Independent Machinery Co., Fairfield, N.J., developed a computerized system for traverse winding
exceptionally long lengths of tension-sensitive materials into large spools. The system features
two-position unwind that can accommodate maximum 36-inch-diameter supply rolls slit to width. The
IMC smartwinders software provides an unlimited range of spool shape, size and winding patterns
easily programmed through a touchscreen. The winding position is cantilevered and has a doffing
feature for easy removal of the large spools.
2000
Computerized Traverse Winder Two-Position Unwind
Idler Master Catalog Features New Expanded Lines
The Idler Master Catalog from Webex, Neenah, Wis., has been expanded. The catalog now includes
FeatherLight Carbon Composite idlers, a new line of rubber-covered de-wrinkling idlers and the
industrys first standard line of heat-transfer rolls.
2000
M-Tec Introduces Finish-Tec
Germany-based M-Tec Maschinen-baugesellschaft Mbh has introduced the finish-tec range for finishing
elastic and synthetic fabrics. The finish-tec range integrates pressing, decatising, setting and
shrinking.Intensive steaming under high surface pressure is the first step, followed by a
steaming/shrinking treatment and, finally, a shock-cooling. This procedure allows a multiplicity of
variants of the fabrics final appearance regarding touch, luster, volume and degree of fixation.
Steam and heat treatments release latent tensions, guaranteeing minimum residual shrinkage values
in the warp and weft.
November 2000
Yarn Market Open-End Yarn Production Decreasing
Yarn MarketBy J. Karl Rudy, Technical Editor
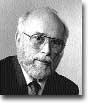
Open-End Yarn Production DecreasingInitial reports from respondents in the cotton field
indicate that, while the crop this year will be large, the quality of the crop has deteriorated.
Drought conditions have ad-versely affected staple length, causing the fiber to be shorter.
Micronaire has also been hit. Rain late in the season will cause a spotted condition that will also
affect unharvested crop quality. Classing for the season has started, with about 10 percent of the
crop checked. Of course, when the irrigated crop starts coming in, crop quality will
improve.Spinners report additional movement in open-end (OE) spinning to reduce overall weekly
production of over a million pounds through closings, mergers and buyouts. They also say that
weavers in vertical operations have begun buying their OE cotton needs or replacing them with
ring-spun yarns, accounting for another million pounds or so weekly. As a result, spinners are
expecting early relief in the pricing situation that has plagued them for so long. Cotton prices
continue to move up, though, which puts a further strain on an already depressed bottom
line.Several respondents to the Yarn Market commented on this situation by saying, Pricing will
improve in 2001. It has to or retailers will not be able to purchase domestic yarn spinners will be
out of business. The follow-up comment to this is something to the effect that retailers care only
about their own bottom line, especially the large-scale merchandisers. Another spinner said, With
cotton up about 13 cents, pricing will have to go up!Volume for most OE spinners continues to be
good but they expect further improvement during the first quarter of 2001. Now, how about that
improvements in both pricing AND volume in 2001!One spinner, reminiscing about the good old days,
said, When I first started , a 10/1 cotton yarn sold for 56 cents a pound. Cotton was a constant 25
or 26 cents. And this was all ring-spun yarn. Some of us can remember when cotton sold for less
than 20 cents a pound and, if you go back far enough, you could buy a cord of wood for $1. But who
wants to go back to outdoor privies and no running waterRing-spun yarn markets are reported to be
very, very, very strong. Others confirm this market is very tight, as it has been for months. Mills
are running wide open and shipping all they make. On occasion they ship more than they make. That
should tell you something!Weaving has slowed in recent weeks, as confirmed by a weaver respondent.
Optimism still prevails, however, and weavers expect the slow-down to be of short duration.
Apparently, the problem is predominately with the apparel side of the market. Could this be due to
retail inventory, mentioned a few months ago by a spinner Last month, Yarn Mar-ket reported a
texturizers comment about a rumor to this effect concerning bottom-weight goods. For your
information this weaver is in bottom-weight apparel production.Synthetic markets are awful, as one
spinner put it. He also said, No area we sell would I consider robust all are weak! We hear it
might be due to inventory at retail but I dont really know. Even home furnishings, which is
normally pretty strong, suddenly became weak. We have curtailed from six- to five-day operations to
control inventory. Im surprised at the markets being so quiet it usually doesnt happen during an
election year. This will be a weak quarter, but I expect it will pick up by mid-January. He also
commented that he was optimistic about the Caribbean Basin Initiative but was discouraged with the
small number of attendees from that area at a recent conference.Trade Versus Fair TradeThe trade
agreement with China is on everyones mind not from the sense of whether we should have one, because
most consider it a done deal, but, rather, whether it will be a fair trade agreement, one that will
have enough safeguards to prevent abuses, with penalties severe enough to discourage unfair
practices. Farmers are, of course, most supportive of the agreement, but we need to remind our
politicians that agriculture is not the only industry concerned here. Even so fair is fair
regardless of the industry involved.To leave you with a thought for the day With the price of gas
