Micro Air Presents TM 1000 TaskmasterWichita, Kan.-based Micro Air Clean Air Systems offers a new, portable TM 1000 TaskMaster for maintenance and air pollution control in shops and plants. The base unit includes a lift-off attachment connection. No tools are required, and attachments can be changed rapidly, according to Micro Air. Among the attachments are: articulated source capture arms in assorted sizes; dual articulated arms for use by two operators; a downdraft table; a backdraft hood; and a long-reach flexible hose with hood. Applicable activities include gluing, painting, cutting, grinding and welding, and others.The TaskMaster can be plugged into a 120-volt (V) single-phase outlet. Optional plug-ins to 208/230V and 460V three-phase outlets are available. An efficient high-capacity motor blower assembly provides flows of 1,000 cubic feet per minute.Dual cartridge filters are cleaned by the companys Roto-Pulse high-efficiency cartridge-cleaning system. Filter options include HO Spunbond cartridges, HEPA 99.97-percent afterfilters to control minute particulate and activated charcoal modules to control odor.January 2002
VF Announces Job Cuts Plant Closings
VF AnnouncesJob Cuts, Plant ClosingsVF Corp., Greensboro, N.C., is cutting its U.S. work force by
13,000 people and closing more than 30 plants as part of a restructuring plan that aims to
eliminate low-margin operations and improve the companys earnings by $115 million annually.The job
reductions represent 18 percent of VFs work force. Approximately 9,000 of the eliminated jobs will
be replaced by production offshore.The plant closings represent cut-and-sew operations for Wrangler
jeans, Vanity Fair underwear and other apparel items. These items will be manufactured in Mexico,
Central America and the Far East. In addition, the company will cease manufacturing Jantzen
swimsuits, private-label sweat shirts and T-shirts, and uniforms for the high-tech industry. Moving
forward, VF will focus on its core businesses of underwear, jeans, outdoor apparel and licensed
apparel; and on acquisition of new businesses.
January 2002
WTO Will Negotiate Textile Issues
W
hen the World Trade Organization (WTO) launches a new round of international trade
negotiations January 28 in Geneva, three issues of major importance to textile industries worldwide
will be on the table. They are: an effort by the less-developed nations, led by India, to speed up
removal of textile and apparel tariffs now due to expire in 2005; reductions in textile and apparel
tariffs; and revisions in trade remedy laws, suchas anti-dumping and countervailing duties.
While the Bush administration has steadfastly said it will not agree to any speed-up for
removal of quotas, the issue remains on the table and is of concern to U.S. manufacturers. The
question of how to address tariff reductions is wide open at this time.
Many in the WTO would like to see an across-the-board percentage cut in tariffs, but the
U.S. industry contends that would not be fair, as many countries currently have tariffs ranging as
high as 70 percent, while U.S. tariffs average 13 percent. Industry representatives are urging U.S.
negotiators to resist any tariff cuts and focus instead on the duties that other nations levy on
imports. Retailers and importers of textiles and apparel would like to see all tariffs removed
everywhere in order to encourage freer trade.
In a statement regarding trade issues, President George W. Bush said: “I will insist that we
press open foreign markets for our textile products as a part of future trade agreements, and that
our trading partners comply with the rules of our existing arrangements. In short, I intend to
ensure that the interests of our textile industry and workers are at the heart of our trade
negotiations.”
FTC Issues Warning On ‘Made In USA’ Labeling
The Federal Trade Commission (FTC) has issued a “Consumer Alert” warning consumers, retailers and
manufacturers that unscrupulous textile and clothing manufacturers may take advantage of the wave
of patriotism following the September 11 terrorist attack and mislabel their products “ Made in
U.S.A.” The FTC warning says consumers are seeking products that are “Made in U.S.A.” with the
expectation that the claim is “truthful and accurate.” There is no law requiring manufacturers in
general to disclose U.S.
content, but many do so for marketing purposes. However, in the case of textiles and
apparel, there is a law requiring labels on every product to state where the product is
manufactured. The textile labeling act is quite specific in that all U.S.-made products have to
have a “Made in U.S.A.” or equivalent phrase; products made in the United States of imported
materials must so state, and products made in part in the United States and partly abroad must
identify both countries.
More Textile And Apparel Quotas Dropped
The third phase of the 10-year phase-out of textile and apparel quotas going into effect
this month lifts restrictions on a verity of yarns, fabrics, made-up goods and apparel. Products
now free from import quotas include: some textured and non-textured filament yarns, man-made fiber
staple yarns and some silk yarns; knit fabrics, wool tapestry fabrics and glass fiber fabrics;
made-up goods, including luggage and some table linens, non-terry towels and blankets; and apparel
products, including brassieres, robes and dressing gowns. Details, including specific product
categories, are available on the Office of Textiles website:
http://otexa.ita.doc.gov/fedreg/finaslfr.stm.
