Kellwood InitiatesGerber Offer, To Supply Casual MaleSt. Louis-based Kellwood Co. is proceeding with plans to acquire Greenville, S.C.-based Gerber Childrenswear Inc. Kellwood subsidiary Cradle Inc. has commenced an offer to exchange any and all outstanding shares of Gerber common stock for cash and Kellwood common stock. In addition to marketing infant and toddler apparel and related products, Gerber Childrenswear owns Auburn Hosiery Mills Inc., Auburn, Ky., and Sport Socks Co. Ltd., Ireland.Edward Kittredge, chairman, president and CEO of Gerber Childrenswear, will continue to head the company, reporting to Robert C. Skinner, corporate vice president of Kellwood.In other news, Kellwood has signed a contract to supply mens sportswear, activewear and furnishings to Designs Inc., new owner of Casual Male Corp. Total purchases over the seven-year term should exceed $400 million, with first shipments targeted for Spring 2003.July 2002
Charles A Hayes Dies At Age 68
Charles A. (Chuck) Hayes, chairman of Guilford Mills, Greensboro, N.C., and president of the
American Textile Manufacturers Institute (ATMI), Washington, for the 2001-2002 term, died Sunday,
July 22 in Myrtle Beach, S.C. He was 68.Hayes turned the one-plant Guilford operation into a
dominant force in the textile industry during his tenure as CEO from 1971-1999. The company earned
a spot on the Fortune 500 in 1988.As the first knitter in the ATMIs history to be elected
president, Hayes sought to bring a united front to the organization, giving all sectors of the
textile industry a unified voice.In addition to his professional accomplishments, Hayes was also a
philanthropist, donating time and money to literacy causes. Hayes served on the University of North
Carolina – Greensboro Board of Trustees from 1980-1991, serving as chairman for six years. He
pledged $666,666 to the school to endow a professorship at the School of Education.
Import Problems Persist
I
nternational trade concerns — both short-term and over the longer pull — continue to
plague mills. Looking at the current year’s outlook first, all signs point to an increase in
incoming shipments — reversing the small, recession-induced slippage noted last year.
To be sure, there are some restraints that will limit any advance, including: the lobbying
efforts of the new American Textile Trade Action Coalition (ATTAC); and expectations of a somewhat
weaker dollar, which could soon make imports more costly. Nevertheless, improving U.S. consumer’s
demand should outweigh these positives and make some import gain inevitable.
How much gain? At this point in time, our projections suggest about a 3- to 5- percent
textile and apparel increase on a square meters equivalent (sme) basis. Not good, but a lot better
than the steady tattoo of double digit advances that prevailed as recently as 2000.
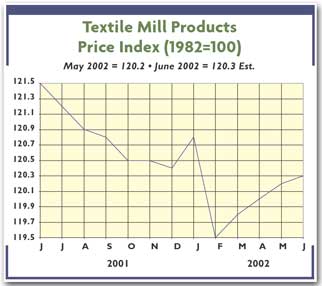
China: A Long-Range Question Mark
But of even bigger concern is the question of what happens in early 2005, when virtually all
quotas are eliminated for World Trade Organization (WTO) countries.
One fear is that China (already the top and fastest growing exporter to the United States)
will at that time become an even more potent competitor of low-cost, high-quality textiles and
apparel.
Point to keep in mind: China’s expertise and manufacturing sophistication already equals or
even tops that of other exporters in both Latin America and the Far East. Upshot: More big changes
in trade flows are inevitable.
Some Indications Of A Turnaround
On a somewhat more optimistic note, there’s a growing consensus that recent declines in
domestic mill output are over. The feeling is that totals are likely to hold near current levels
for the next few years.
Indeed, there are already signs of some bottoming out. Textile purchasing executives now say
they are experiencing increases in both new orders and shipments. Equally significant is the jump
in the textile mill workweek — from 40.3 hours a year ago to 42.1 currently. And, as pointed out in
previous columns, the textile inventory glut continues to fall significantly — making it
increasingly likely that new orders will be quickly translated into new production.
