Seepex Introduces PumpsEnon, Ohio-based Seepex Inc. has introduced a range of MD metering pumps made from corrosion-resistant metals and plastics, and a multi-hose axial flow peristaltic pump (MAP) design.The MD metering pumps can handle very thin liquids and materials and are ideal for acids, hypochlorites, disinfectants and pH-control chemicals, according to Seepex. Rotating parts are available in 316 stainless steel, Hastelloy® C4, titanium and Kynar®. Casings are available in HDPE, 316 stainless steel and Halar® coated stainless steel. The MAP pump combines progressive cavity and peristaltic pump technologies, and offers sealless performance with fewer pulsations and longer hose life than conventional radial peristaltic designs, according to the company. The new pump can transfer and meter simultaneously up to six separate fluids. The product range includes four models with performance options to 17 USGPM and 90 PSIG. Product extensions for higher pressure are planned.March 2002
Interagency Group Will Address Textile Industry Problems
R
esponding to pressure from the U.S. textile industry and its supporters in Congress, U.S.
Commerce Secretary Donald L. Evans has announced formation of an interagency working group to
address international trade and economic issues plaguing the industry. Although the working group
enjoys the strong support of the U.S. textile industry, importers have raised concerns about
whether their views will be adequately considered.
Laura Jones, executive director of the U.S. Association of Importers of Textiles and
Apparel, warned, “You can’t evaluate what is happening on the manufacturing side without
understanding what is happening on the importing and retailing side.”
While the interagency working groups have not yet established a mechanism for receiving
input from various segments of the industry, Commerce Department officials told Textile World they
are aware of the importers’ concerns, which will be “taken into account” as work goes forward.
Evans said the working group, comprised of representatives from the Departments of Commerce,
State, Treasury and Justice, as well as the U.S. Trade Representative and National Security
Council, will work to implement the nine-point program the administration announced in December
(See “Washington Outlook,” www.
TextileWorld.com, January 2002).
The working group’s far-ranging agenda includes establishing trade agreement negotiating
objectives, ways to get compliance and enforcement of already existing trade agreements,
implementation of the quota phase-out under the Agreement on Textiles and Clothing, tariff
preference programs and export expansion for textiles and apparel. The group also will address how
to combat illegal transshipments of textiles and apparel, and how best to provide trade adjustment
assistance for companies and employees impacted by imports.
USDA Continues Cotton Promotion Assessments
The U.S. Department of Agriculture (USDA) will continue the mandatory assessments on upland
cotton production and imports of cotton textiles and apparel to support the Cotton Research and
Promotion Program. Assessments of roughly $2.25 per bale on upland cotton production and the bale
equivalents of cotton products provided $63 million last year for the research and promotion
programs of Cotton Incorporated, Cary, N.C. The funds are used for advertising and a variety of
research and promotional activities designed to encourage greater consumption of cotton textile
products.
A voluntary contribution program was initiated in the 1960s, but Congress made it mandatory
in 1990. Domestic mills and apparel companies pay the assessment if they import raw cotton or
cotton textile and apparel products. U.S. importers are opposed to the mandatory aspect of the
program, charging that it simply amounts to an ultimate tax on consumers.
Under the law, the USDA is required every five years to review the program and determine
whether there is justification for a referendum on continuation of the program among producers and
importers. The USDA said this year’s review showed there is a general consensus that the program is
working as intended, so it likely will be continued for another five years.
EPA Studies Rule On Air Pollutants
ook for the Environmental Protection Agency (EPA) to soon issue its long-awaited proposed
regulation setting the Maximum Achievable Control Technology for hazardous air pollutants. The new
rule could affect how textile manufacturers control emissions from a wide variety of wet processes.
In anticipation of the new regulation, the American Textile Manufacturers Institute (ATMI),
Washington, has been providing the EPA with economic and technical data in the hope that the
regulation will be practical and economically achievable by an industry already suffering from the
recession and foreign
competition.
Issuance of the EPA regulation has a May “drop dead” date, when state regulators will move
in if there is no federal regulation. The textile industry would much rather deal with a single
federal rule rather than a rash of state regulations.
Spooner Named Chief Textile Negotiator
The appointment of David Spooner as special textile negotiator certainly has gone down well
with the U.S. textile industry, and importing and retail interests don’t seem to have any problems
with him either. Spooner was legislative director for Rep. Sue Myrick (R-N.C.), a strong supporter
of the U.S. textile industry, and served as her advisor on textile trade issues.
In announcing the appointment, U.S. Trade Representative Robert B. Zoellick said Spooner’s
textile and Capitol Hill experience provides an “important and special perspective.” Spooner is
expected to play a role where textiles are concerned in the upcoming World Trade Organization (WTO)
negotiations and in the Bush administration’s efforts to get greater overseas market access for
U.S. textiles and apparel.