Textile Industry Gets More Promises From Bush On Trade
The U.S. textile industry and its supporters in Congress have extracted a far-ranging, nine-point
commitment from the Bush administration to address international trade issues that are contributing
to the industry’s severe economic problems. Letters from Commerce Secretary Donald L. Evans to
members of the Congressional Textile Caucus say President Bush recognizes the “competitive
challenges” facing the industry and promises to work closely with members of Congress “to level the
playing field for our industry internationally.” The program outlined by Evans says the
administration will:
1. Work aggressively to pursue the opening of foreign markets to U.S. textiles and apparel
in any future trade agreements, making reciprocal market access in the textile and apparel market a
priority in trade.
2. Place high priority on enforcing existing trade agreements and closely monitor foreign
textile
trade barriers.
3. Resist efforts on the part of some developing countries to accelerate the textile quota
phase-out now scheduled to be completed by 2005, noting that the Agreement on Textiles and Clothing
covering quotas was carefully balanced to provide the U.S. industry with a gradual transition to
eventual removal of all quotas.
4. Help U.S. textile companies take advantage of the benefits of U.S. tariff preference
programs, including the Caribbean Basin Trade Partnership Act and the African Growth and
Opportunity Act. This will emphasize requirements to use U.S.-manufactured yarn and fabrics.
5. Conduct market promotion programs with a variety of trade shows, seminars and other
events under the Commerce Department’s Export Promotion Program.
6. Combat illegal textile transshipments by strengthening customs enforcement both under
U.S. Customs laws and in connection with any future trade agreements, ensuring that they include
clear and enforceable rules of origin.
7. In connection with the administration’s program to assist Pakistan in return for its
support of the anti-terrorist program, to work with Congress to minimize the impact of any such
efforts on the U.S. textile and apparel industry.
8. Expand the Trade Adjustment Assistance Program to better address the needs of textile and
apparel workers who lose their jobs as a result of international trade.
9. Enforce anti-dumping and other trade remedy laws generally and on behalf of the textile
industry in particular.
While the Evans letter outlines a comprehensive approach to addressing textile trade issues,
much of what is contained in the letters depends on just how diligent and effective the
administration will be in following through on its promises and to what extent Congress will go
along with them.
OSHA Agrees To Reporting Changes
An agreement between the National Association of Manufacturers and the Occupational Safety
and Health Administration (OSHA) to modify new reporting rules, which go into effect this month,
incorporates some changes supported by the textile industry. Key among the changes is an agreement
that during the first 120 days after January 1, OSHA compliance officers will not issue citations
for violation of the new rules if employers can demonstrate they are making a good-faith effort to
comply. OSHA also agreed to clarify its definition of work-related injuries. The agreement does not
affect OSHA’s earlier decision to delay implementation of three other provisions of the rule for at
least a year. Those provisions include criteria for recording work-related hearing loss, the rule’s
definition of musculoskeletal disorders and the method for reporting such disorders. Additional
information about the new reporting rules is available on OSHA’s website: www.osha.gov.
Editor’s Note: Blending the best of Textile Industries and Textile World, the new Textile World
will continue to publish James A. Morrissey’s Washington Outlook column.
Accredited by the U.S. Congress Periodical Press Association, Morrissey has reported
extensively on Washington developments affecting the textile industry for more than 30 years.
January 2002
Bowling Green Spinning
Winding And TwistingBy Jim Phillips, Executive Editor Bowling Green Spinning
Investing for flexibility in the combed-cotton ring-spun market In an era in which
the most common comments about textile manufacturing in the United States tend to be moans about
business conditions and the continuing siege by imports, a few companies are quietly adapting to
the requirements of the world marketplace and positioning themselves to take advantage of available
opportunities.Certainly, some of these companies are large Fortune 500-sized enterprises, the names
of which are household names throughout America. But many are relatively small, family-owned
businesses that focus on innovation and the flexibility to be nimble-footed in production, delivery
and service. Bowling Green Spinning Company, a one-plant, combed-cotton ring spinner in Bowling
Green, S.C., is just such an operation.A walk through the Bowling Green plant, which is located a
few miles south of Gastonia, N.C., reveals an operation that has an eye for efficiency and
effectiveness. The plants venerable roving and spinning frames models from Saco Lowell, Whitin and
Zinser have been meticulously maintained and upgraded over the years. While not the latest in
high-technology yarn-prep machinery, the equipment more than adequately addresses the needs of
Bowling Green Spinning and its customers. But where the company really shines is at the beginning
and end of the yarn-manufacturing process. It is in these areas that Bowling Green has invested
considerably over the past few years and can be considered as high-tech as just about any plant in
the country. Staying On Top While Keeping In LimitsOur sole product is combed cotton,
ring-spun yarn, said Daniel S. LaFar III, president of the company. We have carefully maintained
and upgraded our machinery over the years, and we feel it provides us with exactly what we need at
the moment. We have looked at other spinning options, but we felt that our objectives were better
served by focusing on other areas of the process.Indeed, when LaFar and his father, LaFar
Industries Chairman, Dan S. LaFar Jr., examined the production process from top to bottom, they
came up with a clear-cut plan that would modernize the plant within the limits of the companys
budget and provide the necessary improvements to keep the company on the cutting edge of
quality.