Zero in on individual fabrics, and the picture is also looking somewhat brighter. Thus
denim, after a very poor second half in 2001, is again moving well — helped by a growing number of
new fabric finishes. Khaki is also making a comeback with novelty looks, better quality and new
stain-resistant qualities. Dress shirt fabrics are perking up, too — as the trend toward “dressing
up” intensifies.
More Thoughts On Costs
A new DRI-WEFA study on costs also has to be regarded as quite encouraging. The big
econometric consulting firm, taking a look at the textile mill industry, finds that input costs
(including both services and materials) is now lagging year-ago levels by a percentage point or
two.
Much of this is due to the very modest labor hikes, which are now more than being offset by
productivity gains. And the picture is much the same for materials where cotton weakness has more
than compensated for some recent pickup in polyester quotes.
Moreover, all this good news is projected to continue. To be sure, the DRI-WEFA study does
see an end to cost declines.
On the other hand, its new forecast is still basically upbeat — calling for only about a
1-percent-or-so annual increase in material and service costs over the next year and a half.
A Closer Look At Overall Demand
A slowly strengthening economy would also seem to bode well for the industry. Current
consensus calls for about 3-percent GDP growth at the annual rate over the next few quarters.
This, in turn, should help make for similar rises in consumer incomes and spending levels.
Aiding gains will be such additional fillips as little or no price inflation, continuing low
interest rates, and a still-booming housing market. The latter not only is feeding demand for home
furnishings, but is also allowing homeowners to tap into home equity for spending.
Lastly, this robust home market is keeping household net worth at or near peak levels
despite a still-weak stock market.
Factor these pluses into the textile equation, and it may well explain some of the cautious
optimism being voiced by industry analysts and executives.
July 2002
Rutland Celebrates 40th Anniversary
Rutland Celebrates 40th AnniversaryRutland Plastics Technologies Inc. recently celebrated 40 years of providing plastisols to the screen-printing industry. The company, based in Pineville, N.C., is ISO-9001- and QS-9000-accredited. Products produced by Rutland include inks for Pantone® color matching; complete ranges of inks for cotton and cotton/polyester blends; low-temperature curing inks for nylons, spandex and reflectives; specialty inks; and industrial and automotive PVC compounds.July 2002
Congressmen Urge Support For Textiles
Forty members of the U.S. House of Representatives have signed a Joint Resolution urging the Bush
Administration to protect the interest of the U.S. textile industry in dealing with international
trade issues. The resolution is not binding, but is designed to show congressional concern over the
damage international trade is doing and could continue to do in the future. Primary sponsors were
Rep. Howard Coble (R-NC) and John Spratt (D-SC) , leaders of the Congressional Textile Caucus.The
resolution urges President Bush and officials in his administration to: ensure vigorous enforcement
of U.S. trade laws “using all remedies available under those laws;” ensure vigorous enforcement of
existing trade agreements, including the North American Free Trade Agreements and agreements under
the World Trade Organization, take steps necessary to circumvent illegal transshipments; deny
requests from trading nations to change existing trade agreements; and implement strategies to open
foreign markets to U.S. textile and apparel exports.The resolution calls on the President to submit
to Congress annual reports on the ability of the U.S. textile industry to compete with the textile
industries in other countries, and it also addresses one of the U.S. industrys major current
concerns, the fact that devalued currencies are making imports cheaper than ever, and undermining
export markets. It directs the President to take into consideration the effect of devalued
currencies in any future trade negotiations. It says that nations should not receive tariff
concession at times when they are benefiting from devalued currencies.The preamble to the
resolution cites the “serious injury” to the textile industry stemming from its international trade
problems, including job losses, plant closings and loss of markets both at home and overseas.By
James A. Morrissey, Washington Correspondent
Volume Continues Upward, Margins Tight
T
hat seems to be a common theme among most respondents — volume continues to increase, but
margins are very tight. “Things are going pretty darn good right now,” said a spinner. “Margins are
tough, but that is to be expected. It seems that whenever you have gone through a trough or low in
the economic cycle, volume comes back before margins. So I would expect margins to be on the way
back, soon. When? I don’t know, but the sooner the better for some of us.”
