NEWTON, N.C., Jan. 25 /PRNewswire/ — On Friday January 19, 2001 Ridgeview entered into a letter of
intent with Great American Knitting Mills to sell certain assets, including the Ridgeview name and
other trademarks. The intent of the proposed transaction is to continue Ridgeview’s sport sock
business inthe sporting goods market and to provide the resources necessary to build thebrand going
forward. The agreement has a closing date of February 1, 2001. Ridgeview continues to operate and
meet its customers’ needs at the present time. Both companiesexpect the transition to be a smooth
one for Ridgeview’s customers. It isun clear at this point exactly what the transaction will mean
to Ridgeview’s operations. Hugh Gaither, President and CEO of Ridgeview, said, “the transaction
provides an opportunity for our Ridgeview sport sock business tocontinue in the market place.” Jim
Williams, President and CEO of Great American Knitting Mills added, “We are excited about this new
business opportunity and very encouraged by informal customer reaction to the business
combination.”SOURCE Ridgeview, Inc.Copyright 2001 PR Newswire
Great American Knitting Mills To Acquire Certain Ridgeview Assets
ITMA 2003 News
New eight-day format: Circular knitting machinery WILL be shown The first ITMA of the 21st Century
will set a precedent: it will be staged over 8 days, instead of the traditional 10.Organisers of
ITMA 2003, to be held at The National Exhibition Centre (NEC), Birmingham, England, have announced
that the show will run from October 22 to 29 inclusive. The shorter duration is in response to
feedback from both exhibitors and visitors, who want to cut down on expenditure and reduce the
out-of-office time commitment for key personnel.Another vital boost for ITMA 2003 comes with the
news that the leading circular knitting machinery manufacturers have confirmed that they WILL take
part in ITMA 2003, instead of attending another show being organised at the same time in Italy.
Their decision underlines the appeal of ITMA as the world’s premier textile machinery exhibition
for all sectors of the textile industry.Officials at The NEC venue, which will stage ITMA for the
first time in 2003, say they are delighted with these two positive announcements. Maria Avery,
Exhibition Director of the ITMA 2003 Organising Committee at The NEC stated : “Representatives of
several leading knitting machinery companies have visited The NEC recently, and have been impressed
both with the facilities and the cost-effectiveness of the overall package we can offer.”We are
pleased that this has corrected some of the unfair and unfounded criticism that has been stirred up
in some quarters, and we are delighted to welcome circular knitting machine producers as an
important exhibit group.” The NEC and Cematex – the pan-European machinery body which stages the
four-yearly ITMA shows – are also confident that the switch to the more compact, eight-day format,
will be a winner. This decision, which will apply to all future ITMAs, recognises the changing
business environment and the influence of the internet and e-mail.Maria Avery added:
“Overwhelmingly, feedback has confirmed that a 10-day show is too long. We have acted accordingly
and reduced ITMA 2003 to eight days, ensuring that the popular busy weekend is still embraced.
Significantly, eight days ensures that exhibitors do not have their personnel away from the office
for such a long period, while allowing the visitors plenty of time to see all the equipment they
are interested in. The reduced period also means reduced expenditure for both exhibitors and
visitors.”ITMA 2003 will occupy some 160,000 square metres of stand space, with an expected total
of 1,400 exhibitors from 40 countries attracting around 150,000 visitors from the world’s textile
industries. Further details can be accessed from the main ITMA website : www.itma.com and from the
dedicated hotel website : www.itmahotels.com, as well as a brand new site, www.itmatravel.com,
focusing on all aspects of transport to and at ITMA 2003.For further information contact – The ITMA
2003 Organising CommitteeThe NEC Birmingham B40 1NT England Tel – +44 121 780 2003Fax – +44 121 782
2003 email – info@itma2003.comwww.itma.com
ATME-I 2000 Exhibitor Overview
of the companies that exhibited at the American Textile Machinery Exhibition-International 2000
(ATME-I). Obviously, space does not allow a comprehensive review of every display. ATI selected a
representative list of companies to interview in order to provide its readers with a feel for the
offerings at the exhibition. Some major exhibitors are not listed here, such as Rieter, Suessen,
Saco Lowell and Murata; they will be covered in a separate article about spinning technology to
appear in next months issue. Other companies Dilo and Fleissner, for example will be covered in an
upcoming nonwovens roundup. Barmag AG/Saurer Group, Germany/Switzerland (American Barmag Corp.,
Charlotte, N.C.), presented for the first time the new Automatic Winder babyASW. This winder, which
will be used primarily for technical yarns, specifically targets the markets of Mexico and South
America. The dimensions of the babyASW are much smaller than those of the regular ASW winder. It
