GR2 Opens Dominican FacilityGlen Raven Global Resources (GR2), Glen Raven, N.C., has formed a strategic partnership with Dominican Republic-based Phoenix Apparel Resources to open a 70,000-square-foot cut-and-sew facility in the Dominican Republic. The partnership enhances Glen Ravens ability to provide complete apparel packages to its customers.Our new plant allows us to offer customers competitive advantages over the Far East with cost-efficient production and rapid delivery, said Doug Wilson, vice president, GR2.The new facility offers Glen Ravens U.S. customers benefits of proximity, as well as favorable trade advantages created by the Caribbean Basin Initiative (CBI).October 2001
Solaractive Introduces Color 2 Color Threads
Tarzana, Calif.-based Solaractive International has added a new set of color-changing embroidery
and monogram threads to its product line. Under indoor light, Solaractive Color 2 Color threads
show themselves as yellow, soft pink, peach or turquoise. In sunlight, the threads change color,
respectively, to orange, hot pink, wine or blue purple.The new embroidery threads are available in
sampler packs containing four 250-yard spools.
October 2001
Picanol Says Sales Higher Recently
PICANOL SAYS SALES HIGHER RECENTLYBelgian loom-builder Picanol has reported better sales and profits for the first six months of 2001. The firm, based at Ypres, makes both air-jet and flexible rapier weaving equipment.Its sales for the January-June period this year totaled 7.3 billion Belgian Francs (U.S. $1 = 44.5 BEF), compared to 5.8 billion BEF in the corresponding months of 2000. Pre-tax profits rose from 194 to 268 million BEF over the same period.A spokesman said the better performance was linked with the successful launch last year of the new Omniplus air-jet weaving machine. The company had also fine-tuned its business activities, and was setting up a new structure called the “Global Textile Partner” (GTP) concept, aimed at offering total solutions in what it termed “a stagnating machine market.” This will include focus on new installations, upgrades and used machines, spares and accessories, consulting, raw materials, and asset management.Said the spokesman: “All these new activities should help flatten out the cyclical nature of the loom market. They mainly include the expansion of various innovative services situated closer to the client, and total solutions for the textile industry.”Order books were full for the rest of this year, providing the basis for long-term profitability, he added.October 2001
DuPont Announces Kevlar Expansion Plans
DuPont, Wilmington, Del., recently completed the first phase of expansion projects to increase
global production of Kevlar® by 15 percent. DuPont has announced plans for further investment and
will expand its Kevlar® para-aramid fiber-production facility in Richmond, Va. Total investment is
estimated to be approximately $50 million.A new production line based on proprietary DuPont fiber
technology will be built at the site, increasing production capacity for Kevlar by the end of
2002.The Kevlar high-performance fiber market is seeing incredible growth as demand from our core
customers continues to increase and new product applications are developed, said Diane Gulyas, vice
president and general manager, DuPont Advanced Fiber Systems.DuPont is committed to the Kevlar
business as a key contributor to our sustainable growth mission, so we are taking every action we
can to meet the evolving need of our customers, Gulyas added.
September 2001
Heal Receives UKAS Accreditation
United Kingdom Accreditation Service (UKAS) has awarded accreditation to United Kingdom-based
Healink, the service and calibration division of James H. HealandCo. Ltd., for its Titan Universal
Strength and Truburst Intelligent Bursting Strength testers.The British government appointed UKAS
to assess, accredit and audit companies such as Healink that carry out calibration services.
September 2001
Eastman Chemical Announces Name For PET-Acetate Company
Eastman Chemical Co., Kingsport, Tenn., announced that Voridian is the name for its PET plastics,
acetate fibers and polyethylene products company. Voridian will handle the manufacture and
marketing of the aforementioned product lines. The company will operate internationally with nine
manufacturing sites and two contract manufacturing facilities in seven countries.Earlier this year,
Eastman announced that by year-end, the company will be split into two independent public
companies. The second company, focusing on specialty chemicals and plastics, will be known as
Eastman Co.While our corporate brand is new, we will launch our new public company as an
established industry leader that has served customers for 82 years, Allan R. Rothwell,
CEO-designate, said in announcing the new name. Voridian is a great name for what will be a strong
and innovative company with world leadership positions in PET plastics and acetate fibers, he
added.
