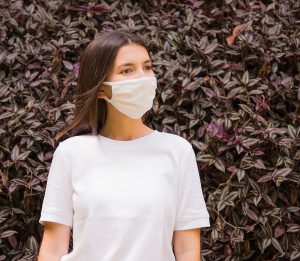
by Parkdale is making a 3-ply knit
cotton face mask.
The global pandemic has the textile industry cooperating in ways not typically seen as it works to meet the need for medical PPE.
By Rachael S. Davis, Executive Editor
As the globe grapples with a pandemic the likes of which hasn’t been seen in more than a century, the textile industry is stepping up and banding together in truly inspiring ways.
The U.S. textile industry — a much maligned industry in recent decades that many observers long ago wrote off — has been energized by the call to help provide personal protective equipment (PPE) as the country is faced with a dire shortage of disposable PPE for its front-line medical personnel.
From the largest to the smallest companies and from the history-rich, legacy companies to businesses relatively new in the textile landscape — all are pitching in during this time of need. Raw material suppliers and machinery companies, yarn spinners, fabric producers, finished goods manufacturers, apparel companies and brands are working alone or collaborating to make a difference.
Industry associations also are lending a hand by helping match companies in the supply chain who are looking for ways to help, but need assistance — either materials, servies or advice — to get started. One such organization, the Atlanta-based Americas Apparel Producers’ Network (AAPN), established an online bulletin board named the “Sourcing Center” back in March. “Anyone interested in participating could login to the Sourcing Center and post their needs and capabilities for others to read and respond to,” said Mike Todaro, AAPN’s managing director.
Facilitated by AAPN President Ed Gribbin, the online message center enabled AAPN to identify producers, qualify prospects, learn about U.S. Food and Drug Administration (FDA) standards, assemble supply chains, build a resource check list and deliver product.
It was a great resource for AAPN members, but the association knew more could be done. According to Todaro, AAPN recognized it had the ability to connect people throughout the supply chain and across a variety of geographies, links in the supply chain and products, which led the association to open the Sourcing Center to non-members for a time.
“Without hesitation and with no motive other than to do the right thing, we wrote every organization we knew in this industry inviting their members into our network,” Todaro said. Members of the Industrial Fabrics Association International (IFAI), the Association of the Nonwoven Fabrics Industry (INDA) and SEAMS – the Association and Voice of the U.S. Sewn Products Industry, among others, jumped at the opportunity. In the space of eight weeks, the board amassed more than 50,000 pageviews with countless posts on a huge number of threads. AAPN also was able to deliver 100,000 gowns to Emory Healthcare in Atlanta.
“The support we received from other association managers and their senior members was instant and spectacular” Todaro noted. “We were united by one cause — to create compliant spec packs, find fabric, identify cut/sew factories, and get masks and gowns into hospitals and onto healthcare workers.”
The network is now back “in-house” for AAPN members only, but the association has created a new level of AAPN membership it calls the Cloud Member — a low-cost membership option that grants participants access to the sourcing discussions, AAPN member emails and virtual events.
What To Make?
There is no one-size-fits-all approach to PPE. While during the pandemic, the term PPE has become a household name now in everyday use, from a regulatory standpoint, there is a clear difference between PPE used in a healthcare or occupational setting versus face coverings used by the general public (See “Textiles & The Coronavirus (SARS-CoV-2),” TW, this issue). However, non-regulated face masks and gowns that may not quite meet the occupational definitions still have their place and are making a difference during the pandemic. The current Centers for Disease Control and Prevention (CDC) guidelines suggest that everyone wear a mask to protect themselves when outside, but more importantly, protect people around them who may be more vulnerable.
Whether wovens or knits, sewn or laser-cut one-piece masks, masks with value-added finishes or without, the industry is coming up with many creative ways to use the available fabrics, machinery and technology to solve the problem and meet a need.
Perhaps the most prominent and largest effort is led by Gastonia, N.C.-based Parkdale Inc. Dr. Peter Navarro, assistant to the president and director of the White House Office of Trade and Manufacturing Policy, called Parkdale’s Chairman and CEO Anderson D. “Andy” Warlick to ask how the textile industry could help with PPE production. “I told him we can actually make masks if we can get a machine over here from Asia, but that could take up to six months for delivery,” Warlick said. With an immediate need for PPE, the conversation turned to what could the industry do with the available manufacturing capacity, materials and resources on hand to make a face mask. Immediately following the conversation, Warlick picked up the phone and began calling Parkdale’s customers to enlist their help.
“That’s how we built the coalition,” Warlick said. “Hanes was already working on a face mask and other companies were cutting and sewing items. So, we banded together and developed one design to get started.” The resulting coalition, put together in about two-and-a-half days, comprises textile companies and apparel brands from throughout the supply chain who are working together to produce face masks and also gowns.
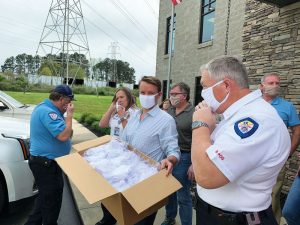
Gaston Emergency Medical Services in Gastonia, N.C.
