In a modern textile mill, filtration is very important, and with government regulations lowering
the dust level in the production area, it becomes even more so.In order to maintain a 133-microgram
per cubic meter (µg/m3) dust level in the production area, it is necessary to have a 20- to
50-µg/m3 dust level on the clean side of the filter. These dust levels are based on a particle size
of 15 microns 0.0006 inch or smaller. These are the particles that can get into peoples lungs and
cause the infamous brown lung disease. However, 15-micron particles are not the stuff one can see
flying around in a textile mill. The important and dangerous dust that needs to be taken out of the
air stream is four to six times smaller than a 50-micron human hair. It takes a good filter media
to accomplish this, especially considering the large amount of dust a textile mill produces every
day.
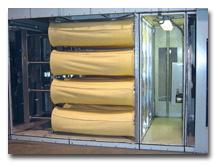
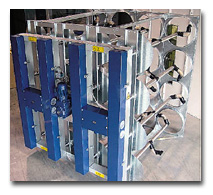
LTG Inc.’s Versadrum Filter VDF-16, shown with the filter media installed (above left) and
without the filter media installed (above right), is an example of a space-saving filtration
system.Choosing A Filter MediaWhat affects the quality of filtration The answer is: mainly, the
filter media. There are a lot of different filter media on the market these days. As a general
rule, the tighter the media, the more dust it will retain. So why isnt every textile mill using the
best filter media available The reason is a tighter media, which has smaller openings for air to go
through and has a higher pressure drop, precipitates higher operational energy costs.Reducing the
velocity through the filter media can compensate for the higher cost. In addition, a lower velocity
will help to improve filtration efficiency because fewer particles will be pulled through the
media. However, in order to lower the velocity, a larger filter is required for the same air
volume. The filter will be more expensive and will use floor space that could be used for
production.Another disadvantage of the tighter media is that it is more difficult to clean. Many
existing filters cannot be improved just by changing the media from an average media to a better,
tighter filter media. The stripper system of the filter cannot clean the new media. Therefore, it
is important to ask some key questions when buying a new filter. What will the dust level be on the
clean side of this filter Can the filter operate with any type of filter media, or does proprietary
media have to be usedA lot of mills have started using a nonwoven-type media that improves
filtration efficiency compared to the traditional media. A standard nonwoven media has an
efficiency of 99.99 percent for 6-micron particles. This efficiency can be further improved with
modifications to the standard media. But the media has a high pressure drop, and so the price to be
paid is higher energy costs. However, if the velocity through the media is kept at around 100 feet
per minute or lower, which is the velocity through most filters in opening and carding, the energy
used is not significantly higher. And compared to using two filters in series to clean, as is
customary in some textile mills, it is definitely a bargain.As already mentioned, reducing the
velocity through the media will require an increase in the filter size. A larger filter requires
more floor space, which is therefore lost for production. Most manufacturers of filter equipment
for the textile industry now offer a compact alternative to the large drum filters. These smaller
filters use half, or even less, floor space than the conventional drum filter.In production areas
that generate a lot of larger waste particles, a prefilter or preseparator is required. For a long
time, most textile mills and contractors used a condenser. Nowadays, the prefilter disc a rotary
disc with a plastic mesh and a suction nozzle has replaced most condensers, saving textile mills
valuable floor space and energy.Another trend affecting filtration is the reduction in air volume
and the increase in waste quantity. This is mainly true in opening and carding operations, and it
is a direct result of technology improvements by the machine manufacturer. In these areas, the
suction air volume per machine has increased only slightly over the years, but the machines
production capacity has increased dramatically. This means a filtration system can handle much more
material coming with the same amount of air. A textile mill in the process of buying a new
filtration system must make sure the filter can handle the increased waste.Different
RequirementsBecause different areas of a textile mill have different filtration requirements,
different types of filter media can be used in these different areas to achieve the same result. In
opening and carding, the best media usually operates with a velocity of 80 to 120 feet per minute.
In spinning and winding, the filter is usually smaller and uses less energy, because the media has
a lower pressure drop.Manufacturers of filter media for the textile industry have been, and still
are, working hard to develop new solutions to help the industry stay competitive and be ready for
tomorrows challenges as well as possible new workplace health and safety laws and regulations. The
trend is definitely towards better filtration using less floor space, while trying to make it
easier for plant personnel to maintain the equipment in the harsh plant environment in which it is
operating.Editors Note: Gerhard Seyffer is president of LTG Inc., Spartanburg. Born and educated in
Germany, Seyffer has been employed with LTG for more than 15 years in various locations and
positions.
August 2003