March 2002
China Shows Claim Success
China Shows Claim SuccessApproximately 21,000 visitors attended ITMEX 2001, Garmentec China 2001 and China FabricsandAccessories Expo 2001, held concurrently in South China late last year. Nearly 100 suppliers from Asia, Europe and the United States exhibited their latest textile and apparel machinery, technology, fabrics and apparel accessories at the three shows and reported receiving significant feedback from the attendees.The shows were organized by the CCPIT Xiamen Sub-council and BusinessandIndustrial Trade Fairs Ltd. Organizers have scheduled the three exhibitions to take place together again in November 2002.March 2002
Dr Thomas J Malone Addresses The 10th Annual National Textile Center Forum
Dr. Thomas J. Malone, president and COO, Milliken and Company, delivered the keynote address for the 10th Annual National Textile Center Forum February 10 in Charlotte.According to Malone, the U.S. textile industry is in the midst of its darkest days, but armed with accurate information and a willingness to fight for its survival, the industry can secure a profitable future.View Malone’s full speech by clicking here Click here to download a pdf copy of Dr. Malone’s speech
Former Burlington Executive Named To International Trade Post
James C. Leonard, former manager of economic analysis and director of government relations for Burlington Industries, has been named deputy Assistant Secretary of Commerce for Textiles, Apparel and Consumer Products. In that post, which has been vacant for more than a year, Leonard will be an adviser to the secretary of commerce on textile and apparel trade issues. He also will serve as chairman of the Committee for the Implementation of Textile Agreements, which administers the governments textile import quota program. The Commerce Department post and that of Special Textile Negotiator are the two of the most important federal government positions involving the textile and apparel industries and importers. The job of Special Textile Negotiator was recently filled by David Spooner, former legislative director for Rep. Sue Myrick (R-NC). Both Spooner and Leonard have considerable experience in dealing with textile international trade issues. For several years, Leonard traveled throughout the world as an industry adviser to government textile negotiators. He and enjoys the respect of both the textile industry and importing interests.
Finishing Touch
Finishing RoundupBy Gary N. Mock, Ph.D., Technical Editor Finishing TouchNew developments in wet and dry finishing produce value-added products for a discerning public. I t is often said that finishing is the most important step in the textile operation because the next set of eyes to see the product are those of the customer. New finishing products are continuously developed around the world, but special emphasis is placed on them during big show years. While 2001 was not an ITMA year (the next show will be held in Birmingham, United Kingdom, in 2003), there were three important shows this past year: ATME-I (Greenville, S.C.) in April, and OTEMAS (Osaka, Japan) and the new ITMA Asia (Singapore), both held in October. ITMA Asia was organized by the European Committee of Textile Machinery Manufacturers (CEMATEX) to offer a major show in the important Southeast Asia market with the specific goal of minimizing the numerous small and large fairs that had sprung up in the ITMA off-years. The cost of showing at all of these venues was becoming prohibitive.Chemical finishing has been shown to be extremely important when used in synergy with developments from machinery manufacturers. Partnerships abound. Following is a brief look at developments this past year. Wet FinishingAquatex, a new development that sprang out of the nonwovens field, has been released by Germany-based Fleissner GmbHandCo. A curtain of water jets 0.1 to 0.15 millimeters (mm) in diameter with 40 to 80 jets per inch, operating at a pressure of 20 MPa, and jet speed of 200 meters per second (m/s) impinge on the textile substrate as it moves underneath. The substrate is supported on a perforated belt or drum and is transported under the water curtain. Water is removed by suction and recirculated. The resulting fabrics are softer and can be constructed with fewer ends per inch than fabrics finished by other means. Upholstery has similar cover with fewer ends per inch and without a latex backing. Denim fabrics made with fewer ends and lower chemical content are more stable and shrink less during compacting. Because more than 3 billion denim articles are manufactured worldwide every year, there is a tremendous opportunity to make more surface with less woven product.For more than 30 years, fluorocarbons have been used in the textile industry to achieve water-, oil-, and soil-repellent properties. New chemical systems released by Rudolf Chemie GmbHandCo. KG, Germany, have enabled finishers to achieve these same results in an environmentally friendly, emission-free way. The reduction of the emission load by about 90 percent is dramatic. Results are achieved using booster chemicals that protect the reactive polyurethanes until temperatures are above 110°C. Surface coating and film stability are dramatically improved. Further, garments washed and air-dried are able to restore the important reorientation of the fluorocarbon tails without tumble drying or ironing.The consumer expectancy for easy-care finishing of cotton has been extended to woolen garments. There are two ways to negate the felting action of wool scales. The oldest and most common method involves the use of active chlorine to erode the scales by oxidation. The surface is subsequently masked by an epichlorhydrine resin. Ciba Specialty Chemicals, Switzerland, has released Dicrylan WSR, a new polyurethane system for washable wool fabrics. The new polyurethane pre-polymer allows crosslinking between the isocyanate group and the wool fiber, thereby masking the woolen scales that cause felting. A silicone rubber additive imparts a softer handle that can withstand tumble drying.Recently, phase change materials (PCMs) have been made possible using products developed for the National Aeronautics and Space Administration (NASA) to protect astronauts from extreme variations in temperature. More than 500 PCMs are known. Frisby Technologies, Winston-Salem, N.C., has been a pioneer in the development of technologies for microencapsulation of these various materials. Coating systems such as the Ciba Dicrylan PMC/PHR, in combination with PCMs, have been shown to offer comfort over a wide range of conditions.Cavitec AG, Switzerland, has been a leader in the development of technical textiles. The improved quality and application flexibility, together with a tremendous drop in cost, make hotmelt the most advisable adhesive for composites in general. The meltprint and screenprint methods use either an engraved roller or a specially designed screen to apply the hotmelt onto a substrate that is subsequently laminated with another substrate to form a composite. Cost, weight reduction and recyclability have put additional pressure on the automotive industry to find new ways to build cars. Comfort, durability and fogging are important in the design of automotive interiors. Hotmelt lamination offers clear advantages. Laminating and coating technology was given a boost when Schaetti AG, Switzerland, manufacturer of thermofusible powders, took over the lamination technology of Kannegiesser and now offers a complete range of thermofusible adhesive products.The worldwide boom in the use of elastane fibers has led to new technologies to safely handle these elastic fabrics without damage. Growth is estimated at 12 to 13 percent for the foreseeable future. It has been estimated that nearly 50 percent of the garments being produced today contain some elastane to help with shape retention. The EcoFix/2 tubular finishing system by Lindauer Dornier GmbH, Germany, stabilizes by heat-setting in tubular form. Two separate chambers allow the goods to be set with minimal selvage marks from being rolled on the knitting machine. If goods are processed soon after knitting, the roll edge is nearly invisible following finishing.Bianco S.p.A., Italy, has also developed a new Linea apritubolare, or tubular opening line, to handle and stabilize tubular goods at speeds of 60 to 80 meters per minute (m/min).
