Weaving TechnologyBy Eric Vonwiller, Senior Technical Editor Weaving Into The Future
Latest technology allows weavers flexibility, versatility in creating value-added
products. Generally speaking, textile machinery suppliers in the United States have
suffered significantly reduced equipment sales of late, especially in the past year. Weaving
machinery sales for 2001, for example, plummeted to a total of approximately 260 machines, a figure
machinery executives say is only about five to 10 percent of the volume normally experienced in a
medium to good year.A salient question to ask is: Can weaving machinery manufacturers survive this
The answer is, of course, an unqualified yes. While the American market remains flat, sales in
other parts of the world have been brisk at times. Even some of the high-labor-cost European
countries, such as Germany and Italy, have experienced significant growth in machinery sales. Some
of the machinery manufacturers even claim the best year ever for their sales in specific European
countries. A significant part of the difference in sales can be attributed, machinery manufacturers
say, to the basic reorganization underway within a significant portion of the U.S. textile
industry. Much as European producers had to do a decade or so ago, many of the large commodity
fabrics weavers in the United States are beginning to position themselves to meet the demands of a
dynamic global market. This requires faster production of smaller lots. For an industry already
running well short of manufacturing capacity, adding new equipment is not always the highest
priority unless it is necessary to remain competitive from a cost, delivery and quality
standpoint. Tuning For ProfitThis reorganization of basic industry structure was one
undertaken out of necessity by a large number of mills in Europe during the latter part of the 20th
century. In order to compete with low-cost products from the Far East, Asia Minor and other
regions, plants in Europe had to learn that volume production does not provide the profits for them
to survive in the long run. Volume may still be required in some weaving applications, but this
type of volume includes the value-added aspects that are difficult to copy, or require extremely
high quality standards. Some weaving end-uses that have become common in Europe and are beginning
to be widely manufactured in the United States include technical/industrial/medical textiles such
as seat belts, airbag fabrics, protective clothing, blood filters, and many other life-saving
applications.Another form of added value is fabric design that integrates new fiber materials (for
example, microfibers, metallic threads, aramid and carbon fibers), having various yarn counts and
compositions in a single fabric. Added value also comes from using varying fabric weights within
one piece of fabric, varying densities (often in extreme setups from very light to very heavy), and
difficult weaves often found in technical applications.So, what did weavers do in Germany, Italy,
France and other highly developed nations They had to find their specific niches and learn that
survival in todays market means getting top-quality product to customers faster than ever before
and, importantly, faster than cheaper imported fabric can be delivered. This, say the makers of the
worlds textile equipment, is the key to the revitalization of weaving in the United States.
DornierGermany-based Lindauer Dornier GmbH promotes strongly the concept of its weaving
machine system family. The company states that flexibility and versatility are the key components
of future investments, especially in high-labor-cost countries. The Dornier system family of rapier
and air-jet machines is designed around a modular concept. Lately, special attention has been paid
to details such as reduced machine downtime and improved handling of mechanical functions,
electronics and on-line communication. Dorniers rapier weaving machines are capable of an extensive
range of applications with cam or dobby shedding, or with an electronic jacquard machine. Article
changes on the fly with different filling yarns recently were demonstrated at ITMA Asia 2001.The
versatility of the Dornier air-jet weaving machine has been extended by integrating the patented
Fast Dobby Change (FDC). A positive cam motion can be replaced by a dobby in a short time and as
the market situation requires. Dornier claims this conversion can take place within the time frame
of a style change.Recently, Dornier introduced its new terry weaving machine, EasyTerry. This
air-jet machine optimizes performance, drastically reduces the number of mechanical components,
decreases wear and achieves a higher weaving efficiency than similar
machines. PicanolBelgium-based Picanols OMNIplus air-jet has been presented to clients with
newly developed air tuckers. The OMNIplus also features the new cyber-display, which gives the
individual weaving machine a Web-enabled man/machine interface.The new TERRYplus is the air-jet for
terry towel fabrics. This Picanol-Gunne machine is based on the OMNIplus technology and, according
to the company, offers extremely high terry quality because of its swinging reed pile formation.
