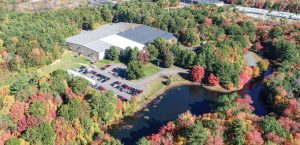
In a year marked by COVID-19 and a very challenging economic environment, U.S. textile companies continued to invest.
TW Special Report
Surprisingly, under the pall of the COVID-19 pandemic, the news pages of TextileWorld.com reveal a fair amount of recent investment by the U.S. textile industry.
Investments including general investment in plant and equipment, polymer and fiber technology, furniture manufacturing, bedding and a strong investment trend in support of domestic production of personal protective equipment (PPE), have defied business challenges in support of new opportunities.
PPE: Domestic Source Focus
Domestic PPE production has become a matter of national security and has the attention of the Federal government.
PPE independence and rebuilding the Strategic National Stockpile (SNS) has also garnered attention at the state level.
In Georgia, Governor Brian Kemp announced the roll out of House Bill 304, the Georgia Made Medical Manufacturing Act. The bill, “will incentivize the production of medicines and medical devices in Georgia, limiting the state’s need to compete with other states or foreign nations for critical supplies.”
“One of the lessons we learned early on in the pandemic is that we cannot waste time in bidding wars with others for life-saving supplies,” Governor Kemp said. “Last session, we incentivized the production of PPE in the Peach State to alleviate that problem, build up our stockpile, and make it easier to stay in business in the era of COVID-19. HB 304 is a natural next step to that program and will help us build on Georgia’s momentum to become a leader in all sectors of the health care industry.”

Masking Up
Late last year, The Fallon Co. and Shawmut Corp. announced a new domestic manufacturing operation to produce N95 respirators. A press release noted: “State-of-the-art manufacturing equipment installed in an expanded facility based in West Bridgewater, Mass., will enable end-to-end production of up to 180 million masks per year. Additionally, the operation is expected to create as many as 300 new jobs in Massachusetts.”
Then in February 2021, Shawmut announced the creation of a new Health & Safety business unit. The company is making isolation gowns and N95 respirators in a 70,000-square-foot retrofitted space in its West Bridgewater facility. Shawmut also invested in almost 60 tons of specialized, high-precision, meltblown machinery from Germany, installed a fully automated and flexible production system to support its N95 particulate respirator line, and installed roughly 50 new assembly lines for gowns and masks, some of which are augmented with advanced robotics capabilities.
Not all PPE investments were on such a grand scale, but still were important in supporting demand. In Harrisonburg, Va., Valley Guard Supply LLC announced investment of $1 million to establish PPE manufacturing. “A service-disabled, veteran-owned company, Valley Guard produces three-ply disposable masks that are 100-percent made in the United States and intends to manufacture other types of safety and security gear in the future. The project will create 45 new jobs,” announced the company.
“Domestic manufacturers of personal protective equipment are critical as we battle this global pandemic, and we thank Valley Guard Supply for answering the call right here in Virginia,” said Virginia Governor Ralph Northam. “The company’s new Harrisonburg operation will play an important role in localizing our supply chain and keeping health care workers and citizens safe.”
Polymer And Fiber Investments
Eastman Chemical Co. recently announced plans to “build one of the world’s largest plastic-to-plastic molecular recycling facilities at its site in Kingsport, Tenn.” The company plans to invest approximately $250 million over the next two years in the facility and “will use over 100,000 metric tons of plastic waste that cannot be recycled by current mechanical methods to produce premium, high-quality specialty plastics made with recycled content.” According to the company, “Eastman was one of the pioneers in developing methanolysis technology at commercial scale and has more than three decades of expertise in this innovative recycling process.”
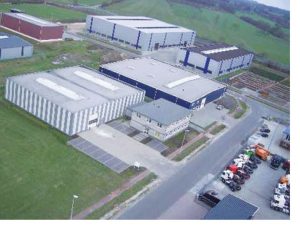
Also following the trend and investing in the recycling arena is Spartanburg, S.C.-based Milliken & Company as it recently announced the acquisition of Zebra-chem GmbH. In a release, the company noted: “With more brands and governments globally setting goals to increase their use of recycled materials, plastics manufacturers are faced with the challenges of using recycled plastics effectively. Peroxide masterbatches, like those from Zebra-chem and Milliken, make it possible to incorporate up to 100-percent recycled content into these new plastics.”
“Milliken’s long-term focus on innovation and sustainability encourages us to consider how we contribute to some of today’s leading challenges, like how to effectively incorporate recycled plastics in manufacturing,” said Halsey Cook, Milliken & Company president and CEO. “I’m excited to welcome the exceptional talent within Zebra-chem as they join the passionate team at Milliken to move the needle on sustainable innovation.”
Rome, Ga.-based Integrated Fiber Solutions (IFS) announced it will invest $30 million to expand its operations to meet growing demand. IFS — a manufacturer of man-made bulked continuous filament (BCF) yarns for the carpet, rug, and automotive industries — was established in 1986 to serve the man-made yarn needs of multiple carpet and rug industries in Georgia with locations in Rome, Dalton, and Lafayette, Ga.
