Martin Color-Fi Granted Exclusive Rights by Clariant Corporation; ColorGuard(TM) Fiber to Enhance
Manufacturers Automotive Segment EDGEFIELD, S.C., Jan. 24 /PRNewswire/ — Martin Color-Fi Inc.
(“MCF”)announced today that it has been granted exclusive rights by the Clariant Corporation to
utilize Clariant’s new Nylostab S-EED(R) additive in the manufacture and sale of polyester fiber
for automotive applications. MCF isone of the leading producers of polyester for use in the
automotive industry and the agreement specifically covers this market segment in the United States,
Mexico and Canada. This unique fiber, introduced today by MCF as ColorGuard(TM), is stabilized
against the long-term effects of ultravioletlight and heat and provides an improved color
appearance. ColorGuard(TM) fiber is a preferred solution available in all of MCF’s demanding
applications as well as the automotive segment. Stephen A. Zagorski, President and CEO of MCF,
commented, “We view this new additive as enabling MCF to provide the next generation of solution
dyed polyester fiber.” Robert A. Post, Vice President of Clariant’s Additives Business Unit added:
“We are excited about the impact our product will have in the automotive segment and are pleased to
have the opportunity to partner with a significant player in Martin Color-Fi.” Martin Color-Fi,
Inc. is a leading producer of specialty staple fiber,both solution dyed and natural, for a wide
range of markets, including automotive, industrial, home furnishings, floor coverings, apparel, and
construction. The company also produces polypropylene and nylon staple fiber,in addition to yarn,
pigments and additives.SOURCE Martin Color-Fi, Inc.Copyright 2001 PR Newswire
Martin Color-Fi Granted Exclusive Rights To ColorGuard TM
AYSA Elects Little President
AYSA ELECTS LITTLE PRESIDENTThe American Yarn Spinners Assn. (AYSA) elected Charles L. Little president during its 34th annual meeting held in September at Sea Island, Ga. Little, president of Mount Vernon Mills Yarn Div., succeeds D. Harding Stowe, president and CEO of Stowe Mills.Members also elected James W. Chesnutt, (president and CEO of National Spinning Co.) as first vice president and Stephen G. Dobbins (president, treasurer and COO of Carolina Mills) was elected second vice president.Fred A. Jackson, president of AmericanandEfird, was re-elected treasurer and Micheal Hubbard was elected executive vice president and secretary.Hubbard replaces long-time AYSA head man Jim Connor, who is retiring. Connor, 64, will serve as an advisor to AYSA for another year.Hubbard, 33, is a native of South Carolina and graduated from Auburn University in 1990 after majoring in German and political science. He attended Heidelberg University in Heidelberg, Germany, and is fluent in German. He received a Masters degree from Baylor University in 1933 with a focus on diplomatic relations and international trade.Hubbard served in Washington on the staffs of Indiana Sen. Dan Coats and Rep. Barbara Cubin of Wyoming. Before joining AYSA in September 2000, he worked in the South Carolina Senate as director of research for the Senate General Committee.October 2001
Planit 2000 Knitted Goods Finishing Machine Introduced
Germany-based Novakust GmbH is offering a finishing machine, Planit 2000, that meets all the
requirements of product-specific finishing of fully fashioned knitwear parts before the parts are
sewn into a garment. The machine can be used for finishing all yarn combinations as well as
continuous finishing of fabric webs.All parameters for finishing quality including top and bottom
heat, steam dosage and temperature, decatizing roller contact pressure, production speed and
uncurling spindle speed can be set. Once determined, the process data can be saved and reused,
permitting exact reproduction of finishing results.
January 2001
West Point Stevens Finds Totes Final Piece Of Automation Puzzle
Materials HandlingBy Cosby W. Woodruff, Assistant Editor WestPoint Stevens Finds Totes Final Piece Of Automation PuzzleContainers allow Clemson plant to improve quality, cut costs.
