Channeled fibers, with their increased capillarity, offer interesting possibilities for enhancing a textile’s performance. Morrisville, N.C.-based Allasso Industries Inc.’s Winged Fiber™, developed in collaboration with North Carolina State University’s (NCSU’s) Nonwovens Cooperative Research Center, is exhibiting remarkable filtration and cosmetic delivery performance; and has potential
applications in tissue scaffolds, hemostatic bandages, battery separators, insulation and apparel. The bicomponent fiber comprises a shaped core polymer and a sacrificial polymer that are coextruded
through a specially designed spinpack. The core features from eight to 32 deep channels between uniform, straight-edged wings. The sheath polymer fills the channels during fiber formation and is dissolved during finishing of the final product.
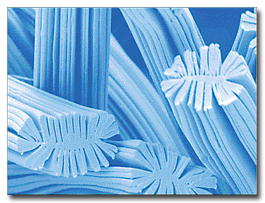
A typical 10- to 20-micron Winged Fiber is oblong. Its complex shape makes it much more flexible than a solid fiber, said Allasso Industries President Walter Chappas, Ph.D. The fiber can be tuned for a specific use by adjusting the width of the wings and the number of channels. It also can be made in a circular configuration, or even a Y configuration with each leg having its own wings.
The Winged Fiber is very lightweight and has the same total surface area as the equivalent volume of 300-nanometer nanofibers. “There has been a lot of interest in developing filtration materials using nanofibers, but there are problems,” Chappas said, noting high costs and fiber
compaction. “They filter beautifully, but the pressure drop goes way up, which prevents air or water, as well as particles, from going through.” The Winged Fiber, in contrast, holds its structure to allow air or liquid to flow through continuously. In filtration applications, dust or other particles first fill the channels, allowing air or water to pass through the spaces between the fibers for a longer time before the particles begin to fill those spaces. Therefore, pressure drop is minimized, and the filter functions effectively for an extended time.
Nano Filtration Technologies LLC (NFT), Pittsburgh, manufactures media for high-efficiency particulate air (HEPA) filters using an electrostatically charged polypropylene Winged Fiber spunbond. The filters produced from this media, branded LEAF™ (Low Energy Air Filtration), are claimed to have 250-percent greater loading capacity than traditional HEPA filters; and offer more efficient air flow, lower energy consumption, a longer filter life and lower filter costs. The same material is going into facemasks for industrial and medical uses.
HEPA filters made from NFT’s electrostatically charged polyropylene Winged Fiber LEAF™ filter
media are claimed to have 250-percent greater loading capacity than traditional HEPA filters, among
other benefits.
Korea-based La Care’s facial mask made using a nylon Winged Fiber spunbond is loaded with moisturizing and rejuvenating essential oils and creams. The mask conforms to facial contours and holds in place.
La Care’s cosmetic facial mask made using a nylon Winged Fiber™ spunbond is loaded with
essential moisturizing and rejuvenating oils and creams.
Researchers at the Joint Department of Biomedical Engineering, colocated at NCSU and the University of North Carolina at Chapel Hill, are growing stem cells on a Winged Fiber substrate to create bone tissue, and report promising results.
Allasso has demonstrated that continuous filaments of the fiber may be suitable for knitted and woven apparel applications. Also in the works are staple fibers of various lengths to suit a range of nonwoven and yarn spinning processes.
For more information about the Winged Fiber™, contact Walter Chappas +919-890-3803; wchappas@allassoindustries.com; allassoindustries.com. Go online to TextileWorld.com for archived Quality Fabric articles.
September/October 2012