Leader Of The YearBy John W. McCurry, Managing Editor Herwig Strolz: Textiles’ Global StatisticianLongtime ITMF Director General is Textile World’s Leader of the Year.
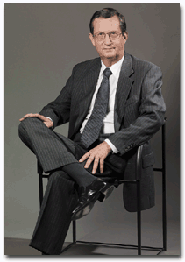
Ask Herwig Strolz a question about worldwide textile machinery shipments and be prepared for an education on the state of the industry. Strolz, director general of the Zurich-based International Textile Mfrs. Federation (ITMF), can offer seemingly unlimited insightful analysis.For example, Strolz believes the U.S. industry is in the midst of a restructuring similar to what its European counterpart experienced in the 1970s. However, what took about 20 years in Europe is on an accelerated pace in the U.S., he believes.”I have thought for a long time that the U.S. will go the way Europe has gone,” Strolz says. “Europe was affected much earlier by globalization. Restructuring of industry started much earlier in the 70s and is still continuing. Companies have learned over a period of time to adapt.” Strolz believes the evolution of the textile industry may take just five years in the U.S. He says to survive, companies must increase flexibility, pay more attention to quality and seek strategic alliances with manufacturers in other countries.”What it will come to is America will have a different textile industry in five years, perhaps even earlier,” Strolz predicts. “Developments are already pointing in that direction. It will be a more versatile, a more quality conscious industry that caters to the upper market segments and pulls out of commodity textiles.”Dan Frierson, chairman of The Dixie Group and a former ITMF president, is a Herwig Strolz fan. He says Strolz has few peers as an industry analyst. “I really think Herwig has done the best analytical work on this industry,” Frierson says. “He is extremely knowledgeable and talented and is a great student of industry trends. If people in the industry listen to him, they will come out ahead.”Frierson says Strolz has been “beating the drum” of overcapacity since the early 1990s, updating his statistical model on installed capacity each year. “He has been very accurate, and candidly, his analysis is one thing that led us to exit the traditional textile business and enter carpet business,” Frierson says.When the worlds textile associations need an expert speaker to dispense a dose of honest industry assessment at an annual conference, they often turn to Strolz, who arguably is a premier tracker of textile trends. One of his recent talks was to the American Yarn Spinners Assn. where he admitted that todays textile market leaves even the most informed observer perplexed. In his speech, which he titled, “Spinning in the Real World,” Strolz told spinning executives their segment has “a giant overcapacity around its neck.” His advice: “excess capacity must be the central point of departure in each spinning companys strategy.”ITMF President Herbert Schmid, president of Brazils huge Santista Textil, a global manufacturer of denim and other fabrics, says Strolz has been involved in every sector of the global textile production process through personal visits, conferences, speeches, committees and publications. “His personal commitment to the industry has been to serve as a bridge between cultures and styles of doing business,through his command of several languages, his unflagging goodwill and his practicality and persistence,” Schmid says.Strolz, one of the worlds premier purveyors of textile industry information, is Textile Worlds 2001 Leader of the Year. He is the first non-industrialist to receive the award. A Global OrganizationITMFs member nations account for about 65% of the worlds textile production. China, which accounts for 20%, is the largest non-member. Strolz expects China may join in the future. “There is a relationship between ITMF and the Chinese industry, but it has not reached the quality of a membership relationship,” he says.An association of associations, ITMF does not have a large staff. Besides Strolz, an assistant director, an economist and a part-time secretary comprise the staff.Strolz, 64, has spent nearly half of his life as head of ITMF. He will observe 32 years with the organization next Jan. 1. During that time, he has enjoyed many professional relationships, which have contributed to his successful tenure. He recalls three men, all former ITMF presidents who are now deceased, who helped him immensely during his early ITMF years.”To be successful, you need a lot of good will on the part of leading people at the helm of any organization,” Strolz says. He cites Craig Smith, former chairman and CEO of Avondale Mills, Tami Guchi, head of Toyoba, the largest textile company in Japan and Mateo Legler, former chief of the huge Legler Group in Italy.Guchi hired Strolz and Smith was the incoming president. Legler also later served as ITMF president. “They all gave me enormous support from the beginning,” Strolz says. “Then there are all my colleagues from associations around the world who have been supportive in our efforts.” ITMF Becomes Authority On Machinery ShipmentsOne of ITMFs greatest accomplishments since Strolz took the reins is the accurate compilation of global textile machinery shipment statistics. In the early 1970s, information of this sort was scarce and consisted mainly of installed capacities in various textile sectors such as spinning and weaving. Today, ITMFs annual “International Textile Machinery Shipment Statistics” is a highly regarded industry publication. The current edition is the product of many years of research and convincing of machinery manufacturers to share information.”In the early 1970s, all we knew were the installed machinery capacities around the world,” Strolz remembers. “It was a good time for the industry in the years leading up to the first oil crisis with machinery manufacturers selling out two or three years in advance, sometimes even more. So, even they had lost sight of investments.”We wanted to go a step further than the information that was available and track investments year to year. At that time, this kind of data was considered absolutely confidential.”What Strolz and ITMF needed was the cooperation of machinery manufacturers. Gradually, Strolz persuaded companies that ITMF could compile the data and then divulge it in a way that would not reveal the number of machines shipped by an individual company. German and Swiss manufacturers were the first to participate and then others joined.
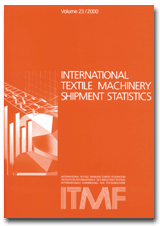
“We started a new thing,” Strolz says. “Today, this is our Number 1 publication, no doubt about it. Nowadays, companies are working with us directly. We dont take any existing trade statistics. We take our questionnaires as they come back from the companies and they provide a picture of investments by the industry today.”The publication continues to grow. Texturing and circular knitting machinery manufacturers joined in recent years and the current issue includes flat knitting machinery figures for the first time.”We can say we are covering somewhere between 95% and 100% of the worlds investment in textile machinery,” Strolz says with a sense of pride.