In other fiber-related news, Duluth, Ga.-based FiberVisions Corp., a subsidiary of Indorama Ventures Public Co. Ltd., will invest $48 million to expand its polyolefin fiber manufacturing operations in Newton County, Ga. According to the company, “This expansion, which comes in response to a sharp increase in demand for hygiene products made with bicomponent fibers such as face masks and baby wipes, will create 21 additional jobs.” Installation of this bicomponent fiber line is expected to be complete during the first half of 2021.
Keeping Up With The Strategic Plan
Burlington, N.C.-based Glen Raven Custom Fabrics announced the progress of its “Multi Phase Expansion Plan” with its first phase initiated at the end of 2019. The plan includes new equipment as well as upgrades “to support the continuing growth of Sunbrella® fabrics and other Glen Raven textile products in the company’s U.S. and Asia facilities.” The customized equipment will be brought online in stages during the first half of 2021. According to the company, the expansion “will not only increase output, but also reduce energy and water usage, laddering back to Glen Raven’s sustainability commitments.”
In addition, Glen Raven announced the purchase of a production facility in France. “Taken together, these actions represent an investment of more than $65 million in expanded production capacity to support its customers and the increased demand for Sunbrella, Dickson® and other Glen Raven fabrics. Future phases of the program include additional production and distribution capacity for the U.S. and Asia markets.”
Nonwoven Moves
Nonwoven manufacturer, Fitesa Simpsonville Inc., announced expansion of operations in Greenville County, S.C. The $100 million investment will expand overall capacity and include the installation of a new melt-blown production line to produce materials for the healthcare market. The expansion is expected to be completed by 2023.
Atlanta-based Georgia-Pacific LLC announced that it has reached an agreement to sell its nonwovens business to Glatfelter, a global supplier of engineered materials, headquartered in Charlotte, N.C., for $175 million. According to a press release: “The proposed transaction includes Georgia-Pacific’s nonwovens operations located in Mt. Holly, N.C., along with a research center operation in Memphis, Tenn. The nonwovens operations in Mt. Holly produces airlaid nonwoven material for commercial customers used to make table top, wiping, food pads, hygiene and related products. In the proposed transaction, current Georgia-Pacific nonwovens employees, totaling approximately 150 people, will become employees of Glatfelter at the time the deal closes.”
Kernersville, N.C.-based Texwipe, a global manufacturer of contamination control supplies, will invest more than $4.5 million to locate a manufacturing facility in Mount Airy, N.C. “Our state’s economy continues to grow, despite public health and economic challenges,” said North Carolina Governor Roy Cooper. “Companies like Texwipe choose to grow in North Carolina because of our talented workforce and our state’s strong management of the pandemic.” Texwipe has been headquartered in Kernersville since 1991.
Greenville, S.C.-based Fibertex Nonwovens Inc., just announced an expansion at its Gray Court, S.C., spunlace production location. The $49.5 million investment is expected to create 39 jobs. The expansion includes a second spunlace line for rolled nonwoven products as well as the acquisition of an 84-acre industrial plot adjacent to the company’s facilities.
“With this new investment, we’ll be able to build an extremely strong position in the important North American market for, among other things, high-performance wipes for sanitizing and disinfection purposes in the healthcare/medical sector, sustainable personal care products, a range of industrial applications, as well as in the automotive industry and the construction sector,” said Jorgen Bech Madsen, CEO, Fibertex Nonwovens.
Bedding Makes News
Multiple companies recently announced investments in the bedding market.
Mattress manufacturer and retailer Brooklyn Bedding officially announced plans to expand in its home state, breaking ground on a new state-of-the art manufacturing facility and corporate headquarters in Glendale, Ariz. According to the company: “The new manufacturing facility and corporate headquarters will merge the capacity of both the company’s current factory and warehouse. The plan entails an investment of more than $72 million to make Brooklyn Bedding nearly 100 percent vertically integrated.”
Tempur Sealy International announced expansion of its manufacturing operation in Scott County, Va., with an investment of $16.7 million. “Tempur Sealy has expanded a number of times since opening in Scott County in 2001, and this expansion will enable the Duffield plant to increase its production and support the growth of Tempur Sealy’s award-winning products,” said Scott Thompson, Tempur Sealy Chairman and CEO. “We have developed a strong relationship with the community, and we are fortunate to have a well-educated workforce committed to excellence in quality, safety, productivity, and environmental compliance. The company reports the expansion will be mostly complete by the end of 2021 with capacity increases realized by 2022.
High Point, N.C.-based Culp Inc. together with its consolidated subsidiaries, CULP — recently announced “strategic investments and enhancements to its global cut and sew mattress cover platform.” CULP will purchase the remaining 50-percent ownership interest in an unconsolidated joint venture in Haiti. The business produces cut and sew mattress covers. Upon completion of the transaction, CULP will be the sole owner and operator of the Haiti operation. “We are very pleased with our Haiti operation, which has proven to be an ideal location for our growing sewn mattress cover business,” said Iv Culp, president and CEO of Culp Inc. “Through our strategic investments, we have demonstrated our ability to improve our operating efficiencies, and we believe there are additional opportunities within CULP to leverage the production capacity and distribution capabilities from Haiti.