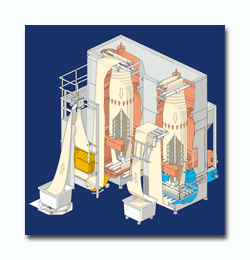
Schematic of Dornier’s EcoFix/2 heat setting machine for tubular knitwear. DryingThe yellowing effect of elastane-containing fabrics caused by direct gas and oil-fired drying has been eliminated with Germany-based A. Monforts Textilmaschinen GmbHandCo.s Exxotherm indirect gas heating system. Hot combustion air is fed from the gas burner through an isolated heat exchanger within the tenter and exhausted by a secure exhaust duct. No combustion gases contact the fabric. Exxotherm is available for the Montex 5000 and as a retrofit for all Montex 4560 (F configuration) machines. Dry FinishingSoftening denim by surface abrasion during garment finishing is time-consuming and can destroy the garment-finishing machines. The Petra machine developed by Biancalani S.p.A., Italy, and first shown at ITMA 99 in Paris, has been made more reliable and delivers higher productivity. Operating at 10 m/min, the Petra uses abrasive cylinders combined with water. The moistened fabric is fed directly into a compressive shrinkage machine for final finishing.The latest development from Comet S.p.A., Italy, is the Pegaso-X11 napper. The active surface uses four silicone carbide brushes and four sandpaper sueding rolls to soften or sand without raising a noticeable pile.The CIBI Compactex, a new compacting machine by Cibitex S.r.l., Italy, is capable of handling widths up to 3.4 meters. The line was developed to soften and stabilize bed sheeting and home furnishing fabrics.SperottoRimar, Italy, a member of the Switzerland-based Santex Group (American Santex Inc., Spartanburg, S.C.), has recently added the Decofast continuous-steam decatizing system to its product line. The objective of Decofast is to exceed the results of traditional batch decatizing machines that use the continuous-atmosphere decatizing process. The machine features adjustable steam under pressure up to 3 bars at temperatures up to 135°C. Decofast is suited for pure wool worsted fabrics, stretch fabrics in wool and poly/wool blends, woolen fabrics in wool/wool blends and pile fabrics, as well as cellulosic and silk fabrics. Applications included for the process are as a final decatizing treatment, as a preparation of fabric before kier decatizing, and as a finish decatizing treatment after kier decatizing. Santex has developed a new Santa brush machine that uses abrasive brushes. In singeing, Menzel, Spartanburg, offers the high-velocity singer (HVS). The machine is the result of a complete reengineering project and, according to the company, performs at three times the speed of traditional singers. The firing rate of the burners is automatically proportional to line speed, keeping the singeing rate constant. ParksandWoolson Machine Co. Inc., Springfield, Vt., has introduced a new Phoenix Polybrush sueding machine for knitted or woven fabrics of all weights (See DP&F News, TW, January 2002). The sueding machine produces a drapeable fabric with a soft hand, according to the company.Eduard Kusters Maschinenfabrik GmbHandCo. KG, Germany (Zima Corp., Spartanburg), has redesigned its two-roll calender with the Swimming Roll to create a more compact and maintenance-friendly machine. The calender features new, up-to-date components, is service-friendly, and can be used in a small space. As well, it features an optimized piping system for lubrication, a cardan shaft drive, decentralized I/O wiring, a Siemens operator panel and easy change of the Flexroll sleeve.Glenro Inc., Paterson, N.J., recently purchased some of the assets of Burlington Textile Machinery Corp. (BTM), also in Paterson. The technology and manufactured product lines of BTM Corp. that were purchased include: fabric-guiding and spreading systems; Tru-Wind Surface and A-Frame winders; accumulators; Spraymiser low-moisture applicators; Tru-Brush lint-removal and pile-orientation systems; laboratory padders; automated comforter filling ranges; roto-brush wet-lint filters; and BTM designs of many auxiliary machines.Glenro also has new offerings in the area of flatbed fabric-laminating machines. Glenros systems place the materials under precisely controlled heat and pressure. A continuous pane of heat from the top and bottom with pneumatically adjusted pressure produces finished materials with complete adhesive coverage for a strong bond. The process eliminates wrinkling, as well.
