ProcterandGamble DonatesPatents To Clemson UniversityProcterandGamble (P and G), Cincinnati, has donated its proprietary Capillary Channel Film and Fiber (CCF) technology to Clemson University, Clemson, S.C. By creating grooves in fibers and films, the new micro-capillary technology could make materials feel drier next to the body. The technology may also add benefits to feminine hygiene products, baby diapers, acoustical insulation, air-filtration systems and wound-care dressings.The technology donation includes rights to 10 U.S. patents and 84 foreign and pending patents, as well as all intellectual property from CCF development.According to Clemson, the pairing of the P and G patents with existing Clemson patents to successfully commercialize CCF technology could result in annual sales of fibers and films in excess of half a billion dollars. The university would benefit from royalties on product sales. We are thrilled that Clemson will be able to continue the development of this significant technology, said Al Dierckes, director, Baby Care Technology Division, P and G. It presents a real-life laboratory for Clemson students to further develop and commercialize a promising technology that can lead to a new source of funding for the university.Dierckes said P and G chose Clemson because of its research strength in the field of films and fibers, as well as its excellent track record in taking a technology from the workbench to the workplace.February 2002
U S Cotton Exports Exceed Domestic Consumption
U.S. Cotton ExportsExceed Domestic ConsumptionAt the National Cotton Councils 02 Beltwide Cotton
Production Conference held in Atlanta, William B. Dunavant Jr., chairman and CEO, Dunavant
Enterprises, Memphis, Tenn., had good news to report regarding consumption of U.S. cotton.Dunavant
said that of an estimated 20.05 million bales produced in 2001, 9.8 million were exported, compared
with U.S. consumption of 7.6 million bales. Dunavant projected 2002-03 crop-year production at 18
million bales, including 7.8 million for U.S. consumption and 10 million for export. Anderson D.
Warlick, CEO, Parkdale Mills, Gastonia, N.C., citing the U.S. textile industrys severe decline and
its loss of more than 60,000 workers, as well as the 26- to 30-percent drop in average prices of
Asian yarn and fabric imported into the United States, called on the industry to demand enforcement
of U.S. trade laws. He noted that enforcement of rules governing trans shipments would enable U.S.
mills to consume an additional 1 million bales of cotton.J. Berrye Worsham III, president and CEO,
Cotton Incorporated, Cary, N.C., said the U.S. cotton sector must become more export-oriented due
to the changing distribution of its customer base. His organizations objectives for improving
demand for and profitability of cotton include improving the yield, value and quality of U.S.
cotton production and development of stronger foreign markets for cotton exports, among other
goals.
February 2002
Clariant Launches E-Business Center
Clariant Launches e-Business CenterSwitzerland-based Clariant International Ltd. now offers customers in Europe access to its new on-line business center. Currently available in English and German, the center will be available to clients in North and South America by no later than mid-2002, Clariant hopes.Using the business center, customers can complete on-line transactions, access technical information and use various Web-based project management tools. In addition, Clariants enterprise management system (ERP), SAP, and numerous business-related databases are available. The center is divided into Shop, Products and Service sections. Each section has been designed for simple and intuitive use.February 2002
Acsis Offers Console Pocket PC 2002 For SAP Console
Acsis Offers Console Pocket PC 2002 For SAP ConsoleAcsis Inc., Marlton, N.J., has launched the Console Pocket PC 2002 for SAP R/3 data collection. The new Pocket PC provides an easily navigated graphical user interface (GUI) for SAP Console transactions that are run on Pocket PC-based mobile data collection computers, according to the company. The program includes Windows-familiar navigation buttons, touch screens, menus and more. Users can use the Pocket PC browser to obtain information from their ERP systems via SAP Consoles direct radio frequency (RF) connection or via the Internet.February 2002
Glenro Offers New Catalytic Oxidizer
Glenro Offers New Catalytic OxidizerPaterson, N.J.-based Glenro Inc. now offers a new catalytic oxidation system that removes multiple solvents including aldehydes, ketones, alcohols, esters and non-volatile vegetable oil and odors from a process exhaust stream at a rate of 13.3 pounds per hour. The system reduces fuel consumption by running at a lower temperature than a direct-fired oxidation process, and by using an air-to-air exhaust preheat exchanger subsystem, according to Glenro. The system is designed to maintain catalyst temperature at 750°F to 800°F, ensuring complete destruction of solvents, oils and odors, thereby meeting air quality regulations.February 2002
INDA Announces Winner Of 2002 Visionary Award
INDA AnnouncesWinner Of 2002 Visionary AwardThe Association of the Nonwoven Fabrics Industry (INDA), Cary, N.C., announced that ProcterandGamble has won the inaugural INDA Visionary Award for its Swiffer Wet Jet product. The award recognizes new products utilizing nonwoven fabrics and technologies. Finalists made formal presentations at INDAs Vision 2002 Consumer Products Conference in New Orleans in January. Conference attendees voted to determine the recipient of the 2002 Visionary award.The other finalists were: Abeil-Destex Nomex fire blanket, Destex SA, Switzerland; ComforTemp, Frisby Technologies, Long Island, N.Y.; Cottonelle Rollwipes, Kimberly-Clark, Dallas; and CIF Double Action Wet Wipes, Unilever, The Netherlands.February 2002
Model Mill Italy39 S Torcitura B And B
Italian Textile IndustryBy Piergiuseppe Bullio, European Correspondent Model Mill: Italy’s
Torcitura B and B
Italian yarn producer combines years of art and tradition with modern technologies to stay
competitive.
