Spartanburg, S.C.-based Spartan International closed suddenly May 4, leaving 1,200 workers in six plants and the corporate offices without jobs.After defaults on financial agreements, assets of the company were seized by General Electric Corp., Fairfield, Conn. The management of the company made the decision to offer us peaceful possession of the assets, the collateral behind the loan, said John Oliver, spokesperson for General Electric, Stamford, Conn.Spartan had been a customer of General Electric since June 1999 but had trouble as early as December 1999, Oliver said.The six mills affected were the Spartanburg plant; the Rosemont plant, Jonesville, S.C.; the Jefferson plant, Jefferson, Ga.; the Cleveland-CaroKnits Lawndale plant, Lawndale, N.C.; the King Finishing plant, Statesboro, Ga.; and J.P. King Manufacturing, Augusta, Ga.Spartan President Barry Leonard said, We worked hard for several months trying to save the jobs of the 1,200 associates at Spartan International. We tried day and night to do that. Its a shame this is the result.Leonard blamed the companys problems on the economic slowdown and imported products.
Brilliant Ideas
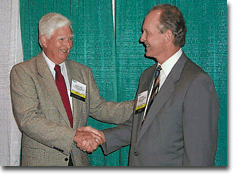
Ted Wirtz (right) congratulates Wayne Hays, recipient of the inaugural IDEA Lifetime
Achievement Award. The nonwovens industry was center-stage at the IDEA01 show held March 27-29
in Miami Beach, Fla.The Association of the Nonwovens Fabric Industry (INDA) and Nonwovens Industry
magazine sponsored the inaugural IDEA01 Achievement Awards, which were presented during the opening
keynote session of the conference at the Miami Beach Convention Center.Wayne Hays, a founding
member of INDA, was honored with an award for Lifetime Achievement in the nonwovens industry. Ted
Wirtz, INDA president said, There are very few people in the world of nonwovens who do not know
Wayne Hays, and certainly everyone owes him a debt of gratitude for his pioneering work during the
formative years of our business.Six additional awards were presented. The 18 finalists are listed
here along with pictures of the award recipient in each category. Every company that was nominated
contributed significantly to the outstanding growth of the nonwovens industry, said Wirtz.Look for
a review of the IDEA01 show by Richard Mansfield in the June issue of
TI.
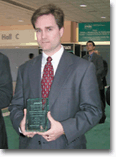
IDEA01 Fibers and Raw Materials Achievement AwardEastman Chemical Co., Kingsport, Tenn.:
Eastar Bio Copolyester (pictured: Jon B. Woods, business unit manager, Packaging, Film and Fiber,
Eastman Chemical Co.)Fiber Innovation Technology, Johnson City, Tenn.: Bicomponent and Specialty
Polymer Staple Fibers3M, St. Paul, Minn.: Nextel Flame Stopping Dot Paper
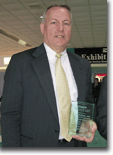
IDEA01 Equipment Achievement AwardDilo Systems Group, Charlotte, N.C.: Hyperpunch Needlelooms
(pictured: Klaus G. Maitre, executive vice president, Dilo Systems Group).KT Industries Inc., Fort
Wayne, Ind.: Stac-PacRieter-Perfojet, Greensboro, N.C.: AirLace 2000
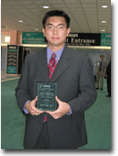
IDEA01 Rollgoods Achievement AwardPTI Inc., Christiansburg, Va.: K-Flex Ballistic Protection
Material (pictured: Alexander J. Park who accepted the award on behalf of his father, Andrew D.