Another spinner responded, “We are busier than we have been in over a year. But you must
remember that we are a different company. We have fewer plants and fewer people; a lot of things
have changed. But we are working flat out. Margins are tight. We are trying to cover increases in
raw materials cost, so we are getting closer to our asking price.”
Margins are back for some. A yarn buyer said, “I have heard that margins are tight for
spinners, but I know that business is very good for some. In fact, it has become so good that two
spinners turned down orders during the past couple of weeks. Prices for some of the yarns that I am
buying were up 4 to 6 percent in the past few weeks.”
Retailers
We have heard much about the Wal-Mart/KMart mentality in recent months — the way they search
the globe looking for the best possible price. Textile manufacturers are quick to say that
retailers and their global sourcing is part of the reason for what has happened to the textile
industry. These retailers have no loyalty to or for American-made products. And we all agree this
is probably true.
This searching the globe for the best possible price is not unique to Wal-Mart and KMart
types. It is also a strategy for the privately owned local retailers around the country. A visit
was recently made to a favorite retailer that has been in business for many decades.
While shopping and browsing, Yarn Market studied a large number of garment tags. Results of
this survey were somewhat surprising. In the menswear area, the line for one of golf’s favorite
players was featured.
These beautiful golf shirts ranged in price from $70 to $100. Would you like to guess the
country of origin on the label? Well, if you guessed Indonesia, India, the Philippines, Korea or
Malaysia you would be right. Put them back!!!
From the Internet — an article about American Airlines indicates the company is getting new
uniforms. So, it is only natural to ask, where were these uniforms made? After several calls to
various American Airlines offices, Yarn Market found they were “Made in the USA.” Sounds like
something positive for American Airlines. Maybe this is an opportunity for the textile industry to
support one of its customers — fly American.
Raw Material Prices Moving Up
Quotation for the base quality of cotton (color 41, leaf 4, staple 34, micronaire 3.5 to 3.6
and 4.3 to 4.9, strength 26.5 to 28.4, uniformity 81) in the seven designated markets averaged
33.64 cents per pound — up from the 29.43 cents per pound reported last month, and down from 49.19
reported for the corresponding week a year ago.
Polyester prices moved up to 55 cents per pound (1.5 denier) —up from the 53 cents reported
last month and down from the 60 cents reported for the corresponding week last year. Most
indications are that fiber demands are increasing. Mills are beginning to show more interest in the
2002 cotton crop, so prices may continue to edge up.
Yarn Price Comparison
Recently, while surfing the Internet, Yarn Market found an article from Pakistan. Listed in
a table were prices for carded and combed 100-percent cotton ring-spun (RS) yarns f.o.b. Karachi. A
comparison of these prices with U.S. prices shown on the facing page is very interesting.
For 10/1-carded RS 100-percent cotton yarn, the Karachi price is 37 cents per pound less,
$0.73 as compared to $1.10. For 24/1 and 30/1 carded RS 100-percent cotton yarns, the Karachi
prices are 48 and 50 cents per pound less, respectively. For combed RS 100-percent cotton yarns,
the differences are similar.
Shipping would add 5 to 10 cents per pound depending on the size of orders. Why is there
such a difference? Cheap labor is one reason.