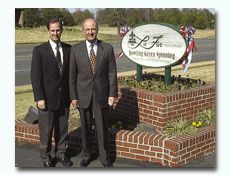
Daniel LaFar III (left), president, and Dan LaFar Jr., chairman, have made flexibility the
cornerstone upon which the success of Bowling Green Spinning Co. is built. The primary
objective of the company is to be highly flexible in order to maintain the capability of meeting
the demands its customers. The bulk of Bowling Greens product line is used in the knit apparel
market, and the companys yarn is prominent in the offerings of some of the worlds foremost names in
fashion.If there is a word that describes our company, its flexibility, the younger LaFar said. We
decided to focus on a specific area of competence and serve that market to the best of our ability.
That enables us, within the framework of our core competency, to be as flexible as possible in
meeting the needs of our customers. We feel like trying to be all things to all people would be a
weakness for us. It would cause us to spread ourselves so thin that we could not adequately serve
the market we serve best.To that end, the company, over the past few years, has divested itself of
a rayon operation and discontinued open-end spinning.When we looked at upgrading machinery, it
became apparent that our needs and those of our customers would best be served by looking at the
front and back of the process. So we have concentrated on opening and winding.We havent
over-leveraged ourselves, LaFar said. Weve upgraded a little at a time. Obviously, we would like to
upgrade the whole plant overnight, but prudence demands otherwise. Opening And Winding
Upgrades
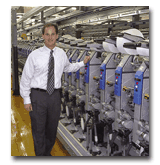
The first step of the process was upgrading opening and cleaning equipment. Bowling Green
installed a Cleanomat CVT system from Charlotte, N.C.-based American Truetzschler Inc., as well as
a Truetzschler Dustex DX dedusting machine.We eliminated about five steps in the opening and
cleaning process with the installation of the equipment from Truetzschler, LaFar said. We felt like
we had been throwing away a lot of good fiber, so it made a great deal of sense to upgrade and
become more efficient in this process.In winding, an older series of machines was replaced by new
Orion-series winders from Charlotte-based American Savio, part of the Itema group of companies
based in Italy. The Savio machines are manufactured in Italy by Savio Macchine Tessili.We were
spending a great deal of money in maintaining the older machines, LaFar said. There comes a time
when you have to make sure youre getting a return on what you are spending.We felt, as well, that,
as the last process in the plant, we had to put the yarn in the most presentable package possible,
verify the reliability of the package, and ensure it is defect-free. The combination of Orion
winders from Savio and Loepfe clearers would do just that.The Orion series from Savio is among the
newest generations of automatic winders on the market. It features a computer-aided package that
maintains constant control and adjusts yarn tension throughout the winding process.Impressed with
the offerings from other companies as well Murata and Schlafhorst, in particular Bowling Green made
its final determination based on the dual-lot availability of the Orion winders.Daniel and I, along
with Robert Montgomery [plant manager] saw several plants with the Orion installed in Italy. The
quality, speed and control were impressive, said the elder LaFar.Added the younger: Our machines
represent Savios only dual-lot stand-alone machine installation in the United States. We do not
link spinning and winding. It limits our flexibility. That was the real selling point to the Savio
machine. It enabled us to maintain flexibility in manufacturing. We can use two yarn counts on the
dual-lot machines and dedicate any number of spindles to those separate counts.Bowling Green
installed six Orion winders, three of which were the dual-lot machines.As weve said before, it all
comes down to flexibility for us, LaFar said. There will always be a certain percentage of goods
that will change quickly because of fashion. It is our goal to be able to adapt to those changes
and help our customers get products to market quickly.While Bowling Green Spinning is a supplier to
a number of noted brands, the company is also positioning itself as a supplier to a number of the
quick response, foreign-sourced programs, LaFar said.We feel our flexibility allows us to compete
in this arena very favorably, he said. Made-To-Order CapabilityAs a result of the companys
dedicated quest for flexibility, Bowling Green Spinning maintains almost no inventory. Were almost
a made-to-order company now, LaFar said. Thats the thing that will continue to set us apart being
able to quickly respond to the needs of our customers with a quality product that few others can or
will produce.As a small, stand-alone company, however, Bowling Green considers the worlds economic
and political climate to be of utmost importance. Recent trade concessions to Pakistan in exchange
for military privileges in the war on terrorism concern the company, as does the phase-out of
quotas in 2005. But both of the LaFars are confident that Bowling Green will continue to carve out
its niche and remain successful in the face of increased competition.There will always be a niche
as a high-quality, quick-turnaround, quick-response supplier, LaFar said. And that is exactly what
we are. New Winding Equipment Improves QualityIn the high-technology yarn preparation arena,
news is dominated by the latest offerings of new spinning technology.Obviously, any process that
speeds both the production and quality of yarn deserves attention. But the methods and techniques
of converting roving to thread arent the only determining factors of production quality and
efficiency. Often overlooked are the automatic winding machines and the accompanying clearers that
encompass the final stage of the spinning process.Ultimately, the winding stage is the final
opportunity to inspect and correct material for defects, as well as for creating a vehicle for
effective presentation of the yarn to customers.