Park, president, PTI Inc.)Freudenberg Nonwovens Group, Durham, N.C.: EvolonKimberly-Clark, Neenah,
Wis.: Intrepid Filter Material
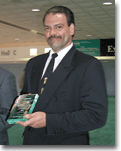
IDEA01 Short-Life End Product Achievement AwardProcterandGamble, Cincinnati: Swiffer
(pictured: Alex Cedeno, associate director, product development, fabric and home care, P and
G)Clopay Plastic Products Co., Cincinnati: Breathable LaminatesKimberly-Clark, Neenah, Wis.:
Huggies Little Swimmers
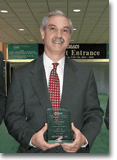
IDEA01 Long-Life End Product Achievement AwardColbond, Enka, N.C.: Electrostat (pictured: Don
L. Brown, director, salesandmarketing, flooring/automotive, Colbond Nonwovens).All Felt/Hollinee,
Ingleside, Ill.: Electrostat Western Nonwovens Inc., Carson, Calif.: PolarGuard
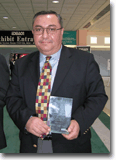
IDEA01 Entrepreneur Achievement AwardMogul SpunbondandMeltblown Nonwovens, Composites, Turkey
(pictured: Ekrem Kayali, Mogul SpunbondandMeltblown Nonwovens, Composites).Jentex, Buford,
Ga.VersaCore Industrial Corp., Kennett Square, Pa.
May 2001
Zimmer To Build Polyester Plant In India
Germany-based Zimmer AG and India-based Lurgi India, have been commissioned by the Indian South
Asian Petrochem Ltd. (ASPET) to supply and construct a polyester plant in Haldia, West Bengal.The
plant comprises a continuous polyester polycondensation unit and a solid-state polycondensation
unit to produce 400 tons of PET granulate per day. The total investment is approximately EUR 110
million, and the plant is due to go on-line in 2003.Zimmer will provide the technology, engineering
and equipment for the production plants, while Lurgi India will supply all ancillary facilities,
including engineering, for the erection of the complete plant.
May 2001
Fehrer AG Acquires Intellectual Property
Austria-based Fehrer AG has recently acquired North Adams, Mass.-based Morrison Berkshires
Papermaking Clothing Equipment (PMC) needling and finishing intellectual property. To ensure the
accurate transfer of the technology and to maintain future progression of the PMC finishing
machinery, Fehrer has hired Morrison Berkshires design engineer, Sadao Yagi.According to company
officials, Fehrer will now be the only machinery builder that can supply complete wet-felt
facilities with all capital equipment from fiber preparation, carding, cross-lapping, pre-needling,
finish-needling, heat-setting and finishing
.
April 2001
Ciba Specialty Chemicals Announces New Simplified Company Structure
Armin Meyer, chairman and CEO of Switzerland-based Ciba Specialty Chemicals, announced a simplified
company structure aimed at increasing profitable growth.The core of the strategy features an
alignment of business operational activities along customer industries. Ciba hopes this will
increase its speed of decision-making and accelerate the companys repositioning away from offering
just products to offering total integrated solutions with one face to the customer.The existing
nine business units will be grouped into five segments, and the divisional level will be
dissolved.Plastic Additives is headed by Felix Meyer and comprises the old Polymer Additives and
Process and Lubricant Additives business units. Coating Effects includes the Imaging and Coating
Additives and Colors for Inks, Paints and Plastics business units. It is headed by Hermann Angerer.
Water and Paper Treatment, a combination of the Paper Chemicals and Water Treatments business units
is headed by Mark Garrett. Textile Effects, headed by Christoph Biedermann, joins the Colors for
Textiles and Textile Chemicals units. Home and Personal Care, led by Tim Schlange, remains focused
on the same industry and will be adapted according to the new organization.Armin Meyer said, The
new simplified structure is aimed at increasing growth and profits and not at primarily saving
costs. We are creating five strong segments focused on their respective markets with all the
opportunities to respond faster and more efficiently to customer needs, to increase customer
relationships and to boost innovation.