September 2001
Eyes On Asia
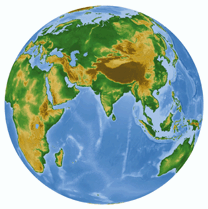
Eyes On Asia
Industrialized Asian countries face pitfalls, seek opportunities, while China anticipates
advantages of WTO membership. The production of commodity textile products, like
lightning, seems always to follow the path of least resistance. Since the dawn of the Industrial
Revolution, when English and American cotton mills began the mass production of fabric, textile
production has settled in what is, at best, a temporary home.From the American Northeast, the
industry migrated south, to take advantage of cheaper labor and proximity to raw materials. And
now, of course, the industry is moving again to Mexico, the Caribbean and other countries
throughout the world.Perhaps no area in the world has been such a hotbed of textile and apparel
production in recent years, though, as the Pacific Rim. As these nations developed their textile
industries much of it with U.S. assistance their products began eroding the market share for U.S.
companies. This erosion is due primarily to the combination of inexpensive labor, favorable trade
agreements and subsidies by many governments in the Pacific Rim that supported production
costs.Interestingly enough in economic circles as in life what goes around, comes around. And now,
industries in such countries as Taiwan, South Korea and Hong Kong are finding their own pitfalls to
remaining as competitive and profitable as in the past. A poor society might be content to remain
poor, as there is no higher standard to which one can aspire. But a taste of prosperity brings on a
craving for more, and companies in industrialized Asia are now finding they are following much the
same path as that traveled by the U.S. industry. Changing Fortunes In KoreaConsider for a
moment the situation in Korea. In the United States, the barometer for trade is the level of
imports. With each percentage point increase in imported textiles and apparel, U.S. jobs are lost
and American plants are forced to close. In Korea and the rest of Asia as might be expected success
is measured in exports. When exports decrease, jobs are lost and plants are closed. And Korean
textile exports have been plummeting.In May 2001, for example, part of peak-demand season, exports
declined 12.8 percent from the previous year to a total of $1.475 billion. By item, shipments of
textile raw materials showed a 10.1-percent decrease; yarn, a 12.3-percent drop; fabrics, a
7.9-percent slide; products, a 14-percent fall; and garments, a 17-percent plummet. For the first
five months of 2001, total Korean textile exports plunged 10 percent to $6.6 billion.The stagnancy
of textile exports, according to the Korean Federation of Textile Industries (KOFOTI), is primarily
due to the economic recession in the United States and Japan, as well as mounting pressure for unit
price reduction by buyers and increasing consumer tastes for low-priced goods.The industry in Korea
has been suffering, as well, from excessive supply and price increases in raw materials. Therefore,
the industry, mirroring the U.S. situation, has established the development of value-added products
as a major focus for the coming years.Not only are economic conditions creating difficulties, but
troubles with organized labor threaten the profitability of the synthetic-fibers industry in South
Korea. The industry is attempting to regain its competitive posture by replacing old equipment and
relocating its plants to foreign countries.The industry, however, is facing difficulty in carrying
out its restructuring plans due to strong opposition from the labor union and creditors. A Hyosung
spokesman was recently quoted as saying, [M]anagement recently tried to implement rearrangement of
workers because of the replacement of old facilities but its trial faced strong opposition from the
union and, eventually, bore no fruit. Under these circumstances, how can we improve our
competitiveness in the international market, where were losing share As well, he said, the union
objects to the building of a fibers factory in China.Hyosung is making a major push in the U.S.
