Peter Dornier, Owner OfLindauer Dornier, Passes AwayDipl. Ing. Peter Dornier passed away at his home in Lindau, Germany, on January 28, 2002. He was 85. Dornier was the sole owner of Lindauer Dornier GmbH, the largest producer of weaving machines in Germany.Dornier was the second son of aircraft pioneer Dr. Claude Dornier. He began his career in 1944 as anairplane design engineer in his fathers company.For his achievement in design, he received, along with other leading engineers, the 1943 Trophy of Honor of the Carl-Lilienthal-Association of Aeronautics, Germany.Dornier established Lindauer GmbH in 1950. In the early 1960s, Dornier started a second manufacturing program consisting of specialty machinery for the textile and plastic foil industries.Dornier also found time to develop 50 patents that were registered in his own name.In 1978, he expanded the company with the founding of the American Dornier Machinery Corp. in Charlotte, N.C.In 1985, Daimler Benz AG acquired majority ownership of the Dornier group of companies, with Dornier taking full ownership of Lindauer Dornier GmbH.In 1986, he created the Peter Dornier Trust Fund, a benefactor to social and environmental improvements in the community.After 50 years as head of the company, Dornier handed over management of the company to his son, Peter D. Dornier, at the beginning of 2001.March 2002
Imports Show First Decline Since 1988
By James Morrissey, Washington CorrespondentReflecting the soft U.S. economy and what many economists describe as a major soft goods recession, textile and apparel imports for the first time since1988 declined last year. U.S. Commerce Department data for 2001, show that textile and apparel imports of 32.8 billion square meter equivalents were down by 0.6 percent from 2000. While the decline was minor, it reflects a reversal of a trend that had seen a steady annual rise of both textile and apparel imports. Of particular significance was a 9 percent drop in apparel imports from Mexico, which in recent years had increasingly been displacing imports from the Far East and Orient, and under terms of the North American Free Trade Agreement (NAFTA) generally contained U.S. fabric and yarn.Running counter to the overall downward trend, imports from Pakistan, South Korea, Cambodia and Indonesia showed significant increases and nearly offset the decline in imports from Mexico and the Caribbean.According to trade officials at the American Textile Manufacturers Institute (ATMI), Asian nations have become more price-competitive as a result of currency devaluations, and they are eating into what for some time had been a competitive advantage of NAFTA countries.The year-end data also show that U.S. exports of textiles and apparel measured in dollars, also declined, reversing a 15-year trend of annual increases. Textile exports of $10 billion were down 4.3 percent and apparel exports valued at $6.5 billion were off 20.3 percent. This resulted in a record-breaking annual trade deficit of $62 billion. As was the case with imports, much of the decline in exports is attributed to less trade with Mexico and the Caribbean Basin nations.