features a camshaft traverse system, a string-up device with package protection function and a
counter for current yarn capturing. Options include machine frame and unheated godets, yarn sensors
and yarn cutters, spin-finish and intermingling equipment, and a cradle.Belmont Textile Machinery
Company, Mount Holly, N.C., exhibited its new EW1000 winder for the carpet industry. By means of a
new traverse cam-and-dog assembly, winding speeds of up to 1,100 meters per minute (m/min) can be
achieved. A new overfeed system guarantees perfect tension control independent of speed and fiber
type. The EW-1000 is compact and features a modular design that is expandable up to 72 spindles in
12-spindle increments. An electronic touch-screen panel regulates winding speeds, displays
production efficiency and monitors winder operating parameters.The company also showed the new
Rototwist yarn twister that produces 2-, 3-, 4-, 5-, or 6-ply yarns in one pass. It is designed for
continuous operation to run up to 600 m/min, and it offers the feature of alternating S+Z twists
that are carefully tacked through a servo-controlled air jet. The machine can be installed in line
with existing heat-setting equipment, or as a stand-alone Rototwist system. Belmont Textile
Machinery also presented a new prototype of a package knotter and placement robot that was designed
for auto-doff winders.CMD Systems, Charlotte, N.C., provides consulting services to textile
manufacturing and distribution organizations in computerized Enterprise Resource Planing (ERP)
systems. The company assists small and large textile and apparel manufacturers and distributors in
the selection, design/ modification and implementation of software and hardware for ERP and supply
chain management systems.Datatex USA, Alpharetta, Ga., a supplier of specialized ERP systems for
the textile and apparel industries, featured its Textile Integrated Management (TIM) software for
network-oriented applications in AS/400 environments. Datatex announced that, to date, it has
implemented 250 systems in large- and medium-sized textile manufacturing plants in 30 countries.
Datatex provides software modules, designed specifically for the modern textile mills, for sales,
manufacturing, planning, and inventory and purchasing. Datatex claims its software will optimize
the use of manufacturing resources, continuously monitor contribution margins, provide basic
quick-response capabilities, improve customer service, reduce waste and reduce work-in-process and
finished goods inventories.
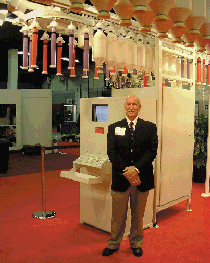
Electro-Jet S.A., Spain (PSP Marketing, Charlotte N.C.), introduced the new Roving Bobbin
Stripper for spinning installations. The machine uses compressed air to open and remove remaining
fiber and roving pieces from the bobbins. Since this is a modular system, there can be from one to
as many as required stripper heads installed. The system consists of the TAB-System for roving
bobbin transport, and the TAC-System for bobbin transfer. Fiber-optics sensors ensure all material
is removed, and other special sensors detect any misalignment to avoid damages that could be done
to the bobbins or the bobbin hangers. After the cleaning process, the bobbins are automatically
integrated into the clean roving bobbin supply.Electro-Jet exhibited for the first time in the
United States a manual system for ring-spinning bobbin cleaning, model MLB. An automatic version is
available that consists of a CT sorting unit; the MLB cleaning machine; and a JET-1, JET-2, or
JET-3 laying machine. The system works with any kind of bobbin without specific adjustments.
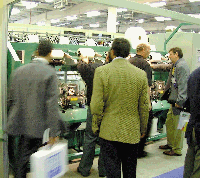
Fehrer AG, Spinning Machinery Division, Austria (Symtech Inc., Spartanburg, S.C.), promoted
its DREF 2000 friction-spinning machine with extended yarn applications. The machine expands the
scope of yarn-friction spinning in the medium-yarn-count range and the coarse count range. The
machine shown at ATME-I produced yarns for secondary carpet backings, filter cartridges, blankets,
cleaning rags and mops, and FR fabrics. The use of synthetic fiber waste materials was demonstrated
for use in combination with yarns for blankets, upholstery, filler yarns for ropes, carpets and
many other applications. FranklandThomas Inc., Greenville, S.C., a long-time supplier of
Nippon Nozzle Co. Ltd. spinnerets and manmade-fiber spinning accessories, has added Sue® Seki
separator rolls, HSGM heat cutters and Seydel stretch tow breakers to its offerings.Heberlein Fiber
Technology Inc., Switzerland (Heberlein North America Inc., Greenville, S.C.), exhibited a wide
range of its components for processing and finishing of synthetic yarns. The company builds core
elements for synthetic-fiber spinning machines. This includes high-performance interlacing jets
that enable todays high-process speeds in spinning, drawing and false-twist texturing. Heberlein
also offers air-texturing jets for the production of Taslan® textured yarns with spun yarn
character, at speeds of up to 1,000 m/min. The company offers friction discs made of special
materials that guarantee durability and a long life span at high texturing speeds.IKOS Inc.,
Charlotte, N.C., develops software for ERP and consults on the installation/implementation of its