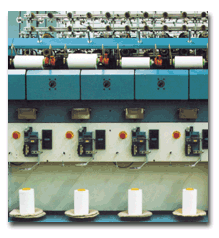
Torcitura B and B, a silk manufacturer in Italys Crema province, has demonstrated its lively
legacy of experience, knowledge and business skills for more than 25 years, blending innovation and
tradition in typically Italian style.For years, by scrupulously pursuing production quality in raw
silk and man-made yarn processing, as well as continuously updating technologies, B and B has
asserted its competitive presence on the market in Italy and the world.B and B traces its origins
to SATEX, a raw silk thrower founded in the late 19th century. At that time, the cultivation of
silkworms in Italy, which had flourished from the turn of the century until after World War II, was
in decline because of insufficient production to meet market demand. Raw material was imported from
China because of its high quality and later from Brazil. B and B was established in 1976 and, in
the 1990s, added to its silk-throwing activities by throwing yarns such as acetate, viscose, nylon
and polyester. Today, the B and B plant covers 10,500 square meters. Production of yarn totals
300,000 kilos per year, of which 70 percent is silk and 30 percent is man-made.Originally from
China, silk culture was introduced to Mediterranean countries around 500 A.D. In the centuries to
follow, silkworm culture spread throughout Europe. Italy, the worlds top producer of yarn and
fabrics until the 18th century, is still famous for the high quality of its silk products.Imported
raw silk, especially from China, comes for processing in the form of a hank. Through the various
treatment processes, different types of yarns are produced that can be used for anything from
scarves to shirts, and from ties to bridal gowns. The first treatment phase consists of a bath in
natural substances part of each companys secret recipe which makes the yarn softer and more
pliable. Then, the hank goes to the winder, where the yarn is wound on a spool and then loaded into
the uptwisting machine. This is followed by steaming, doubling and, finally, spooling, where the
yarn goes from the twisted bicone to the final package.A 1-kilogram bobbin raw yarn of 20 to 22
deniers produces a yarn approximately 428 kilometers long, the distance from Turin to Venice. At
this point, using new-technology machines, any imperfections in the yarn are removed through
slub-catching, measuring, antistatic oiling and precision traversing, which facilitate and prepare
the yarn for dyeing or weaving processes.After this meticulous crafting with an entire production
process lasting from one to two months the scientifically processed yarn is entrusted to human
skill and experience for quality control. Under expert eyes, even the tiniest defect can be
spotted. Of course, man-made fibers undergo the same production treatment before being presented
for dyeing and weaving. These fibers can be mixed with each other or with silk, depending upon
market demand and fashion, which uses the yarn for knitwear and apparel fabrics. Today, the trend
is to use silk crepe combined with viscose or cotton mixed with polyester in various combinations
obtained by high-technology machines.Traditional craftsmanship is still a part of the initial
phase, production control and final inspection. The 1980s were an important turning point for
Torcitura B and Bs productive innovation and the potential created by the introduction of new
technologies. As the textile sector adopted new high-speed looms and new coloring techniques,
production parameters for winding also needed to be changed, making yarn processing overall more
modern, efficient and rapid. Throughout the companys existence, there has always been constant
cutting-edge attention to updating machinery, which needs to follow the rhythms of the textile
sectors entire cycle. The process is accompanied by the increasingly attentive pursuit of quality
in the workplace and the environment in general. Wastewater from the yarn-bathing process has been
eliminated to avoid pollution. Clean technologies have been adopted for purification, and natural
substances are now used to better protect the environment and its natural equilibrium.By using the
most advanced technologies in processing silk and man-made yarns, Torcitura B and B has become one
of the leading textile mills in Italy, with a reputation for high quality and a large array of