market as well, having recently opened an office in Charlotte, N.C., to market its Creora® spandex
line.When U.S. companies build off-shore facilities, the most likely location is Mexico, Central
America or the Caribbean. For Korean companies, cheaper labor can be found in China and Vietnam,
although there has been investment in the United States and other developed nations as well.Korea,
behind China (including Hong Kong), Italy and Germany, is the worlds fourth-largest exporter of
textile products. Hong Kong Poised For OpportunitiesFurther south along the Pacific Rim, Hong
Kong has developed into the worlds ninth-largest trading entity. As a hub for fabric and garment
brokering, the Hong Kong industry is well-positioned geographically to meet a number of
international demands.Hong Kong, as well, stands to benefit significantly from Chinas impending
accession to the World Trade Organization (WTO), and will likely realize even more access to world
markets, particularly by those companies that have production facilities on the Chinese
mainland.Rising production costs, however, coupled with by Asian standards stringent environmental
regulations, have resulted in a number of Hong Kong companies shifting commodities production to
the Chinese mainland. Manufacturing operations in Hong Kong are more focused on value-added
productions, including both ring-spun and open-end yarn, fine-gauge knitted fabrics and complicated
dyed and printed fabrics.Of Hong Kongs exports, almost 70 percent go to the Peoples Republic of
China. Asia as a whole consumes about 85 percent of textile production from Hong Kong. The United
States, the second-largest customer of Hong Kong exports, accounts for about 4 percent of the
total.As in the United States and Korea, much low-end manufacturing is shifting away from Hong Kong
and onto the Chinese mainland and other countries in Southeast Asia. Some companies have even
established facilities in Mexico and Caribbean Basin countries in order to take advantage of
preferential U.S. trade agreements, such as the North American Free Trade Agreement (NAFTA) and the
Carribean Basin Initiative (CBI).As well, Chinas WTO membership will, ostensibly, require the
mainland to lower import tariffs on textile and apparel products, further opening opportunities for
Hong Kong textile producers. China Heads Toward WTO MembershipThe sleeping giant of the
Pacific, though, is China. And the major issue currently confronting that country is when the
much-anticipated election to the WTO will occur.Chinas quest to join the WTO is a 15-year-long
battle that is now all but over. Bilateral agreements reached in June with both the United States
and the European Union have removed almost all of the final obstacles to end the protracted
saga.Following six days of talks at WTO headquarters in Geneva in June, diplomats announced that
practically all of the membership issues had been settled, paving the way for China to join the
141-member organization by early next year at the latest.We hope that this advance will lead us to
be able to make the formal decision on Chinas membership in [November], top E.U. negotiator Karl
Falkenberg told the Reuters news service. The WTO trade ministers will meet in Qatar in November.
Falkenberg said he expects a couple of loose ends to be tied up at the next meeting, and then,
hopefully, we can gavel the whole thing through.The legislatures of WTO countries, as well as
Chinas parliament, must ratify the deal before it can be implemented. Chinas accession to the WTO
will occur exactly one month after the Chinese parliament notifies the WTO of ratification.The
impact that the countrys accession to the WTO will have on the rest of the world is both eagerly
anticipated and significantly feared, depending upon the point of view of the individual.Chinas
accession to the WTO is heralded as a boon for the economies of the worlds developed nations by
China/WTO supporters. With its huge population and heretofore-untapped market, there is opportunity
for considerable export and prosperity. Opponents argue that, while China does indeed represent
opportunity, reality is a different matter. China, they say, has not honored its trade agreements
in the past, refusing to remove barriers to exports while engaging in illegal product dumping to
its trading partners. Textile Leaders Voice ConcernWithin the U.S. textile/apparel complex,
there are several issues with which industry leaders take exception.In 1995, all WTO members had to
face a 10-year period during which the United States would phase out its quotas on textile and
apparel imports. China, on the other hand, should it gain WTO membership in 2002, would face only
three years before phase-out.As well, according to the American Textile Manufacturers Institute
(ATMI), the WTO has been ineffective in enforcing the bilateral and multilateral agreements under
which its members trade. The WTO, according to ATMI, has not provided market openings it promised,
and the U.S. government has not taken action to open those markets.Five years into the WTO, at
least 16 major exporting countries, including India, Pakistan, Egypt and Thailand, have failed to
meet their WTO obligations and open their markets to U.S. textile and apparel imports, an ATMI
report states. In fact, this report could not find a single country that is currently a major
exporter of textiles and apparel to the United States that has provided significant market access
because of the WTO.China was granted permanent Normal Trade Relations (Ntr) status by the U.S.