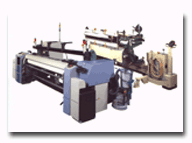
The ability to swap the back part of the split frame on Picanols rapier and air-jet weaving
machines allows style changes in 30 minutes.The Gamma rapier machine offers a wide field of
applications even up to heavy canvas. The ETM on-screen tension control of the filling yarn, and
special waste-reduction scissors on the left-hand side are some of the latest features added.The
Cyclops system for automatic on-loom inspection uses a traveling camera system mounted in the loom
in order to inspect the fabric. In case of a running defect, the system stops the loom. The SUMO
switched-reluctance motor that is available for Picanol machines has been a huge success, as it
drives the weaving machine directly without belt transmission or clutch and brake. The motor speed
can be varied almost instantly from extremely slow motion to top speed by simple electronic
control.By entering the accessories business for textile machines (with the acquisition of Steel
Heddle and Verbrugge NV), Picanol will also play a role as a supplier of consumable goods
(See Supplier Notes, TW, January 2002).PromatechItaly-based Promatech, the recently formed
manufacturing group that includes Somet and Vamatex weaving machines, provides rapier and air-jet
weaving machinery technology to satisfy practically all weaving needs.The newest offering, the
Somet Alpha series, is designed to combine technology, ergonomics, versatility, reliability and low
running costs. The Alpha is available in single-beam and twin-beam models, with upper-beam and
double-beam models under development. The machine is available in dobby version featuring either
the Fimtextile 3080 or Stli 2670 or in electronic jacquard version. Fifteen different widths are
available. Somet also generated success recently with its much-reviewed Super Excel rapier weaving
machine and Mythos air-jet machine.The Vamatex Leonardo is a negative rapier weaving machine that
targets the highest performance levels in the rapier weaving sector. Vamatex says the Leonardos
machine concept is geared towards the production of quantity and quality, offering quick response
to the variability of orders and output requirements of todays global textile industry. Other
weaving machines from Vamatex are the P 1001 SuperEK, which is a highly competitive loom in terms
of initial investment offering high productivity with lightweight rapiers, and the Vamatex 9000
Plus ES, which features positive rapiers mounted on flexible ribbons for maximum versatility. The
Leonardo DynaTerry is a terry weaving machine that offers a combination of performance, versatility
and efficiency. Sulzer TextilThe Itema Group of Italy, the parent of Promatech, acquired
Switzerland-based Sulzer Textil in 2001. Sulzer Textil will remain a separate business, but it can
be expected there will be significant exchange, integration and standardization of equipment
technology within the Itema Group. Sulzer says its projectile weaving machine with sales of more
than 150,000 machines worldwide is the most successful weaving machine in history relative to a
specific weft-insertion system. Its low energy consumption, wide variety of applications, and
suitability for technical and industrial applications allow the projectile weaving machine a strong
position in textile manufacturing. Sulzer Textils Customized Weaving Technology is the specialty
fabrics division where tailor-made weaving machines are designed and produced. For example,
machines can be designed to produce agrotextiles and geotextiles, conveyor belts, sailcloth, tire
cord, cinema and theatre screens, filtering fabrics, tarpaulins, wire fabrics and many other
industrial products.
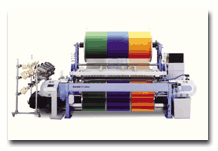
The G6200 rapier weaving machine has proved itself by being a strong competitor, with more
than 5,000 units sold since its introduction in 1999. The new G6300 offers higher insertion rates
and an even better price-to-performance ratio, the company says. The Sulzer G-series rapier
machines have successfully entered many diversified fields of weaving and, for example, can show an
impressive success in airbag fabric weaving. Sulzer Textil also offers a terry version of the
G6300.The L5200 air-jet weaving machine is especially suitable for the economical production of
standard fabrics such as bed linens and linings. It is successful as well in the field of glass
fiber fabrics, in which Sulzer claims it is the market leader. The M8300 multi-phase weaving
machine produces simple, standard fabrics with an extremely high weft-insertion rate.
ToyotaJapan-based Toyota Industries Corp. (formerly Toyoda Automatic Loom Works Ltd.)
concentrates in the United States on the sale of its LW600 water-jet weaving machines. The LW600s
electronic let-off, in conjunction with a newly developed automatic pick-finding system, achieves
the optimum in warp yarn control, sharply reducing start marks and ensuring fabric quality,
according to Toyota. As well, the company offers the JAT610 air-jet, which is designed for
efficiency and high-speed operation for fabrics ranging from cotton and wool, to spun fabrics such
as denim, filament and fiberglass. The JAT610s all-in-one frame is manufactured by a high-tech
production system based on Toyotas advanced automotive production process.