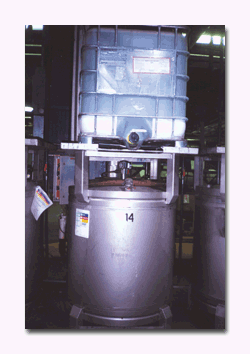
WestPoint Stevens sprawling Clemson (S.C.) complex is one of the largest and most diverse operations in the companys portfolio. Inside the walls of the four plants that make up the Complex, some 2,000 associates perform functions from opening bales of raw fibers to shipping finished bedding products that are complete with bar codes for the appropriate retail outlet.Like other major textile operations, WestPoint Stevens automated the Clemson Complex in recent years, and this presented specific problems for various departments.At Clemson Finishing Plant, one of the big automation needs was the ability to dispense dye ingredients from standard containers via an automated system. Clemson Finishing Plant Manager Billy Harris says the company spent a year working out a system of totes that allows the Bespoke automated dyehouse equipment to dispense just what a dye batch needs.The WestPoint Stevens team came up with a series of 64 fixed totescalled bottom toteseach with necessary plumbing, sensors and pumps. These stainless-steel fixtures hold the key ingredients for dyes and printing inks that go into WestPoint Stevens sheeting.Each bottom tote has a frame to support a top tote. The top tote is a standard off-the-shelf container that a chemical supplier ships full of a dye, pigment or other chemical. When the Bespoke system alerts the operator that one chemical is low in the bottom tote, the operator moves that tote, hooks up a tube to the top tote and lets gravity refill the bottom tote. When the top tote is empty, the operator simply replaces it with another one and the empty tote ships back to the chemical supplier.WestPoint Stevens rejected using the suppliers totes as the main container for several reasons. Installing the pumps, plumbing and monitoring equipment was not feasible on the supplier totes, which sometimes are little more than a plastic container on a wooden pallet with an aluminum frame.WestPoint Stevens was looking for something more permanent. So a company team drew a sketch of what would work and passed it on to Hoover Materials Handling Group, which developed what the company now uses.Requirements included a sloped bottom and no sharp corners where dyes may settle, then break loose, causing specks or uneven dyeing. The bottom tanks also needed to be a standard size, and market totes vary slightly from company to company.”There is no such thing as a standard tote,” Harris says. “We had to have a tote that was standardized.”Clemson Finishing Plants storage system allows its automated dye facility to do its job of anticipating what color will be required for the next run, locating chemicals needed to make it, gathering those chemicals from the totes, mixing the color and sending it to the dye pad.This saves the company money in several ways. WestPoint Stevens enjoys labor savings as associates no longer mix dyes by hand, and there is a quality gain. And because the machine only mixes what is needed, there is less waste. Clemson Finishing also gets productivity gains by being able to deliver the dye when it is needed.The plant no longer runs patches – the old way of ascertaining that a dye was the correct color. Now, the machine mixes the dye, it is checked against a prior sample, and the batch of material is dyed. Color changes can be achieved within 20 minutes.Clemsons fabric ranges 120- to 310-count sheeting, and it goes to Clemson Finishing Plant, along with fabric from WestPoint Stevens five other sheeting plants. Clemson Finishing Plant dyes in up to 400 colors, with more than 300 active at any time.
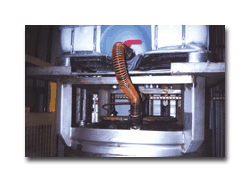
Chemicals shipped in manufacturers’ totes drain into WestPoint Stevens’ totes through a connecting tube.
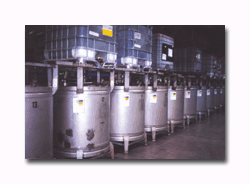
Totes line the floor at WestPoint Stevens Clemson (S.C.) plant. The containers store chemicals used in dyeing and finishing.November 2001
Salant Corp Acquires Tricots St Raphael
NEW YORK, Jan. 17 /PRNewswire/ — Salant Holding Corporation, a wholly owned subsidiary of Salant
Corporation (OTC Bullentin Board: SLNT), has announced the acquisition of Tricots St. Raphael
(Tricots), the designer knitwear collection. Salant acquired Tricots through an Asset Purchase
Agreement dated January 10, 2001, which was effective January 2, 2001. Salant is primarily known as
the manufacturer and distributor of Perry Ellis Menswear, which includes sportswear, dress shirts,
slacks and accessories, to retailers such as Federated Department Stores, The May Company and
Dillard’s. Tricots is one of the most prestigious labels in designer men’s sweaters and knitwear;
the collection is sold at Nordstrom, Saks Fifth Avenue and other better specialty stores. The
alliance with Tricots affords Salant the opportunity of adding an upscale tier to its distribution.