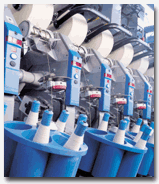
Savio introduced its Orion series of winders at ITMA 99 in Paris. That introduction,
according to one Savio executive, changed the rules of the game. Savio developed the Orion based on
a thorough analysis of customer needs, the company said. The aim was to improve the total quality
of the wound package, reduce overall process costs and increase manufacturing flexibility.At ITMA
in Paris, the Orion was introduced in two models, E and I. The Orion E is an independent winding
machine, and the Orion I has an automatic bobbin loader than can be linked to spinning frames. The
Orion series is also available in a dual-lot configuration in which two separate yarn counts can be
wound on any number of dedicated spindles. The frame for both models is available in six- or
eight-head sections. The number of heads per machine ranges from a minimum of six to a maximum of
64 in steps of two. Take-up speed ranges from 400 to 2,000 meters per minute (m/min). Now, with
worldwide acceptance of the Orion design, Savio, a unit of the Itema Group in Italy, has introduced
two additional models, the Orion M and the Orion L.Both encompass the same features as the original
Orion models but have different levels of support automation. The Orion M is an automatic winder
with manual bobbin feeding and manual package doffing. The L model has manual bobbin feeding as
well, but includes automatic doffing.Another machine one that was the talk of the recent 7th OTEMAS
in Osaka, Japan is the new 21C Process Coner from Japanese manufacturer Murata (See Spinning In
Control,
TI, December 2001).One of the key issues of the new Muratec brand winder is its Perla
system for reducing hairiness, said Bill Gray of Murata of America Inc., Charlotte, N.C.The new
Perla Hairiness Reducing System comes in both mechanical and air derivatives. The Perla-A, an air
system, can be used in conjunction with Muratas tension-control system to reduce hairiness at up to
1,800 m/min. The Perla-D system employs a disc-type design and can operate at up to 1,200 m/min.
The D system shows a higher hairiness-reducing effect than the A model, according to Murata
executives.Of the other major manufacturers of winders, Schlafhorst has as its flagship the
Autoconer 338, which, according to the company, features constant yarn tension, driven by the
companys balloon controller, electromagnetic yarn tensioner, and Schlafhorsts proprietary Autotense
yarn tension sensor. SSM Schr Schweiter Mettler AG, Switzerland, features among its winding
offerings: the PW1-W preciflex precision package winder for filament yarns and silk; and the CW1-1
cone-to-cone winding machine for weaving, warp knitting, and circular knitting operations. New to
the market for American Sahm Co. LLC, Greenville, S.C., is the 240E winder targeted toward flat and
circular loom warp packages, as well as the 2000E take-up winder that can be used to retrofit most
spinning lines. Barmag Spinnzwirn, Germany, has developed the babyASW900 winder. Compared with the
conventional ASW winder, its dimensions are significantly smaller. It can especially be used for
winding up BCF as well as PP-FDY and POY yarns.An oft-overlooked element in the effectiveness of
winders is the technology for clearing defects. The Loepfe Yarnmaster® clearer detects foreign
fibers, neps, short thick places, long thick places and thin places as well as splices. A
long-standing offering in the area of clearers is the Uster® Quantum Clearer from Zellweger-Uster,
Switzerland.
January 2002
Making The Grade
U.S. Colleges and universities are constantly re-evaluating textile programs to meet the needs of a changing industry.
By Rachael S. Dunn, Associate Editor and Jim Phillips, Executive Editor
The need for well-trained men and women to meet the demands of a growing textile industry was the cornerstone upon which the first textile programs at universities throughout the United States were founded more than a century ago.
In the intervening years, the face of the U.S. textile industry has altered dramatically, but the need for qualified, well-educated individuals to assume leadership roles has remained constant. To keep pace with the dynamic nature of the industry, colleges and universities have found it necessary to change the curricula taught to prepare individuals more adequately for careers in an industry that is global in scope, and more technical in nature.
“Years ago, Clemson University [Clemson, S.C.] taught courses such as loom fixing and the fundamentals of spinning and weaving,” said Louis P. Batson, Jr., chairman of the Louis P. Batson Co., Greenville, S.C., 1948 Clemson graduate and an emeritus member of the university’s Board of Trustees. “Today, you see a lot more of the young people graduating with degrees in polymer science, design and marketing. With the growing prevalence of niche markets and specialized products in the U.S. textile industry, the colleges and universities are offering more diverse programs in order to meet the needs of the industry and provide more opportunity for graduates.”
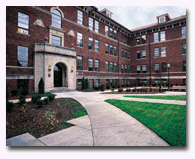
Charles Little, president of the Yarn Sales Division, Mount Vernon Mills, Greenville, S.C., a 1978 graduate of North Carolina State University (N.C. State), Raleigh, N.C., and president of the North Carolina Textile Foundation, agreed. “Twenty five years ago, the emphasis was specifically on textile manufacturing training. Today, there is a much greater diversity in course offerings. Chemistry, engineering, design and management degrees account for as many degrees at N.C. State as basic textile technology, if not more.”
To assist the universities in keeping pace with the needs of the industry, Little said, the North Carolina Textile Foundation donates more than $1.3 million per year to the schools to fund scholarships, support new facilities and provide tools for the recruitment of outstanding high school graduates.