Lovejoy Develops New Couplings Line
Lovejoy Develops New Couplings Line
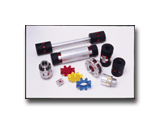
Downers Grove, Ill.-based Lovejoy Inc. has introduced new curved-jaw (CJ) flexible elastomeric and jaw in-shear (JIS) elastomeric couplings.The CJ couplings line has been expanded to include larger sizes, including hub outside diameters ranging from 30 through 420 millimeters (mm). It can accommodate applications driven either by electric motor or by internal-combustion engine, with nominal torque ratings.The new JIS couplings line has six larger sizes extending maximum bore up to 9 inches. Lovejoy also has introduced a JIS spacer-type series intended as non-lubricated, drop-in replacements for grid spacer couplings.March 2002
DuPont Forms TextilesandInteriors Subsidiary
DuPont FormsTextilesandInteriors SubsidiaryWilmington, Del.-based DuPont has formed DuPont TextilesandInteriors (DTI), a subsidiary that becomes the largest integrated textile fiber and interiors company in the world, according to DuPont.DTI will comprise two businesses, each with subgroups. TextilesandInteriors will include apparel, home and industrial, and flooring. Intermediates will include nylon; Terathane® and polyester intermediates, specialties and joint ventures.Upon formation of this subsidiary, we will become the largest player in the worldwide textile and interiors business with a portfolio of brands that is second to none, and it will enjoy the number-one position in the six markets that comprise 75 percent of its revenue, said Richard Goodmanson, executive vice president and COO, DuPont, and chairman, DTI.With the formation of the new subsidiary come new leadership appointments: DuPont ApparelandTextile Group Vice President and General Manager Steve McCracken Textiles and Interiors; and DuPont Chemicals and Polyester Group Vice President and General Manager George MacCormack Intermediates. Under McCracken and MacCormack, subgroups will be led by the following: Bill Ghitis apparel; Alan Wolk flooring; Carol Gee consumer brands; Dave Trerotola home and industrial; and Ken Wall nylons, intermediates and specialties.The new company will have the largest research and development budget in the industry, with $170 million earmarked for product and process innovation in 2002, according to DuPont.March 2002
Springfield Introduces Airo-Soft Hydrophilic
Springfield IntroducesAiro-Soft HydrophilicSpringfield Occupational Apparel, Jericho, N.Y., has enhanced its woven and knitted Airo-Soft workwear fabrics with a hydrophilic finish that wicks moisture away from the skin to evaporate on the fabric surface. The durable, easy-care fabrics also have soil release properties.Airo-Soft Hydrophilic workwear fabrics feel great and look much better at the end of the workday, even under extremely warm, humid conditions, said Frank Reese, vice president. Plus, the fabric maintains the strength, color retention and high wearability standards that are imperative in all Springfield fabrics.The fabrics are available in a variety of weights and can be dyed to customer specifications.March 2002
Quality Fabric Of The Month: Stretching To Fit
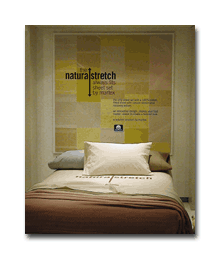
Incorporated, New York City.
Now, WestPoint Stevens Inc., West Point, Ga., is using the technology in the home fabrics arena. The company’s Natural Stretch fitted sheet, developed in response to consumer demand for better-fitting sheets, is marketed under its Martex brand of bed and bath products. The new sheets are the only stretch sheets available that contain no man-made or elastomeric yarns.
Partnering Achieves Results
Cotton Incorporated and WestPoint Stevens collaborated to adapt the stretch technology for use in sheets. It all began with a meeting between product development and marketing personnel from
Cotton Incorporated and a cross-functional development team from WestPoint Stevens that included product development, manufacturing and advertising management, according to David Earley, Northeast
regional manager of global product marketing, home furnishings, Cotton Incorporated, Cary.
“It was a good situation for all of us,” said Earley. Cotton Incorporated gave WestPoint Stevens a six-month exclusive license to develop the product. Using machinery already in place in its mills, WestPoint Stevens conducted several trials to achieve the degree of stretch and recovery desired for the company’s sheeting application. The results were beneficial to both companies, giving WestPoint Stevens a new product and extending the research and development begun by Cotton
Incorporated.
A combination of weaving and finishing technologies is used to give lasting stretch properties to cotton without the addition of man-made materials. The trick has been to produce a yarn that relaxes back to its original state after repeated and/or prolonged stretching and numerous washings. The recovery rate of WestPoint Stevens’ sheeting fabric — after stretching 11 percent to fit smoothly and tautly over a mattress — is 97 percent. Laundering restores the sheet to its original shape.
The first Natural Stretch fitted sheets are being shipped to select retail stores this quarter.
For more information about stretch cotton, contact Victoria Pace, Cotton Incorporated, (212) 413-8350. For more information about Natural Stretch fitted sheets, contact Toni Cauble, WestPoint
Stevens, (706) 645-4879.