April 2001
Speizman Industries Martint Agree To Joint Venture
Speizman Industries, Charlotte, N.C., has signed a joint venture agreement with Martint Equipment
Co., Cornelius, N.C., to distribute Braun dye/extracting machines worldwide. Martint has the
exclusive right to sell Braun dye/extracting machine principally to the textile industry through a
worldwide distributorship agreement with Syracuse, N.Y.-based G.A. Braun Inc.The terms of the
agreement between Speizman and Martint end in January 2004. The companies have agreed to work
together to acquire additional textile wet-processing equipment rights. We are excited about
selling Brauns pocketed textile-dyeing machines in North America and other international areas that
we feel are poised for growth. This joint venture will combine the strengths of Martints sales and
marketing department and Speizmans global network of sales agents and reputation for service, said
Robert S. Speizman, president and CEO, Speizman Industries.
April 2001
The Blue Revolution
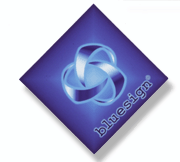
The Blue Revolution
bluesign® Technologies promotes eco-compatability throughout textile-processing supply
chain. A new revolution is underway in industry, and it is starting in the textile and
apparel sector. There is a difference, however, between this new revolution and the Industrial
Revolution that began in the 18th century and completely transformed production processes. That
earlier revolution also sped up the processes that have polluted the air and water, created toxic
substances that threaten human health, caused climate changes and depleted natural resources. The
new revolution aims to halt the progress of environmental degradation by using only those
materials, technologies and processes that cause no harm to the environment and result in products
that are safe in all aspects for consumption and use by humans. Blue Is For CleanThe
Industrial Revolution is often associated with the color black, suggesting coal, smoke, iron and
black gold. The revolution taking place today often associated with the color green, which
signifies the earth can also be linked to the color blue, which represents clean water and air, as
well as purity in general. Switzerland-based bluesign® Technologies AG, a new consortium dedicated
to promoting and facilitating environmentally sustainable, toxin-free textile production, is
currently involved in the research and development of new processes, technologies and components
for the manufacture of apparel.
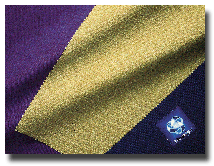
Consumers looking for apparel guaranteed to be free of toxic substances and produced without
causing environmental harm can look forward soon to a day when garment hang-tags will certify the
eco-compatibility and safety of garments that conform to the new bluesign Standard. At the same
time, comfort, design and functionality levels of these new products will not be compromised. Since
1997, bluesign has been working in partnership with a number of textile and textile-related
companies in efforts to develop and market new products. With regard to textiles, the consumer
wants a simple and clear orientation system he can trust, states Dr. Cornelia Voss, nutritionist
and head of the Textile Department, Wissenschaftsladen Bonn e.V. Zentrum fur burgernahen
Wissenstransfer, Germany. Credible concepts for the greatest possible freedom from toxins, safety
and transparency are also receiving the support of powerful consumer and environmental
associations.Of course, the move to improve and clean up production processes and develop
sustainable technologies and products has gained momentum in recent years, and, indeed, is mandated
by certain government policies and laws.
TI has reported on a number of other efforts to this end in the textile community
including efforts in the carpet industry and Cargill Dows development of synthetic fibers using
polylactic acid (PLA) from corn sugars. Among bluesigns objectives is the creation of a network
throughout the textile product supply chain of companies dedicated to using environmentally safe
and responsible methods and materials at each step in the manufacturing process. First
Products In The MarketplaceThe first products of bluesigns venture, made from synthetic fibers,
have recently been introduced to the marketplace. Switzerland-based Schoeller Textil, a company
known for its innovative performance fabrics, has produced a line of polyester fabrics made
entirely without the use of environmental toxins. This new production process lowers energy
consumption by 85 percent and water consumption by 75 percent.The new production process for these
fabrics requires less raw materials and eliminates toxic by-products, said Tom Weinbender,
president, Schoeller Textil USA, Seattle, Wash. The quality of these cutting-edge fabrics is not
compromised in any way, resulting in the same high standards that Schoeller customers expect.