products released on the market every year. In Italy, this market, handled by a network of sales
agents, consists of large fabric weavers and converters around Como, Biella, Prato and Carpi areas
known worldwide for their ancient textile history. Outside of Italy, B and B sells its yarns
primarily in Switzerland and Germany, which, in turn, supply the U.S. market. Of course, fashion
trends influence production decisions, which today are experiencing an increase in demand for pure
silk as well as fibers combined with silk; such as silk and viscose, silk and wool, silk and nylon,
and silk and acetate.The company is now committed to more strongly asserting its presence within
Italy and Europe by strengthening a more widespread network of sales agents. In addition, the
company maintains a strategy that constantly pursues product quality, environmental quality and
increasingly advanced technological updating. It believes this is the only way to meet the
competition from other countries. By implementing strategies designed for the immediate future, B
and B counts on increased sales of its textile products and higher revenues.In order to stem the
flow of imitation Made in Italy products that have appeared in recent years, B and B, in
collaboration with the Associazione torcitori italiani della seta, has established a quality mark
for Italian twisted silk. The various products from the entire silk-processing cycle, from
spinneret to finished fabric, may be released on the market with the associations certification and
mark. This mark will also indicate the social commitment of the producers, which operate in full
compliance with silk production processes, from working conditions to environmental protection.
February 2002
Quality Fabric Of The Month: Strong & Silent
Q uietness, durability and resistance to extreme cold are much desired qualities in fabrics used in hunting apparel. With these requirements in mind, Glen Raven Knit Fabrics, Glen Raven,
N.C., introduced its Microsuede® with DuPont’s abrasion-resistant Cordura® to the hunting and outdoor apparel market in early 2001.The fabric represents a new generation of the company’s original warp-knit Microsuede hunting fabric, which was introduced about five years ago as an alternative to traditional woven fabrics and the newer fleece fabrics being used for hunting and outdoor apparel. According to Hal
Bates, marketing manager, Microsuede offers advantages of quietness and softness over louder, stiffer woven fabrics and of burr-resistance over wooly fleece, as well as being more wind-resistant than most fleeces. In addition, he said, the brushed surface of polyester Microsuede shows a more photo-realistic, non-fading printed camouflage pattern than cotton. The fabric also is treated with Glen Raven’s Repelzz® water management system for long-lasting water repellency.
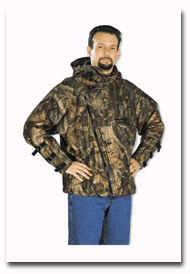
Sportchief uses Glen Raven’s Microsuede with Cordura in a range of outerwear products
including the archery jacket, shown above.
Collaborative Efforts
With all these advantages, the fabric’s quietness has remained its primary advantage for hunters. However, Glen Raven sought to improve the fabric further by adding abrasion resistance. The company has had a strong association with DuPont for a number of years and worked with the fiber company to develop a warp-knit version of Cordura nylon, which is normally used in woven applications, Bates said.
In Microsuede with Cordura, the two yarns are knitted together in two layers, with Microsuede presenting a brushed face to be printed and a lightweight, 160-denier Cordura in the back layer to provide the abrasion resistance.Initially, Glen Raven granted an exclusive license to
Canada-based Sportchief, an outdoor hunting apparel manufacturer, which introduced the fabric as Durasupple® in a range of outerwear products. Sportchief sells its products in the northern United States, Canada and Europe, and its customers require heavy, durable apparel to wear in extremely cold climates.
Glen Raven is now licensing other companies as well to use Microsuede with Cordura in products for activities such as hiking, backpacking and snowboarding, in addition to hunting.
For more information about Microsuede with Cordura, contact Hal Bates (336) 586-1325.