July 2002
Gore To Establish Operations In China
Gore To EstablishOperations In ChinaIn an effort to expand the companys manufacturing capabilities,
W.L. GoreandAssociates Inc., Newark, Del., will establish a fabrics-manufacturing operation in
China.The new facility, located near Hong Kong, will begin production of Gore-Tex® fabrics for both
the regional and export markets in 2003. Thirty to 50 positions are expected to be filled by the
end of 2002.Asia has emerged as a formidable textile supply and innovation center, said Terri
Kelly, fabrics business leader. This region also presents significant market opportunities. We are
very excited about the global supply chain flexibility and international market potential that
operations on three continents will provide.The company has operations in Europe, North America and
the Asia Pacific region.
July 2002
Tweave Offers New Stretch Woven Fabrics For Intimates
Tweave Offers NewStretch Woven Fabrics For IntimatesTweave Inc., Norton, Mass., has added two new styles, 528 and 529, to its Durastretch® line of stretch woven fabrics for intimate apparel. Tweave claims woven constructions allow spandex to move more freely, providing superior recovery and memory, as well as improved fit and contouring with less bulk, when compared with knit constructions.July 2002
DuPont Ink Jet Ichinose Offer Digital Printing System
DuPont Ink Jet, IchinoseOffer Digital Printing SystemWilmington, Del.-based DuPont Ink Jet and Japan-based Ichinose Toshin Kogyo Co. Ltd. presented a new digital textile printing system at the Japan International Apparel Machinery 2002 Trade Show. It is the first fully integrated, production-capable, digital textile printing solution for the apparel industry, according to the companies.DuPonts Artistri Color Control and Management System software allows designs of all types to be printed directly from the computer, while the Artistri 700 Ink Series is available in shades for reactive dye, acid dye, and disperse dye and pigment.The Ichinose 2020 roll-to-roll printing system is equipped with fabric transport technology that allows printing on wovens and knits, including stretch fabrics. The system will be commercially available in the fall.July 2002
It39 S In The Jeans
By Virginia S. Borland, New York Correspondent It’s In The JeansMeeting market demands and fashion needs, manufacturers are developing denim using new fiber blends, weights and finishes. From workwear to business attire, denim is the fabric of choice. Its in almost everything pants, skirts, dresses, jackets, accessories, even eveningwear and products for the home.The phenomenal growth of denim has been gradual and global, and does not appear to have reached its peak. What is new is the variety of denim fabrics in the marketplace. Just when you think nothing else can happen to denim, it turns up in new weights and fiber blends, with new finishes and application treatments.The French lay claim to inventing denim and believe the word is an English adaptation of “serge de Nimes,” a fabric woven in the French city of Nimes in the 16th century.Italy takes responsibility for the creation of jeans, a word derived from Genoese and referring to cotton twill trousers worn by sailors in Genoa. The popularity of denim jeans started in the l9th century in America with Levi Strauss.
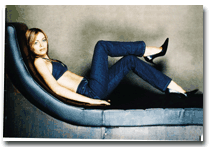
Denim made from Irish linen and Lycra® offers stretch properties, easy care and a soft hand, according to Masters of Linen. Denim Is AuthenticKeith Hull, president, Marketing and Sales, Avondale Mills, Monroe, Ga., said, Denim is popular because it is comfortable, it looks good and it is versatile. Part of its current success is a reaction to 9/11 and a direction to back-to-basics. Denim is authentic.John Heldrich, president and CEO, Swift Denim, Columbus, Ga., agrees: Denim is a cradle-to-grave product. It is the best and most versatile global fabric. It can take on so many different looks through yarns, construction and laundering.Mike Moody, executive vice president and general product manager, cotton apparel, Burlington WorldWide Ltd., Greensboro, N.C., attributes denims popularity to casual dress in the workplace. Denim is both fashion- and performance-driven, he said.Universally, denim weavers agree that the core business is the five pocket jean, made in 10- to 12-ounce 100-percent cotton that is ring-spun and indigo-dyed. Approximately two-thirds of all denim apparel purchased in 2001 was jeanswear.Basic denim is always there, said Livingston, but today it has many different characteristics and different touches.Denim mills are sold up well into the third quarter of the year. Today, our biggest problem, said Hull, is meeting the demand.Avondale weaves between 80 and 100 different denim fabrics. Darker blue shades are popular; black has become a staple. There are softer finishes, shiny surfaces and flatter looks. Even rigid denim has a soft touch, said Hull.Avondale works in partnership with its customers to develop special looks. Currently, the direction is to lighter weights, softer finishes and casts of indigo. Some of the popular jeans cuts include cargos, low rises and carpenters. Other apparel categories include skirts and jackets. Other end-uses include curtains and slipcovers. Jack Mathews, vice president, fabric sales and marketing, American Cotton Growers (ACG), Littlefield, Texas, said, Denim is in a strong fashion cycle. The basics are selling, but fashion denims that have texture and character are what is in demand. Some of the new garment washes and finishes are also helping to drive this business.Other factors Mathews cited for the renewed popularity of denim are low retail inventories after Christmas and mill closings.