“Salant intends to maintain the design, merchandising and marketing integrity of the Tricots brand,
while enhancing its back office efficiencies through operational alignment,” stated Michael J.
Setola, Salant’s Chairman and Chief Executive Officer. “I am delighted with the dimension that our
new association will bring to the Salant organization.” The acquisition of Tricots, together with
the recent licensing arrangement with Tallia Uomo, an upscale contemporary men’s sportswear
collection, will strengthen Salant’s position in better channels of distribution. Setola continued,
“Through our continued efforts in forging new businesses and the appropriate alliances, Salant is
strongly positioning itself for the future. We are focused on marketing through multiple channels
of distribution, and on increasing our share of the total menswear market.”SOURCE Salant
CorporationCopyright 2001 PR Newswire
Letters Concerning Sept 11
LETTERS CONCERNING SEPT. 11(The following letter was sent by the National Textile Alliance to President Bush.)The PresidentThe White House1600 Pennsylvania Avenue NWWashington D.C. 20500Dear Mr. President:As our government and people respond to the barbaric events of September 11th, the members of the American Textile Alliance want to pledge our support for your efforts to fight back against those who have attacked our great nation.We represent various sectors of the United States textile industry, including suppliers in the cotton, wool, man-made fiber and textile machinery industries. The entire textile industry complex provides the U.S. military with approximately 13,000 different items made either partially or entirely from textiles.As we are key suppliers to the Armed Forces, we want you to know that we stand ready to do our part in the war on terrorism. We have already contacted procurement officials at the Defense Supply Center Philadelphia to make them aware of our readiness to help, as we did when they were confronted with the unique supply challenges of the Persian Gulf War.Mr. President, as you know, for the past several years, our members have been experincing tough economic times. They have had to deal with the pain of massive layoffs, plant closings and bankruptcies. But these economic hardships will not deter uswe will help shoulder the burden of meeting and defeating the threat terrorism poses to our American way of life.Sincerely.Alabama Textile Mfrs. Assn.American Cotton Shippers Assn.American Fiber Mfrs. Assn.American Sheep Industry Assn.American Textile Machinery Assn.American Textile Mfrs. InstituteGTMAAssociation of Georgias Textile, Carpet and Consumer Products Mfrs.Knitted Textile Assn.National Cotton CouncilNorth Carolina Mfrs. Assn.Norther Textile Assn.South Carolina Mfrs. AllianceTextile Distributors Assn., Inc.(Textile World also received the following letters regarding the Sept. 11 attacks)DEAR FRIENDSIN AMERICAThe information about the disastrous attacks on the United States shocked everybody here at Dornier immensely.We join you in your mourning for all the lives lost and deplore the horrible damages these brutal acts of terrorism have done to your country and the whole civilized world.May we assure you of our steadfast partnership with you, our dear friends and customers on the other side of the Atlantic Ocean.One of the most important cornerstones in the history of our company was the good and reliable business conducted with our friends in America. We have every intention to carry on this close relationship into the years to come, despite of the adverse conditions that exist at present.If you can think of any way we could be of assistance to you, please do not hesitate to call on us.Peter D. DornierHans GeigerLindauer DORNIER GmbH(The following letter is from Mexicos apparelmanufacturers association.)Dear AmericanPartner:Receive our greatest condolences for the unspeakable acts that have occurred in the last days. This association and its members are truly worried for your situation and the safety to your families. Please remember that you will have as always, all the support you need from Mexico. Think of us not only as a business partner, but as your friends, we will stand at your side in these and other situations.We send you our best wishes and thoughts, knowing the strong character and great determination of the American people.Sincerely,The Board and Membersof Camara Nacional de la Industria del VestidoOctober 2001
Partners In Success
After 23 years at one of the worlds largest producers of textile auxiliary products, long-time
friends and co-workers Ramon Navarro and Lorenzo Liste left the safety and security of the
corporate world to start their own company in Barcelona, Spain. The two friends, whose families
spend holidays and vacations together, worked 16-hour days, making sales calls during the day and
filling orders at night.Today, 14 years after Aplicaci Suministros Textiles, S.A. (Asutex) opened
its doors, the textile chemical formulator boasts $20 million in revenues; annual growth close to
30 percent; three production facilities on two continents; and market share across Europe, South
America and Asia. Along the way, Navarro and Liste sought key partnerships to offer the
highest-quality products and services to their customers. Genencor International, one of the worlds