Doug Ellis, chairman of Southern Mills, Union City, Ga., and a past president of the American Textile Manufacturers Institute (ATMI), earned a textile degree from the Atlanta-based Georgia Institute of Technology (Georgia Tech) in 1963. Ellis told Textile World the experience was invaluable in preparing him for a leadership role in the industry. “I was able to learn in a very short time what it would have taken me years to learn otherwise. Today, the experience can be just as valuable to those looking for a career in the industry. We have a very, very broad industry, and there is still a need for graduates with traditional textile manufacturing knowledge. But there is also a need for those with knowledge about synthetic fiber processes, polymer chemistry, nonwovens and the other various segments of the industry. Plus, graduates today need to be well-versed in a number of other areas, such as general management, accounting, engineering, marketing, statistics and other areas.
While there seems to be considerable and justifiable confidence in the quality of education provided at U.S. textile schools, a lingering question in the minds of many prospective students concerns the wisdom of entering an industry many consider to be declining. Is this an issue that should preclude young people from seeking a textile-based education and ensuing employment in the industry?
“There will always be a textile industry in the United States,” Batson said. “No doubt, it has changed over the years and will evolve even more in the years to come. It used to be that it was a labor-intensive industry. Now it is a capital-intensive industry. Management, marketing, chemistry and engineering skills are vital today. I would heartily encourage anyone considering a textile education to pursue it. There is still a lot of opportunity out there.”
History
The diversity of offerings at textile schools today can trace its roots to innovative programs founded more than a century ago. In his book, A Century of Progress The Textile Program, North Carolina State University, 1899-1999, Dr. Gary N. Mock chronicles the development of N.C. States textile program. Mock addresses, as well, the beginnings of textile education in the United States.
The initial programs the Lowell School for Practical Design, established in Boston in 1872; and the Rhode Island School of Design, founded in Providence in 1878 taught only fabric design, according to Mock.In Philadelphia, textile business owners wanted to develop a center of instruction to teach design and fabric styling so they could compete with imported fabrics. On January 10, 1895, Theodore C. Search, the then-vice president and chairman of the Instruction Committee at the Pennsylvania Museum and School of Industrial Art,
spoke to the 30th annual meeting of the National Association of Wool Manufacturers. His speech focused on the bankrupt policy of trade protection and tariffs and the way to overcome the competitive advantage of imports. At the time, more than $100 million per year of imported textiles were coming into the country despite a 40-percent tariff. I am here tonight, not to discuss the tariff, as that is a question already settled by our people, Search said, but I am here to make a plea for textile education in the manufacture of textiles. These schools, he said, abound in
France, Germany, Belgium, Switzerland and England.Southern cotton farmers and mills were
instrumental in the establishment of textile programs in the South. Daniel Augustus Tompkins, an
engineer and builder of cotton mills, proposed the creation of a private school in South Carolina.
He was later convinced that textile education could be supported by public funds. He went on to
establish the textile program at Clemson in 1898, and supported the establishment of a program at
the North Carolina College of Agriculture and Mechanic Arts, known today as N.C. State.The first
textile engineering students arrived at the Atlanta-based Georgia Institute of Technology in 1899.
The Pittsburgh industrial millionaire Aaron French donated $15,000 to the university, allowing the
creation of the Aaron French School of Textiles.From these early beginnings, textile education in
the United States has developed and expanded. Today, textile institutions are not only providers of
trained professionals for the industry, but also important contributors to textile innovation and
development through their comprehensive research programs.School ProgramsThere are many
institutions across the United States teaching a variety of textile and textile-related curricula
(See table at end of story). Programs range from highly technical engineering and polymer
chemistry degrees to design and merchandising education. The following highlights some of the
programs offered.N.C. State offers a comprehensive program covering both the technical and design
aspects of textile education. Degrees in chemistry, engineering, textile technology, management and
design are available at both the undergraduate and graduate levels.The Anni Albers Scholars Program
is a new dual-degree program offered at N.C. State. The program was established in 2000 to provide
students with simultaneous education in design and in textile and apparel technology. Students in
the program earn two undergraduate degrees a bachelor of art and design, as well as a bachelor of
science in textile technology. The university hopes graduates of the program will benefit from
creative flexibility and design skills with extensive knowledge in textile technologies.
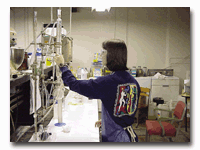
Mock, who is also a professor at N.C. States College of Textile Engineering, Chemistry and
Science, said, We are constantly looking at our programs and evaluating what we are doing, where
are we going, and what we can do to support the needs of the industry. Mock mentioned protective
garments and medical textiles as big areas of current research at N.C. State. He also thinks
educating students in design,sourcing and testing, and quality control is important in supporting
the apparel industry in the future.Georgia Tech offers undergraduate degrees in textile and fiber
engineering, polymer and textile chemistry, and textile enterprise management. Masters degrees and
doctorate programs are also available. Dr. Fred Cook, chair and professor of the School of
TextileandFiber Engineering, said, Companies value a textile education in that it gives the
graduate entering the industry the necessary nomenclature and scientific/engineering process
information to be of immediate use to the hiring company without lost training time.Cook continued,
The general industry estimate is that it takes two years to bring a generic major up to the same
use level as an entering textile-related major, at a support cost to the hiring company of
approximately $200,000 per year.From the summer of 2000 through the spring semester of 2001,
Georgia Tech awarded 31 textile-related degrees at the bachelor, master and Ph.D. levels. The
average starting salary for all undergraduate students in 2001 was approximately $45,000. Employers
included such companies as KoSa, Honeywell, Shaw Industries, and Southern Mills. Masters and Ph.D.
