recession. Real GDP will expand by 3.4 percent, after a strong performance in 2000.Consumer
spending, business investment and exports will drive 2001s expansion.Our balance of trade for goods
and services will deteriorate, with a deficit exceeding $350 billion for the second year in a
row.Expect inflation to come down by nearly a percentage point from 3.4 percent last year.The
Federal Reserve is likely to reverse course by cutting short-term interest rates only if growth
slows down sharply.Hiring will slow down with non-farm payrolls rising 1.2 percent, after gaining
an estimated 2.1 percent in 2000.New homebuilding will remain above the 1.5 million mark in 2001
for the fourth consecutive year.Growth in industrial output will shift to a lower gear.Textile
industry results overall will be mediocre again this year. The U.S. economy was in the fast
lane over the last four years, with growth above 4 percent a year. In fact, last years growth,
estimated at 5.2 percent, was the strongest since 1984. After six interest-rate hikes since
mid-1999 and a sharp upturn in world oil prices, the U.S. economy is showing signs of weakness.
While the jobless rate, at 3.9 percent in October, was down again to the lowest level in three
decades, gains in non-farm payrolls have slowed to less than 150,000 per month. As oil prices
soared to more than $30 per barrel, up from an average of $17.50 per barrel in 1999, the inflation
rate climbed to 3.5 percent by October, up a full percentage point from a year ago. On the bright
side, the sharp upturn in oil prices had little impact on the core inflation which excludes food
and energy price increases. The concern of a slowing economy is more evident in the stock market
prices and, in particular, the technology sector. This, in turn, has added to the fears that the
economy may even go into a recession if the wealth effect kicks in, as some analysts fear.Another
concern is the value of the dollar as the trade deficit reached an estimated record $364 billion in
nominal dollars, an increase of more than $110 billion. While the U.S. trade imbalance reached a
new record, the U.S. dollar has gained strength in foreign exchange markets, particularly against
the Euro.
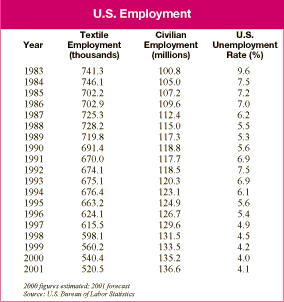
Despite all the concerns, the expansion the longest ever for
the U.S. economy is expected to remain intact for another year. The latest consensus forecast of
the Survey of Professional Forecasters, conducted by the Federal Reserve Bank of Philadelphia,
calls for a 3.3-percent growth in U.S. economic activity in 2001. Our econometric model of the U.S.
economy forecasts that real GDP will rise 3.4 percent this year, following gains of 5.2 percent in
2000, 4.2 percent in 1999 and 4.4 percent in 1998. Gains in consumer spending, business investment
in equipment and exports will power growth. Further increases in interest rates are unlikely, and
there is a possibility that rates will come down half a point from current levels. Job creation is
expected to decelerate, while remaining strong enough to hold the jobless rate marginally above 4
percent. Inflation will continue to be under control, assuming no further increases in oil prices
beyond $30 per barrel. The dollars value in foreign exchange markets is expected to decline, but
the drop will be modest.
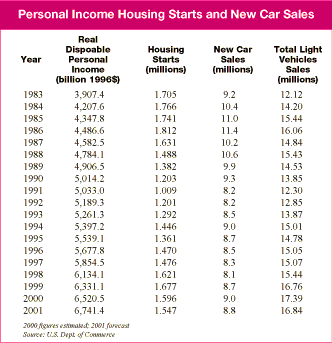
Factors Contributing To OutlookHere are the main reasons for
this outlook. With economic growth in Asia back in the fast lane, world demand for petroleum has
risen by more than a million barrels per day in the last two years. World demand rose to an
estimated 76.1 million barrels per day in 2000, up 6.2 million barrels from 1995, which was an
acceleration from an increase of only 3.9 million barrels in 1990-1995. It is not surprising that
OPEC had little difficulty pushing oil prices up to current levels. Despite a slowdown in economic
activity in the United States, the daily world demand for oil is likely to go up by another million
barrels in 2001, assuming normal winter conditions prevail. This means that OPEC will not be in a
rush to bring oil prices down by increasing production. As a result, oil prices are unlikely to
fall sharply from current levels. The U.S. refiners acquisition price of crude oil is assumed to
average $27.11 per barrel in 2001, down 2.3 percent from $28.95 per barrel in 2000, but up 55
percent from $17.50 per barrel in 1999. This means that the impact of slightly lower energy prices
on this years U.S. inflation rate will be small. With the U.S. population growing by 1.0 percent
per year and the labor force participation rate slowing down, the labor supply gain is capped at
1.4 percent per year. With the economy adding 150,000 jobs a month in 2001, the unemployment rate
will edge up to 4.1 percent from 4.0 percent last year. Faced with a slower growth and squeezed
profitability, the focus of employers will be on increasing productivity gains and tying
compensation to profitability. As a result, wage increases will be modest.