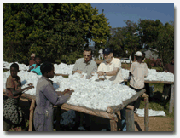
Other ITMF milestones include establishment of various committees for industry segments. Strolz cites the Spinners Committee, in particular. ITMF created the Spinners Committee in 1985 to give the spinning sector a greater voice in matters of interest to the industry. A major objective is to support the development of quality cotton fiber based on modern spinning requirements.”We decided that if we really wanted to bring this industry forward, we needed to seek a dialog between the spinner and the grower of natural fibers,” Strolz said. “In its 16 years, it has grown to 12 members.” Strolz says the committee is representative of the worlds spinning industry. A new member is Andy Warlick, president of Parkdale Mills.The Spinners Committee travels to the worlds cotton growing regions and this summer toured areas of southern Africa. “We try to bring the message from the modern spinning industry to those in the field that produce cotton who have little idea of the constraints of spinning machinery,” Strolz says. Consolidation Of Machinery ManufacturersMirroring trends in textile manufacturing over the last several years, makers of textile machinery are merging and acquiring competitors at a quick clip. Major conglomerates include Saurer, Rieter and Radici. Strolz thinks the trend will continue.”Its in full swing,” he says. “Consolidation is going on in all areas. The essential thrust is toward higher concentration because companies are finding it more difficult to constantly innovate with the volume of business they are doing now.”Still, there remain many major machinery companies in the world, about 150 by Strolzs count with about one-third in China. Expanding ITMF MembershipStrolz enjoys his work with ITMF membership and states a goal of expanding its base, an effort he says is never ending. ITMF represents about 50 nations, although there are some notable exceptions such as China and Mexico.”I cherish my relations with my membership and I want to bring in more members,” Strolz says. “Some have been in and out like the Mexicans. China should have a place in the Federation. I would also like to see the Japanese textile machinery industry join. There is a good chance of this.”
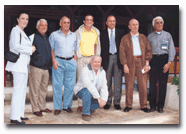
Strolz (center, in yellow shirt) stands with members of the Turkish Textile Employees Association during its meeting in April.ITMF should become more of an “umbrella” organization, expanding both ways in the textile pipeline with increased membership from the fiber and apparel sectors.Interestingly, the U.S. does not have a full member of ITMF since the American Textile Mfrs. Institute left the fold early this year. However, several U.S. associations are associate members, including the American Yarn Spinners Assn., a recent addition. MillikenandCo. and huge Korean fiber manufacturer Huvis Corp. are ITMFs two corporate members.With expanded membership come expanded services. A new initiative is the Young Entrepreneurs Group, which had its first meeting in September at ITMFs annual meeting in Budapest. The group gives young industry leaders (maximum age is 40) a forum to discuss opportunities. Says Strolz, “It brings new blood into the Federation.”The Herwig Strolz BiographyHerwig Strolz was born in Bregenz, Austria, in 1937. He studied law and political science at the University of Vienna where he graduated in 1961 as a doctor in law.Strolz joined the foreign trade department of the Austrian Federal Chamber of Commerce in 1962 and was appointed Assistant Austrian Trade Commissioner in Caracas, Venezuela, the following year. He was transferred to the Austrian Foreign Trade Office in Montreal, in 1966. In 1968 he was appointed director of the Austrian Federation of Industries and assumed managerial responsibilities for the textiles and clothing department of the Chamber of Commerce of Vorarlberg, the province where most of Austria’s textile manufacturing activity is located. Strolz became director of the International Federation of Cotton and Allied Textile Industries (IFCATI) on Jan. 1, 1970, by appointment of the Federation’s Committee of Management at its meeting in Oporto, Portugal, in October 1969. The Federation changed its name to International Textile Mfrs. Federation (ITMF) in 1978. During his term of office ITMF has become the leading global trade association of the primary textile industry with close to 50 of the world’s most important textile producing countries in membership. In 1991 Strolz received the “Golden Jenny Award” of the Schlafhorst Foundation. ITMF Evolves With Industry For 97 YearsThe International Textile Manufacturers Federation (ITMF), founded in 1904 by the British cotton spinning industry, is one of the worlds oldest textile trade associations. Its original name was International Federation of Master Cotton SpinnersandManufacturers Assn. and first headquartered in Manchester, England.In 1954, the organization adjusted to the changing industry and changed its name to International Federation of CottonandAllied Textile Industries. The Federations headquarters moved to Zurich, Switzerland, in 1963 to broaden its international scope. In 1978, the name was changed to International Textile Mfrs. Federation.ITMF membership includes:Full Members are associations and other constituted organizations of manufacturers of textiles. There can be only one member association from each country. Associate Members are associations and other constituted organizations of manufacturers of textiles in countries where there is already a member association; and associations allied to the textile industry. Corporate Members are manufacturers of textiles or of products allied to the textile industry in countries where their respective central trade association is not affiliated with the Federation. Today, ITMF says its main objectives are toprovide a forum for discussion of matters appropriately within the common interest and concern of textile companies. provide a neutral meeting ground for textile trade associations for the exchange of information on matters affecting their textile industries, consistent with the trade regulation laws of the nations represented. act as a central agency of the textile industries for the collection of information, statistical and otherwise, on textile manufacturing developments in all countries of the world. act as spokesman for the world textile industry in matters relating to raw materials (cotton and manmade fibers). perform the functions of a liaison agent between the textile industries and governments and intergovernmental organizations interested in the textile industry. October 2001