February 2002
Weaving Into The Future
Weaving TechnologyBy Eric Vonwiller, Senior Technical Editor Weaving Into The Future
Latest technology allows weavers flexibility, versatility in creating value-added
products. Generally speaking, textile machinery suppliers in the United States have
suffered significantly reduced equipment sales of late, especially in the past year. Weaving
machinery sales for 2001, for example, plummeted to a total of approximately 260 machines, a figure
machinery executives say is only about five to 10 percent of the volume normally experienced in a
medium to good year.A salient question to ask is: Can weaving machinery manufacturers survive this
The answer is, of course, an unqualified yes. While the American market remains flat, sales in
other parts of the world have been brisk at times. Even some of the high-labor-cost European
countries, such as Germany and Italy, have experienced significant growth in machinery sales. Some
of the machinery manufacturers even claim the best year ever for their sales in specific European
countries. A significant part of the difference in sales can be attributed, machinery manufacturers
say, to the basic reorganization underway within a significant portion of the U.S. textile
industry. Much as European producers had to do a decade or so ago, many of the large commodity
fabrics weavers in the United States are beginning to position themselves to meet the demands of a
dynamic global market. This requires faster production of smaller lots. For an industry already
running well short of manufacturing capacity, adding new equipment is not always the highest
priority unless it is necessary to remain competitive from a cost, delivery and quality
standpoint. Tuning For ProfitThis reorganization of basic industry structure was one
undertaken out of necessity by a large number of mills in Europe during the latter part of the 20th
century. In order to compete with low-cost products from the Far East, Asia Minor and other
regions, plants in Europe had to learn that volume production does not provide the profits for them
to survive in the long run. Volume may still be required in some weaving applications, but this
type of volume includes the value-added aspects that are difficult to copy, or require extremely
high quality standards. Some weaving end-uses that have become common in Europe and are beginning
to be widely manufactured in the United States include technical/industrial/medical textiles such
as seat belts, airbag fabrics, protective clothing, blood filters, and many other life-saving
applications.Another form of added value is fabric design that integrates new fiber materials (for
example, microfibers, metallic threads, aramid and carbon fibers), having various yarn counts and
compositions in a single fabric. Added value also comes from using varying fabric weights within
one piece of fabric, varying densities (often in extreme setups from very light to very heavy), and
difficult weaves often found in technical applications.So, what did weavers do in Germany, Italy,
France and other highly developed nations They had to find their specific niches and learn that
survival in todays market means getting top-quality product to customers faster than ever before
and, importantly, faster than cheaper imported fabric can be delivered. This, say the makers of the
worlds textile equipment, is the key to the revitalization of weaving in the United States.
DornierGermany-based Lindauer Dornier GmbH promotes strongly the concept of its weaving
machine system family. The company states that flexibility and versatility are the key components
of future investments, especially in high-labor-cost countries. The Dornier system family of rapier
and air-jet machines is designed around a modular concept. Lately, special attention has been paid
to details such as reduced machine downtime and improved handling of mechanical functions,
electronics and on-line communication. Dorniers rapier weaving machines are capable of an extensive
range of applications with cam or dobby shedding, or with an electronic jacquard machine. Article
changes on the fly with different filling yarns recently were demonstrated at ITMA Asia 2001.The
versatility of the Dornier air-jet weaving machine has been extended by integrating the patented
Fast Dobby Change (FDC). A positive cam motion can be replaced by a dobby in a short time and as
the market situation requires. Dornier claims this conversion can take place within the time frame
of a style change.Recently, Dornier introduced its new terry weaving machine, EasyTerry. This
air-jet machine optimizes performance, drastically reduces the number of mechanical components,
decreases wear and achieves a higher weaving efficiency than similar
machines. PicanolBelgium-based Picanols OMNIplus air-jet has been presented to clients with
newly developed air tuckers. The OMNIplus also features the new cyber-display, which gives the
individual weaving machine a Web-enabled man/machine interface.The new TERRYplus is the air-jet for
terry towel fabrics. This Picanol-Gunne machine is based on the OMNIplus technology and, according
to the company, offers extremely high terry quality because of its swinging reed pile formation.