graduates were employed by 3M Corp., DuPont and Ciba Vision Products, among others.Cook added that
by completing a four-year textile degree, the graduate has demonstrated a dedication to the
industry that a generic major has not, and thus is more likely to remain with the industry for the
long term.Georgia Tech shares some resources lab courses, professors and recruitment efforts with
Southern Polytechnic State University (SPSU), Marietta, Ga. Dr. Walter Thomas, head of the
Apparel/Textile Department, said that SPSUs apparel/textile engineering technology degree provides
more hands-on, applied training than programs at other universities. Thomas said there is a
tremendous demand for SPSU textile graduates, despite the difficulties the industry is facing. He
also said starting salaries for new graduates are between $5,000 and $6,000 higher than they were
last year.N.C. State, Georgia Tech and Auburn University, Auburn, Ala., offer the only engineering
programs in the United States accredited by the Accreditation Boards for Engineering and Technology
(ABET).Dr. Peter Schwartz, professor and dean of Auburns Department of Textile Engineering, said,
The health of textile education is an important issue in Alabama. In order to assure the continued
viability of textile engineering at Auburn, we are in the process of establishing a Futures
Advisory Group, consisting of faculty, students and industry representatives, to advise the
department on how to best position itself to meet the challenges we will face in the next decade
and beyond. Philadelphia University, Philadelphia, offers a range of undergraduate and graduate
degrees in engineering, design and management-related programs at its School of Textiles and
Materials Technology. The college recently added an on-line masters of business administration
(MBA) in textile and apparel marketing to its offerings. The course can be completed in 13 months,
or students may choose to take courses at a slower pace. Armed with a computer and Internet access,
busy working professionals with time and location issues can complete course work on-line when its
convenient with work schedules.Philadelphia Universitys Center of Excellence in Digital Ink-Jet
Printing, directed by Professor Hitoshi Ujiie and coordinated by Professor William Wolfgang, allows
students and professors to explore and research textile design initiatives based on digital
printing technologies. The center has Mutoh, Colorspan, Hewlett-Packard and EnCad equipment.
Funding comes from annual subscriptions by machinery manufacturers, ink developers, and textile
manufacturers.The New York City-based Fashion Institute of Technology (FIT) offers textile-related
business degrees through its School of Business and Technology, as well as design degrees through
the School of Art and Design. FIT prepares students for various fashion careers, including fashion
design, fabric styling, textile design, fashion merchandising management and textile development
and marketing. Prominent alumni include Calvin Klein and Michael Kors.FIT houses the Peter G.
Scotese Computer-Aided Design and Communications Center. This facility offers students access to
state-of-the-art computer equipment for textile design. The Gladys Marcus library includes a
special collection of textile design archives, and the museum at FIT has the worlds largest
collection of textiles dating from the 18th century, according to the school.The Institute of
Textile Technology (ITT), Charlottesville, Va., was founded in 1944 by textile industry leaders who
saw a need for individual companies to join forces in collective support of a private educational
and research institution. ITT teaches graduate students, conducts research and offers a
comprehensive textile information service. The institute is also home to one of the largest
collections of English-language textile information in the world the Roger Milliken Textile
Library.To further provide value to industry, ITT recently established the Center for Textile
Economic Competitiveness. The center combines innovative research with Collaborative Consultancy.
According to ITT, Collaborative Consultancy involves proficiently transferring solutions from
research into practical industry applications that lead to tangible results. ITT believes this
merging of research and consultancy is the key to creating added value from new knowledge.Many of
the universities including N.C. State, Clemson, ITT, North Carolina Center for Applied Textile
Technology (NCCATT), and Auburn also have continuing education or professional training courses.The
Madren Conference Center on the campus of Clemson University hosts a wide range of seminars every
year to further train or enhance the knowledge of people in the industry. Medical textiles, carpet
manufacturing and textile printing are just some of the topics that are covered.Dr. Richard V.
Gregory, director, School of Materials, Science and Engineering, said, The focus of the textiles,
fiber and polymer science program at Clemson University will be on industrial, technical and
medical textiles; that is, on advanced materials made from fibrous structures.NCCATT Belmont, N.C.,
has resources to cater specific courses or seminars depending on individual or company needs.