Congress last year. That status, however, only takes effect once China becomes a WTO member. Until
such time, Ntr status for China must be renewed annually. President George W. Bush cleared the way
for renewal this year by waiving the Jackson-Vanik Amendment, which specifies that Ntr may not be
granted to any non-market economy that restricts free emigration, unless the President of the
United States waives the restrictions for certain specified reasons.ATMI, in a hearing July 10
before the House Ways and Means Subcommittee on Trade, released a statement opposing renewal of Ntr
for China that read in part:With respect to textile-related issues specifically, China has signed
six bilateral textile trade agreements with the United States over the past two decades and has
subsequently broken every one of them. China illegally smuggles more than $4 billion worth of
textiles and apparel into the United States each year. It routinely violates U.S. design and
copyright laws in fact, China has signed four intellectual property rights agreements and
intellectual property theft in China remains rampant. In fact, a recent National Trade Estimates
report compiled by the U.S. Trade Representatives Office notes that U.S. industry estimates of
intellectual property losses in China due to counterfeiting, piracy and exports to third countries
have exceeded $2 billion.In addition, China is already exploiting a loophole which exists in
current U.S. trade regulations that allows it, as a non-market economy, to be inexplicably exempted
from U.S. countervailing duty law against export subsidies. Further, China maintains tariff and
non-tariff barriers that have restricted U.S. textile and apparel exports, despite repeated
promises to liberalize. This is yet another example of how China gets better treatment than our
other trading partners.Thus, there is nothing normal about the manner in which China conducts its
trade policy, and it is not deserving of Ntr status with the U.S.Also, make no mistake about it Ntr
status for China, and the terms under which it is preparing to enter the World Trade Organization,
will severely undermine the economic partnerships that have formed and continue to form between
U.S. yarn and fabric producers and apparel manufacturers in Mexico and the Caribbean. Once all
global textile and apparel quotas are removed, China is poised to essentially wipe out these
mutually beneficial trade arrangements we have made with our hemispheric neighbors.This concern is
borne out by a 1999 U.S. International Trade Commission (ITC) study on Chinas accession to the WTO,
which determined the Chinese share of apparel imports into the U.S. would more than triple as
quotas are phased out by the year 2005.Already the largest producer of textile products in the
world the country accounts for fully 25 percent of world production China stands poised to enter
the WTO with the capacity and governmental support to further erode market share of industries
throughout Asia, Europe and the Americas. Critical to the prosperity of the worlds industry is the
willingness of the Chinese to abide by their trade agreements with other nations. As well, both the
WTO and its individual members must pursue compliance by China with dogged tenacity.
September 2001
TeleFlash Non-Contact System Available From X-Rite
X-Rite Inc., Grandville, Mich., has introduced TeleFlash, a non-contact spectrophotometer. The unit
is manufactured by Germany-based Optronik, a subsidiary of X-Rite.TeleFlash can be used for
continuous, on-line color measurement. The unit is able to measure and evaluate color deviation in
all samples, including textured, finely patterned or glossy samples.Visual or acoustic warnings
alert the operator to out-of-tolerance color in tested samples. Color measurement data can be
stored and compiled into a printed report, or processed for automatic network transmission.X-Rite
also manufactures a compact version of the TeleFlash system. The smaller unit offers identical
features.
September 2001
Lasting Impressions
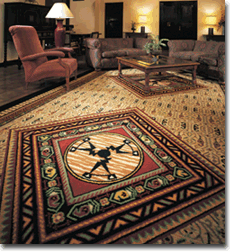
Lasting Impressions
Expectations and budget must be balanced in an industry in which public impression
matters. The ambiance created by the architecture and furnishings of a public space such
as a hotel or restaurant must meet the expectations of an ever-increasingly refined
public.Balancing expectations and budget, however, can be a difficult experience in an industry in
which many items are custom-designed. All products specified for a property must meet code and
maintenance requirements and wear well over time, in addition to meeting the image needs of the
site.In general, low-end properties demand lower cost, less maintenance and high-durability
furnishings, whereas high-end projects demand a distinctive appearance and have fewer constraints
on budget, according to Bettie Carey Bragg, principal, Niles Bolton Associates, Atlanta. The firm
was recently selected by Building Design and Construction magazine as one of the top 35
architectural firms in the United States.Most hoteliers expect softgoods to last four to six years;
for casegoods and base seating, the expectation is eight to 10 years. Resort properties, as a rule,
must replace softgoods more often because guests are in and out of the rooms all day, compared to
urban or airport hotel properties, where guests usually occupy the rooms only at night. A
restaurant that is open only in the evenings would have to replace softgoods less often than a
high-turnover restaurant. The more durable a manufacturer can make the fabrics and furnishings, the
less often they need to be replaced. Bragg mentioned durability as one of her biggest challenges
when working on a design project. The budget doesnt always allow for frequent changes, so the items
specified for a project must last as long as possible. Many hotels try to keep a stock of
replacement fabrics on hand for emergency repairs. Designing For Public Spaces
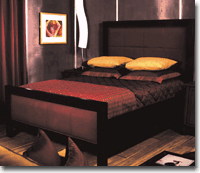
The design process for fabric and carpet is an integral part of the overall interior design
process market familiarization, concept development, client input, design development and interior
architecture, Bragg said. Design and selection of the accoutrements finishes, furnishings, carpet,
fabrics, art and accessories follows.The designer must maintain relationships with manufacturers of
fabrics and carpets in order to select the best manufacturer for the particular project. Designs
are communicated by sketch, photo or similar product. The manufacturer will then create samples,
which are sent to the designer for revision and/or approval. Custom fabric and carpet samples also
are often shown to the client for approval. Once the product is approved, the designer creates
detailed specifications for each and every item in the project. The specifications are then turned
over to a designated purchasing agent for tight budgeting and order processing.Final selections of
everything are based upon their physical attributes regarding appearance, durability, maintenance,
code compliance, availability and price, Bragg said.The type of project often dictates what kind of
fabrics and carpets are selected. Traditional projects include Axminster, patterned and cut-pile
carpets, and patterned and solid fabrics evocative of historical reference, Bragg stated.