software in a manufacturing environment. The company featured its Locator® software that gives
manufacturers a competitive edge in warehouse management through production automation, reduced
workforce, reduced rework, just-in-time (JIT) management, real-time information, Internet
connectivity, B2B communications and inventory accuracy. Additionally, IKOS demonstrated its
Resource Management Solution, software assisting management in resource allocation decisions; IKOS
Scheduler; and IKOS Logger all of which permit management to manipulate the schedule for and track
the material flow through a product or project management situation. Industrial Air Inc.,
Greensboro, N.C., presented filtration systems ranging from integrated air systems to air washers;
fiber and waste separators; custom HVAC systems; and bag, drum and roll filters. Among the newest
offerings from Industrial Air is the S series drum filter, which is constructed of steel perforated
panels bolted together to form a cylindrical, horizontal rotating drum. The arrangement allows even
air distribution across the fabric-filtering media. When bolted together in multiple sections,
these panels form a rigid cylindrical truss member that eliminates the need for a continuous center
support shaft, thus facilitating maintenance. The drum is cleaned by a series of vacuum nozzles
located on the outside of the cylinder, allowing convenient media inspection.Industrial Air has
also introduced a new Hi-Vac sleeve receiver that has 400 percent more screen area than standard
30-inch flat-screen receivers.J. D. Hollingsworth on Wheels Inc., Greenville, S.C., promoted its
metal clothing wires for opening, carding and yarn-spinning applications. The company claims that
the Mastersteel wire is the longest-wearing wire available for high production cards in 1-meter
(40-inch) width, with good performance for every fiber type. The other wire type, the Enhanced
Point Wire, allows for a wider setting between the doffer and the cylinder on high-production
cards, thereby reducing the risk of facing. It has controlled points that pick up fibers
efficiently from the cylinder and is available in non-serrated and serrated finishes and in a
variety of sizes.Jomar Software Corp., Charlotte, N.C., presented the Web-based e-TPF software that
offers textile-specific applications. It is suitable for controlling textile processes and tracking
from fibers to the finished fabric. The e-TPF software is integrated with JAVA and Web Server
technology. For example, the weaving and knitting systems software is designed for the assignments
of warp/section beams to a knitting or weaving schedule by individual beams, or number of ends. The
system allows warps to be matched by style, number of ends, weight and length. It also supports
process control for the width and length fabrics have to be cut, slit or rolled. The Jomar e-TPF is
available for spinning, warping, weaving and knitting, dyeing, finishing, cut and sew, and
converting processes, among others.

LTG AG, Germany (LTG Inc., Spartanburg, S.C.), showed the improved Versa Drum Filter VDF-16,
which now features 16 larger drums. A further improvement is that the filter medium can be changed
in approximately 15 minutes. All mechanical parts are on the clean side, which makes it easy and
clean to service the filter. The VDF also features continuous-suction cleaning of the internally
loaded filter drums. The capacity is up to 35,000 cubic feet per minute (cfm) for cotton-opening
and carding applications, and 60,000 cfm for general room filtration. The VersaDrum Filter is a
compact filter unit.LTG also had on display a large Tangential Fan that delivers a sheet of air
flow and can be used in a large variety of applications such as heating, cooling and drying, with
an even air flow over large surface areas.LTG promoted once again its diffuser systems type WDA/WDB
for direct conditioning of weaving machines. Company officials said the system is simple and,
therefore, very competitive in relation to installation and operating costs. A few months ago, LTG
Inc. changed its philosophy to turn away from providing complete turnkey projects in the United
States. The company now offers its technology to other vendors and fulfills orders for
customer-installed equipment.
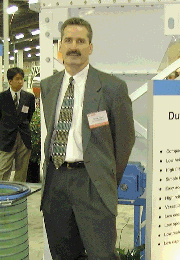
Luwa Bahnson Inc., Winston- Salem, N.C., displayed its new Dust Separator III, model DS-III.
The DS III reduces space requirements and improves ease of maintenance. It is the final element in
removing dust from textile and nonwovens processes. The vertical design of the filter cartridges
provides more efficient pulsing of dust. In extra-heavy fiber loading, an optional screen sleeve is
mounted around the cartridges. Extra-wide cartridge spacing prevents bridging of fibers. The
special cone in the center of the cartridge enhances the automatic cleaning by compressed air. This
provides a longer cartridge life and reduced service requirements. The discharge air can be
returned either to the room or to the central filtration system.Luwa also exhibited the latest
version of its Multi Drum-Vac® (MDV), the 9-foot-diameter MDV that supplies spinning-production
applications with up to 50,000 cfm of air, and ambient filtration up to 70,000 cfm.N.