Furniture, Home Furnishings & Flooring
Raleigh, N.C.-based furniture and home furnishings manufacturer Riverside Furniture Corp. announced a $5.4 million investment for a warehouse and distribution center in Caswell County, N.C. A recent press release reported: “Founded in 1946, Riverside Furniture Corporation designs, manufactures and distributes residential furnishings to 3,000 furniture retailers across the United States. Since opening their first plant in Arkansas nearly 75 years ago, the company has experienced exponential growth. Riverside’s additional 300,000-square-feet of distribution and warehouse operations in Caswell County will reduce shipment lead times to retailers in the Eastern United States from receipt of order. “
“Riverside’s investment in North Carolina, including both the new High Point showroom and the Caswell County distribution center, is a combined $15 million, which is a reflection of our growth as a company and the expansion of service to our customer base,” said Fred Henjes, CEO and president of Riverside Furniture. “Because the distribution center is situated on 50 acres of land, the campus will give us the ability to expand.”
Lawndale, N.C.-based Ison Furniture Manufacturing Inc. will invest $3.5 million to acquire and renovate the recently closed A.C. Furniture Co. Inc. facility in Pittsylvania County, Va. The company also will purchase new equipment for the assembly and full production of its upholstered furniture products. The company’s supplier, Dogwood Global LLC, will locate to a vacant 30,000-square-foot building on-site, investing $500,000 in new equipment to manufacture high-end wood tables and custom furniture frames that will be upholstered by Ison Furniture.
“We are pleased to welcome Ison Furniture Manufacturing and Dogwood Global to Southern Virginia,” said Governor Northam. “Manufacturing is an important pillar of many communities across our Commonwealth and is key to rebuilding our economy in the wake of the ongoing global pandemic. The region’s strong history with textiles and furniture combined with the caliber of the existing upholstery and furniture-building workforce makes this project a natural fit for Pittsylvania County, and we look forward to the future success of this new operation.”
Skutchi Designs Inc., a national contract office furniture company, recently announced a more than $3.5 million investment and plans to expand operations in Horry County, S.C. The company specializes in producing office cubicles, interior glass office walls, and desks and conference room furniture, among other workplace products. According to the company, the expansion is expected to be completed by 2022.
On the flooring front, Mohawk Industries Inc., a global manufacturer of residential and commercial flooring products based in Calhoun, Ga., announced an investment of $22.5 million to expand an operation in Carroll County, Va. The Hillsville facility will grow by 19,000 square feet to house new extrusion and loom equipment for increased production speeds. The expansion will create 35 jobs. According to a press release about the expansion: “Mohawk employs more than 900 Virginians. The company’s Hillsville facility manufactures carpet-backing from 100 percent recycled post-consumer materials, which is then used to manufacture commercial carpet at its Rockbridge County facility as well as other Mohawk carpet manufacturing locations across the Southeast.”
Knitting And Apparel
Pennsylvania-based AKAS Tex has announced an increase in its knitting capacity. According to the company: “Due to overwhelming demand of the fabrics that are used for face masks and surgical gowns, AKAS Tex has added five knitting machines in the year 2020. Two machines are for double knits, such as its the ProCool® interlock; two machines are for its Zorb® Dimple spacer fabric; and one machine is for its TransWick® 1-Way Wicking fabric. These five machines will add 200,300 pounds per year to the existing knitting capacity and generate much needed employment.”
In the childrenswear space, New York City-based United Legwear & Apparel Co. (ULAC) has acquired TicTacToe, a brand of infant, toddler, and children’s legwear, accessories and apparel. According to the company: “The acquisition of TicTacToe allows ULAC to offer a wholly-owned brand to retailers who want to give their customers top-quality children’s apparel and accessories at a good value. Additionally, ULAC is developing a global licensing program across all categories in the kids’ market, from layette, infant, and toddler sets to baby blankets, underwear, toys, and more.”
Denver-based VF Corp. recently announced the completion of its acquisition of Supreme®, a privately-owned global streetwear brand, for an aggregate base purchase price of $2.1 billion. Supreme now is a wholly owned subsidiary of VF Corp. “The acquisition of the Supreme brand accelerates VF’s consumer-minded, retail-centric, hyper-digital business model transformation and builds on a long-standing relationship between Supreme and VF, with the Supreme brand being a regular collaborator with VF’s Vans®, The North Face® and Timberland® brands,” VF Corp. stated in a press release. “The Supreme brand is expected to contribute at least $500 million of revenue and $0.20 of adjusted EPS in fiscal 2022.”
Investment Continues
As the pandemic trends downward and the economy opens up, one would expect growth and consumer spending to strengthen. U.S. textiles is poised for that growth and looks forward for additional opportunities.
March/April 2021