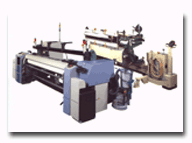
The ability to swap the back part of the split frame on Picanols rapier and air-jet weaving
machines allows style changes in 30 minutes.The Gamma rapier machine offers a wide field of
applications even up to heavy canvas. The ETM on-screen tension control of the filling yarn, and
special waste-reduction scissors on the left-hand side are some of the latest features added.The
Cyclops system for automatic on-loom inspection uses a traveling camera system mounted in the loom
in order to inspect the fabric. In case of a running defect, the system stops the loom. The SUMO
switched-reluctance motor that is available for Picanol machines has been a huge success, as it
drives the weaving machine directly without belt transmission or clutch and brake. The motor speed
can be varied almost instantly from extremely slow motion to top speed by simple electronic
control.By entering the accessories business for textile machines (with the acquisition of Steel
Heddle and Verbrugge NV), Picanol will also play a role as a supplier of consumable goods
(See Supplier Notes, TW, January 2002).PromatechItaly-based Promatech, the recently formed
manufacturing group that includes Somet and Vamatex weaving machines, provides rapier and air-jet
weaving machinery technology to satisfy practically all weaving needs.The newest offering, the
Somet Alpha series, is designed to combine technology, ergonomics, versatility, reliability and low
running costs. The Alpha is available in single-beam and twin-beam models, with upper-beam and
double-beam models under development. The machine is available in dobby version featuring either
the Fimtextile 3080 or Stli 2670 or in electronic jacquard version. Fifteen different widths are
available. Somet also generated success recently with its much-reviewed Super Excel rapier weaving
machine and Mythos air-jet machine.The Vamatex Leonardo is a negative rapier weaving machine that
targets the highest performance levels in the rapier weaving sector. Vamatex says the Leonardos
machine concept is geared towards the production of quantity and quality, offering quick response
to the variability of orders and output requirements of todays global textile industry. Other
weaving machines from Vamatex are the P 1001 SuperEK, which is a highly competitive loom in terms
of initial investment offering high productivity with lightweight rapiers, and the Vamatex 9000
Plus ES, which features positive rapiers mounted on flexible ribbons for maximum versatility. The
Leonardo DynaTerry is a terry weaving machine that offers a combination of performance, versatility
and efficiency. Sulzer TextilThe Itema Group of Italy, the parent of Promatech, acquired
Switzerland-based Sulzer Textil in 2001. Sulzer Textil will remain a separate business, but it can
be expected there will be significant exchange, integration and standardization of equipment
technology within the Itema Group. Sulzer says its projectile weaving machine with sales of more
than 150,000 machines worldwide is the most successful weaving machine in history relative to a
specific weft-insertion system. Its low energy consumption, wide variety of applications, and
suitability for technical and industrial applications allow the projectile weaving machine a strong
position in textile manufacturing. Sulzer Textils Customized Weaving Technology is the specialty
fabrics division where tailor-made weaving machines are designed and produced. For example,
machines can be designed to produce agrotextiles and geotextiles, conveyor belts, sailcloth, tire
cord, cinema and theatre screens, filtering fabrics, tarpaulins, wire fabrics and many other
industrial products.
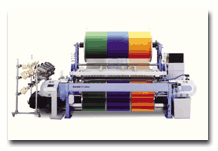
The G6200 rapier weaving machine has proved itself by being a strong competitor, with more
than 5,000 units sold since its introduction in 1999. The new G6300 offers higher insertion rates
and an even better price-to-performance ratio, the company says. The Sulzer G-series rapier
machines have successfully entered many diversified fields of weaving and, for example, can show an
impressive success in airbag fabric weaving. Sulzer Textil also offers a terry version of the
G6300.The L5200 air-jet weaving machine is especially suitable for the economical production of
standard fabrics such as bed linens and linings. It is successful as well in the field of glass
fiber fabrics, in which Sulzer claims it is the market leader. The M8300 multi-phase weaving
machine produces simple, standard fabrics with an extremely high weft-insertion rate.
ToyotaJapan-based Toyota Industries Corp. (formerly Toyoda Automatic Loom Works Ltd.)
concentrates in the United States on the sale of its LW600 water-jet weaving machines. The LW600s
electronic let-off, in conjunction with a newly developed automatic pick-finding system, achieves
the optimum in warp yarn control, sharply reducing start marks and ensuring fabric quality,
according to Toyota. As well, the company offers the JAT610 air-jet, which is designed for
efficiency and high-speed operation for fabrics ranging from cotton and wool, to spun fabrics such
as denim, filament and fiberglass. The JAT610s all-in-one frame is manufactured by a high-tech
production system based on Toyotas advanced automotive production process.