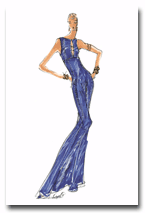
Denim eveningwear designed by Christian David Kozaki for Les Belles Choses. Photograph courtesy of Cotton Incorporated. ACGs business is focused on jeanswear. Most of the line is 100-percent cotton, open-end, faux ring-spun and ring-spun denims. All fabrics are indigo-dyed. Mathews noted a new blue/black shade called Raven is popular. New styles containing Lycra® are in development. Mathews sees denim sales continuing strongly through the end of the year, with no slowdown in sight until the first quarter of 2003. The biggest challenge is to get the price up, he said. In bad times, prices fall in quarters; in good times, they go up by nickels. Service And Price Drive The BusinessService and price are what drive the business, said Monte Galbraith, vice president, sales and marketing, Denim North America (DNA), Columbus, Ga. We will never be the lowest price, but we do offer the best service. What the domestic market has going for it is proximity and speed to market. We can work with customers on a daily basis to develop new products.DNA came on-line May 1, taking over Marubenis state-of-the-art four-year-old plant (See News, TW, this issue). The bulk of its production is ring-spun cotton denim in the 10- to 12-ounce range. Fabrics can go as light as 7 ounces.With fashion silhouettes cleaning up and becoming sleeker, Galbraith said there is a lot of talk about color, but all casts of blue will always be available. A black shade called Asphalt is selling in every construction. In addition to all-cotton, DNA is weaving cotton/Lycra and cotton/polyester, and is developing a variety of stretch products.Ring-spuns, stretch and lighter weights are popular at Swift. Customers are still looking for denims with a vintage-look, flat and worn appearance, Heldrich said. Our basic Hard Core Blues continues to be a best seller.Along with apparel, Swift denims are in comforters, belts, hats, log carriers and dog beds. Denim will always be in fashion, Heldrich said. Sometimes the fashion cycle is stronger. As long as we focus on being innovative and provide good value around the world, we will continue to be successful.” S-t-r-e-t-c-hAlthough the majority of Burlingtons line is 100-percent cotton, stretch denim is one of the fastest-growing segments of its business. The company is weaving blends with both Lycra and DuPonts T-400. Polyester blends are there for strength. Moody also mentioned that black denim is having a resurgence.He also noted that most of Burlingtons customers are using more sophisticated wet processing such as sand-blasting. Sometimes a garment will go through several different treatments. Burlington is working on new technologies to give denim fabrics different looks when processed.At Cone Mills, Kara Nicholas, director, new product development, specialty stores, said, We have developed a lot of new blue shades. We are getting a good reaction to some of the clear blues and lighter colors.Were past the idea of basic denim, she continued. As long as we innovate and keep coming out with something new, we will find a fashion customer. Stretch is one area of innovation. Cone is developing lighter-weight, stretch denim fabrics with spandex and with polyester for comfort stretch. The company also is experimenting with new cotton yarns to give different looks to denim. Stretch denim has been popular in Europe for more than a decade. In the United States, it is selling strongly in juniors and is beginning to be accepted by other age, gender and ethnic groups. According to Livingston, stretch is adding another dimension: it provides comfort, shape and fit. Cotton Incorporated is working on development of 100-percent cotton stretch denim by using finishes and treatments.