largest biotechnology companies, became an integral part of Asutexs success. A Baby Is
BornWhen Navarro and Liste decided to leave the multinational company, friends and family were
astonished. Despite feeling really at home at the company, our desire to form our own firm was much
greater, said Navarro. We both felt we had the knowledge and experience to go out on our own, and
we didnt see it as a big risk.The company opened its doors in 1986 to produce and sell products for
preparation, dyeing, finishing, continuous printing and serigraphy. Asutex began with five
employees and 20 customers in a small warehouse near Barcelona. Navarro focused on sales and
marketing, while Liste concentrated on technical service and research and development. Daniel
Carreras and Arturo Ferrando, also from the multinational company, joined Navarro and Liste to
handle the dyes and warehouse responsibilities. Two years later, the companys rapid growth
necessitated its relocation to a larger facility in Barcelona the heart of Spains industrial region
in the province of Catalonia. The 11,000- square-meter facility, located 140 kilometers south of
the French border, houses the companys sales and marketing, customer service, research and
development laboratory, and warehouse. Today, the companys 65 employees produce 14,000 metric tons
of auxiliary products per year, plus 4,000 metric tons of liquid sulfur black at production
facilities in Barcelona and Portugal. Last September, Asutex opened a plant in Morocco.Never did we
expect the success that we have realized in such a short time, said Liste. We knew we had the
knowledge and experience, and we are so excited to see our baby has grown up. Long-Time
PartnersSeeking alpha-amylase enzymes for use in desizing preparations, Asutex discovered Genencor
International in 1990. In the last decade, the relationship between the two companies has grown and
flourished. Asutex has been instrumental in helping Genencor commercialize new products by
conducting trials on several new enzymes including IndiAge® Neutra, launched in 1999. Neutral
cellulases are key products for our stonewash customers in Europe and South America, and we were so
happy when Genencor developed this product, said Navarro. We are very pleased with IndiAge Neutra
enzyme; its the only neutral cellulase that we formulate for our end-users.
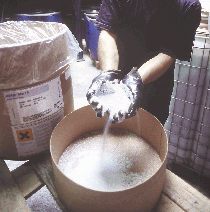
Genencor claims the IndiAge Neutra enzyme offers textile chemical formulators the most
flexible neutral cellulase available in the market today. The enzyme operates over a wide range of
temperature and pH, 40°C to 60°C and 5 to 9, respectively. Unlike conventional neutral cellulases,
the IndiAge Neutra product responds to variations in temperature and pH with only moderate changes
in abrasion activity. This flexibility allows processors to operate at lower temperatures than with
conventional products.IndiAge Neutra comes in both liquid and granule forms. IndiAge® Neutra G
enzyme features Genencors proprietary granule, which includes a patented Enzoguard® coating. These
granules are safer to handle than dusty powders and have improved features for easy blending and
storage stability. The IndiAge® Neutra L product is very beneficial for automated liquid feed
systems. We compared IndiAge Neutra G against other products, and we prefer to use it over anything
else because it is very easy to formulate and has the encapsulated enzyme technology, said
Liste. About GenencorGenencor International is a diversified biotechnology company that
develops and delivers innovative products to the health care, agriculture and industrial chemicals
markets. Using an integrated set of technology platforms, Genencors products deliver innovative and
sustainable solutions to many of the problems of everyday life.Genencor was established in 1982 as
a joint venture between Genentech Inc. and Corning Incorporated. Since its founding, Genencor has
grown to become a leading biotechnology company, with over $300 million in 1999 revenues, more than
250 biotechnology products in commerce, and more than 3,000 owned and licensed patents and
applications. Genencor, with more than 1,500 employees worldwide, has principal offices in Palo
Alto, Calif.; Rochester, N.Y.; and Leiden, the Netherlands. Long Hours, Hard Work Pay OffFor
the last 14 years, Navarro and Liste have logged long workdays and many kilometers traveling around
the globe selling their products. Their families continue to spend holidays and vacations together,
and they hope that one day their children might run the business. Through the ups and downs of
running a business, one constant has remained: their friendship. There are lots of people who say
our situation is unbelievable, especially after being friends for 30 years and continuing to work
successfully together, Liste said.Both owners also say they attribute much of their success to
forming partnerships with key companies like Genencor. We have always been interested in new ideas,
new products or new processes, and we appreciate it when Genencor calls us seeking our opinions,
said Navarro. From the first trial we ran of IndiAge Neutra G to participating in the University of
Genencor three-day textiles training seminar, we feel that by working together, we are a part of
Genencor, even though we are only a customer.