SchlumbergerandCie, France (N. Schlumberger USA Inc., Fort Mill, S.C.), showed the latest version
of its CF-60 series double-sided ring- spinning frame that is specifically suitable for the
production of semi-worsted lines of carpet and rug yarns, upholstery yarns, knitting yarns and
technical yarns. It covers a yarn-count range from Nm 2 to 20/24 and can be equipped with an
automatic doffing system.NSC also exhibited the latest version of its tandem chain gill, the TM/GC
15 RE with an electronic autoleveller. It is designed for integration in compact spinning lines for
the production of carpet, upholstery and hand-knitted yarns. It features bi-directional control
through touch-screen dialogue, electronic draft adjustment and other advanced features that allow
production speeds of up to 550 yards per minute (500 m/min).Network Systems International Inc.,
Greensboro, N.C., offers the turn-key Net Collection, an enterprise-wide suite of ERP solutions
designed to enhance management planning and control in complex process and distribution centers.
The software includes modules covering enterprise demand management, time-phased resource planning,
supply-chain advisements and monitoring, distribution center authority and executive information
analysis broken down into task-specific sub-modules governing the major steps involved in producing
and delivering textiles, apparel and made-up items. At ATME-I 2000, Network Systems introduced four
new functions for its netCollection suite: netCashController, netSalesExec, Tracking Portal and
UltraClient. The first three apply to specific management areas, while the fourth allows access to
all functions of the complete software package over the Internet using a standard Web browser. This
allows away-from-home access and control over internal systems and provides remote sales personnel
and customers with ready access to sales order and delivery information without additional
connection costs or special software.Pneumafil Corp., Charlotte, N.C., presented the Everclean®
Rotary Pleated Belt Filter (RPB) that filters air more thoroughly than conventional tandem filters,
according to company officials. The RPB filter consists of a number of filter cells. Each cell is
comprised of an endless pleated filter-media belt, looped between two pulleys. Unfiltered air
enters the unit parallel to the filter cells and passes through the straight sections of the belt
loop. Larger fibers collect on the outer edges of the pleat, and smaller particles build up on the
media surfaces between pleats. The clean air continues between the two sides of the cell into a
plenum in back of the filter and then exits. Pressure drop across the media is constantly monitored
by a dual set-point Dwyer Photohelic gauge. When the high point is reached for a given cell, that
cells belt begins rotating around the pulleys, and a stationary suction plenum underneath the cell
is activated. As the belt moves around the lower pulley, the pleats open up and air flow through
the media is reversed, allowing the pleats to be easily vacuum-cleaned.Pneumafil promoted the
compact modular system utilized by its conditioning units. This system facilitates movement during
installation or relocation.OMM/Fillattice SPA, Italy (Fillattice Inc., Charlotte, N.C.), exhibited
the OMM type SPE covering machine for the production of Fillattice spandex yarn. The machine offers
several features, including the new SX spindle type, an electronically controlled take-up, and an
electronically controlled traversing device that assures excellent quality without any mirror
effects. The machine is available with a wide range of heads and a spindle gauge of 200 or 265
millimeters.
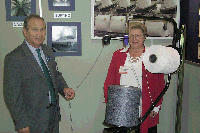
Otto Zollinger Inc., Spartanburg, S.C., displayed its full line of yarn controls. The O-Z®
Yarn Control System provides constant, uniform tension with no adjustments; reduces yarn breaks;
increases quality; increases production; reduces maintenance; allows easy package transfers; and
does not restrict speed, according to the company.Roberts, CurryandCo., Greenville, S.C., is a
management-consulting firm specializing in the textile and apparel industries. Its experience and
expertise cover all facets of textile operations with heavy emphasis on productivity improvements,
management systems, technology assessments, marketing, human resources development and total
quality management (TQM). Additionally, the organization is well-versed in many apparel operational
issues.
