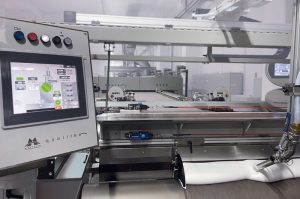
European-built coating technology is allowing Monforts’ customers to move into new markets.
TW Special Report
The flexibility offered by the latest Monforts Montex®Coat coating units — with their multiple coating head options and modular construction for bespoke projects — is proving a big hit with manufacturers of technical materials.
These machines are designed and engineered in Germany and assembled at the Montex plant in Austria, which is celebrating its 40th anniversary in 2022.
“The market has definitely been looking for this kind of added-value proposition,” said Monforts Engineer for Textile Technologies Alexander Fitz. “Since we acquired the coating technology that our systems are based on a number of years ago, we have made a lot of refinements and all of them are reflected in higher coating accuracy and the resulting quality of the treated fabrics.
“We’ve been kept very busy recently with both new installations and on running trials on the Montex Coat line at our Advanced Technology Center (ATC) in Germany, with a number of further new orders confirmed.”
Possibilities
On Montex Coat coating lines, the possibilities range from the single-sided application of finishing agents for outdoor clothing and adding functionality to home textiles, to the creation of materials for sophisticated lightweight construction and automotive and aerospace components.
Layouts for the technical textiles and nonwovens industries now account for more than 25 percent of Monforts’ turnover and systems are in place for applications ranging from outdoor and medical fabrics to filter media which must perform in extreme temperatures and flame-retardant barrier fabrics.
All of these materials require expert coating and finishing for maximum efficiency and the ability to switch quickly from one fabric formula to the next, without compromising on the economical use of energy or raw materials.
“Many more applications are possible with the Montex Coat, such as the overdyeing of denim, the creation of double-face coated materials, fabrics awnings, tents and medical drapes and the pre-treatment of substrates for digital printing,” Fitz explained. “A range of different doctor blades and their combinations can be supplied to meet individual requirements, including air knife, roller knife, foam and paste, screen and magnetic roller coating.”
Fully Adjustable
Magnetic roller coating is an interesting option, especially for wider widths, in enabling a wide range of coatings and finishes to be carried out due to the fully-adjustable positioning of the magnet within the roller. With different magnet positions, it can be set to operate both as a direct coating system and as an indirect coater.
With traditional dip coating systems, as well as with many standard knife coating technologies, there is always a difference in the tension between the center and the edges when wide width fabrics are being treated — and hence, the amount of pressure with which the coating is applied. With the use of a magnetic roller, equal pressure is applied across the full width of the fabric, with entirely consistent results. In addition, adjusting the roller surface, rather than changing the coating formulation to match the required add-on and viscosity for each coating effect required, leads to much higher output from the line.
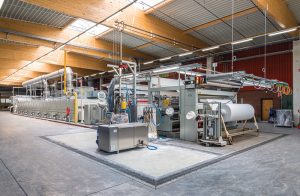
Niche Applications
Recent new Montex Coat customers include Germany-based Dolinschek, a knitting, dyeing and finishing specialist. Dolinschek attributes its success in part to the continuous successful identification of profitable new niche markets.
“There is just so much more to textiles than clothing,” said Technical Director Theo Dolinschek. “We handle many different technical materials such as automotive components, geotextiles and wallcoverings, but also those for more unusual applications such as inlays for extractor hoods, cut protection fabrics and even wool felts which are employed as insulation on wind turbines.”
The company has installed a new seven chamber Montex TwinAir tenter range with a Montex Coat coating unit in knife execution, enabling the coating of dimensionally stable knitted fabrics with polyurethane or acrylate.
A unique feature of this line is a Teflon-coated transportation belt through the system, and it is also equipped with integrated heat recovery and exhaust gas purification to ensure the most resource-efficient processing available on the market. The exhaust air goes from the Monforts heat recovery system into an existing air/water heat recovery system and then into an electrostatic precipitator.
Highly-intuitive Monforts Qualitex visualization software allows all machine functions and process parameters to be assessed and controlled easily, and thousands of article specific settings and formulations to be called up at any time — with 100-percent reproducible results.
Weatherproofing
Scotland-based Halley Stevensons also has commissioned a new Montex finishing range with a Montex Coat coating unit in knife execution for paste and foam coating, to further boost the company’s highly flexible operations.
Founded in 1864, Halley Stevensons has amassed unique technical know-how and manufacturing experience in the art of waxed cotton for weatherproofed fabrics. The company exports worldwide and its premium brand customers include Belstaff, Barbours, Filson and J.Crew.
The new range enables the company to pigment dye, direct coat and pad apply finishes and provides more scope for research and development.
“R&D is the lifeblood of our business,” said Managing Director James Campbell. “The precise process control functions of the line give our technicians confidence to make new products as well as finely tuning the energy requirements of existing products. We love the fact that we can record the energy used on each production batch and use this for continual improvements and efficiency savings. The touchscreen software is visual and easy to use, moving from one screen to another to check the various parameters of processing.”
Foam Application
Turkey-based home textiles and furnishing fabrics producer Altun Tekstil has meanwhile recently commissioned the first Montex Coat coating system in Turkey.
The advanced line has been installed at the ever-expanding family-owned company’s industrial complex in Bursa and is being employed to provide an anti-slip and textured backing to upholstery fabrics with a stable and uniform foam, via knife-over-roller coating.