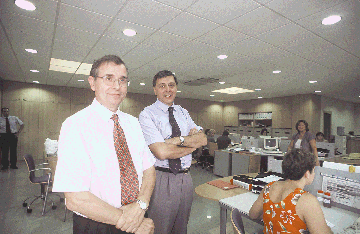
Long-time friends and co-founders of Asutex, Lorenzo Liste (left) and Ramon Navarro, turned a
start-up textile auxiliary company into a thriving business with 65 employees; three production
facilities; 30-percent annual growth; and market share in Europe, Asia and South America.
January 2001
Product Resource Guide
Product Resource GuidePumps, heavy duty, are for totes, tank and barrel washing. Units are designed for caustic, high-temperature and recycled fluids. Pumps have no cups, packings or seals and can run dry without damage. Hydra-Cell. www.hydra-cell.com
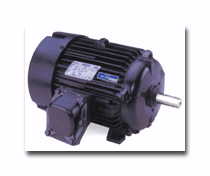
Motors, explosion proof, are for applications in hazardous environments containing explosive gases or dusts. Motors are available in single-phase power through 2 hp and in 3-phrase through 250 hp. Motors available in steel frames through 5 hp and in cast iron through 250 hp. Leeson. (262) 387-5239.
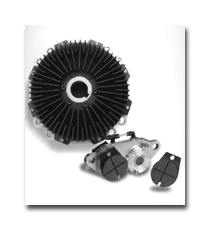
Brake actuator, UA, is a replacement for in-place brake systems for web converting machine. Actuator uses a dual-disk brake upgrade with anti-squeal friction pads. Each assembly has two pneumatic cylinders and four friction pads. Other features include quick-change release locks that allow pads to be changed in seconds, zero-maintenance piston and a 5-yr warranty. Dover Flexo Electronics. www.dfe.com
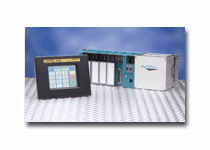
Operator interface, Model 2300, is a combination of a PLC and a motion control interface, offering a programmable touchscreen HMI, two connection ports, a programming port and a PS2 keyboard port. SoftPLC provides software and hardware products. Connection is by Winbuild 2000 HMI software and serial connection. Eason Technology. www.eason.com
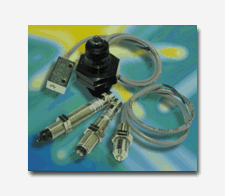
Switches, My-Con, offer repeatability to within 0.000040 in. and switch-point accuracy of +/-0.001 mm. Activitaging forces are defined by user between 30 and 250 grams. Units offer barrel-type housings, rectangular enclosures and M8 screw-on connectors. Standard activitating pin materials are offered, and devices are either a-c or d-c. Baumer Electric.www.baumerelectric.com
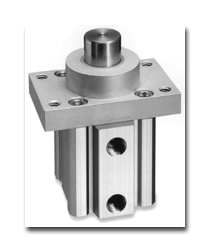
Actuator, conveyor-stop, bases on an EF1 cylinder, self-lubricating nylon-shaft bearing and compact size. Rod end of stopper cyclinder is modified with a flange and anchored with four bolts. Flange has a pilot with an energy-absorbing polymer bearing, and cylinders oversized piston rod maximizes effecting bearing area. These features give stopper a load resistance up to 65 lb at 10 in./sec. Bimba Mfr. Co. www.bimba.com
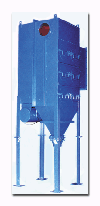
Dust collectors, PleatJet II, uses a horizontal cartridge filter design for easy maintenance and filter changes. A Venturi-Pulse cleaning system is included as a standard feature. An Opti-Pulse cleaning design optimizes energy from the pulse pipe, providing uniform dust release. Device offers all-welded construction without cantilevered supports. Models available to 50,000 cfm. Sly. www.slyinc.comNovember 2001
ATMI Offers Support For War Effort Against Terrorism