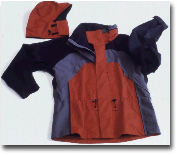
Schoellers new line includes a variety of fabrics, from soft and drapable microfiber fleece
knits to durable and rugged lightweight rip-stop weaves. In addition, the companys own Nano-Finish,
developed using nanotechnology applications in accordance with the bluesign Standard, provides
optional water- and soil-repellent attributes to the fabrics.Other development partners or
licensees in the bluesign system include Acordis, Ciba, 3M, Ems-Chemie, Eschler, Gortz KG
(Greenpeace products), KUAG, Nike, Prym, Rudolf Chemie, and Trevira.These partners are licensed by
bluesign to use its technologies, and their production processes are monitored to ensure that the
bluesign Standard will be maintained in products using the companys name. In turn, bluesign
reinvests the fees paid by these companies in new research. Licensees have access to bluesigns
entire body of knowledge; compatible components, processes and technologies; and engineering
services. The products are marketed by the labeling of bluesign® brands, company-brand
communication and distributor support.Leaders in science, environmental policy, industry, and
environmental and consumer organizations are monitoring bluesigns work. Research institutes
associated with the system include ETH Zurich, Tex-a-Tec and oko-Institut Freiburg. In addition,
bluesign is in a technology partnership with the Steilmann Group to develop new polyester textiles
that comply with its standards. What’s Blue And What’s Blackbluesign has placed products,
substances and technologies into three categories, according to their degree of compliance with its
standards. The bluesign standards exceed those set forth in oko-Tex Standard 100, the European
standard established in 1992 for the environmentally responsible production of textiles.The
bluelist includes products, substances and technologies that make the entire production chain as
toxin-free as possible and demonstrate totally environment-compatible behavior from raw materials
processing (including fiber and dyestuff manufacture) through fabric finishing and garment
manufacture. The list also embraces consumption and disposal methods. It includes:single-sort
materials that are easily reduced to their raw materials and are recyclable in raw-material form
(e.g., polyester into terephthalic acid and glycol);innovative technologies, such as
nanotechnology;the use of sustainable raw materials, such as cornstarch;catalyst systems that
comply with the bluesign standards;disposal methods that allow bio-compatible materials to break
down aerobically or anaerobically; anddisposal methods by which non-bio-compatible materials are
mineralized into carbon dioxide and water, so that their residues are bio-compatible.Next in rank
is the greylist of Best Available Technologies (BAT), comprising products and technologies that are
the best currently available. They are being used in the interim, but they will be improved upon as
better technologies become available, and once deemed eligible, they will be transferred to the
bluelist.Last is the blacklist of hazardous substances and technologies. These items will never be
used in the manufacture of bluesign-licensed products. The blacklist includes any substances that
have potential carcinogenic, mutational or adverse reproductive effects; that accumulate in water
or living organisms; or that have toxic or hormonal effects on living organisms. Included on this
list are antimony, mercury compounds, polycyclic aromatic hydrocarbons (PAH), tributyl tin (TBT)
and chlorine bleaching, among other items. Ecology And High-Tech Go Hand-In-HandEco-efficiency
is defined by bluesign as the relationship between the overall expenditure of nature and the
specific benefit per project or service unit. As Peter Waeber, CEO, explains: Ecology and high-tech
are not opposites. On the contrary, we can only observe our responsibility to living and future
generations by using the most modern technology. Ecological is no longer synonymous with hand-knit
We will be able to treat sustainable raw materials such as corn starch so that they display the
functions of modern chemical fibers and can be returned to the natural cycle at the end of their
useful lives.Another example of the ecology/ high-tech connection is the use of nanotechnology to
develop new textile-finishing processes that can imbue fabrics with various properties, including
dirt- and water-repellency, by changing the molecular structure of the fibers. Fabrics having dirt-
and water-repellent properties behave in the same way as a lotus leaf, which repels dirt and water
due to its rough, scale-like surface. The use of nanotechnology to create these properties in
fabrics eliminates the need to use halogenated compounds to achieve the same effects.Driving home
the importance of implementing eco-efficient practices is the fact that normal industrial
production creates 30 tons of waste for every one ton of finished product.