According to Gwen Perkins, dean of development and special programs, NCCATT has well-equipped
textile labs, high-tech computer labs and facilities to host conferences.Research ConsortiumsThe
National Textile Center (NTC) is a research consortium of six universities: Auburn University;
Clemson University; Georgia Tech; N.C. State; the University of Massachusetts, Dartmouth; and
Philadelphia University. These six institutions share human resources, equipment and facilities to
serve the U.S. fiber/textile/fabricated products/retail complex. NTCs goals include: research
discovering, designing and developing new materials, innovative and improved manufacturing, and
integrated systems essential to the success of a modern U.S. textile enterprise;education training
personnel, establishing industrial partnerships, and creating transfer mechanisms to ensure the
utilization of technologies developed; andpartnership strengthening the nations textile research
and educational efforts by uniting diverse experts and resources in unique collaborative
projects.Georgia Tech has established a Polymer Education and Research Center (PERC) with the
mission of providing the highest-quality multidisciplinary education and research opportunities in
polymer science and engineering. PERC is a joint program involving six schools on the Georgia Tech
campus: Chemical Engineering, Textile and Fiber Engineering, Material Science and Engineering,
Chemistry and Biochemistry, Electrical and Computer Engineering, Mechanical Engineering, as well as
the Georgia Tech Research Institute (GtrI). PERC is committed to assisting and providing leadership
for polymer and related industries.Industry CooperationThe Textiles and Nonwovens Development
Center (TANDEC), Knoxville, Tenn., is a cooperative partnership between the ExxonMobil Chemical
Co., Irving, Texas, and the University of Tennessee (UT), Knoxville. TANDECs primary goal is to
provide quality research, educational opportunities and service in the field of nonwovens and
textiles.The partnership began in 1983, when Exxon decided to move a meltblown pilot line from its
Baytown Polymers Center to UT. Exxon wanted the line to be available to the academic community, as
well as to the nonwovens industry. Expansion of efforts continued, and equipment was added and
upgraded, allowing TANDEC to become one of the leaders at UT in the development of new patents.A
National Science Foundation (NSF) grant for a maximum of eight years with matching funds from the
State of North Carolina and the nonwovens industry, enabled N.C. State to establish the Nonwovens
Cooperative Research Center (NCRC) in 1991. NCRC serves the nonwovens industry through fundamental
and applied research. The center has developed core and non-core research, and participates in
technology-transfer activities. Support is still provided by the State of North Carolina, from
industrial members and affiliates of the center, and by companies with research or developmental
needs. Member companies include 3M Corp., Cotton Incorporated, Dow Plastics, DuPont, Fleissner,
KoSa and ProcterandGamble, among others.Importance Of Education To The Textile IndustryThere is no
doubt that the numerous textile schools and colleges have contributed significantly to the growth
and development of the textile industry over the years. In an era in which quality is no longer an
option but a steadfast requirement for remaining viable, the consummate knowledge of textile
processes brought to bear by the graduates of textile schools has been invaluable.Also, it is
well-known that the key to success for the U.S. industry over the next few decades will rest on the
ability of its people to innovate and deliver new products that meet the changing needs of the
marketplace. Remember, said Batson, that the United States is still the fashion capital of the
world. The textile industry must continue to develop the capability to meet the high-end demands of
the consumer.Peggy Earle, owner of the childrenswear company Hartstrings Inc., and a 1974 graduate
of Cornell University, said, There are many, many jobs in the apparel industry where an individual
would benefit from having a good, solid background in textiles. To that end, the industry will
continue to rely on the innovative thinking and new ideas that emerge from the nations colleges and
universities.SchoolsAuburn UniversityClemson UniversityColorado State UniversityCornell
UniversityFashion Institute of Tech.Florida State UniversityGeorgia Institute of Tech.Institute of
Textile Tech.Iowa State UniversityKansas State UniversityLouisiana State UniversityNorth Carolina
State U.N.C. Center for App. Textile.Ohio State UniversityPhiladelphia UniversitySouthern Poly.
State U.Syracuse UniversitytrI-Princeton UniversityTexas Tech UniversityTexas Women’s
UniversityUniversity of AlabamaUniversity of GeorgiaUniversity of Mass.University of
MissouriUniversity of North TexasUniversity of Rhode IslandUniversity of TennesseeUniversity of
WisconsinVirginia Polytechnic InstitutePhone(334)844-4123(864) 656-3176(970) 491-5360(607)
255-3151(212) 217-7999(850) 644-2498(404) 894-2490(804) 296-5511(515) 294-7474(785) 532-6993(225)
578-2281(919) 515-3761(704) 825-3737(614) 292-8063(215) 951-2750(770) 528-7272(315) 443-2455(609)
924-3150(806) 747-3790(940) 898-2661(205) 348-6176(706) 542-4888(508) 999-8453(573) 882-7317(940)
565-2436(401) 454-6136(865) 974-2141(715) 232-2483(540) 231-6164Fax(334) 844-4068(864)
656-5973(970) 491-7975(607) 255-1093(212) 594-9413(850) 645-4673(404) 894-8780(804) 296-2957(515)
294-6364(785) 532-3796(225) 578-2697(919) 515-6621(704) 825-7303(614) 688-5565(215) 951-2651(770)
528-7454(315) 433-9688(609) 683-7836(806) 747-3796(940) 898-2711(205) 348-3789(706) 542-4890(508)
999-9139(573) 882-3289(940) 565-4348(401) 454-6320(865) 974-5236(715) 232-5042(540) 231-1697
January 2002
Congress Has Far Reaching Textile Agenda
When the second session of the 107th Congress convenes January 28 it will have considerable
unfinished business that will impact the textile industry. While an economic recovery program,
taxes and dealing with terrorism and home security will be grabbing the headlines, international
trade, tax and farm legislation will be of equal importance to textile manufacturers, organized
labor and importers.Just before Congress left for its year-end recess, the Bush administration put