TsudakomaTsudakoma, Japan, emphasizes that its air-jet and water-jet weaving machines are
backed by a robust frame structure and strong beat-up systems that allow ultra-high-speed operation
and heavy-duty fabric weaving. The ZAX-e, Tsudakomas brand-new model air-jet weaving machine, is
equipped with the iT board, which features a touch-type operation with color graphical interface.
The ZW408 is Tsudakomas new model water-jet weaving machine that has improved basic functions for
higher productivity, higher operation efficiency and highest standard of fabric quality. Van
de Wiele Carpet And Velvet WeavingBelgium-based NV Michel Van de Wiele is one weaving machinery
manufacturer that seems to have had good to very good sales years over the past decade. Not long
ago, the company acquired Germany-based Memminger-IRO GmbH, manufacturer of feeders for knitting
machines, and Bonas Machine Company Ltd., United Kingdom, a manufacturer of electronic jacquard
machines. Even though velvet weaving machinery sales seem to be down presently, the carpet sector
holds steady, with an upward sales trend. The consumer preference is towards more expensive rugs
with a wider variety of fiber and yarn materials because the latest machine-woven rugs look and
feel very similar to handmade rugs.
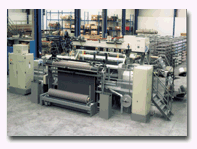
Van de Wiele recently introduced a new carpet weaving machine, the CLP81
(See CarpetandRug News, TW, this issue). The new machine is a modified version of the
CarpetandRug Tronic CRT82, capable of weaving loop-pile carpets. Dorniers Legend Says Auf
WiedersehenBefore the end of the past year, Hans Geiger, long-time president of American Dornier
Machinery Corporation, Charlotte, N.C., said goodbye or in German, Auf Wiedersehen to many personal
and business friends in the United States.At the facilities of American Dornier, Geiger received a
surprise retirement reception, which included more than 150 customers, colleagues and friends. Even
his wife, Ingrid, flew in from Europe and surprised him with her presence. Geiger quipped that this
was one of the very rare occasions that made him speechless at least for a short moment.
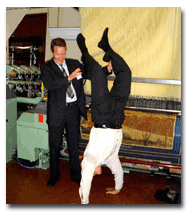
During the goodbye celebration, Geiger said, Ill show you that Im not an old man!, and swung
himself into a handstand.Geigers official retirement date was January 1. He handed over the reigns
of the company to Peter A. Brust, 41, who brings with him a solid business and textile education,
as well as machinery sales experience. Brust was for 10 years plant manager with Rohleder HITEX,
one of the leaders in upholstery, jacquard and woven velvet fabrics in Germany. At the reception,
Geiger issued a strong vote of confidence in Brust and assurance of the continuity of a high level
of service.The retiring Dornier executive started his career with the company in 1956 as an
assistant weaver in the demonstration room in Lindau, Germany. A little over a year later, he was
sent out as a technician to Central America to install 24 shuttle weaving machines. Realizing that
he wanted more of a foundation, he went to study at the Textile Technology Institute in Reutlingen.
After his studies, he returned to Dornier. Geiger drew colorful pictures of the nightmares he had
with the first shuttleless Dornier machines, which worked on a much different principle than todays
machines. He said he had his sincere doubts about that technology, but he wanted to go only one
time to America. His wish was granted in the late 1960s, when he traveled to introduce Dorniers
rapier machines to U.S. weavers. But he saw very quickly that the first technology had too many
flaws. For certain applications, the U.S. market would not accept the selvage the machine produced.
However, CollinsandAikman, Siler City, N.C., was the first mill to install 24 rapier machines the
fathers of todays positive filling transfer technology and used them for the production of
automotive fabrics. This was a significant success for Dornier (and also for Geiger). From then on,
the industry started to accept Dorniers technology, and many other mills followed with orders.
Geiger started to travel 50/50 back and forth between Lindau and Charlotte, and there was no way to
stop him.At a point in the early 1970s, Geiger started to look for property to establish a service
center in the United States. He asked Peter Dornier Sr. for a very humble amount to purchase land
and to build the first physical building for Dornier in the States. In 1978, American Dornier was
established. By the end of 2001, approximately 9,000 Dornier rapier and air-jet weaving machines
had been sold in the United States and Canada, and certainly the majority can be in one way or the
other directly linked to Geigers personal efforts and diligence. The sales numbers and the image of
Dornier in the United States are indicative of his efforts.As he was preparing to depart, Geiger
said he plans to be back in the States soon. But this time, it will be for vacation.