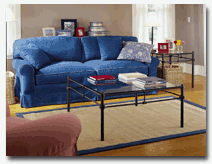
Eddie Bauer Home is using denim for home furnishings.Photograph courtesy of Cotton Incorporated. Most of the stretch denim sold in the world today contains an elastomeric fiber. DuPont Textiles and Interiors (DTI) is promoting stretch denim containing Lycra at high-fashion and mass-market levels, from Armani to Levis. Recently, DuPont participated in New Yorks Fashion Week in a joint show featuring stretch denim apparel created by six designers/brands.Another DuPont product that can provide comfort stretch to denim is T-400. It is chlorine-resistant and can withstand a variety of bleaching and washing conditions such as sandblasting, whisker washing and antique finishes. For more tailored looks, T-400 will retain trouser creases after washing.In partnership with Velonorte Mills of Brazil, DuPont has created a knitted stretch denim called Veloflex®. Containing 96-percent cotton and 4-percent Lycra, Veloflex denim has been sampled by designers such as Theory, BCBG, DDC Lab, Hippie Jeans, Adriano Goldschmied and Melanie Apple. The fabric has a soft hand, is supple and enables designers to create slim-cut jeans that provide comfort and freedom of movement. Linen And BlendsAlso jumping onto the bandwagon, European linen weavers have developed denim fabrics in a variety of looks and weights. According to Pauline Delli-Carpini, U.S. representative, Masters of Linen, denim woven of linen can be clean, structured and elegant; or rustic and casual. She cites shades of dark cobalt blue and graphite as popular.There are rigid linen denims, cotton blends and stretch with Lycra. The trend is to lighter weights and faded, antique finishes that have an elegant look. All of the linen-content denims are easy-care, and many are pre-washed to give the fabrics a soft hand.In addition to apparel, Delli-Carpini noted that denims of linen are widely used in fabrics for the home. Because of its antistatic properties, linen doesnt attract dust or dirt, so it is especially popular for upholstery, slipcover and drapery fabrics.A lot of European mills are showing denim fabrics and the look of denim with application treatments and embellishments. There are flocked, embroidered and coated surfaces; reversibles; sheers that are printed to look like denim; indigo-dyed jacquards knitted or woven using linen and cotton; laser cut-outs on denim; puckers; matte/sheen patterns; and the ultimate denim-patterned sequins applied to lace (See Premiere Vision Predictions, TW, May 2002). Tencel®Another fiber that is widely used in denim is Tencel®. June Lauck, marketing communications manager, Tencel, said the Belgian firm UCO and Tejidos Royo of Spain are selling Tencel-content denim fabrics. UCO denims are woven using dyed Tencel in the warp, and they have a uniquely soft and silky touch.Lauck pointed out that two reasons for Tencels popularity in denim are its aesthetics and performance. Because of its strength, Tencel can withstand harsh bleaches, acid washes and finishing treatments, even in lightweight constructions.Denim fabrics containing Tencel have a clean, neat look and natural luster. High levels of stretch can be achieved without the use of elastomeric fibers because of Tencels unique fiber-swelling properties.Enrique Silla of the Spanish firm Jeanologia has created jeans, jackets, skirts and other apparel in Tencel-content denim. Some of the newest looks shown at his most recent presentation were whitened or tinted blue shades. Some had gray or yellow casts. Most of the apparel has movement and excellent stretch and recovery.Will the denim momentum continue Mills are sold up through the third quarter, and denim producers are continuing to come out with new and relevant products. As Galbraith said, At DNA, denim is in our genes.June 2002