running $25 for a tank, will consumers buy a $25 shirt they dont need just because they like the
color
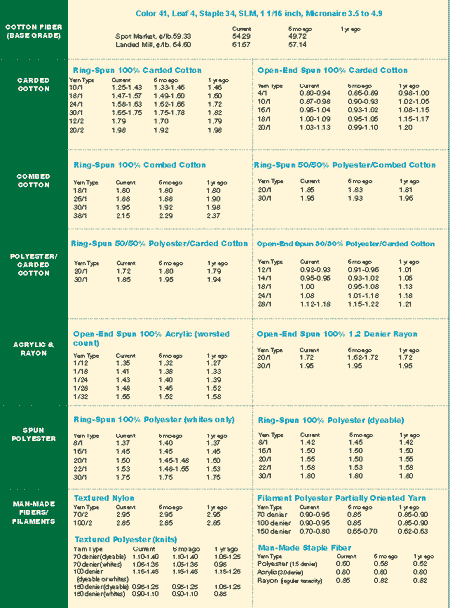
November 2000
Milliken Headquarters Receives OSHA Recognition
The Roger Milliken Center, Spartanburg, S.C.-based MillikenandCompanys corporate headquarters, has
become the companys 46th VPP STAR Site. The designation is awarded by the U.S. Department of Labor
Occupational Safety and Health Administration (OSHA) Voluntary Protection Program (VPP) through the
S.C. Department of Labor, Licensing and Regulation, Palmetto VPP. The VPP program recognizes
companies that surpass normal safety requirements to meet and exceed OSHA standards. Since Milliken
began participating in the program in 1992, 45 of its manufacturing locations have been given the
VPP STAR Site designation.This is tremendous recognition, said Roger Milliken, chairman and CEO. It
is a tribute to every associate in our company, because every associate knows that they have
ownership of the safety process. [VPP] is not a management program.The VPP program has been
tremendously successful in helping our company establish an uncompromising safety and health
process, said Richard Dillard, director, public affairs, Milliken and Co. What better gift can you
give your associates and the community, than a safe working environmentMilliken has the most VPP
STAR sites of any company in South Carolina (28 of a total of 35) and also tops the list in every
other state where it operates, according to Wayne Punch, director, safety and health. It is second
nationwide only to International Paper.Janet Nixon, Palmetto STAR VPP coordinator, points to
Milliken when other companies complain that the VPP standards are set too high. [Millikens] record
speaks for itself, she said. They are one of our strongest advocates for the program.Remarking on
the attainment of VPP STAR Site status for the companys headquarters, Punch said, It has been quite
a challenge. This is our largest facility, and that just makes success that much sweeter.
November 2000
GE Plastics Buys NetProfiler From GretagMacbeth
GE Plastics, Pittsfield, Mass., has purchased 70 NetProfiler B2B, Web-enabled instrument management
software systems from GretagMacbeth LLC, New Windsor, N.Y.The purchase was driven to meet GE
Plastics ColorxpressSM corporate objective to maintain and monitor its spectrophotometers and
manage its electronic color standards on a global basis via the Internet. With 70 GE plastics color
resin facilities around the globe (in countries such as the United Kingdom, France and Brazil),
this purchase will enable GE plastics to significantly reduce inter-instrument biases and improve
instrument agreement between all spectrophotometers.
November 2000
New Developments From Rutland Plastic Technologies
Rutland Plastic Technologies, Pineville, N.C., has introduced three new products.HS Series inks are
formulated as economical press-ready plastisols for hot-split transfer applications on 100-percent
cotton and 50-percent polyester/50-percent cotton white fabrics.For printing on polyester/cotton
dark fabrics, Rutland offers a low-bleed plastisol, ML9230 Maximum White. For finely detailed
images, ML9230 can be applied as an underlay white, or it can be printed as a stand-alone white for
maximum whiteness.Complimentary M2000 Pantone-approved software will optimize the use of pre-mixed
inks and control production costs. M2000 can improve quality by allowing for the precise mixing of
more than 2,000 colors.Rutland has also announced a distribution agreement with Atlanta-based
Freedom Imaging Solutions. The agreement will provide distribution of Rutlands plastisol screen
line in the territories covered by Freedom.
October 2000
Texel Inc Plans Nonwovens Expansion In Canada
Texel Inc., a unit of technical nonwoven and composite materials company ADS, Canada, is planning a
large expansion of its nonwovens capacity.Texel will install state-of-the-art capacity to make as
much as 12,000 tons of advanced spunlaced nonwoven fabrics. Its technology will produce a variety
of differentiated spunlaced nonwovens. The company will be the only producer of spunlaced in
Canada.Simultaneously, Texel will invest to expand its technical needlepunched nonwovens capacity.
October 2000
Brilliant Scarlet From Dystar
Germany-based Dystar has added a new high-performance reactive dye to its Levafix® CA range. The
new dye, Levafix Scarlet CA, is suitable for all processes on cellulosic fibers. It can be combined
with both Levafix and Remazol® dyes to produce a wide range of colors. The dye is AOX- and
metal-free. According to Dystar, the dye has excellent washoff properties, high fastness to
repeated wash cycles and good fastness to light and chlorine.
October 2000
Bayer To Acquire Sybron
Bayer Corp., Pittsburgh, Pa., and its wholly owned subsidiary, Project Toledo Acquisition Corp.,
have entered into a definitive agreement with Sybron Chemicals Inc., Birmingham, N.J., to acquire
all of Sybrons outstanding shares at $35 per share, payable in cash. Any shares not purchased in
the tender offer will be exchanged for cash in the amount of $35 per share in a merger of Sybron
and Project Toledo Acquisition Corp. The acquisition is subject to approvals from regulatory
authorities in the United States and in Europe as well as other customary conditions.This
acquisition will provide Bayers Coatings and Colorants Business Group (Polymers segment) and
Special Products Business Group (Chemicals segment) with access to new technologies and products
and will enable them to expand their market positions in the NAFTA region. “Sybron Chemicals Inc.
offers us an excellent opportunity to strategically augment and strengthen important business
sectors and thus continue to enhance the value of our business” said Dr. Manfred Schneider,
chairman, Bayer Management Board.
October 2000