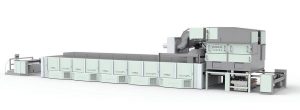
Albarrie – a major player in North America’s industrial nonwovens industry – is now benefiting from one of the first Monforts Montex tenter installations equipped with the full range of MonforClean heat recovery and exhaust air purification technologies.
TW Special Report
With the new three-chamber Montex tenter at its plant in Barrie, Ontario-based Albarrie Canada Ltd. is treating specialized needlepunched nonwovens up to 4 millimeters thick. These nonwovens have applications in a wide range of filter media and performance fabrics.
The new Montex enables Albarrie to heat set and dry its materials to produce denser, higher quality fabrics which can also be finished and delivered to customers more rapidly.
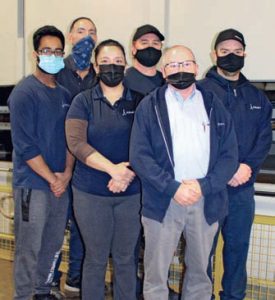
Across Time Zones
It took a crew of skilled millwrights, electricians and product specialists to build the line which was delivered in 11 shipping containers to Albarrie’s production facility. The line was originally scheduled to be fully operational in the Spring of 2020, but the ongoing global Covid-19 pandemic inevitably led to several delays during the start-up and commissioning process.
“Through the challenges of the pandemic, Albarrie staff worked remotely across time zones with Monforts technologists and product specialists to access and configure the machine and run it through a rigorous testing schedule prior to launch,” said Kevin Horner, Albarrie’s director of Operations.
Assistance closer to home also came from PSP Marketing, which represents Monforts in North America from its base in Charlotte, N.C.
PSP reports that there currently is a push for the replacement of tenter frames in the United States. “There’s a move by a number of our customers to bring more manufacturing back to North America, which is definitely a benefit to us,” said PSP Vice President Alex Franco. “And the trend to smaller lot sizes and speed-to-market is something at which the latest Monforts’ technologies excel.”
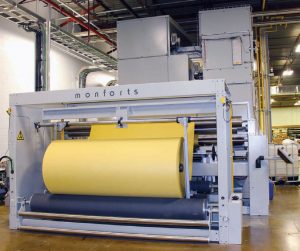
Energy Savings
The Albarrie Montex line’s MonforClean capabilities include an air-to-air cross flow heat exchanger and an electrostatic precipitator providing the ability to purify the exhaust air and to recover energy to a maximum of 22,500 cubic meters of air per hour, resulting in a radical reduction in the conventional heat supply required. The MonforClean was developed in cooperation with Germany-based partner KMA Umwelttechnik.
The fully automated system is powered by a Siemens SPS S7 controller and KP 700 touch panel from which the recycled energy can be continuously monitored and savings calculated.
“The further integration of a washing system that automatically cleans the heat recovery and the exhaust air filter is a serious benefit to U.S. manufacturers because the labor costs for the normally manual cleaning work is so high,” Franco said.
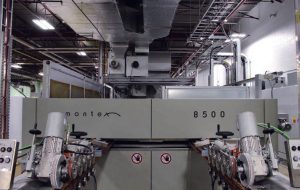
“This is an exciting time here at Albarrie and this new Montex tenter will ultimately open new doors for our business,” Horner noted. “We have noticed significant improvements in many areas compared to our old unit, such as the cleaning access and the ability to easily clean, which reduces down-time, while the efficient burners and exhaust system allow quicker start up and cool down periods. In addition, more controllable features allow for increased quality control and the air filtration system reduces smoke and pollutants, keeping pollutant-free air in our neighborhood.”
The three-chamber Montex tenter is fitted with the latest Monforts Qualitex 800 PLC control system with WebUI, providing ease of operation, a full operating cost overview and maintenance monitoring.
“The new tenter has been very easy to learn for the operators,” Horner said. “It is easy to monitor, and the controls are simple and easy to understand. While reviewing the requirements for the new machine, energy savings were part of our OEM score card. Energy costs are rising, and with carbon taxes being implemented, having our tenter use natural gas will result in energy savings. We are still early in the process of reviewing the consumption data from the new unit compared to the older unit, but currently, the early data indicate that we are consuming on average the same amount of energy, but achieving 1.5 times the amount of BTUs per hour for the same consumption. Most importantly, all of our products run without problems.”
“This was a big investment for Albarrie, but it was an investment for the future, one that will ensure we have the capability to remain competitive in the fabricated textile market for years to come,” added Albarrie’s Executive Director Margaret Driscoll.
January/February 2022