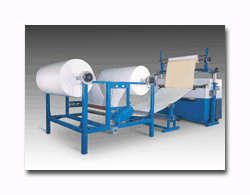
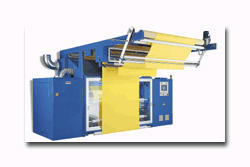
Two new machines were introduced recently by Lafer S.p.A., Italy. The first machine, Ultrasoft, was designed to create a dense and low-cut brushed-suede finish on knitted fabrics. The UltraSoft is supplied with six brushes in drum configuration, which create a multiple action effect. Both the drum and the brushes can rotate in different combinations to achieve the desired surface finish on different fabric types. Originally developed for knits, the UltraSoft also has been shown to work well on woven fabrics, according to the company. Lafers second new finishing machine introduction, Microsand, incorporates synthetic diamond emery on 24 rollers. It is suitable for all types of fibers and structures, but it has proven popular on shirtings and synthetics.March 2002
Techtextil Industry Hotspot
Techtextil North AmericaBy Janet Bealer Rodie,Assistant Editor Techtextil: Industry Hotspot
Exhibits, symposium will offer North American visitors a comprehensive overview of technical
textiles today. W hen it comes to market size, innovation and the use of engineered fiber
products to solve problems, North America leads the world in the textile industrys technical
textiles sector, according to Germany-based Messe Frankfurt, producer of Techtextil International
Trade Fair for Technical Textiles and Nonwovens. The German trade fair organizer projects annual
growth rates in this specialized sector will exceed 5 percent through 2005. In an effort to serve
the North American market, Messe Frankfurt introduced Techtextil North America (TTNA) on this side
of the Atlantic in March 2000 as a biennial event that is juxtaposed to the original German
exhibition held in Frankfurt in the spring of odd-numbered years. Messe Frankfurt also stages
Techtextil exhibitions in South America and Asia in the fall of alternate years.For North America,
the location is Atlanta, and this years TTNA will take place April 10-12 at the Cobb Galleria
Centre.According to Messe Frankfurt, the shows are recognized as the most comprehensive technical
textiles and nonwovens trade fairs produced, representing all aspects of this growing and promising
sector of the textile industry. Other trade shows for this field, and also for most other segments
of the industry, focus on particular aspects, such as fabrics and yarns, or machinery.
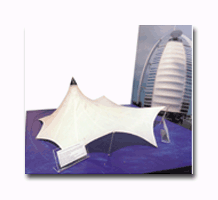
Architectural membranes are among the many technical textile applications that will be shown
at Techtextil North America.The inaugural TTNA in 2000 brought together 254 exhibitors and more
than 4,300 visitors from 16 countries. This year, more than 300 exhibitors and 5,000
buyers/visitors from around the world are expected to participate in the show. In addition to
individual exhibitors, there will also be national pavilions grouping exhibitors from several
countries including France, Germany, Spain and Taiwan.Representatives from
Textile World and
Textiles Panamericanos will be on hand at the exhibition to meet with Techtextil
exhibitors and visitors and distribute complementary copies of both magazines. A Comprehensive
ExhibitionAt TTNA, technology, research and development, planning, consultation, machinery and
equipment manufacturers, associations and publications will exhibit alongside the entire material
supply chain from raw materials; to fiber, yarn and fabric manufacturers; to converters and
finishers; to end-products and recycling. To help visitors find exhibitors in specific categories,
the exhibition manual will group exhibitors according to products and services offered:research,
development, planning, consultation international institutions, national research institutes,
universities and polytechnical institutes, industrial research centers, planning and consulting
companies;
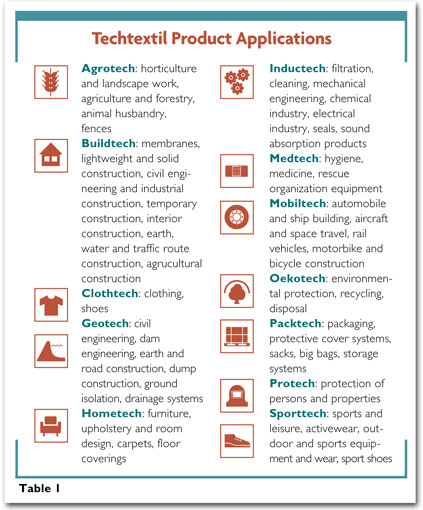
technology, machinery, accessories production processes, processing technology, machines and
equipment, control and monitoring methods, purification and regeneration technology, technical
accessories, laboratory and measuring equipment, quality assurance;fibers and yarns;woven fabrics,
laid webs, braiding, knitted fabrics tapes, strings, cords, belts, ropes, cordage,
nets;nonwovens;coated textiles, laminated, textiles, tent fabrics, packaging materials, tarpaulin
fabrics, awning materials, manufacture of end products, accessories;composites reinforcing
textiles, composite textiles, prepregs, structural components and mouldings, fiber-reinforced
materials, membrane systems, films and sheeting, textile-reinforced plastics for concrete
components, pipes and containers, textile sheet products for lamination with solids such as metal,
plastic or glass;bondtec finishing, adhesive, sealing and moulding materials, laminating and
coating materials, raw materials and additives, application processing, material pretreatment,
plastics and other hardening masses, adhesive mixing and application equipment, robot technology,
surface treatment technologies, plasma treatment, flocking, foaming; andassociations,
publishers.Companies also will be listed in the manual according to product applications (See Table
1). Techtextil SymposiumTTNA is coupled with Techtextil Symposium North America (TTSNA),
which opens April 9 with a keynote address by John A. Boland III, GTMA (The Association of Georgias
Textile, Carpet and Consumer Products Manufacturers) executive in residence at the Georgia
Institute of Technologys School of Textiles and Fiber Engineering, Atlanta. Boland will present
observations on the evolution of industrial textiles. Following the opening general session, which
includes presentations on the state of the industry, new directions, a global perspective and other
subjects, TTSNA will offer three days of seminars covering such topics as new and emerging
technologies, standards and testing, research, construction textiles, interior textiles, product
development and marketing, nonwovens technology, developments in high-performance fibers and yarns,
transportation textiles, and developments in protective textiles. Future Techtextil
EventsMesse Frankfurt will stage Cinte Techtextil China in Shanghai September 25-27, 2002.