forth a nine-point program designed to address some of the U.S. textile industrys economic
problems. Several of these issues will require congressional action.One of the first issues likely
to come to the forefront is a commitment from the Republican leadership in the House to enact
legislation that would require textile and apparel products qualifying for benefits under the
Caribbean Trade Partnership Act to be dyed and finished in the U.S. The House leadership promised
to deal with this issue at the earliest opportunity, so it could be attached to the first
international trade bill to be considered.Legislation that would for the first time incorporate
textiles and apparel in an Andean Nation preferential trade program passed the House, much to the
consternation of the U.S. textile industry, and is awaiting action in the Senate. Since the current
law, which does not include textiles and apparel expired in December, quick action is expected. The
American Textile Manufacturers Institute strongly opposes extending the trade preferences to
textiles and apparel, but the proposal is supported by the American ApparelandFootwear
Association.Legislation granting broad trade promotion authority to the President passed the House
by a single vote in last December, and it is pending in the Senate Finance Committee. If the Senate
makes any changes in the bill, it will have to return to the House, where there could be another
major showdown involving textile state congressmen. The bill passed the House with key support from
textile state legislators who voted for it in return for promises from the administration that it
would take steps to address textile trade problems. If those members do not feel the administration
is following through, they could scuttle the trade promotion bill.In connection with the economic
stimulus package passed by the House and pending in the Senate, the textile industry is seeking at
least a five-year tax loss carryback, repeal or reform of the alternative minimum tax and faster
depreciation for machinery.And, finally the U.S. textile industry will be lobbying hard to
safeguard the cotton competitiveness program which is part of the Farm Bill pending in the Senate.
The industry wants to eliminate the 1.25 cents per pound differential between world and domestic
prices in order for the program to be activated. ATMI estimates that repeal of the 1.25 cent per
pound requirement would save American textile companies some $50 million annually.
SheLyn Upgrades SLI-Form Color Measurement System
SheLyn UpgradesSLI-Form® Color Measurement SystemSheLyn Inc., Greensboro, N.C., has added three new products lightfastness prediction, dye compatibility and color inconstancy index to its SLI-Form® formulation color measurement and management systems.In formulation mode, SLI-Form can now predict lightfastness, evaluate dyes to see if they work well together and evaluate whether a developed color will behave properly under different light sources.Also, SheLyn has integrated two new programs to SLI-Form. The first SLI-Recipe is a laboratory information system that includes tools for tracking and managing orders, lab requests, styles, finishes, expenses and procedures, among others.e-Submit allows users to send digital color data over the Internet. SheLyn claims e-Submit can speed up the approval process for new colors by reducing response times.January 2002
PSC Introduces Perfect RF Dryers
PSC Introduces Perfect RF DryersCleveland-based PSC Inc. has introduced its line of Perfect RF (radio frequency) dryers for the textile industry. The dryers are heated from within to provide fast, uniform heating and drying in textile processing.PSC offers the dryers in standard models or in custom designs for special applications. Laboratories are available for testing and feasibility analysis of the customers application.January 2002
Burlington Files Chapter 11 Hastens New Business Model
Burlington Files Chapter 11,Hastens New Business ModelIn an effort to implement a new business
model and better serve its customers, Greensboro, N.C.-based Burlington Industries Inc. and certain
of its subsidiaries have filed voluntary petitions for reorganization under Chapter 11 of the U.S.
Bankruptcy Code. The companys new business model focuses on enabling it to introduce fabric
innovations and distinctive products to the market. Burlington is now concentrating on its Lees
Carpets business and on the performance and fabric innovations provided through the proprietary
technology developed by its subsidiary Nano-Tex LLC. As well, it will continue to improve its North
American manufacturing operations and will expand global opportunities through its subsidiary
Burlington WorldWide Ltd., Hong Kong.The petitions filed for reorganization did not include
international operations, joint-venture partnerships, Nano-Tex LLC and Burlington WorldWide Ltd.Our
business model going forward adds worldwide reach to our North American capability to provide
products, services and global solutions to our customers, said George W. Henderson III, chairman
and CEO. We are creating a more flexible and responsive company capable of meeting the diversified
and ever changing needs of our customers.The company received final court approval for $190 million
in debtor-in-possession (DIP) financing underwritten by J.P. Morgan ChaseandCo. The financing is
available to help cover operating expenses during the reorganization process.
January 2002
Honeywell Expands Spectra Fiber Manufacturing
Honeywell ExpandsSpectra Fiber ManufacturingThe specialty materials business of Honeywell International, Morristown, N.J., announced it is to expand manufacturing capacity of its Spectra® high-modulus polyethylene fiber. The need to increase capacity resulted from an increase in demand for Spectra fiber and Spectra Shield® composites.The expansion will be completed in two phases. Phase One, to be finished by the end of the third quarter 2002 and to cost approximately $20 million, includes the installation of a new gel-spinning line and additional drawing capacity at Honeywells Colonial Heights, Va., facility.Phase Two, still in the planning stages, involves the construction of a new, state-of-the-art plant. Locations in Europe, Asia and the United States are all being considered.January 2002