March 2002
Wayne Mills Purchases Luithlen Dye
Wayne Mills PurchasesLuithlen DyeAfter announcing that it would be closing its doors, Luithlen Dye Corp., Philadelphia, was purchased by Wayne Mills Co. Inc., also based in Philadelphia. Luithlen was in business for more than 125 years. The decision was made to close the plant because it was determined the operation could no longer be a prosperous, economically viable entity in the future.Wayne Mills, Luithlens biggest customer, was presented with an opportunity to buy the operation. The sale was completed in 2 1/2 weeks.March 2002
Drive-All Launches Shiftable Gear Drives
Drive-All Launches Shiftable Gear DrivesDrive-All Manufacturing Co. Inc., Harbor Beach, Mich., has introduced a new line of DAW series transmissions. Widely varied ratios can now be combined into one drive in a standard configuration. The multi-speed transmissions can shift on-the-fly while under full load. Smaller motors and variable-speed drives may be used because the transmission maintains motor horsepower through all of the reductions and multiplies torque, thus lowering costs, Drive-All claims. Eleven different model sizes are available. The DAW is also available in a manual-shift version.March 2002
Prodescos Board Of Directors Announces Launch Of New Company Secant Medical LLC
Prodesco, Inc., founded in 1942 and a leading supplier of highly engineered fabrics for applications in the medical, aerospace, filtration and automotive markets, today announced the formation of a new company SECANT MEDICAL. As a wholly owned subsidiary of Prodesco, Secant Medical will offer its growing base of customers in the medical device and biotechnology industries dedicated resources for the design, development and manufacture of engineered fabric and composite structures. Prodesco will continue to focus on the needs of industrial markets.”Prodescos Medical Division has enjoyed significant growth over the past few years and now has an excellent worldwide reputation for supplying component structures for medical implant applications. With the launch of Secant Medical, the company will continue to be the premier developer and supplier of engineered components for use in the demanding and expanding field of Class III implants,” stated Steve Chadwick, President and CEO of Secant Medical.The following were appointed as officers of the company:Mr. Robert Sievers has been elected Chairman of the Board of Secant Medical. Mr. Sievers has been in the Prodesco organization since 1988, serving successively as Chief Operating Officer, Chief Executive Officer and Chairman of the Board. His prior experience includes a 33-year career at DuPont, capped by assignment as President, DuPont Japan, Ltd. He is a graduate of the Polytechnic Institute of Brooklyn with a BS in Chemical Engineering.Mr. Stephen K. Chadwick has been appointed President and CEO of Secant Medical. Mr. Chadwick joined Prodesco in 1992 as Chief Operating Officer and was appointed President and Chief Executive Officer in 2001. He graduated from the US Naval Academy in 1962 and served as a Surface Warfare Officer before transferring to the retired list as a Rear Admiral in 1990. Mr. Chadwick is a Director of Hitco Carbon Composites, Incorporated. In the non-profit sector he is a Director of Pearl S. Buck International and Chairman of the Annual Fund for the U. S. Naval Academy Foundation.Mr. Thomas Molz has been appointed Executive Vice President and Chief Operating Officer of Secant Medical. Mr. Molz joined Prodesco in 1995 as Marketing Director and was promoted in 2001 to Executive VP. Prior to working at Prodesco, Tom held key management and sales positions at Magnetec Corp, Mars Electronics and DuPont. He graduated from Virginia Polytechnic Institute with a BS in Mechanical Engineering and West Virginia College with an MBA.Dr. Skott Greenhalgh has been appointed Vice President and Chief Technology Officer of Secant Medical. Dr. Greenhalgh joined Prodesco in 1998 as Director of R and D and Engineering Services and was promoted in 2001 to Vice President, R and D. Prior to Prodesco, Skott was head of the Biomaterials Program at Philadelphia University and worked in R and D for Flexmedics and Pfizer. He graduated from Drexel University with BS in Mechanical Engineering and North Carolina State University with a MS in Textile Engineering and a Ph.D. in Fiber and