Techtextil will again be held in Frankfurt April 8-10, 2003; and Techtextil South America will take
place in SPaulo, Brazil, November 11-13, 2003.The list of exhibitors that follows is up-to-date as
of
TWs press time.
For more information about Techtextil North America and Techtextil Symposium North America,
contact Messe Frankfurt Inc., 1600 Parkwood Cir., Atlanta, GA 30339; (770) 984-8016; fax: (770)
984-8023; e-mail: info@usa.messefrankfurt.com; www.usa.messefrankfurt.com. Techtextil
Exhibitors, Booth LocationsAATCC138AccuMotion Control Technologies715Acordis Industrial
Fibers720Aderly301-303Adhesive Films Inc.621Ahlstrom Fiber Composites332A.H. Rice Corp.335Alexander
Fabrics Inc.237Allied ConvertingTechnologies715American Kynol Inc.224American Liba639Apex Mills
Corp.105APIM203ATI Advanced Testing Instruments Corp.735Atlantic ThreadandSupply325Auto
Interiors735Bafatex Bellingroth1138Bally Ribbon Mills121BASF Corp.1011Beaver
Manufacturing433Bekintex751belChem Fiber Materials GmbH938Bemis529bluesign Technologies825Bond Cote
Corp.233Paul Bonte – Fils Techniques205Bostik714Boston/Bacon Felt Co.239Bradford
Industries820Brawer Technical Yarns Division828British Millerain Co. Ltd.724Business Link
NorthManchester1121Christoph Burckhardt429Canadian Textile Journal132Cargill Dow LLC334CarbonX
PerformanceFibers Division1319Carrington Performance Fabrics Ltd.722Cavalier Textiles839Cavitec
AG1020Cerex Advanced Fabrics910Chapman Thermal Products1319Clariant Corp.536Club Textile
Integral305Clubtex203Coatema EngineeringGmbH c/o Bollinger432Consoltex Inc.914Conwed
Plastics1310Cooley Group, The810Cortex S.A. 210Culimeta America Inc.1301Dailytec201Deerfield
Urethane/A Bayer Co.644DHJ International120Dietze+SchellMaschinenfabrik1035Dilo Inc.1000Dimension
Polyant123Dickson PTL307DMT313Dow Chemical920Dubar Warneton211Duflot – non-tisstechniques100Duro
Industries538S.A. Philippe Ebelmann200Elk Inc.935Ems-Chemie (North America) Inc.828Engineered Yarns
Co.750Enka Tecnica GmbH429Espace textile de Lyon et region301-303Europlasma NV732Everest Textile
Co. Ltd.605Fabric Development Inc.240Fachhochschule Hof,Abteilung Munchberg1151Fairview Machine
715Febeltex745Fi-Tech429Fiber Dynamics Inc.336Fleissner GmbHandCo.1029Flexabar835Future
Materials136Gehring Textiles/Militex320Gem Urethane537Gentug Technical TextileProducts221Gerlingher
GmbH1050Girmes In-Tex GmbH1028Glenro Inc.1300Glo-Tex International Inc.434Green Textile
Associates837Guilford Mills Inc.220h.k.o. Isolier- und Textiltechnik GmbH928James H.
Heal735Heberlein North America124H. Hergeth GmbH1144Highland Industries Inc.300Honeywell
Performance Fibers900HunterLab635Huvis/Republic of Korea504IBENA728Industrial Specialty
Fabrics532Interkordsa Inc.421Industrie-Vereinigung Garne-Gewebe-Technische Textilien849Institut fur
Textil- und VerfahrenstechnikDenkendorf1136Institut frans du textileandde lhabil301-303
International Fiber Journal127InterprojektGPITS Publishing633ITW Dynatec924Jaeger Textile
Tapes Corp.937Johnston Industries500Jomar Softcorp International628Jowat Lobers u. Frank GmbHandCo.
KG1032Kappler Protective ApparelandFabrics528Keith Manufacturing Co.1303Keramab NVGPKings Metal
Fiber Technologies Co. Ltd.605Kleinewefers Textile Machinery Corp.428Klevers GmbH
1149Klieverik314KoSa1010Kruss USA234Eduard Kusters Maschinenfabrik GmbHandCo.314Kuraray America
Inc.1120Lacent Technologies Inc.520Lacom Vertriebs GmbH1129Laroche S.A.208Lawson-Hemphill
Sales739Lectra1305Lenzing Fibers/Ivodex338Leesona Industries330C.A. Litzer Co. Inc.140Lumat B.V.