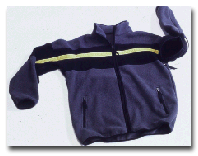
The products of nature are not necessarily excluded from bluesigns efforts to develop new
eco-friendly products, although the consortium is concentrating on improving production of
synthetics because, in general, their manufacture generates more toxic pollution than the
processing of natural fibers. The key to compliance with the bluesign Standard is the use of
environmentally responsible cultivation, harvesting and processing methods. In the interest of
eco-efficiency, the bluesign system is promoting the following goals and ideas:Harvesting,
processing and finishing of raw materials and products must all be accomplished in an intelligent,
economical, environmentally safe (including toxin-free) mannerIntelligent solutions combine
eco-efficiency with a high degree of functionality, design and quality; combine nature and
technology; and use sustainable energies, such as solar and hydrogen energy.The elimination of
harmful materials and processes begins in the design stages of a product; hazardous substances and
technologies are never even considered to be viable. Science Is A Better Tailor Than NatureIt
is bluesigns contention that by pulling knowledge from the entire spectrum of textile processing,
studying natural processes and mimicking them, and taking a holistic approach to synthesizing it
all, scientists are able to achieve the best solutions for eco-friendly production. bluesign is
constantly updating research and development, as well as its own standard, to maximize the
environmental benefits of the products manufactured under its license. New processes, technologies
and components are put in place as soon as possible to ensure the best solutions are being used at
all times.Looking toward the future, bluesign plans to develop technologies for the polyamide field
and for new synthetic fibers produced from sustainable raw materials. In addition, Schoeller is
working on developing new processes for the production of nylon.bluesign is also pursuing further
developments in process and mechanical engineering, as well as environmental technologies. Among
the current projects are the vatting of indigo or copper dyestuffs and waste-water treatment
through anaerobic breakdown.Another new development is corfix, a new, patented process technology
to be used in pretreatment, dyeing or finishing. The process improves dye absorbency considerably
and requires much less energy and water than do other processes currently in use. The machinery to
be used in the process is being developed by Switzerland-based Tex-a-Tec, one of bluesigns
technology providers.
April 2001
Stork Offers New Version Of Its Color Physics System
Netherlands-based Stork has introduced the 4.1 version of its Color Physics System (CPS), a
software program for color measurement, recipe calculation and correction. CPS now runs under
Windows NT and features an open interface that allows easy communication with any CAD system. The
program converts color information on designs and colorways into color recipes, as well as
transmitting information on the available basic colors to the digital pre-print systems. The CPS
can be linked directly to a Stork IPS2/Saturn color kitchen for automatic recipe dispensing and
forwarding design/colorway information to production. Stork lists cost savings, flexibility and
efficiency as some of the advantages offered by the software. The CPS will determine which
dyestuffs should be used and what the maximum dyestuff yield should be, as well as indicating the
price per calculated recipe.
April 2001
Erhardt Leimer Offers Enhanced Control For Web Systems
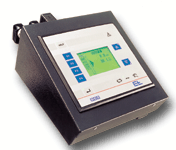
Erhardt+Leimer Inc., Spartanburg, S.C., has announced that its DO 2000 command device is now
available for use with digital web-guiding systems. The new modular multi-use control station
combines advanced guidance technology with multi-language, user-oriented features, which are
designed to facilitate enhanced control, continual accuracy and ease of operation.With the command
device, users can operate up to eight control loops from a single command station. The device
features an integrated oscilloscope and voltmeter, and allows simple parameter setting.All input
and output elements on the panel are clearly displayed, and all function areas including
information, input control, operating mode and display are separated. All text on the DO 2000 is
presented in one of six available languages: English, French, German, Italian, Portuguese or
Spanish. In addition, the device is a diagnostic tool and can be used as maintenance aid to help
reduce downtime and eliminate waste.