TsudakomaTsudakoma, Japan, emphasizes that its air-jet and water-jet weaving machines are
backed by a robust frame structure and strong beat-up systems that allow ultra-high-speed operation
and heavy-duty fabric weaving. The ZAX-e, Tsudakomas brand-new model air-jet weaving machine, is
equipped with the iT board, which features a touch-type operation with color graphical interface.
The ZW408 is Tsudakomas new model water-jet weaving machine that has improved basic functions for
higher productivity, higher operation efficiency and highest standard of fabric quality. Van
de Wiele Carpet And Velvet WeavingBelgium-based NV Michel Van de Wiele is one weaving machinery
manufacturer that seems to have had good to very good sales years over the past decade. Not long
ago, the company acquired Germany-based Memminger-IRO GmbH, manufacturer of feeders for knitting
machines, and Bonas Machine Company Ltd., United Kingdom, a manufacturer of electronic jacquard
machines. Even though velvet weaving machinery sales seem to be down presently, the carpet sector
holds steady, with an upward sales trend. The consumer preference is towards more expensive rugs
with a wider variety of fiber and yarn materials because the latest machine-woven rugs look and
feel very similar to handmade rugs.
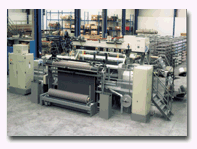
Van de Wiele recently introduced a new carpet weaving machine, the CLP81
(See CarpetandRug News, TW, this issue). The new machine is a modified version of the
CarpetandRug Tronic CRT82, capable of weaving loop-pile carpets. Dorniers Legend Says Auf
WiedersehenBefore the end of the past year, Hans Geiger, long-time president of American Dornier
Machinery Corporation, Charlotte, N.C., said goodbye or in German, Auf Wiedersehen to many personal
and business friends in the United States.At the facilities of American Dornier, Geiger received a
surprise retirement reception, which included more than 150 customers, colleagues and friends. Even
his wife, Ingrid, flew in from Europe and surprised him with her presence. Geiger quipped that this
was one of the very rare occasions that made him speechless at least for a short moment.
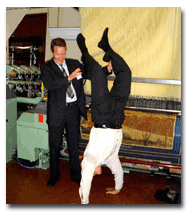
During the goodbye celebration, Geiger said, Ill show you that Im not an old man!, and swung
himself into a handstand.Geigers official retirement date was January 1. He handed over the reigns
of the company to Peter A. Brust, 41, who brings with him a solid business and textile education,
as well as machinery sales experience. Brust was for 10 years plant manager with Rohleder HITEX,
one of the leaders in upholstery, jacquard and woven velvet fabrics in Germany. At the reception,
Geiger issued a strong vote of confidence in Brust and assurance of the continuity of a high level
of service.The retiring Dornier executive started his career with the company in 1956 as an
assistant weaver in the demonstration room in Lindau, Germany. A little over a year later, he was
sent out as a technician to Central America to install 24 shuttle weaving machines. Realizing that
he wanted more of a foundation, he went to study at the Textile Technology Institute in Reutlingen.
After his studies, he returned to Dornier. Geiger drew colorful pictures of the nightmares he had
with the first shuttleless Dornier machines, which worked on a much different principle than todays
machines. He said he had his sincere doubts about that technology, but he wanted to go only one
time to America. His wish was granted in the late 1960s, when he traveled to introduce Dorniers
rapier machines to U.S. weavers. But he saw very quickly that the first technology had too many
flaws. For certain applications, the U.S. market would not accept the selvage the machine produced.
However, CollinsandAikman, Siler City, N.C., was the first mill to install 24 rapier machines the
fathers of todays positive filling transfer technology and used them for the production of
automotive fabrics. This was a significant success for Dornier (and also for Geiger). From then on,
the industry started to accept Dorniers technology, and many other mills followed with orders.
