VIENNA / SALZBURG, Austria — August 14, 2025 — OETI is partnering with Austrian designer Julia Deiger, founder of the sustainable label DeLin. INSPECTED QUALITY is a quality label from OETI for textile and leather businesses. Based on OETI’s 60 years of market experience and current standards, the label is supported by a transparent labelling guideline and independent verification processes.
The initiative is part of TEX-DAN, an EU-funded project led by the Salzburg University of Applied Sciences, which aims to develop innovative, market-ready concepts promoting circular economy models for small and medium-sized enterprises in the textile sector across the Danube region.
As an accredited and independent testing institute, OETI – Institute for Ecology, Technology and Innovation GmbH brings its extensive expertise to this project partnership. Together with designer Julia Deiger, OETI has developed the new INSPECTED QUALITY “Regionally Produced” label.
This label confirms the strong regional focus and sustainable philosophy of the DeLin brand: the entire value chain is based exclusively in Austria, using only natural, durable materials. The label enhances transparency for consumers and highlights the brand’s commitment to resource-efficient textile production.
Through this project, OETI and Julia Deiger are making a valuable contribution to promoting future-oriented, locally rooted production models within the European textile industry.
Verified Quality Builds Trust
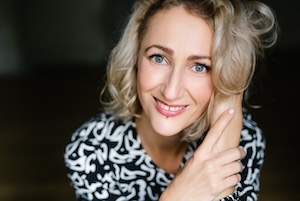
“The label makes these quality features visible to end consumers and enhances transparency across the textile value chain. Brands like DeLin benefit by being able to credibly communicate their commitment to sustainability and regional sourcing. With independent verification by OETI, their products gain additional trust and a unique market position,” explains Dr. Miriam Scheffelmeier, Head of Marketing & Sales at OETI.
“This cooperation means a lot to me. I believe in my brand DeLin and in regional production – a sector with great potential. A certificate like this offers a great opportunity to increase visibility and strengthen authenticity,” adds Julia Deiger.
A Model for Market Transformation
“The TEX-DAN project generates new, marketable ideas for advancing circular economy models across the Danube region. Our collaboration with Julia Deiger demonstrates how natural materials, short supply chains, and regional production – supported by a structured quality assurance system and visible label – can collectively drive transformation in the textile sector,” concludes Helene Melnitzky, Head of Department Ecology / OEKO-TEX® Products, at OETI, who is responsible for developing the INSPECTED QUALITY “Regionally Produced” label.
Posted: August 18, 2025
Source: OETI – Institute fuer Oekologie, Technik und Innovation GmbH