Netherlands729Mahlo America325Martin Color-Fi634Mayer Textile Machine Corp.428McAllister
Mills510Mehler Engineered Products GmbH1114Messe Frankfurt GmbHTBDHerbert Meyer GmbH1049Miller
Weldmaster Corp.236MillikenandCompany700Murtra Leon910N.C. State University College of
Textiles143Narcote LLC129National Drying Machinery Co.107National Jet Co.324Nawon USA
Inc.337Nonwovens Industry238Nordson Corp. Fiber Systems615Noveon Inc.229Olbrich314Outlast
Technologies338P-D Glasseiden GmbH1146Pennel Industries104PGI-Polymer Group Inc.539Pharr
Yarns811Plastibert915Polimeros y Derivados S.A. de C.V.1124Porvair International228Powerloom
DevelopmentandExport Promotion Council103Precision Fabrics Group1015Proline Textile
S.a.S.122Protechna Herbst GmbHandCo. KG1134Pyradia715Reichhold Inc./Swift Adhesives1120Reimotec
GmbH1036Rieter Perfojet241rokona Textilwerk1128Robatech USA Inc.736Roscontract, The FederalContract
Corp.345Rovitex 309Royal Ten Cate810Rubans Gallant S.A. 110Rue Polotsk PASteklovolokno738Safety
Components Fabric Technology310Georg Sahm934Saint-Gobain Quartz838Sarna Xiro621Saunders Thread
Co.514Seaman Corp.1308Service Thread Mfg. Co.534Schaetti AG611Schoeller Textil GmbH1043SGL
CarbonGPSGL Technic Ltd.1039Shanghai Sealtex Co.235Shawmut Mills933Sider Arc S.p.A.614Sitip
S.p.A.614Sourex Co. Ltd.436Southern Felt Co.829Southern Mills Inc.800Spinnkock USA Inc.1004Spunfab
Adhesive Fabrics632SSM Industries438R. Stat S.A. 206Stockhausen Inc.814Stoll H. GmbHandCo.946Stork
Screens America128StotzandCo. AG524Stre+Hess GmbHandCo. KG.1133Struto LLC710STT
311Sunfil-Turati-Fil Man Made Group1316SynteenandLuckenhausTextil-Technologie1140Tah Tong Fiber
Technologies Co. Ltd.605Techtex Vliesstoffe 1132Teijin Twaron USA Inc.400Telsonic AG130Tetratec
PTFE Technologies1306Textile Engineering Auburn UniversityTBD
Textile WorldTBDTextiles Human Resources Council733
Textiles PanamericanosTBDTextiles Tecnicos S.A. de C.V.741Textest Instruments741Thai
Taffeta Co. Ltd.1302Tietex International Ltd.815Tissavel 102Titex Vertriebs GmbH944Toom Tekstiil
Ltd.109Tournier JulesandFils 315TUT – Technical Usage Textiles 301-303Ubifrance301Ungricht
GmbHandCo. KG429Uretek/Coated Fabrics Group414Wacker Silicones Corp.610Wenzelband GmbH324Western
Nonwovens Inc./Needlepunch Div.638Wise Industries328W.L. GoreandAssociates435Xirion747Xymid
LLC339Yamuna Industries Ltd.1124YKK (USA) Inc.535Zenith Products Division Parker Hannifin
Corp.125Zima Corp.314J. Zimmerman Maschinenbau GmbH721Zoltek437Zwick USA341GP: German Pavilion
March 2002
Woolrich Nester Hosiery Partner For Sock Line
Woolrich, Nester HosieryPartner For Sock LineWoolrich Inc., Woolrich, Pa., announced a licensing agreement under which Nester Hosiery Inc., Dobson, N.C., will produce a line of outdoor socks designed to be worn with Woolrich apparel.The socks will be made predominantly of merino lamb’s wool and will be available in 11 styles including the tri-tone Ten-Mile Day Hiker, the CoolMax® Hiker for warm conditions and the TechnoWool Ragg sock for multiple uses.March 2002
Industry Activity
Fiber WorldBy John E. Luke Industry ActivityLast year’s performance demands decisions and action for survival in 2002. In the wake of the moral and economic shocks suffered by the United States since September 11, it appears time to return the focus of Textile Worlds Fiber World feature to the distribution patterns in the fiber and fabric industries and to provide a look at the preliminary results of textile industry activity in 2001. Industry performance last year seems to point to even more survival decisions for 2002 and beyond. A Point Of Comparison
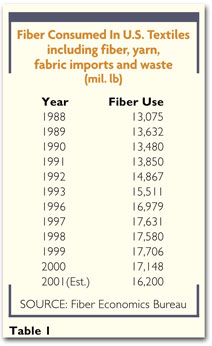
Traditionally, industry activity has been explored as a stand-alone process without detailed comparisons to other periods. The pace and depth of activity in 2001 suggests methodology may be lacking. An interesting correlation of trends appears to exist between the recessions of 1989/1990 and 2000/2001. This report will focus on 2001 as part of a greater cycle 1996 to 2001 comparing industry activities and opportunities to those from 1988 to 1993.The year 2001 was set apart by the horrific September events superimposed upon an economy struggling to stay afloat after a dozen years of prosperity. Granted, textiles did not always share that prosperity, as additional exogenous events forced competing economies into socio/political/economic decisions that changed the world platform for textile and apparel manufacturing and distribution. Given this aggregation of economic forces, the traditional stand-alone methodology will be broken in order to understand 2001 by trying to deal only with those actions induced by events over which the textile industry might have some control.Many textile spokespersons focus on imports in describing the ills of the U.S. textile economy. Imports are a problem that will not go away. Industry leaders, pundits and observers can rail against executive and legislative government as they appear to sacrifice textiles on the altar of trade, but the die is cast: the textile industry has overstayed its welcome at the trough of protectionism. The apparent reluctance of at least part of the industry to employ modern management approaches and its very reliance on entry-level employment encourage government to jump to politically expedient conclusions. Survival now demands decisions and actions through which the industry will find products and distribution channels somewhat less susceptible to foreign incursions.Many events are burned into our