“With the Montex Coat unit, Altun is able to achieve an even foam application at high speed which results in a very economic process,” said Monforts Sales Manger Thomas Päffgen.
Advanced Functions
Other special features on an integrated Montex Coat tentering line relate to the ability to treat materials not only at temperatures of up to 320°C, but also to be able to treat the top and bottom faces of certain materials at different temperatures within a single pass through the machine.
To achieve this, the chambers of the tenter are fitted with TwinTherm chamber system with separate burners for individual top/bottom temperature. A temperature differential of up to 60°C can be achieved between the upper and lower nozzles within the chamber, depending on the treatment paramenters.
“There are many applications where employing two separate temperature treatments is beneficial, such as floorcoverings, where the textile face fabric is treated at one temperature and the rubber backing at another,” Fitz explained.
In addition, Monforts can provide the necessary explosion-proof ranges for solvent-based coatings and high temperature processes up to 320°C, such as polytetrafluoroethylene coating of nonwoven filter material. These lines are equipped with special tenter chains and insulation.
“Monforts is the only manufacturer to offer completely integrated coating lines from a single source and the coating machine is tailored to the subsequent Monforts drying technology — with all the benefits resulting from a fully integrated PLC control,” Fitz concluded. “Our systems have the shortest fabric path from the coating unit into the tenter and we have all variations of coating application systems too — and all of these options are available in wider widths, with the engineering and manufacturing from a single source here in Europe.”
Dickson-Constant Anchors Its Presence In Hauts-De-France With The Assistance Of Monforts
Dickson-Constant recently opened its second brand new plant in northern France in response to growing demand for its range of well-known technical fabrics. New technology installed at the plant includes a highly-customized Monforts Montex 8500 tenter.
Know-How
The oldest weaving operation in France, with roots dating back to 1836, Dickson- Constant specializes in woven acrylic fabrics and has been part of Glen Raven since 1998. Its Dickson-branded solar protection and flooring materials and Sunbrella home upholstery and market-leading marine industry fabrics are renowned for their quality and durability.
Representing a 40-million- euro-investment, the new Dickson-Constant plant, located in Hordain, Hauts-de-France, builds on many of the proprietary practices and the processing know-how established over many decades at the company’s existing plant less than an hour’s drive away in Wasquehal, France.
Various locations were considered for the plant, and its selection provided a significant boost to the region’s textile industry. In the absence of suitable technical textile training in the immediate vicinity of Hauts-de-France, Dickson-Constant also created a training center to fully train its 75 new plant employees, in addition to other new textile technologists entering the industry.
With many new weaving machines, the plant increases the company’s overall manufacturing capacity by 50 percent while providing the flexibility to accommodate more medium-sized orders and meet requests from certain customers for full exclusivity in respect of specific performance fabric ranges.
Non-Stop
The seven-chamber Montex tenter for drying, heat-setting and polymerizing applied resins has a maximum working width of 2.2 meters. It is installed in line with the washing compartments and is equipped with special entrance and exit fabric accumulators to enable non-stop processing during batch changes, in addition to an integrated vertical infrared dryer and exhaust air cleaning. Two weft straighteners provided by Germany-based Mahlo GmbH & Co. KG also ensure maximum regularity of fabric batches at strategic points in the line.
“The line is very specific to our requirements, building on the experience of running our highly-efficient warping and weaving operations and the Montex tenter for many years in Wasquehal,” explained Process Manager Louis Masquelier. “The new plant in Hordain has a similar layout, but is adapted to new market requirements, since the Wasquehal plant is not set up to enable single runs of under 500 meters of fabric.
The tenters at both plants, he added, have the potential to cause a major bottleneck in operations, should anything go wrong.
“We have also made considerable upgrades to the existing Montex stenter in Wasquehal, including upgrading the electrical components and inverters, as well as ensuring we have all spare parts in-house to ensure all our operations continue to run smoothly. Monforts and its local partner Monel Industrie Services have always provided us with prompt service when needed.”
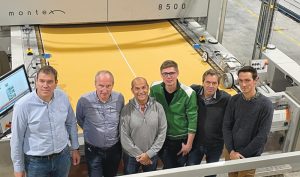
Coatings
Dickson-Constant develops all of its specialized coatings and finishes in-house, and a good example of its prowess in this field is in the latest development for advanced dirt-resistant woven flooring fabrics — the result of more than three years of research.
CleanGuard technology adds an invisible varnished overlay to the woven wear surface, delaying soiling while enhancing its stain resistance and ease of maintenance. The layer of varnish is integrated directly into the finished product, providing additional protection.
The woven flooring system is made up of five distinct layers, each of which provides unique technical features such as a minimum sound absorption of 18 decibels, a dimensional stability of less than 0.1 percent and almost zero risk of fraying thanks to its monofilament construction, which also ensures a clean cut for quick and efficient fitting and a neat finish.
“Sustainability is now paramount to our company and in addition to working towards ISO 50001 standards at both plants, our R&D team is currently focused on developing an oil repellency coating formulation that does not rely on flurocarbons, yet is as effective,” Masquelier said. “We have had a record year in 2022 but the energy situation in Europe is now causing some turbulence. The latest advanced technology, including the Montex tenter, have equipped us to maximize our resource savings and face the current market challenges with confidence. In addition, we have also invested in a water treatment plant allowing the plant to reuse 50 percent of its exhaust water.”
November/December 2022