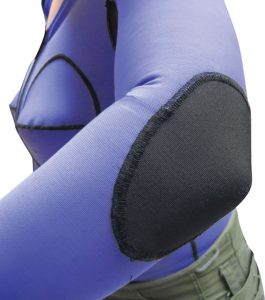
Tamarack’s GlideWear® low-friction fabric technology protects skin from friction and shear-related injuries.
By Rachael S. Davis, Executive Editor
Minneapolis-based Tamarack Habilitation Technologies Inc. was founded in 1990 to design and fabricate custom orthotics and prosthetics. In more recent years, Tamarack has focused on the development of fabric technologies that protect skin and soft tissue from injuries and wounds caused by friction and shear stresses.
Tamarack’s latest innovation is its patented GlideWear® low-friction dual-ply fabric. The low-friction property of the fabric — it has an interface coefficient of friction of 0.18 — protects skin from friction and shear, which cause injuries including chafing, rubbing, blisters, ulcers and calluses making it highly suitable for medical and sports applications. GlideWear is comprised of two 86-percent nylon/14-percent spandex knitted fabric layers that glide smoothly when rubbed together.
Because of the extremely slippery nature of the two layers, the company had to devise a way to successfully incorporate it into finished products. The solution was to prepare a “GlideWear Pre-Ply” using a water-soluble bonding agent. The pre-ply material exhibits no slip whatsoever so the two bonded layers may easily be added to a garment or other product using any traditional construction methods including sewing and welding. A final washing step dissolves the water-soluble bonding agent and activates the low-friction effect.
“The low-friction effect is due to the fabric’s design and exact positioning of the two layers against each other; no unique coatings or treatments are applied,” said Adam Erickson, manufacturing manager, Tamarack.
According to Erickson, the product evolved from Tamarack’s ShearBan® fluorinated polymer film. “We wanted a conformable, breathable, washable fabric with the same low-friction properties as our ShearBan films,” Erickson said. “Now with GlideWear, strategic friction management can be applied to textile products where our ShearBan films were not compatible.”
Currently, GlideWear is featured in wheelchair seats, burn protection garments, bike shorts and athletic socks, among other products. Stockholm-based MIPS — the innovator behind the patented MIPS Brain Protection System — recently partnered with Tamarack to develop new products designed to protect athletes’ brains from rotational forces and energies linked to brain injuries. The first product to be introduced is the MIPS-E3 GlideWear liner, which may be incorporated between the comfort padding and energy absorbing shell of a helmet to provide broad coverage from rotational impacts.
“By incorporating a revolutionary technology like GlideWear, we can offer a broader range of solutions so more companies can easily and affordably incorporate MIPS into their existing designs, thereby offering added protection against rotational motion to more athletes of all abilities and ages,” said Johan Thiel, CEO, MIPS.
“Our customers are making some really innovative products,” Erickson said. “A fun aspect of the GlideWear fabric, and the textile industry in general, is the vast markets and product ideas we and our customers envision.”
For more information about GlideWear®, contact Kimberly Sanberg, +763-795-0057; kimberlys@tamarackhti.com; glidewear.com
March/April 2018