April 2001
European Yarn Fair Expands
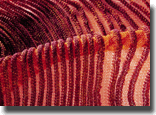
European Yarn Fair Expands
New quarters, acquisition strengthen Expofil Along with new fibers, colors and yarns
shown at the most recent Expofil in Paris, two major areas of expansion were announced by
management of this biannual yarn exposition. In June, the show will move to larger quarters at a
new location, where it will be able to accommodate international exhibitors. Yarn Fair
International, held in New York City every August, is being taken over by a consortium of French
trade organizations and will be run by Expofil management.In making these announcements, Didier
Tardy, Expofil president and recently retired head of the yarn firm Emile Tardy, said, For the
first time non-Europeans are exhibiting at Expofil. With the arrival of new countries, we will be
strengthening our profile and international viewpoint. By acquiring the show in New York, we now
have a foot on three continents. Expofil has a 50-percent interest in Filasia, a yarn fair which
takes place once a year in Hong Kong.Philippe Pasquet, secretary general of the Association franse
pour la promotion des fils textiles (AFPFT), the organization that runs Expofil, said that the move
from Quai Branly to Parc des Expositions, Paris Nord, will provide an additional 30,000 square feet
of exhibit space. This new space will be equally divided among exhibitors, fashion information and
visitor comfort facilities.About 7,000 weavers, knitters and manufacturers attended the December
Expofil, where close to 200 exhibitors gave a first look at fibers and yarns for the Spring/Summer
2002 season. Lenzing introduced Lyocell LF, a low-fibrillation fiber that has all of the properties
of lyocell and can be processed like conventional cellulosic fibers. Target end-uses are knitwear,
terry cloth, lace and garment dyes.Aquafil Textile Yarns, which is part of Gruppo Bonazzi, selected
Expofil as the venue to announce a new microfiber polypropylene to the market. Called Dryarn, it is
lightweight; resists abrasion, bacteria and moths; and offers UV protection. Like conventional
polypropylene, it is hydrophobic, so it expels perspiration and stains and transports
moisture.Dryarn is available in 12 colors. Research is underway to enable the fiber to be dyed. It
is expected to sell for sportswear, intimate apparel, hosiery, knitwear and medical
end-uses. Unifi Introduces New ProductsGreensboro, N.C.-based Unifi, the worlds leading
producer of texturized polyester and nylon, and a first-time exhibitor to Expofil, launched 10 new
products that, according to Jim James, European product development manager, have been in work for
three years. This is like our coming out party, he said.One new product, called Sorbtek, is a
moisture-management performance yarn that has been adapted by Nike for socks. Lee Gordon, Unifis
senior vice president, product development, said, The power behind Sorbtek is its advanced formula
that integrates itself into the molecular structure of the yarn. It outperforms all other yarns,
natural or synthetic, in the ability to catch, move and release moisture quickly and efficiently.
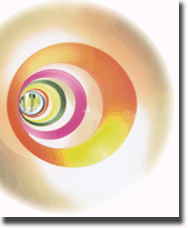
Sorbtek is available as continuous-filament polyester or nylon and in yarn counts ranging
from 70 to 150 denier. It can be used in the warp or filling in woven applications, and on
seamless, circular and warp knitting machines.Two new Unifi yarns that offer luster, brilliance and
shine are Sparkle and Novva. Sparkle is a false-twist yarn with a metallic look, and Novva is a
textured yarn with the brightness of a flat yarn.Myriad, another new yarn from Unifi, gives
striated or heather looks to fabrics. Eclypse is a thick-and-thin microfiber with the look of a
marled yarn. Donegal is a striated yarn with the touch of wool and the appearance of worsted.