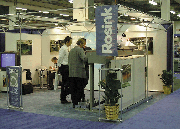
Rosink GmbH, Germany, exhibited the RK-W-235 rectangular can coiler with automatic can
changer. Rosink states that the RK can coiler is the worlds first self-contained rectangular can
coiler. Conveyor belt and calender rollers are independently servo-driven. The coiler operation is
synchronized electronically with the host machine. There is no mechanical interface, gearbox or
chain drive. A coiler-head dust-extraction system is included. Rosink RK can coilers are adaptable
to the Rosink can-transport system. The company also offers round can coilers, carriers and
can-changer systems for new cards and as retrofits for older cards.SAP America, Newtown Square,
Pa., teamed with its textile-industry specialist, Prescient Consulting, Atlanta, to introduce the
Prescient-designed textile-industry-specific version of SAPs R/3 ERP software. Building on the
recent success of SAPs Apparel and Footwear Solution (AFS), the partners are extolling the virtues
of the software, which is composed of modules specifically designed to address issues in management
of the textile supply/value chain. SAP has considerable experience in supply-chain management
controls and has partnered with Prescient to bring industry expertise to the design, installation
and implementation of the R/3 system for textiles.Savio Macchine Tessili SPA, Italy (American
Savio, Spartanburg, S.C.), showed the Orion Automatic Winder and the Geminis Twister. The Orions
key feature is its electronically controlled computer aided package (CAP) that prevents any
patterning of the yarn on the package. The Orion winder surpassed all early predictions for
incoming orders between the introduction of the machine at the International Textile Machinery
Exhibition (ITMA 99) and ATME-I 2000, according to company officials. Savio received the ATI Award
for Innovation in 1999 for this machine. Since then, the company has expanded the application and
model range of the Orion winder. Orion M is a model with manual feeding and doffing; Orion L
features manual feeding with automatic doffing; Orion E is a fully automatic version; and Orion I
is the linked version of the series.SML Lenzing, Austria (Tex America Inc., Charlotte, N.C.),
promoted its product line that includes extrusion technology for the plastics and textile industry,
BCF spinning technology and FDY spinning technology. SML is a member of the Starlinger Group,
Austria, which has more than 35 years of experience in developing, designing and manufacturing
extruders. SMLs Austrofil® BCF spinning system offers minimum floor space, high crimp contraction,
good crimp stability and low shrinkage. For Austrofil® FDY spinning, SML offers the MT version for
the production of continuous filament with medium tenacity, and the HT version for the production
of continuous filament with high tenacity of up to 8.5 grams per denier, both in the yarn- count
range of 200 to 1,600 denier.TextileWeb.com, Greensboro, N.C., featured its new relationship with
VerticalNet, the Philadelphia-based backer of 57 new economy enterprises. TextileWeb is focusing
its current efforts on expansion of its trading platform, which covers textile materials from
fibers to sewing supplies. The company is adding services to its website, which now features access
to databases for services in consulting, marketing and investment banking.The Dock, Los Angeles, is
introducing a website/database for trading textile machinery. Target customers are traditional
machinery dealers and individual companies looking to buy, sell or trade used textile equipment.
The Dock does not require it be included in all purchases/sales transactions. The site establishes
contacts and is willing to be involved in negotiations and financing, but The Dock also is willing
to allow the principals to conclude a deal without its involvement. Revenue is gained from
advertising, sale of home pages to active buyers/sellers and from the fee charged if The Dock is
included in a purchase negotiation.
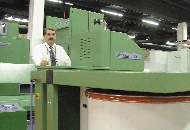
Truetzschler GmbH, Germany (American Truetzschler, Charlotte, N.C.), presented its newly
enhanced high-production card, the model DK 90. A new equipment kit specifically designed for
synthetic fiber applications has considerably improved productivity and efficiency for man-made
fiber processing. New also is the linking of the DK 903 with the integrated draw frame (IDF) that
was originally shown in Paris as a prototype. Depending on the final application, it offers the
possibility of bypassing one draw-frame passage and, in some cases, even two draw- frame passages.
The new production-ready equipment from Truetzschler helps to improve the economy of the yarn
preparation room.Also displayed in the booth was the HSR 1000 draw frame with rectangular
can-delivery system. Up to 50 kilograms (approximately 110 pounds) of draw-frame sliver can be
smoothly coiled into these rectangular cans, which are designed for use at roving machines. Also
new is the Securomat SCFO, which is a multifunctional machine for fiber preparation. It ensures an
intensive dedusting of the cotton through the use of an integrated camera system that detects and
separates foreign particles.U.T.I.T Textile Division, Wagner Automation, SPA, Italy, displayed
cone-cartoning automation systems. The U.T.I.T. line provides an example of a fully integrated,
automated packaging system. All stages of the process, collection of cones from the link-cone
winders, checking and labeling of individual cones, conditioning, carton placement taping and
palletizing are executed automatically without intervention by human operators. The line permits
the collection of cones from various cone winders that produce yarns of different counts. Dedicated
control software allows the simultaneous management of control, packaging and palletizing of
different yarn counts, while maintaining independent management of each count during the whole
cycle.Xorella AG, Switzerland (PSP Marketing Inc., Charlotte, N.C.), exhibited the Contexxor®
Compact Unit LTC-S for yarn conditioning. The rectangular shape of this new machine permits
optimized utilization of space for the yarns inside, lower space requirements for the mill and
shorter processing times. It also has low energy consumption because of the new ECO system. Xorella
received the ATI Award for Innovation after ITMA 99 for this technology.Zellweger Uster,
Switzerland, (Zellweger Uster Inc., Knoxville, Tenn., and Charlotte, N.C.), showed the Uster® Afis
Pro, Uster Tensorapid 4 and Uster Tensojet, the most technologically advanced fiber- and
yarn-testing equipment the company has available. With its new Windows-based software, Uster Afis
Pro offers up to 50-percent-faster testing speeds than its predecessor. It integrates new reporting
and diagnostic software for graphical comparison of fiber quality to Uster Statistics, thus
contributing to a more efficient use and control of the raw material in the production process.The
Uster Tensorapid 4 improves quality and process control with its increased yarn-quality evaluation
capabilities. New are sensors for denim fabrics and technical yarns; and warning and control limits
can easily be configured. The equipment facilitates new test procedures, especially in the areas of
strength testing and filament yarns.The new Uster Tensojet 4 is the latest generation of the
high-performance tensile testing installation for effective and mill-oriented yarn quality
control.New, as well, is the Uster HVI Spectrum, which represents the companys new generation of
bundle- fiber testing. Features include completely automated sampling, accurate and precise cotton
fiber maturity index, and drastically reduced sample and laboratory conditioning requirements.