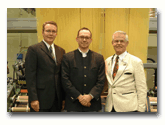
Left to right: Peter Brust, American Dorniers incoming president; Peter D. Dornier, chairman
of the Board; and outgoing president Hans Geiger. Quaker Fabric Weaving Profits
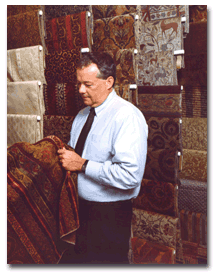
The willingness of the U.S. textile industry to develop value-added products and service
niche markets is a key ingredient to the overall success of the industry.Quaker Fabric Corp., Fall
River, Mass., is one of the weaving enterprises in the United States that combine these elements to
profitably weave fabric.Quaker began operations in 1945 as a small family-owned fabric mill. Today,
Quaker is one of the largest producers worldwide of jacquard upholstery fabric and one of the
leaders in the $2-billion-plus U.S. upholstery fabric industry. The company also produces specialty
yarns, which it uses in its fabrics and sells to other fabric manufacturers.Quaker Fabric has not
only been doing well over the past years, but also it is expanding its manufacturing facilities
with two additional pieces of real estate to be converted into manufacturing plants, according to
Jim Dulude, vice president, manufacturing. One is an 86,000-square-foot building in Fall River that
is to be a chenille yarn plant; the other is a 180,000-square-foot facility that will be the
prototype manufacturing complex where beaming, weaving, finishing and post-finishing will be
performed. The company is installing 36 new dobby-equipped Dornier weaving machines to produce
plain or simple weaves.Dulude mentioned that Quaker produces a significant portion of fabrics that
do not require the investment of much more expensive jacquard machines; therefore, the decision was
made to equip a safe portion of the production capacity with dobbies. Quaker has a large number of
existing Dornier rapier machines with jacquard set-up, and about 50 older looms, also with
jacquards. It really took a lot of soul-searching to get us to the dobbies, said Dulude. But Quaker
is sure this was a proper and cost-effective decision. The company plans to install about 90 dobby
machines in total. Rapier machines due to the nature of the business and fast-changing trends in
upholstery fabric design are the only sensible choice for Quaker Fabric, Dulude explained. We
design products for customers, and air-jet weaving machines and heavy chenille yarns just dont mix
well, he said.Quaker Fabric sees export sales as a necessity for survival. Larry Liebenow,
president and CEO, is aggressively pushing the company toward even greater participation in global
trade. Dulude said trading with foreign markets creates challenges for the manufacturer. Also,
preferred colors are different in foreign countries, often reflecting culture and environment. Part
of this export influence has led the company to offer a huge variety of styles. He said the days of
running all machines on the same style are gone. We have a wide variety of styles. In a typical
week, we will make more than 3,000 different SKUs [individual style pieces] in our mill. While
complex, this versatility enables Quaker to compete in the realm of specialties instead of in
commodities. Also, individual fabric piece lengths have been dropping more and more over the years.
This development challenges the abilities of the mill, and Dulude is convinced the companies that
can handle it are the ones that will succeed. It also requires a modern infrastructure to support
production planning and scheduling systems, as well as support and control systems for labor and
machinery. Quakers management believes U.S. mills can learn from their European counterparts. U.S.
companies can do well when they make their products more upscale. This model works in Europe but
can be internationally applied.Training and retraining of the labor force is very important for the
company, and Quaker does not believe in quick on-the-job training. Quality, commitment and
leadership are major ingredients Quaker expects from its labor-force. The company, though, supports
its employees with labor-friendly and structured action plans. It currently employs approximately
2,600 people.Quaker strives to be a world-class leader in the upholstery fabric industry and in
manufacturing of specialty textile yarns. This is achieved through exceeding customer expectations
and Quakers associates continually improving the value of the products, processes and services.
February 2002
BBA Group Restructures
BBA Group RestructuresThe BBA Materials Technology Group, Nashville, Tenn., a division of the BBA Group, is to close its Lewisburg, Pa., nonwovens manufacturing facility by the end of the month. BBA acquired the facility from International Paper in mid-1998 as part of its acquistion of Veratec.Our goal is to focus on and grow those technologies that we believe will provide our customer base with the products they require in the future, said Ross McMillan, CEO, materials technology group.February 2002