Contemporary projects generally utilize new textures, geometric and solid fabrics, and off-beat
color directions.She said many contemporary and textural fabrics are sensuous to the touch; leather
and simulations are popular. Avora® and Crypton® fabrics are also increasing in popularity.Avora FR
is a flame-resistant polyester fiber available from KoSa, Charlotte, N.C. The flame-resistant
properties are inherent, not derived from a topical finish, and will never wash or wear off. Avora
FR fibers can be converted into a wide array of textile cloths from sheers to velvets for use in
hotels and restaurants. KoSa claims fabrics made with its Avora fiber in addition to being
flame-resistant have good ultraviolet stability, are dimensionally stable, and have high abrasion
resistance and outstanding wash characteristics.Hi-Tex Inc., Farmington Hills, Mich., engineers
Crypton Super Fabrics. Fibers are immersed in a patented formula (P385), which permanently encases
them and offers superior performance characteristics. Fabrics including prints, jacquards and
suedes repel liquid, moisture and bacteria; are breathable; and can be cleaned using plain water.
Hi-Tex claims that, because the treatment becomes an integral part of the fabric, the finish
properties will exist for the life of the fabric. Fabric is backed by a five-year warranty against
spills, pilling or abrasion damage. Special Warranty ProgramsBASF Corp., Mount Olive, N.J.,
offers a comprehensive, branded nylon fiber system catering to the hospitality industry. BASFs
Performance Certification program subjects all carpets made of Zeftron®, Zeftron 2000, Zeftron
2000® ZX and SAVANT to stringent performance testing and backs the carpet with the most
comprehensive warranties in the industry. BASF works with carpet manufacturers such as Templeton
Carpet Mills, Dalton, Ga., to ensure that carpet made with BASF fiber meets the highest quality
standards (see sidebar, page 28). Stain-removal guarantees, wear and colorfast warranties, and
anti-shock warranties are provided.
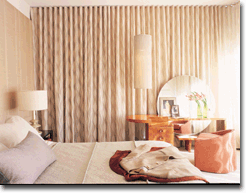
In 1994, BASF created the first nylon-recycling program in the industry. The 6ix Again
Program® is a closed-loop system for the recycling of Zeftron 2000 nylon. The fiber can be recycled
repeatedly, and old carpet no longer must go to a landfill or incinerator. Considering that hotel
carpet is replaced on average every four to six years, BASFs recycling program can eliminate
millions of pounds of waste nylon from landfills.For a recent renovation of the Ahwahnee Hotel in
Yosemite National Park, Calif., assisted by BASF Contract Nylon Fiber Systems, Ahwahnee property
management reclaimed the old carpet for recycling. Replacement carpet, manufactured by Templeton
Carpet Mills, contained BASFs nylon 6ix fibers, so it too, is recyclable. Templeton Carpet
Mills: Tufting One Unique Design At A TimeTempleton Carpet Mills, the hospitality division of
Mattel Carpets, is owned by Mike and Jerry Thomas. Templeton manufactures carpet primarily for
hotel guest rooms, corridors and public areas, but also for golf clubs, free-standing restaurants
and assisted-living facilities.Custom product is a big manufacturing challenge. Every order is
different and requires some kind of modification. Tufting machinery is becoming more complex, but
also more expensive. Templeton tries to find ways to take existing technology and make it fit with
its business. The key is modification, says Ann Brown, vice president, operations.David Dunn, vice
president, marketing, said Templetons business is almost totally customer-driven.At the size that
we are, and in making our own yarn with our own in-house extrusion, we are able to be responsive to
the customer, from the owner of the company down, Dunn stated.Equipment from Superba and ICBT, both
based in France, is used to heat-set and twist in-house extruded yarn. For tufting carpet,
Templeton uses Ringgold, Ga.-based Tapistrons hollow needle technology, as well as multi-level,
cut-and-loop (MLCL) machines made by Nakagawa, Japan.
