T
he nonwovens market is showing steady growth, especially for hydroentangled products,
also called spunlaced nonwovens. From the first rigid, paper-like products, production technologies
have reached a level at which products truly have a textile appearance in terms of hand, softness
and also fabric weight.
Spunlaced products are enjoying a rising interest around the world. There is growing demand
for lightweight hydroentangled products for medical and hygiene applications especially in
Asia, where the Chinese market plays a major role.
Fibers
The fibers used for the spunlace process generally have been developed especially for this
process and should be specified as such, notes Germany-based chemical company Zschimmer &
Schwarz GmbH & Co. KG, adding that appropriate fiber finishes, such as hydrophilic finishes,
must be selected. The company reports its products designed for the spunlace process show
excellent, homogeneous web formation, even at high carding speeds and low web weights, because they
have good antistatic properties and high fiber-on-fiber friction. There also is very low foam
formation in the process water and in the filtering stages.
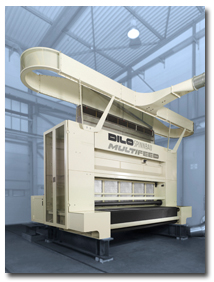
Even at highest throughputs of about 400 kg/m of working width per hour with 1.7-decitex
fibers, DiloSpinnbau’s Multifeed can provide an evenness in the cross direction of CV 2 to 3 within
the flock mat before the card infeed.
Carding
Germany-based DiloSpinnbau’s carding systems for web forming in wide working widths, made
for high web speed applications, are used as direct cards. Within the last few months, the company
has sold four carding installations of this type in working widths ranging from 370 to 510
centimeters (cm). Spinnbau developed random roller card technology and profits from many years of
experience with random and condenser rolls in card doffing systems. The technology offers
throughputs of more than 400 kilograms per meter (kg/m) of working width per hour with fine fibers,
and a fiber orientation to achieve the desired cross strength.
DiloSpinnbau reports its Multifeed offers breakthrough performance with regard to fiber
throughput and evenness. Even at throughputs of about 400 kg/m of working width per hour with
1.7-decitex fibers, a cross-direction evenness of CV (coefficient of variation) 2 to 3 within the
flock mat before the card infeed can be achieved. Machine direction evenness is controlled by an
additional apron scale that controls the card’s infeed speed. The feeder is available in working
widths greater than 500 cm.
The carding systems consist mainly of two, but occasionally three, cards, depending on
several technical features that allow high productivity and web homogeneity as well as easy
operation and maintenance. The result is high availability and production efficiency for Fleissner
or Perfojet hydroentangling production lines.
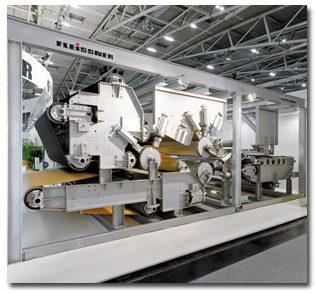
The trend in spunlaced products, made on Fleissner’s AquaJet system, is toward lightweight
nonwovens in the range of 25 to 50 g/m
2.
Lightweight Products
Germany-based Fleissner GmbH — a subsidiary of Germany-based AquaJet system manufacturer
Trützschler Nonwovens — reports there is a trend toward lightweight nonwovens in the range of 25 to
50 grams per square meter (g/m
2). This tendency is owing mostly to the constant evolution of the manufacturing lines.
Line widths range between 360 and 450 cm for wipes, and between 180 and 260 cm for cotton products
such as wipes or pads.
Thanks to throughputs of more than 400 kg/m of working width per hour for fine fibers, the
Fleissner production lines can produce at high speed with a pressure of some 80 bar in
pre-entangling, and 120 to 150 bar in the final stage. A question mark in hydroentangling always is
water consumption. Fleissner estimates average water consumption is 100 cubic meters (m
3) per hour for an average wipes production line, and some 150 m
3 for perforated products. Water reclaim in the whole circuit is at 96 percent without
backwashing; and with backwashing, only 1 percent of the water is lost.
The main products on these AquaJet lines are wipes made of viscose, polyester, polypropylene
or lyocell; cotton products; and also filter media interfaced with mechanical needling. Years ago,
to treat fiber material such as flax, hemp or even bicomponent spunbonds was unthinkable, but this
also is possible today.
New Owner For Perfojet
In December 2009, the Andritz Group, parent company of Andritz Küsters GmbH, Germany,
acquired France-based Perfojet from the Rieter Group, Switzerland. Küsters is well-known for
calenders that also are incorporated into nonwovens production lines. With this acquisition,
Andritz Küsters has moved on from being a supplier of finishing machinery alone to a supplier of
web forming machinery as well.
Andritz Küsters reports Perfojet’s spunlace and SPUNjet
® systems as well as the through-air dryers complement its own portfolio, which now
includes two bonding technologies: Küsters’ thermal bonding and Perfojet’s hydroentanglement. The
latest generation of Perfojet JETlace
® 3000 equipment is capable of producing spunlace fabrics weighing from 30 to 500 g/m
2. Perfojet claims its recent Jetlace Essentiel is especially suitable for production of
wipes from 30 to 80 g/m
2. Another recent launch by Perfojet in the spunlaid market is a new Spunjet technology
for hydroentanglement of continuous filaments, thus creating a new generation of nonwovens. It is
said to offer high fabric properties with regard to bulk, softness, drape, and tensile strength.
Finishing
Zschimmer & Schwarz develops customized products for specialized applications for the
man-made fibers, ceramics, surfactants, leather and fur industries. The company also offers a wide
variety of spin- and secondary finishes for a range of staple fiber and nonwoven applications.
The Man-made Fiber Auxiliaries Division has expanded the scope of its activities across a
broad range of applications, including nonwovens. The current focus is on developing customized
auxiliaries to match the diverse demands of a wide range of nonwoven product end-uses.
Currently, Zschimmer & Schwarz is focusing on developing its range of permanent
hydrophilic products, which are reported to offer high specification and performance to meet the
exacting demands of different spunbonds. For hygiene products, it is necessary to provide products
with exceptional toxicological data as well as to offer special additives that provide even caring
effects. According to the company, the spin- and secondary finish is essential especially for these
applications, for which the finish provides the necessary hydrophilicity and determines the end-use
as well as the properties of end products such as diapers, and incontinence and feminine products.
During spunlacing, the spin finish typically is washed off the fibers, leaving fiber
materials like polyester or polypropylene to exhibit their relatively hydrophobic characteristics.
For many application fields, a hydrophilic spunlace material is specified. Adding hydrophilic
finishes in a wet-on-wet-process after hydroentanglement eliminates the need to incorporate
hydrophilic fibers such as viscose, as has been the custom in the past, Zschimmer & Schwarz
explains.
The company’s in-house nonwovens pilot line enables products to be applied in conditions
very similar to the customer’s actual production processes. At its center of fiber excellence, new
developments are tested on a lab-line using different application systems, such as kissroller or
spraying. Direct feedback of data to the research and development department reduces development
times and leads finally to more competitive products.
May/June 2010