Complete automation reduces operator influence to a minimum. Additional new features include
automated calibration checking, accurate short-fiber index, automatic moisture measurement of
samples and quality control tools.
Editor’s Note: Executive Editor Jim Phillips, Senior Technical Editor Eric Vonwiller, Fibers
Technical Editor John E. Luke, Spinning Technical Editor Dr. William Oxenham, and Nonwovens
Technical Editor Richard G. Mansfield contributed to this article.
December 2000
Radici Becomes Sole Owner Of FIM Textile
The previously announced joint acquisition of Italy-based FIM Textile by Picanol, Belgium, and the
Italy-based Radici Group has been called off. Radici is now the sole owner of FIM Textile.It
appeared that the expected synergies related to the double-shareholder structure by Picanol and
Radici would be difficult to materialize in practice. Therefore, both parties agreed that Picanol
will not enter the capital of FIM Textile.
December 2000
DuPont Combines Apparel And Textile Businesses
DuPont, Wilmington, Del., has announced the integration of its apparel, home textiles and related
businesses into a market-focused global organization. The name for the new organization is DuPont
Apparel and Textile Sciences.DuPonts Lycra® elastane-, nylon textile- and Dacron®-branded
specialties and fiberfill businesses will become a single unit effective January 1, 2001. The new
unit will capitalize on DuPonts global brand franchise, technical expertise, operational scale and
market knowledge to provide a more streamlined and competitive offering.Our vision is to create
consumer preference and loyalty to help grow our customers offerings by linking DuPont science with
the promise of our brands, said Steven R. McCracken, group vice president, who will lead the new
organization.DuPont Apparel and Textile Sciences will provide a world-class integrated market
platform that will allow better linkage between the marketplace and DuPont technologies. The
combined organization will have approximately 10,000 employees and marketing, technical and
manufacturing operations in every region of the world.We believe this centralized market approach
will provide economies of scale and scope, enable us to build stronger partnerships with our
customers and better deliver the constant flow of newness our global markets demand, added
McCracken.
December 2000
KoSa Announces Technical Fiber Price Increase
CHARLOTTE, N.C., Dec. 6 /PRNewswire/ — KoSa, one of the world’s largestpolyester producers, is
increasing the prices of its technical fiber productsby 5 to 22 percent, depending on market
segment, effective with Jan. 2, 2001,orders. Included in the increase are the company’s Technical
Filament andTirecord product lines.The move, necessitated by raw material cost increases and
generalconditions in the global technical fiber marketplace, will allow KoSa tocontinue supporting
its customers with superior polyester products andservices. SOURCE KoSaWeb Site:
http://www.kosa.com
Copyright 2000
PR Newswire
Living The American Textile Dream
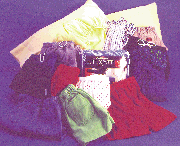
It wasnt too long ago around 1986 when a bunch of guys decided to put up everything they
owned as collateral to start a textile mill. What, you want to start a textile mill was the
somewhat incredulous response from friends and financing officers to then 42-year-old J. Keith
Crisco, founder, owner, and current president of Asheboro Elastics Corp. especially in terms of
customer service, product performance and price.So in 1986, the company was started from ground
zero, in the facilities of a former textile plant and with no employees or machinery. From day one,
the company purchased only new equipment, Crisco said. The company started to manufacture knitted
elastic fabrics for waistbands in jeans and boxer shorts, underwear, lingerie, fitted sheets,
furniture, automotive applications, hats, medical bandages, and many other usual and unusual
applications.From 1978 to 1986, Crisco was the general manager of Stedman Elastics. In addition, he
served as chairman of the National Elastic Manufacturers Association for two years, and had spent
nine years in management with Burlington Industries. Therefore, he brought some significant
experience with him, as did the other members of the original owners group. Another active owner is
Warren D. Knapp Jr., current vice president of the company, responsible for sales and marketing.
