Chemical TreatmentandFinishingBy Edward J. Elliott PE, Ccol, FSDC How Meridian Improved Dyed Yarn RepeatabilityValdese plant gets a boost in quality and achieves an amazing 3- to 4-month payback. At the Meridian Industries Inc. Dyed Yarn Group Plant in Valdese, N.C., management is obviously attuned to responding to new technology as frequent changes in customer needs. Tim Queen, dyeing manager, says to achieve prime dyed quality depends on awareness of technology applicable to the companys need to dye approximately 300,000 lb/ 5-day wk, including acrylics, spun polyester, wool, rayon, cotton and blends, with yarn counts ranging Ne 1-150. Dye classes used are vat, direct, reactive, acid, basic and sulfur. Queen says, “About five years ago, most dyed yarns were for apparel. Today the accent is on automotive, homefurnishings and novelty yarns.”And a 200,000-lb inventory of specific manmade and blended dyed yarns allows Valdese to quickly respond to customers needs. Experience shows this to be of the utmost importance to Meridians customer base. Valdese has 18 Gaston County Dyeing Machine Co. package dye machines. The plant can dye up to 2,500-3,500 pounds of a dye shade. Gaston County Dyeing Machine controllers and process control system optimize dye machine performance. Paul Barnes, laboratory manager, says, “A Datacolor color match system is able to efficiently match about 75 shades per day from customer fabric samples, Pantone chips or Pantone fabric standards. Most matching is for new shades, not repeats.”
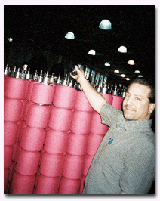
Wayne Powell, dyeing department supervisor, adds one of the company’s new caps to the dye tupbe spindle.Using a Datacolor (Gain) DyeMaster and 108-bottle laboratory dispense unit facilitates the duplication and repeatability of lab dyeings that are efficiently transposed to production package dye machines. Barnes says, “Often we require only 3-4 days from color match to shipping dyed yarn. And in some special cases, we have been able to complete the cycle in one day.”Queen says, “One of the many challenges a dyer faces is to compensate for the yarn shrinkage that occurs during the hot/wet process cycle.”You can expect each package to “shrink” about one millimeter. With eight packages on a spindle, a vertical shrinkage of approximately three inches plays havoc with dye liquor circulation. Usually, this shrinkage is addressed by cooling the solution, opening the dye machine lid, manually tightening the wing-nuts on each spindle, closing the lid and returning to operating temperature. This manual wing-nut tightening (capping) must be done after each separate hot liquid cycle (wet-out, dye, rinse, soap, etc.) so the dye/chemicals are uniformly applied to each part of every package. “Capping” is equally important in drying to preserve dye shade and attain uniform moisture content within all of the yarn.Queen says Valdese found that the patented R-TEX cap answered all the concerns about shrinkage. With the R-TEX principal of using the cap weight and gravity, the device automatically compensates for shrinkage within the machine, with no lost time for opening the kier. This dramatically improves dyed yarn uniformity, avoids the safety concerns of opening a hot kier, conserves cooling water needed to reduce kier temperatures to 190 F, improves machine usage and has a 90-120 day pay-back. With many dye stands containing 1,280 packages per load (in stacks of eight/spindle), wing nuts may be manually tightened in varying degrees of torque depending on operator effort/attention at any particular time. It is a technique fraught with myriad possibilities for chaos on a 3-shift, 5-day/wk operation.Valdese capital expenditures for color match prediction and lab dispensing was to ensure accurate shade samples. But, it’s axiomatic that lab results must be duplicated in production.
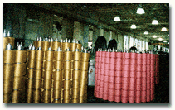
Many dye stands at the Valdese plant contain 1,280 packages per load (in stacks of eight/spindle). Manually tightening wing nuts results in varying degrees of torque, depending on operator effort/attention at any particular time. Valdese recognized that machine process controls were an important aspect of dyeing. But, process controls are dependent on the correct functioning of the parameters they control. It doesn’t help to have state-of-the-art controllers if the seal between yarn packages isn’t stable and assured. The installation of the R-TEX caps on all spindles has proven to be a practical and technological innovation.Queen concludes, “Our combination of lab techniques and strict control of production dye conditions have demonstrated the practically of lab-to-production dye quality controlaka, a high success rate in attaining first-time production dyeing. The Valdese mission statement is to be a customized supplier. The company can, and will, adapt its skills and technologies to match its customers.October 2001