ATMI OFFERS SUPPORT FOR WAR EFFORT AGAINST TERRORISMThe president of the textile industrys national trade association has notified the defense supply center in Philadelphia (DSCP) that the U.S. textile industry stands ready to do whatever is necessary to support anti-terrorist military activities. He also has urged companies to make plans now to meet any additional military textile needs. According to the DSCP, the textile industry provides more than 13,000 items for the military, ranging from uniforms and combat gear to shelter and protection from extremes of weather and chemical weapons. Through two world wars and the conflicts in Korea, Vietnam, Panama and the Persian Gulf, the U.S. textile industry mobilized its resources to meet sharply increased demands of the military while continuing to supply civilian needs.In a letter to textile industry chief executive officers, Charles A. Hayes, president of the American Textile Mfrs. Institute (ATMI) said, “As our government evaluates the situation and decides on actions it will take, Ithought it prudent to urge each and every one of youregardless of the products you currently offerto immediately begin thinking of what your company can do if our nation calls on us for help.”He said ATMI has been in touch with DSCP and pledged the industrys cooperation in responding to the attack, and we have offered to work with them in any way we can should circumstances dictate that they need additional supplies of items currently produced or any new items that may be required. As part of its reorganization earlier this year, ATMI created a government textile procurement committee, under the chairmanship of Mike Kilkenny of Greenville Mills. That committee will be working closely with military procurement officials.At ATMIs 2001 annual meeting last March, Gen. Henry H. Shelton, chairman of the joint chiefs of staff, said the American textile industry has always been a “reliable partner of our nations military in times of peace and war.”In a related development, the Apparel Foundation immediately launched a program to provide apparel and footwear to victims and rescue workers. In New York City, there was a critical need for steel-toed footwear for fire fighters and clothing and blankets for other search and rescue workers. Many of those needs were quickly met by suppliers in the area, and the foundation is coordinating continuing offers of help from apparel and footwear manufacturers.October 2001
Dry-Heat Lamination Offers Options
Dry-heat laminating is best described as high-volume production bonding of two or more different
substrates in a continuous reel-to-reel operation, using dry adhesive, at relatively low
temperatures.Low-temperature laminating is an effective, controlled and flexible procedure, which
allows for a wide range of substrates to be bonded together on the same production line with quick
changeover times between production runs.The process of flat-bed, dry-heat laminating involves a
combination of heat, pressure and the speed at which the substrates are transported through the
laminating machine. The machine is a heating tunnel consisting of an upper and lower conveyor,
which sandwich and transport the layers of materials to be laminated, and inter-layers of adhesive.
The process relies on moving the upper and lower conveyors until they come into contact with the
materials, and then applying heat to the upper and lower surfaces of the sandwiched materials.