Sultra is a splitable yarn that goes from 50 filaments to 450 after dyeing and imparts a peach-skin
touch. Augusta delivers the hand and drape of cotton. Sirrus is a false-twist yarn with inherent
stretch. It gives a crepe touch and thick-and-thin appearance to fabrics. Repreve is an
easy-to-process textured yarn made of post-industrial content.New at Nylstar are two nylon
variants, Meryl® Ecodye and Meryl® Skinlife. Meryl Ecodye is produced using a process that reduces
quantities of dyestuffs required and increases color saturation during the dyeing phase. The result
is less pollution, less clean-up and cost reduction ranging from 15 to 25 percent. Meryl Skinlife
is a bacteriostatic fiber that controls bacteria and keeps it at a natural level on the skin, even
during strenuous exercise. It lasts through repeated washings. New Technical Yarns From
FranceFrench spinner Paul Bonte, a division of Saint-Lieven and noted for technical yarns,
introduced new thermoplastic yarns containing Kevlar®. They can be laminated by applying heat and
pressure. Fabrics can be shaped and molded or spot-patterned. Other products of interest are
shrinkable yarns that can be used for seersuckers and plisses, semiconductive yarns,
electromagnetic yarns, antibacterial and antistatic yarns, and cut-and-slash protective yarns.With
the current trend to lightweight fabrics and open patternwork, Paul Bontes Chimere dissolvable yarn
is increasingly popular. Development fabrics shown are light, sheer, slubbed and nubbed.
Saint-Lievin also showed stretch yarns; plisses; light, ultra-sheer nylon crepe yarns; glittery
ribbon yarns; tie-dyes; raffia; and soft, dry-touch yarns.Crepe yarns are also popular at Emile
Tardy. One of the best sellers is a blend of viscose/nylon/elastane. Another is a twisted yarn of
acetate/textured Corterra. There are matte and shiny crepe yarns some with a dry touch, others with
a cold hand.Billion Mayor is selling new slubbed crepe yarns of 100-percent polyester and blends of
polyester/nylon. A twisted matte yarn of 44-decitex Corterra has a sensuous, silky touch. There are
trilobal polyesters, air-jet textured yarns, and dope-dyed, melange and pigtail yarns.At Chavanoz,
an increasing part of the line is selling to weavers of fabrics for the home. Fine polyester yarns
are going into organza for curtains; heavier, slubbed linen-type yarns are going into drapery and
upholstery fabrics. Wrinkle-Free LinenAnother French company, Safilin, has been spinning linen
since 1870. Today, it is producing 600 tons of yarn a month, of which 50 percent is exported.
High-twist yarns are selling to Northern Ireland. New are dry-spun yarns blended with Lycra® and
yarns that have been treated to be wrinkle-free.Italian spinner Linificio e Canapificio Nazionale
is noted for linen yarns. The company sells boiled natural yarns to apparel markets and bleached
yarns for bed, home and shirting fabrics. There are twisted yarns blending linen with nylon, iron
or copper; intimate blends of linen with silk or wool; covered yarns with top-dyed linen over
cotton; and dyed yarns to give a dvffect. A new high-twist crepe yarn is crease-resistant and is
selling to the shirting trade.Of the 68 Italian exhibitors at Expofil, Zegna Baruffa is one of the
most popular. Noted for stock color service, high performance and on-time deliveries, the company
sold 11.5 million kilograms of yarn to the United States last year, with a turnover of $200
million.