Polymer Science.Mr. Thomas Dertouzos has been appointed Secretary, Treasurer and Chief Financial Officer of Secant Medical. Mr. Dertouzos joined Prodesco in 1995 as Chief Financial Officer and was promoted to VP of Finance in 2001. His prior experience includes Controllership and Vice President of Finance positions at ThomasandBetts, Contrologic, Inc., and Markel Corp. He is a CPA and holds a BA from Susquehanna University.Wallace M. Starke has been appointed Assistant Secretary and Corporate Counsel of Secant Medical. He is a partner at Troutman Sanders and is Prodescos Corporate Counsel.For over 35 years, Prodescos medical division has been manufacturing OEM class III implants for its customers, concentrating on items such as vascular grafts, implantable meshes, adhesion barriers, heart valve components, scaffold structures and stents. This will form the core of Secant Medicals growing business. The company has worked with leading global health care providers, including CR Bard, Boston Scientific, Edwards LifeSciences, Genzyme, Guidant, JohnsonandJohnson, Medtronic, Tyco and many others. Secant Medical will be ISO 9001 certified and an FDA registered device manufacturer. All products are produced to GMP standards.Tom Molz, COO, commented, “The establishment of Secant Medical will provide our customers dedicated, experienced resources and an even greater focus to solve the clinical needs of the medical community.””The key to our success has been our ability to provide innovative and proprietary solutions for our customers challenging design issues, adding value to the end product. We have extensive experience with numerous biocompatible, bio-absorbable and metallic fibers for many types of medical devices,” added Dr. Skott Greenhalgh, VP and CTO.About Secant Medical:Secant Medical, a privately held company headquartered in Perkasie, Pennsylvania, is an OEM developer and manufacturer of highly engineered fabric and composite structures for cardiovascular, orthopedic, neurologic and other medical applications. For more information, visit their web site at www.secantmedical.com.Contact: Tom Molz, COO(215) 257-8680, ext. 115(877) 774-2835, ext. 115tom.molz@secantmedical.com
Rapidly Changing Textiles A Double-Eged Sword
RAPIDLY CHANGING TEXTILES A “DOUBLE-EGED SWORD”The U.S. textile industry is in the midst of its darkest days, but armed with accurate information and a willingness to fight for its survival, the industry can secure a profitable future, according to Dr. Thomas J. Malone, president and COO of MillikenandCompany, Spartanburg, S.C.Malone, delivering the keynote address for the 10th Annual National Textile Center (NTC) Forum February 10 in Charlotte, N.C., said the textile/fiber/fabrication/retail complex is the most rapidly changing industrial complex in the world.However, rapidly changing is a double-edged sword in this case, he said. In the past decade, we have seen advances in our materials, technologies and manufacturing systems that could best be described as pipe dreams when we first gathered to develop a mission statement [for NTC] in 1992. The flip-side of rapidly changing is the accelerated job loss and erosion of our manufacturing base that continues in spite of these developments that are intended to make us stronger.Malone said contributing factors include escalation of imports from the Far East and the continuing devaluation of Asian currencies. However, trade agreements supposedly negotiated to benefit U.S. industry have also had a devastating effect. For example, the North American Free Trade Agreement (NAFTA), heralded as a benefit to U.S. industry, has resulted in serious overcapacity, Malone said. Since NAFTAs inception, domestic production has decreased by 6.4 billion square yard equivalents, despite considerable growth in U.S. market potential. One of three U.S. textile jobs has been lost since NAFTA was implemented.The Caribbean Basin Initiative (CBI) has the same potential impact, especially if the U.S. dyeing and finishing clause is not included in the legislation.To survive as a healthy industry, Malone said the U.S. must: block new agreements that allow duty-free foreign fabric; prevail in the CBI dye and finish issue; improve the competitiveness of both U.S. cotton and man-made fiber; and focus on differentiated products and short lead times. By Jim Phillips, Executive EditorMarch 2002