Knapp had a personal friendship with Crisco for many years that goes back to the time when both
studied at Pfeiffer College. Knapp said, From the very beginning, the company was based on honesty
and integrity. The men stressed this in their first company brochure and openly disclosed their
Christian faith, their unconditional commitment to the business and to their families. Today, the
company has about 130 crochet-knitting machines, 165 employees and three manufacturing
plants. Impressive GrowthThings started to go well from the very beginning. In fact, in 1991,
AEC earned a ranking on Inc. Magazines list of the top 500 fastest-growing privately held companies
in the country. Inc. Magazine, with a circulation of more than 600,000, is a leading business
publication for entrepreneurs and growing businesses. The ranking was based on the companys
percentage increase in sales between 1986 and 1990. AEC posted sales of $842,000 in 1986 and $7.6
million in 1990, an 800- percent increase. With that, AEC was viewed as one of the best and most
innovative companies in the world. The steep rate of increase in sales has, of course, not
continued to the present. ATI asked AECs president what current profit and sales figures look like,
Crisco pointed, with confidence, at the continuing growth in sales and market share, stating,
Expected sales in 2000 will be well above $20 million. Just to show how well things are going,
Crisco mentioned a production capacity increase of approximately 30 percent over the last three
months, and an increase in overall production of approximately 45 percent in 1999. Crisco
emphasized that in 14 years, the company has never had a short week of production, unless there was
a holiday. Every year, the company has experienced a sales increase there was never a down year.
These are impressive facts when compared to the average textile statistics worldwide.By 1993, AEC
opened a second plant in Franklinville N.C., just a few miles from Asheboro. Plant 2 concentrates
specifically on elastics for home furnishings and mens underwear elastics. This past July, ACE
announced the start-up of Plant 3 in Asheboro, and the acquisition of Sommers, Inc., Elastics
Division, Stroudsburg, Pa. This acquisition allows for the expansion of manufacturing capacity that
will be integrated into Plant 3. Versatility In Every Aspect
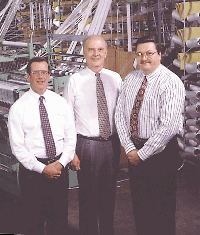
Even though the majority of the goods manufactured are still knitted narrow elastic fabrics,
the company also produces some non-elastics and narrow woven fabrics. Approximately 65 percent are
related apparel applications, while a wide variety of products about 25 percent are related to home
furnishings; and 10 percent are other, including industrial, applications.The focus has been on
customer service and adapting manufacturing for the market. Especially for fitted sheet elastics,
AEC made a special commitment to adapt the production requirements to increase the overall
efficiency for fitted sheet elastics. Crisco mentioned that doing this helped the company become
the market leader in this specific field of bedding elastics by 1996. Crisco, without wishing to
disclose actual percentage figures, explained that the market share is extremely large in this
particular segment.AEC also has offshore warehouses in San Pedro Sula, Honduras; Santiago,
Dominican Republic; and three in Mexico Aguascaliantes, Puebla and Torreon. Other remote locations
for the company include Brownsville, Texas, and Miami, Fla. These facilities are all distribution
points that help the company learn the markets and the customs of the people. It is kind of a
learning curve, said Crisco, that the company had to undergo before it would even consider
investing in actual remote manufacturing.The company also forms partner-ships with customers by
developing new products with them. Some-times we know we will never ship a yard, or maybe only for
one week, Crisco said with a sigh, but he also acknowledged that this effort has been a very
positive experience, a learning process from which at some point busi-ness will originate.
Therefore, forming partnerships with customers is a high priority for AEC. Prepared For The
FutureCrisco said he thinks there will be a lot of changes happening worldwide in the narrow
fabrics industry over the next couple of years. He emphasized that the company is prepared for this
by being debt-free; having a good balance sheet; strong distribution focus and low labor cost; and
investing in automation. The company is also continually replacing older equipment with modern
machinery. We invested in machines and in people, said Crisco. Team effort is very important at
AEC, and so is the training effort that the company puts in for its people.Just recently, the
company purchased new Jacob Mueller narrow fabrics machinery to expand its capacity. Crisco spoke
very favorably about all Muellers machinery and equipment that is installed in the three plants,
and also about Muellers service and training commitment towards the company. The Raschelina® RD3 is
the model that AEC preferred during its latest purchases. This warp-knitting machine, with weft
insertion, reflects the technology based on practical customer experience and latest technology
developments in research and development. The RD3 offers high performance, versatility,
ease-of-operation and low maintenance, exactly what AEC expects from a production machine. Another
advantage is that the RD3 offers a usable knitting width 20-millimeter wider than offered by
competitive machines, which gives the company the advantage of producing more tapes per unit.
During the interview with ATI, AEC pointed out that all gear mechanisms of the RD3 run in
dust-proof oil baths that protect against wear, avoid any fabric contamination that could relate to
gear mechanisms, and are virtually maintenance-free. Needless to say, AEC is very pleased with this
machine and is planning to purchase more of them during its continuing modernization program. AEC
has started to adapt its products even more to customer needs with respect to product performance
and price. This helps in gaining market share. For example, replacing woven goods with newly
developed knitted products is exactly what makes Crisco and his team successful in gaining every
bit of the desired market share. But, on the other hand, AEC has also added some woven products to
expand its overall coverage of the market.