memories of textiles in 2001: September 11; the recession; increasing imports of garments and made-up items; mill closings; layoffs; and hundreds of smaller individual hurts. It is sometimes tempting to ask what else can go wrong. The lesson from our countrys history is not to focus on the bad, but to examine events, determine their causes and provide solutions that preempt repetition.There is an interesting correlation between Textiles 2001 and Textiles 1990. Both years are characterized by stagnant/decreasing textile activity in a national economy of the same description. The interesting view comes by examining the paths textiles took into and out of each recession and the structure of the industry in and after recovery. Table 1 outlines total fiber consumed in U.S. production of four major end-use categories: apparel; home textiles; floor coverings; and industrial and other consumer-type items. The data reflect only items manufactured in the United States, but also include raw material fibers and fabrics imported for inclusion in these items.The first notable message in Table 1 is the almost catastrophic usage estimate for 2001. Preliminary Fiber Economics Bureau (FEB) data for domestic consumption, plus traceable imports of fibers, fabrics and waste, paint a grim picture for U.S. textiles. Statistical and anecdotal evidence has been accumulating for years, although the industry has until recently continued to report increased total fiber consumption. It appears that a change, probably one necessitating fundamental revisions in goals and strategies, is about to descend upon American textiles.The important information from Table 1 lies in subtracting domestic shipments from total consumption to note how fiber and fabric imports add to the pressure already caused by imported garments. In 1988, fabric and fiber imports totaled 452 million pounds. As U.S. industry rallied from the 1989/1990 recession, 1993 fiber and fabric imports had risen to almost 1.5 billion pounds. By 1996, fiber and fabric imports had jumped to 2.27 billion pounds and were starting a rise to almost 3.0 billion pounds estimated in 2001. Distribution ChangesAn even more interesting pattern emerges when the data in Table 1 are graphed (See Figure 1). The U.S. textile industry has worked through the 2000/2001 recession in a manner almost identical to that in which it survived the 1989/1990 experience. In each period, fiber use rose approximately 4 percent in the year preceding the recession and declined about 1 percent the next year. In the third year, industry shipments rose again: 1991 exceeded 1990 by 2.7 percent and 1999 beat 1998 by slightly under 1 percent in retrospect, a sign of impending change.Unfortunately, the two graphs now begin to diverge, definitely foretelling a fundamental change in U.S. textiles. Domestic fiber usage stagnated in the 1988/1991 period at approximately 13.5 billion pounds, finally rising above 14 billion pounds in 1992 and above 15 billion in 1993. Recovery was at hand. In the 1996/2001 period, domestic shipments rose from 14.7 billion in 1996 to 15.2 billion in 1998, and then industry began to derail. 1999 industry consumption dropped to 15.1 billion; in 2000, consumption declined to 14.6 billion pounds. Through 1999, total industry consumption rose, with the domestic shortfall satisfied by imports. From 1996 through 2001, imported fibers and fabrics captured 500 million pounds of the U.S. market while from 1998 through 2001, the recession cost U.S. producers 1 billion pounds.
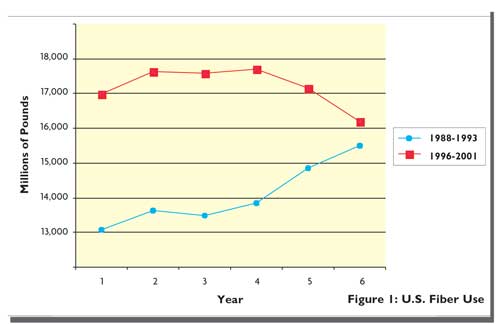
2001For textiles, 2001 will prove to be a watershed year. The industry must decide how to operate in a national environment likely unsympathetic to pleas for continued protectionism.In the data shown in Table 2, 14 percent of 1999 usage, 15 percent of 2000s and 18 percent of 2001s are estimated to come from imported fibers and fabrics. The losses in home fashions and carpet markets are logical, given changes in housing starts in the recession. One can rationalize the drops in industrial market distribution, although the gross numbers cover some important details, which are partially revealed in labor productivity statistics (See OTEXA Data Reveals Export Opportunities, ATI, November 2000).Fiber use in nonwovens has risen almost 20 percent since 1996. Measuring industrial markets by pounds is not entirely accurate because many traditional knitted or woven structures are being replaced by generally lighter, nonwoven substitutes; the actual loss to traditional weaving mills is larger than poundage comparisons reveal.The real issue comes down to apparel. The labor sensitivity of apparel is driving manufacturers to Southeast Asia, but the U.S. apparel business will not disappear. The question becomes: how far down will fiber usage fall before a much smaller, more nimble base industry begins to emerge And, more importantly, who will remain For various reasons, home fashions, carpet and industrial end-uses are substantially less vulnerable to imports than is apparel, and they have provided cover for lost apparel sales. However, there are limits to the size of home fashions and carpet apparently, current levels. Lacking a serious breakthrough in industrial fabric technology, industrial growth seems limited. The 2001 fiber performance, supported by the plethora of layoff and mill-closing announcements, shows there is scant room for some current apparel fiber and fabric suppliers to crawl into home fashions, carpet and industrial markets.