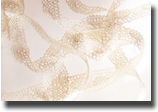
Among the top sellers at Zegna Baruffa are waterproof cotton yarns with a cashmere touch;
antibacterial yarns containing Amicor; UV-protective yarns; and yarns with fragrance, aloe and
seaweed for anti-stress. Dry-touch yarns include a twisted yarn of cotton/cupro; another is a
linen/cotton blend. There are chunky tweed yarns and lightweight dressy yarns. The B Exclusive line
at Zegna Baruffa is showing silk for spring in stretch, ultra-sheer, twisted and crepe yarns. There
is a new spinning technique that gives cotton an extra-fine, dry hand.At Marioboselli, the focus is
on lightweight yarns for casual- to formalwear. Dressy clothing is coming back, said Carlo Boselli.
We are selling new crepe yarns to the apparel trade for formal- and streetwear. One yarn he pointed
out is a blend of triacetate/polyester that is machine-washable and wrinkle-resistant.Marioboselli
is known as a spinner of fine silk yarns. With the fluctuating price and availability of silk, the
company has added synthetics and blends. With China becoming more industrialized, workers can make
more money in factories, so silk production is lower. Today we are getting some silk from Brazil.
It is top-quality, but more expensive, said Boselli.Viscose is another fiber Boselli cited as being
in fashion, but in short supply because of the closing of several major facilities. As a result,
Marioboselli has developed yarns of bright monofilaments and semi-dull trilobal polyester.At
Jaeggli, there are continuous-filament textured, twisted and stretch yarns spun in blends of
acetate, nylon, cupro, Bemberg, viscose, polyester, silk, microfibers, elastane and metallic
fibers. There are melange yarns, crepes and ultra-fine yarns of 50 to 160 denier. They sell to
weavers and knitters for a variety of apparel and home furnishings end-uses. A Return To
EleganceReiner Elend, sales export manager for German spinner Schoeller, agreed that there is a
return to dressing up. He showed a lot of dry, paper-touch fine yarns in blends of viscose/nylon
and acrylic/cotton. An eyelash yarn of cotton/nylon and a glitter yarn of acetate/nylon are some of
the novelties. Both have a dry hand. For casualwear, there is a new light, high-bulk yarn of
cotton/acrylic/copper.There were 31 exhibitors from Spain at Expofil. Josep Campanera of Consejo
Intertextile Espa#44; who coordinates textile promotion in Spain, said that exports are on the
upswing. He expects a large number of spinners to sign up for Yarn Fair International in New York
City.The yarns at Edgarfil fall into three groups: viscose, which is available as bright and matte;
linen; and fancy yarns. Most of the fancy yarns are blends. There are flammarns of cotton/nylon,
glitter of acrylic/nylon with a dry hand or of acrylic/polyester with a soft touch, and
fine-twisted yarns of acrylic/nylon.
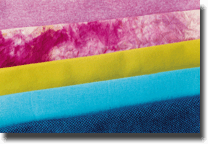
Himiesa showed yarns that are printed, covered, twisted, slubbed and flamm. There is a
polyester/nylon stretch yarn that has a paper touch and a shiny, two-tone chain yarn of
cotton/acrylic/nylon.Catfils line has a lot of stretch, linen and fancy yarns. There are new tape
yarns in linen/nylon. Some are natural, others space-dyed.The Portuguese firm TMG Yarns is part of
Textile Manuel Goncalves. They are equipped with spinning, twisting and dyeing facilities. The
product range includes cotton, linen, polyester, Tencel®, A-100 and specialty performance fibers.
Optic white Amicor/cotton blends are going into a variety of products including hospital sheets and
athletic socks. New this season are flame-retardant yarns spun with Kanecaron®, a fiber from
Kanebo. These yarns are selling to contract markets.At Somelos, there is a lot of long-staple
cotton from the United States. Some of it is blended with wool or modal. There are single and plied
yarns in medium to fine counts. Linen, silk and viscose are other fibers here. Somelos sells yarns
to circular and flat knitters for apparel and to weavers for apparel and home fashions.The next
Expofil will take place June 5-7 at Parc des Expositions, Paris Nord, with focus on the Fall/Winter
2002/03 season. Dates for Yarn Fair International in New York City are August 21-23.
April 2001