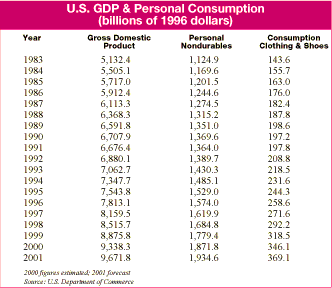
Assuming no major surprise, food prices are expected to move
up not more than the overall inflation rate. Thus, low inflation and a low unemployment rate will
continue to coexist for another year. Year-over-year inflation is seen rising by 2.5 percent in
2001, down by nearly a percentage point from the 3.4 percent in 2000. U.S. exports growth and a
gradual decline of the value of the dollar in foreign exchange markets will be a positive factor on
profits from foreign operations. With the overall industrial operating rate at 82.0 percent in
2001, virtually flat from 82.2 percent in 2000, growth in capital spending on plant and equipment
in manufacturing will follow suit. However, the big boost in capital spending on equipment in the
last five years came from investment in information- and telecommunications-related equipment. In
the telecommunications sector, only the major players can be expected to continue increasing
investment in replacements and on new technologies. With stock prices sharply down, smaller players
will have a tough time raising capital in the financial markets to expand investment. Furthermore,
many of the Internet-related start-up companies, which contributed to the growth in capital
spending on information equipment, are faced with the prospect of going out of business. In short,
real nonresidential investment is seen rising 5.5 percent in 2001, less than one-half the gains of
12.9 percent in 2000, 10.1 percent in 1999 and 13.0 percent in 1998.
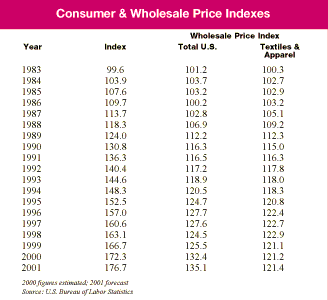
As the nations output of goods and services expands by 3.4
percent, non-farm payrolls are expected to increase by 1.8 million over the course of 2001 down
from an estimated 2.4 million jobs created in 2000. With low inflation, growing employment and
rising incomes, consumer spending will be quite healthy rising 3.4 percent in 2001, after surging
5.3 percent last year.Total sales of new light vehicles are expected to ease a bit to 16.8 million
units in 2001, from a record 17.4 million in 2000. This will be the third year in a row having
total unit sales above 16.5 million, and the eighth year above 15 million. New construction will
edge down to 1.55 million, from 1.6 million in 2000. Accordingly, the pace of consumer spending on
durable goods will slow down to 3.8 percent, after double-digit growth in each of the previous
three years.The balance of trade deteriorated rapidly last year, as the U.S. economy grew at a fast
pace and economic activity overseas was modest. Total U.S. exports grew 11.9 percent in nominal
terms and 10.1 percent in real terms, as economic activity returned to high growth in Southeast
Asia. Meanwhile, imports continued to be a sore point for the United States, even after factoring
out the impact of the sharp rise in oil prices. Strong domestic demand and a 3.5-percent
appreciation of the dollars value against most of the currencies combined to push imports up 13.6
percent in real terms in 2000. In current dollars, the trade deficit ballooned to an estimated $364
billion, from $254 billion in 1999.
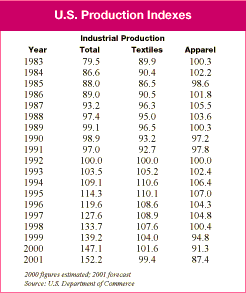
The return of high growth in Southeast Asia, coupled with a
small decline in value of the U.S. dollar in foreign exchange markets, will help U.S. exports in
2001 grow by 7.5 percent in real terms, led by capital goods down from an estimated gain of 10.1
percent last year, but a major improvement from the anemic increases of 2.9 percent in 1999 and 2.3
percent in 1998.Our growth in imports is expected to slow down, as U.S. economic activity
decelerates from 2000s booming rate. The end result, however, would be a small improvement in the
trade deficit in net exports of goods and services in nominal terms. With surpluses for the fourth
year in a row, after large deficits for nearly three decades, federal government spending adjusted
for inflation is expected to post a modest gain in 2001. This will be the third year in a row that
government spending grows, reversing real spending declines for eight consecutive years.
