N
ew data point up an ongoing shift in overall mill strategy that’s making for a lot
smaller but increasingly efficient domestic textile/ apparel complex. Looking at size first, the
latest figures show capacity in the basic textile sector fell about 7 percent over the four
quarters ending late last year. And for more highly fabricated mill products and apparel,
comparable capacity reductions of 6 percent and 4.5 percent, respectively, are reported. These
declines were far above the 1-percent-or-so slippage noted in overall U.S. production potential
over the same period. But many of the closings involved older, relatively inefficient facilities —
and, in most cases, are leaving the industry in better competitive shape. The fact that textile
productivity has continued to improve over the past year would certainly seem to confirm this
conclusion. Still another indication of a stronger industry: U.S. mills have shown few signs of
cutting back on purchases of new plants and equipment. Indeed, according to the Institute for
Supply Management, a grassroots organization of the nation’s top purchasing executives, textile
mills actually plan to increase capital outlays for the coming year. And the same is true of
apparel producers. To be sure, the spending numbers are not nearly as robust as they were a few
years back. But they do indicate that domestic producers mean to be major players in the global
textile/apparel industries – both for now and over the long haul.
An Improving Business Outlook
There are also indications that demand will continue to edge higher as Washington puts more
emphasis on reducing unemployment. The new budget calls for billions of dollars in new job-creating
measures. Adding to this are proposals to extend federal unemployment benefits and a program to
double U.S. exports. To be sure, not all these proposals will be given the green light, but some
new moves to prop up the economy will almost certainly be approved. The big question: How much can
this help? One hint comes from the Congressional Budget Office estimates on what happened with last
year’s big stimulus package. The group figures this extra spending helped boost employment in the
third quarter of 2009 by between 600,000 and 1.6 million — enough to raise gross domestic product
anywhere from 1.2 to 3.2 percent. And similar results are likely this year if the Democrats and
Republicans can finally agree on some overall strategy. Top business analysts also are cautiously
optimistic. Thus, several polls of these leading prognosticators find all pretty much agreed on
2.5- to 3-percent economic growth for 2010. True, this won’t guarantee any significant pickup in
domestic textiles and apparel. But it will almost certainly prevent any further declines and
hopefully set the stage for some modest pickup by late in the year or early 2011. Another factor
likely to help: After a recession, consumers tend to put replacement of worn-out clothing and
linens at the top of their shopping lists.
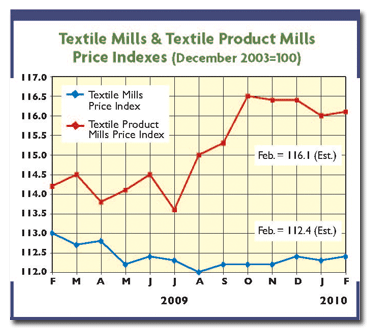
A Changing Trade Picture
The past month or so has also raised questions on future trade trends. On the export side,
the Obama administration proposes to double overall outgoing shipments to $2 trillion within five
years. Any such move would hopefully increase export promotion efforts; put more pressure on U.S.
trading partners to open up their markets; and result in more trade agreements. Imports could be
affected by upcoming Washington talks with China, which are now almost certain to include stronger
demands for upward revaluation of that nation’s currency, the yuan. And it makes sense: Many
financial analysts say the yuan is still undervalued by the same 25 to 40 percent as in 2005 when
Beijing okayed small upward adjustments. Latest U.S. import figures would also seem to confirm a
major currency imbalance. Thus, cheap Chinese textile and apparel shipments to the United States
are again accelerating — jumping 13 percent and 27 percent, respectively, in November and December
2009. True, these year-to-year comparisons are with earlier recession levels. Nevertheless, it’s a
trend that can’t be allowed to continue. Add in the fact that other nations are also pressing for
change, and some upward yuan revaluation may not be that far off.
March/April 2010