Geiger started to travel 50/50 back and forth between Lindau and Charlotte, and there was no way to
stop him.At a point in the early 1970s, Geiger started to look for property to establish a service
center in the United States. He asked Peter Dornier Sr. for a very humble amount to purchase land
and to build the first physical building for Dornier in the States. In 1978, American Dornier was
established. By the end of 2001, approximately 9,000 Dornier rapier and air-jet weaving machines
had been sold in the United States and Canada, and certainly the majority can be in one way or the
other directly linked to Geigers personal efforts and diligence. The sales numbers and the image of
Dornier in the United States are indicative of his efforts.As he was preparing to depart, Geiger
said he plans to be back in the States soon. But this time, it will be for vacation.
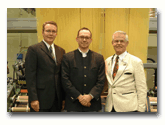
Left to right: Peter Brust, American Dorniers incoming president; Peter D. Dornier, chairman
of the Board; and outgoing president Hans Geiger. Quaker Fabric Weaving Profits
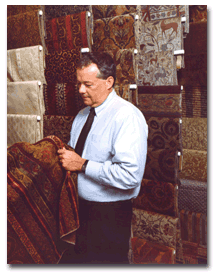
The willingness of the U.S. textile industry to develop value-added products and service
niche markets is a key ingredient to the overall success of the industry.Quaker Fabric Corp., Fall
River, Mass., is one of the weaving enterprises in the United States that combine these elements to
profitably weave fabric.Quaker began operations in 1945 as a small family-owned fabric mill. Today,
Quaker is one of the largest producers worldwide of jacquard upholstery fabric and one of the
leaders in the $2-billion-plus U.S. upholstery fabric industry. The company also produces specialty
yarns, which it uses in its fabrics and sells to other fabric manufacturers.Quaker Fabric has not
only been doing well over the past years, but also it is expanding its manufacturing facilities
with two additional pieces of real estate to be converted into manufacturing plants, according to
Jim Dulude, vice president, manufacturing. One is an 86,000-square-foot building in Fall River that
is to be a chenille yarn plant; the other is a 180,000-square-foot facility that will be the
prototype manufacturing complex where beaming, weaving, finishing and post-finishing will be
performed. The company is installing 36 new dobby-equipped Dornier weaving machines to produce
plain or simple weaves.Dulude mentioned that Quaker produces a significant portion of fabrics that
do not require the investment of much more expensive jacquard machines; therefore, the decision was
made to equip a safe portion of the production capacity with dobbies. Quaker has a large number of
existing Dornier rapier machines with jacquard set-up, and about 50 older looms, also with
jacquards. It really took a lot of soul-searching to get us to the dobbies, said Dulude. But Quaker
is sure this was a proper and cost-effective decision. The company plans to install about 90 dobby
machines in total. Rapier machines due to the nature of the business and fast-changing trends in
upholstery fabric design are the only sensible choice for Quaker Fabric, Dulude explained. We
design products for customers, and air-jet weaving machines and heavy chenille yarns just dont mix
well, he said.Quaker Fabric sees export sales as a necessity for survival. Larry Liebenow,
president and CEO, is aggressively pushing the company toward even greater participation in global
trade. Dulude said trading with foreign markets creates challenges for the manufacturer. Also,
preferred colors are different in foreign countries, often reflecting culture and environment. Part
of this export influence has led the company to offer a huge variety of styles. He said the days of
running all machines on the same style are gone. We have a wide variety of styles. In a typical
week, we will make more than 3,000 different SKUs [individual style pieces] in our mill. While
complex, this versatility enables Quaker to compete in the realm of specialties instead of in
commodities. Also, individual fabric piece lengths have been dropping more and more over the years.
This development challenges the abilities of the mill, and Dulude is convinced the companies that
can handle it are the ones that will succeed. It also requires a modern infrastructure to support
production planning and scheduling systems, as well as support and control systems for labor and
machinery. Quakers management believes U.S. mills can learn from their European counterparts. U.S.
companies can do well when they make their products more upscale. This model works in Europe but
can be internationally applied.Training and retraining of the labor force is very important for the
company, and Quaker does not believe in quick on-the-job training. Quality, commitment and
leadership are major ingredients Quaker expects from its labor-force. The company, though, supports
its employees with labor-friendly and structured action plans. It currently employs approximately
2,600 people.Quaker strives to be a world-class leader in the upholstery fabric industry and in
manufacturing of specialty textile yarns. This is achieved through exceeding customer expectations
and Quakers associates continually improving the value of the products, processes and services.
February 2002