December 2000
GretagMacbeth Acquires McMahan Electro-Optics
GretagMabeth, New Windsor, N.Y., has acquired McMahan Electro-Optics Inc., Research Triangle Park,
N.C. McMahan spectroradiometric instruments and software are used by reference laboratories to
measure, characterize, qualify and certify sources of visible, UV, infrared and optical radiation.
Ron Anderson, president and CEO, GretagMacbeth, said, The combined firms of GretagMacbeth and
McMahan will play an extremely important role in providing complete solutions in the increasingly
integrated world of lighting and color management.In related company news, GretagMacbeth announced
plans to open its state-of-the-art ResearchandAdvanced Products Development Center in Research
Triangle Park, N.C. The new facility will focus on rapidly translating leading-edge technology and
systems research into software and instruments to enhance its position in the areas of color
management and color control systems. It gives us immediate access to enabling technologies which
are critical to our color measurement, communication and simulation activities, Anderson said.
December 2000
Conneaut Industries Acquires Chadwick Yarn
Conneaut Industries Inc., West Greenwich, R.I., has purchased the assets of Chadwick Yarn Co. Inc.,
Central Falls, R.I. Both companies specialize in yarn products for the electrical and cable
industries. The two companies have a high level of experience and expertise in twisting and winding
processes. Our merger will create a high level of synergy to grow the existing products and develop
new applications, said John Santos, vice president, Conneaut.
December 2000
China The Long March
China has always been a separate star in the constellation of the world textile industry.
Today, however, signs of substantial economic take-off are surfacing, in concert with the favorable
overall trend at the international level.Concurrent with the China International Textile Machinery
Exhibition (CITME) 2000, staged in Beijing, the Chinese Communist Party (CCP) concluded a three-day
meeting of the Central Committee by issuing a document which, laying aside the traditional,
strongly ideological tones, focused instead on the reforms required to cope with global
competition. The 10th five-year plan worked out by the CCP no detail of which has yet been revealed
envisages a doubling of the gross domestic product (GDP) by 2010, with an annual growth of at least
7 percent. The growth anticipated for the year 2000 is 7.5 percent (in 1999, the GDP totaled $992
billion).Behind the concern for the countrys social development, there is, obviously, its impending
entry into the World Trade Organization (WTO). However, the document makes no mention of the WTO,
but warns instead against the danger of competitiveness and globalization. If no development takes
place, states an editorial published in the Peoples Daily, the differences in relation to advanced
countries will widen, and China will no longer have a say in the international arena.Beijing must,
therefore, prepare for its ever-larger integration into the international economic scene. The
launching point of the new economy lies, however, in political reforms, which is why the Central
Committee raised the issue of modernization. The goal is the maintenance of a long-term political
stability in order to create a good atmosphere for the reforms and for the opening to the rest of
the world. The Search For StabilityTo put it bluntly: political stability is a must. Needless
to say, this kind of news appealed to the entrepreneurs and managers seen in the crowded halls at
CITME. And, likewise, the outcome of the Central Committee session was in the forefront at press
conferences and meetings with representatives of Chinese industry. Even though for months the Asian
giant had shown a clear upswing in the purchase of textile machines (virtually for all segments of
the production chain, from fiber opening plants to finishing plants), there is no doubt that
renewed and tangible interest surfaced at the fair. The prospects opened up by the new five-year
plan also feed a grounded hope of business development.Many people think that China may embark,
with the advent of the third millennium, on a new version of the long march that came to an end 50
years ago with the founding of the Peoples Republic of China. However, the obvious difference is
that the future course will no longer be marked by military bands and the rumble of guns, but by
the more reassuring rhythm of machines that promise to bring the most densely populated country in
the world to new economic levels. CITME 2000CITME pulled in nearly 103,000 visitors, including
a large number of top managers of the world textile industry. At the event, 685 companies had a
major presence, with numerous machines and a large group of techno-commercial staff.Two events
related to CITME proved to be particularly interesting. The Swiss Evening was a lavish celebration
of the 50th anniversary of diplomatic relations established in 1950 between China and Switzerland,
the first European nation to officially recognize the new republic formed by Mao Ze Dhong.The
evenings events included a unique competition among four Chinese universities and institutes
engaged in the education of young designers. The four winners (one from each school) will be hosted
for one week in Switzerland, where they will see what is being done at the Swiss Textile College
the comparable Swiss training institute for the textile and clothing industry.Another presentation
was made by a delegation of Japanese industry executives headed by Junichi Murata, chairman of the
Japanese Textile Machinery Manufacturers Association (JTMA). The information so far available about
the 7th Osaka International Textile Machinery Show (OTEMAS) scheduled to take place in October 2001
included an updated list comprising several hundred companies that have already booked booths for
the Japanese exhibition. Also highlighted was the 10,000-square-meter IT Pavilion, which will
present information technology and supply-chain management as the textile industrys keys to new
levels of efficiency and quality.
December 2000