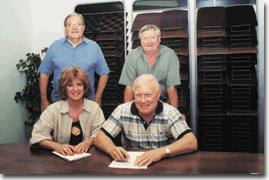
(left to right, front to back): Ann Brown, vice president, operations,Templeton; Jerry Thomas,
vice president, Mattel; James R. Carlisle,vice president, operations, Mattel; David Dunn, vice
president, marketing, Templeton.Templeton has moved away from yarn-dyed and piece-dyed carpets
and now sells almost exclusively solution-dyed product. The solution-dyed yarn is provided by
in-house extrusion or as branded fiber from BASF. Dunn said most customers require solution-dyed
product in guest rooms due to its performance and durability.Tufting machinery from Tapistron
allows Templeton to manufacture a style of solution-dyed carpet that evokes the look of a woven
Axminster carpet. People have enjoyed the performance of solution-dyed product for both public
areas and guest rooms, and Tapistron now lets them get that performance coupled with the look of a
woven or printed carpet, said Dunn.Recently, Templeton has seen an increase in sales of multi-level
cut-and-loop carpet. Dunn sees a trend away from 100-percent cut-pile carpet towards texture in
loop or cut-and-loop styles.Templeton offers a range of in-house designs to customers, but Dunn
said that almost every project involves some kind of custom work even if it requires only color
changes to an existing in-house design.The company manufactures in-house strike-off samples so the
designer can evaluate colors, design and texture. Five days is the typical turnaround time for
carpet strike-offs. However, for Tapistron product, using NedGraphics and Xerox technologies,
Templeton generates a color-calibrated CAD printout that is sent initially to the designer.If the
customer requests Tapistron, we will send a CAD drawing first. We can turn CAD drawings around
faster, said Dunn. Typically, three to four strike-offs are generated before the design meets the
designers satisfaction.In order to be in this custom business, said Jerry Thomas, vice president,
Mattel, you have to have samples woven that duplicate production. If you dont have good sample
equipment, including great design staff, it would be impossible to be in the hospitality
business.The typical turn-around time, from the moment the design is conceived to the time product
is shipped, is anywhere from eight weeks to eight months. Customers are given a delivery date based
on the availability of yarn and based on availability of machinery, said Thomas.Because the company
specializes in custom product, warehouse space is limited, and Templeton operates on a make and
ship basis. Product is often manufactured and shipped immediately to the customer. The sales team
coordinates delivery dates with the customer to coincide with construction and installation
dates.We became really serious about servicing the hospitality industry about 10 years ago, said
Mike Thomas, owner, Templeton. We were moving out of the commission tufting business and had
machinery that fit well with the hospitality business. Its a lot more competitive today than it was
10 years ago, but we are committed to working with our customers to create unique, custom product
for any hospitality application.
September 2001
Bianco Designs Six-Roller Weftstraightener
Bianco S.p.A., Italy, has introduced a six-roller weftstraightener with new software compatible
with all Bianco machines.The Digitex weftstraightener component features inverter drives, which
replace a DC system, as well as a new compensator that is lighter and more sensitive to run
delicate fibers such as cotton and Lycra®. The system reduces fabric path by 20 percent, providing
faster response and correction, according to Bianco.The machines VDTEX terminal includes a touch
screen and uses new software that can manage a maximum of 10 input/output devices.The machines DSP
10R reading system includes improved readability for thick fabrics with surface effects or
hairiness, and calculation power 16 times higher than previous models.
September 2001