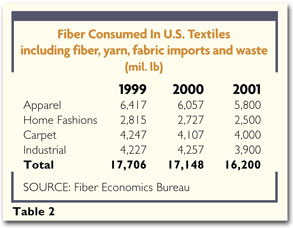
How To SucceedIf textiles does nothing to stem the loss of textile and apparel production and jobs, the losses will continue. The World Trade Organization (WTO) takes its final steps onto the stage in less than three years. Quotas will disappear and the full trade weight of economically ambitious developing nations will focus on the United States. Political decisions have displaced economic selection processes in trade. Analysis of exports by U.S. manufacturers must conclude that the playing field is not level now and will become less so with full implementation of the WTO. Certain markets are difficult to enter or are closed to U.S. manufacturers, despite the reverse being open.Market strength built on knowledge is an answer, implemented by joining with more countries in North American Free Trade Agreement (NAFTA)-like trading plans. The European Union (EU) has formed a rigid trading bloc, and Asia appears to speak with a single voice. In contrast, the United States, the object of desire for every exporting nation, sails alone. Arguably, NAFTA has increased trade among the participants. Taking advantage of shorter lead times, Mexico has replaced China as the single largest exporter of apparel to the United States, although shipments from the total Asian region continue to dominate. Mexico probably has gained more from NAFTA than has the United States, but this is a natural consequence of a capital-goods nation trading with a labor-capital nation. The United States ships raw material; trading partners add labor value and return finished product.Can the United States bring Central and South America into the NAFTA model Does the United States gain any advantages by joining with additional Western Hemisphere nations Answers must be viewed with a long-term perspective. Rather than expend political capital defending politico-trade skirmishes in the WTO, should the United States strive toward associations that grant greater voice and strength in trade The United States, as the center of a trade association in the Western Hemisphere, surely carries a larger stick than it would alone. While the political impact of this strategy should be almost immediate, it will take years to identify, train and operate large-volume, labor-sensitive manufacturing in the developing nations of Central and South America. Economic gains can be visible early, though. Once negotiating progress is apparent, companies will act to uncover benefits, customers, trade-encouraging policies, improved infrastructure and other advantages. Time’s A-Wastin’Time is of the essence. If the United States is to expend political capital, there must be a rapid move to enjoy the fruits of its labors. Should the United States not encourage trade in its backyard to add to the regions voice and economic strength Europe and Asia are feverishly trying to negotiate trade pacts with Central and South American nations. It is certain these compacts will not favor the United States and might preclude future U.S. participation. The House of Representatives passed a resolution granting the President trade promotion (fast-track) authority. Similar legislation is inching through the Senate, scheduled for March discussions. If this nation wants to affect change, should pressure not be applied to areas where change is possible and long-term benefits can be offered Railing against the WTO will generate marginal changes; changing the balance of power by endorsing and promoting NAFTA expansion will force more decisions that favor the United States. As well, it is important not to lose sight of what business were in. Just moving a weave shed to Peru doesnt improve competitiveness. Exporting capital and knowledge, the strengths of the U.S. industry, can improve the supply chain between the United States and a Southern Hemisphere trading/manufacturing partner.Product economies gradually evolve to service economies. Using capital creatively, the United States should convert some equities, knowledge particularly, into service activities. U.S. industry can use its expertise in distribution to attack the all-too-long apparel supply chain. Put the weave shed in Peru next to a dye house, export across the land bridge of Central America or through the labor economies of the CBI region, employ and ultimately sell to a new customer. This adds service to the equation, takes the U.S. textile industry beyond a pure manufacturing mentality, and makes it competitive and a survivor.Editors Note: John E. Luke is owner of Five Twenty Six Associates Inc., Bryn Mawr, Pa., a consulting firm specializing in strategic marketing and operations facing textile fiber and fabric manufacturers. He is also a professor of textile marketing at Philadelphia University, Philadelphia.March 2002
Nano-Tex Launches NANO-TOUCH Technology
Nano-Tex LaunchesNano-Touch TechnologyNano-Tex LLC, Greensboro, N.C., a subsidiary of Burlington Industries, has introduced the fourth of its nanotechnology-based textile products. NANO-TOUCH fabric technology enhances fabrics by grafting an outer layer of cotton-like attributes to a man-made fiber core, adding cottons softness, comfort and matte finish to the durability, strength, colorfastness and crease retention inherent in the man-made fibers.Working at the molecular level, the new technology eliminates the need for traditional spinning processes or blended fibers and fabrics, according to Nano-Tex. Our proprietary technology is engineering fabrics that create advanced performance sustainable through the life of the fabric, said George W. Henderson, CEO. Scientists in our research and development center are pioneering new ground with cutting-edge applications of nanotechnology to textiles, creating a pipeline of future innovations.Burlington is producing NANO-TOUCH-enhanced fabrics under exclusive license from Nano-Tex. The fabrics are being shown to customers and are available for immediate sale.March 2002