Heating is achieved through a series of parallel, electrically heated elements, which are sited
immediately behind both conveyors. The materials are transferred through this heating section at an
optimum speed, which ensures the inter-layers of adhesive medium are melted to produce a strong
bond between the materials.At the end of the heating section, the materials then pass through nip
rollers that run the full width across the middle of the machine. The nip rollers exert pressure on
the materials and molten adhesive, which spreads the adhesive, expels any trapped air and creates a
permanent bond.Immediately after the nip roll section, cooling of the laminate takes place. This is
achieved using parallel aluminum cooling modules, which are found immediately behind the upper and
lower belts. Refrigerated water from a central chiller system is pumped through the modules, which
cool the laminate and solidify and cool the inter-layers of adhesive. Finally, the product can be
rewound on a separate rewinding station after leaving the laminating machine. Dry-Heat
Lamination AdvantagesBecause of increasing worldwide concerns and legislation regarding the release
of toxic emissions into the atmosphere, as well as the need for clean, safer working environments,
textile and lamination companies have been forced to seriously consider cleaner, safer
alternatives. These concerns include the elimination of high isocyanate and chemicals emissions and
heavy energy usage associated with solvent- and flame-lamination processes. Moving to dry-heat
laminating technology can provide the following advantages: complete elimination of toxic
emissions; clean, dry and safe production processing; lower energy use; processing temperatures as
low as 80°C; controlled production with the ability to stop mid-flow without causing problems;
flexible or rigid bonding possibilities for different substrates up to 150 millimeters thick on
flat-bed laminating tunnels; fast or slow production speeds; heating and cooling both sides of the
lamination to reduce energy consumption; continuous reel-to-reel production or piece-by-piece panel
production; no shelf-life problems and no need for special storage conditions for adhesives; and
quick changeover of adhesives.The technology is being used by producers of laminated materials as
they come under increasing pressure to produce stronger and more durable textile laminates. Another
advantage is the ability to change production rapidly and automatically to cope with just-in-time
(JIT) manufacturing, while retaining quality control and process control, and eliminating
batch-to-batch variations as demanded by the customer.Textile laminates can be used in a wide
variety of end products. Some of the possible applications include: automotive interior components
(carpeting, headliners, air bags and seat construction); defense (gas-mask filters and body armor);
footwear and apparel uses (sports shoes, inner soles, interlinings and fabric coatings); and
medical uses (bandages, filters and protective fabrics), just to name a few. Adhesives
AvailableIn order to remain at the forefront of adhesion technology, adhesive manufacturers must
develop and produce the best adhesive solutions for new lamination technology. These producers have
invested a large amount of research and funding to develop the optimum adhesive medium for the
industry.One example of this adhesive technology at work is an automotive interiors application,
whereby the laminated substrate is subjected to temperature extremes over a continuous cycle
program to ensure the adhesives used will perform as intended during a vehicles lifetime. When used
in the production of an automotive interior laminate, the adhesives are expected to withstand
temperatures of more than 130°C to less than minus 40°C over a 900-hour continuous cycle. At the
end of this cycle, a delamination test is done to assess the adhesives performance. Only then is
the adhesive approved for usage.Obviously, with an infinite number of different substrates and
materials to be bonded, there needs to be a sizeable range of different adhesives available to
provide the optimum bonding strengths for different structures. There is also a need to provide
these adhesives in different formats to suit the applications. The most common formats in which
adhesives are available are webs, films and dry powders. These are normally derived from
thermoplastic compounds such as EVA, polyurethane, polyamide, polyethylene or acetyl. They can also
be provided in various widths and lengths to suit the application. They are inert and completely
safe. No special storage is required for these adhesive formats.These thermoplastic materials have
the ability to be melted again and again if necessary, which may be useful for multi-pass
laminating, whereby a user may prefer to build up the lamination layer-by-layer.There are also
thermoset adhesives, which, once heat-activated, will melt into the fabrics, set permanently and
give a very powerful bond.
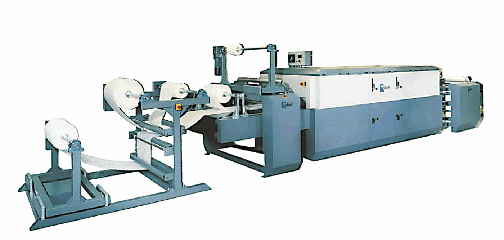
Benefits Of Low-Temperature BondingThere are several reasons why it is important to
maintain relatively low-temperature bonding for a wide range of substrates, including: ability to
process heat-sensitive materials; elimination of material shrinkage; prevention of laminating
problems, such as strike back and strike through; importance of maintaining the original appearance
of the materials; and possibility of lower temperatures and higher speeds in longer heating
tunnels.In most dry-heat laminating applications, processing temperatures between 60°C to 150°C are
the normal temperatures at which bonding between substrates will take place. The temperature will
vary, however, according to the thickness, density and number of layers of material through which
the heat must penetrate.It is also important that heating take place simultaneously above and below
the substrates to maximize process efficiency for best results. ConclusionBecause of industry
demands for faster production and shorter lead times with JIT manufacturing, as well as the
necessity to reduce or eliminate harmful toxic emissions, dry-heat laminating provides an excellent
alternative to and improvement upon traditional processes of flame, solvent and calendering
production.
For more information on dry-heat lamination technology, contact Ian Field, sales manager,
Bandwise Reliant Ltd., United Kingdom, at 44 01494 792299.
January 2001