teek
BASF Corp., Mount Olive, N.J., named
Tilman Krauch
to head its Industrial Fibers Business Unit. Krauch is also group vice president, Fiber
Intermediates, and has been with BASF since 1990.
Gaston County Dyeing Machine Co., Stanley, N.C., announced that
Alex Franco
joined the company as director of international sales for Latin America.
New York City-based Cotton Incorporated named
Kathryn Gordy
Novakovic director, THE COTTONWORKS® Fabric Library.
WestPoint Stevens, West Point, Ga., announced new responsibilities and assignments within
its management team.
Joan Amberg
, senior vice president and president, sales, will add responsibility for the company’s
Canadian and Central/South American sales efforts to her existing domestic responsibilities. She
will also oversee the Product Management Group.
Paxar Corp., White Plains, N.Y., appointed
David Osiecki
vice president and general manager of the company’s Apparel Identifications Systems
Division.
Zellweger Uster Inc., Knoxville,
Tenn., named
Alvin Ellison
director, sales and service, and member of the Executive Committee. Ellison manages the
company’s sales and service activities in the United States and Canada and heads the IntelliGin
Business Unit. He also serves as site manager for the company’s facility in Charlotte, N.C.
Alvin Ellison
Burlington Industries Inc., Greensboro, N.C., announced that
Delores Sides
was promoted to director of corporate communications.
Avondale Mills Inc., Sylacauga, Ala., announced two appointments at Gregg Plant,
Graniteville, S.C.
Archie Coleman
was named manager, technical quality assurance for piece-dyed fabrics.
Mel Francisco
joined the company as plant production manager.
Alba-Waldensian Inc., Valdese, N.C., named
James Douglas Dickson Jr.
CFO.
William T. Walker
, senior vice president, operations and planning, will oversee the Sourcing organization,
directed by John Cafaro. The Customer Service, Planning and Logistics Group will also report to
Walker’s organization.
Donnie Hodge
was named senior vice president, strategic planning. He will report to David C. Meek,
executive vice president, finance, and CFO.
Scott Maddalene
was appointed vice president and managing director, European operations.
The U.S. Small Business Administration named
Avishai Nevel
, president, Lawson-Hemphill Inc., Central Falls, Rhode Island Falls, R.I., the 2000 Rhode
Island Small Business Exporter of the Year. The company’s international program, initiated in 1982,
accounts for more than 60 percent of its manufacturing revenues.
Johnston Industries Inc., Columbus, Ga., appointed
Ron Wright
senior vice president, sales and marketing, JI Fabrics Division.
Marshall and Williams Products Inc., Greenville, S.C., appointed
Blas A. Miyares
president of the company. Miyares previously was president of Küsters Textile Machinery
Corp.
Culp Inc., High Point, N.C., named
John H. Beason
vice president, specialty fabrics, with responsibility for the company’s sales to the
contract and hospitality markets.
August 2000