Furthermore, with the school-age population increasing, spending by local and state governments is
seen growing by 2.9 percent in real terms, down from 3.5 percent in 2000 and 3.8 percent in
1999.
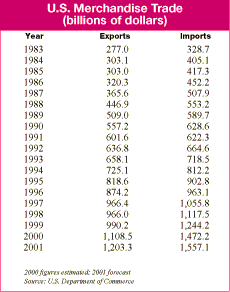
Textile Forecast Shows Little PromiseProspects for U.S.
producers of fibers, textiles and apparel are not very promising for 2001.Clothing prices have been
on the decline since 1992, except for 1998, falling by an average of 1.2 percent per year. The
decline in prices has contributed in part to the strong demand for clothing in real terms. In 2001,
total outlays for clothing and shoes are expected to grow 6.6 percent in volume and 6.0 percent in
dollar terms. Last year, spending on clothing and shoes surged 8.7 percent in volume and 7.0
percent in dollar terms. The trade deficit for apparel ballooned to an estimated $56.6 billion in
2000, from $48.5 billion in 1999 and $45.2 billion in 1998. Unfortunately, all the benefits of
increased domestic demand for apparel accrued to foreign producers because U.S. output of apparel
declined 3.8 percent last year, on top of a loss of 6.4 percent in 1999.Because U.S. industrial
output is expected to soften this year, industrial fibers and textiles will end at their current
levels. With the vacancy rate down to low levels, the addition of 1.8 million new jobs in 2001
bodes well for additional demand for office space and a small improvement in new construction. In
2001, investment in nonresidential buildings is expected to grow by about 1.5 percent in real
terms, after surging 8.5 percent in 2000. With after-tax corporate profits still up by 3.5 percent
in 2001, growth in business spending on carpeting and furnishings will slow down. Demand for
U.S.-made fibers, textiles and apparel is likely to decrease in 2001. Exports will make a minor
contribution to growth as economic activity overseas improves, while imports will continue to gain
ground, resulting in further deterioration in the trade gap.Despite a gain in economic activity,
production of domestic apparel and products is expected to decline in 2001 for the sixth year in a
row. In 2000, output was down an estimated 3.6 percent, after falling 5.6 percent in 1999. Textile
production is expected to decline 2.2 percent this year, after falling 2.3 percent in 2000 and 3.4
in 1999. Shipments by textile producers are expected to ease to $77.0 billion, from an estimated
$77.5 billion in 2000 and $78.3 billion in 1999. In a slowing economy with low inflation and still
a relatively strong dollar, wholesale textile and apparel prices are likely to remain essentially
flat for the second straight year.The outlook for the industrys payrolls is for a 3.7 percent drop,
down for the seventh year in a row. Payrolls declined 3.5 percent in 2000 and have declined by
157,200 jobs since 1994. Expect employment to average 520,000 jobs in 2001, down nearly 20,000 jobs
from last year. Finally, hourly wages will rise 3.0 percent in 2001.
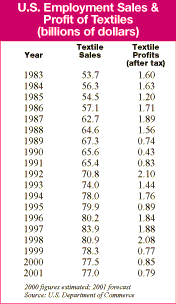
In a cutthroat environment, the industrys capital spending
will be concentrated on replacing noncompetitive capacity and increasing efficiency in order to
defend domestic markets from rising foreign competition. In 2000, growth for textile exports slowed
down to a meager gain of $0.1 billion, while imports rose by $1.0 billion, lifting the textiles net
trade deficit for 2000 to $6.3 billion from $4.4 billion in 1999 and $3.9 billion in 1998. Clearly,
the sharp appreciation of the dollar in the aftermath of the Asian crisis is partly to blame. While
the industry is to a large extent insulated from foreign competition due to its capital intensity,
the trade deterioration in the last three years is not likely to go away in the near future.
Moreover, in a low-inflation environment and with squeezed profit margins, rationalization is
unavoidable. With the industrys operating rate down to 81.1 percent from 82.3 percent in 2000 and
83.1 percent in 1999, this years textile spending on plant and equipment cannot be expected to
grow. Risks To The ForecastA major risk to our economic outlook is the uncertainty due to the
possibility of higher oil prices if there is any disruption in the Middle East. A jump in oil
prices will tax consumer budgets, which in turn will accelerate the slowdown in consumer spending.
In this case, economic growth will be in the 2.5- to 2.8-percent range in 2001. On the bright side,
if oil prices subside and fall below the $25-per-barrel mark, inflation will be lower and the U.S.
economy is likely to pick up speed in 2001, with growth at better than 4.0 percent.
January 2001