Companies who joined the coalition in the early stages includes Hanesbrands, Fruit of the Loom, American Giant, Los Angeles Apparel, AST Sportswear, Sanmar, America Knits, Beverly Knits and Riegel Linen. But as the initial members reach out to companies in their networks to collaborate, the coalition is growing. Parkdale is working directly with more than 20 companies currently, and Warlick said the extended network totals approximately 50 companies.
“As you can imagine, bringing together a group of competitors wasn’t going to be an easy thing, except for the fact that Parkdale wasn’t a competitor to any other coalition member,” Warlick noted. “This made it easier for me to bring people together and lead and organize the effort.”
The mask is a 3-ply cotton construction made using a 4-ounce knit jersey fabric that is finished with an antimicrobial silver and copper-based chemistry. Warlick is quick to point out however, that the mask is not intended for medical environments and the companies involved do not make any claims about antiviral protection or infection prevention or reduction, among other claims. “If we could have made N95 masks, we would have made N95 masks,” Warlick said. “But that wasn’t possible. So, we’ve done the next best thing we could do, which is to offer another level of protection.
“The great thing about this coalition the number of companies that are involved,” Warlick added. “It’s thousands of workers in the United States alone, and then when you expand out the supply chain to Central America to customers and factories there who are working with adjacent factories, it really strengthens the customer base. It’s helping companies not lose money or go out of business at a critical time when retail is virtually shut down. There’s thousands of people that have been mobilized for this cause, and it’s a great story that I’m proud to be a part of.”
“I do think after the immediate needs are met there are going to be opportunities that I hope the coalition can take advantage of,” Warlick said. “Not just in working together, but also in the PPE business, which would be good for the textile industry.”
Keeping Plants Running
Contempora Fabrics, Lumberton, N.C., joined the growing list of coalition companies when it received a call from Beverly Knits, Gastonia, N.C., who was looking for jersey knit fabrics for the masks. Contempora’s President Ronald Roach said for the first time in his career, the company had just furloughed most of its employees on a Friday because business had basically come to a halt, when the opportunity to make masks materialized. “Our quality control manager made a few masks that we started to present to the market,” Roach reported. “Over the next two days, we were able to secure enough business to bring 70 percent of our furloughed people back to work that Tuesday.” The company quickly set about making fabric for masks and gowns, as well as actually making masks — a completely new endeavor.
Contempora is an employee stock ownership company where its employees own shares in the business. Roach said: “The catalyst to make the change quickly was to not only help out with what we could provide in the way of PPE, but was also protecting the franchise of the company along with our employee owners. Getting them back to work was a priority, but only if we could do it safely. We had to put in a lot of new procedures to be able to work safely while social distancing.”
As a producer of fabric for team sports, athletic apparel, military and other apparel categories, Roach reported there was a huge learning curve as the company learned about PPE. “There was an even bigger learning curve as we started producing our own masks, especially since we own no sewing equipment!”
Contempora relied on the expertise of other companies in the textile supply chain to ensure its finished products were produced using the right materials and met testing requirements. Carolina Cotton Works and Deep River Dyeing assisted with antimicrobial treatments and durable water repellents; and ImagineKnit Global made sure Contempora was adhering to proper labeling and product claims from a testing and regulatory standpoint. Clothier Design Source, OnPoint Manufacturing and Apparel USA all played a role in getting Contempora set up and running with mask-making capabilities.
“Two organizations that played a vital role for so many of us was AAPN and SEAMS,” Roach noted. “The AAPN Sourcing Center was able to provide everyone in the supply chain a contact for any service or component in real time. Then when the center opened up to SEAMS members, it exploded with helpful information.
“I have watched our company completely transform from a fabric supplier for sports to running fabrics for PPE,” Roach continued. “We also set up mask manufacturing at six different U.S. locations, and then brought on mask production out of Nicaragua and Mexico when we couldn’t keep up with demand here in the United States.”
Retooling To Make Testing Swabs
When swabs for COVID-19 testing became critically low, another Parkdale-owned company U.S. Cotton retooled equipment at a facility in Cleveland running cotton fiber for cotton swabs to run polyester for test swabs. “If we could have used cotton for the test swabs, then overnight we would have been able to cover the country and the world up in cotton swabs,” Warlick said. “But cotton has its own DNA, and that can lead to false negatives in testing.” U.S. Cotton worked with the White House and the Gates Foundation on the project, and now is shipping the test swabs to sites where they are needed.
Reusable Instead Of Disposable
Some companies are offering an alternative to disposable products with their reusable medical fabric options. Spartanburg, S.C.-based Milliken & Company has pivoted its textile manufacturing to focus on advanced medical textiles. Milliken Perimeter™ fabrics and barriers are available in Level 1, 2 and 3 options for different medical environments and products including gowns, scrubs, lab coats and hospital privacy curtains. Each product is tested to the ANSI/AAMI PB70 Standards. Milliken fabrics are complemented by its BioSmart™ antimicrobial technology, which harnesses the power of bleach to kill up to 99.9-percent of common bacteria on contact, according to the company. Milliken reports it also is researching and developing materials for incorporation in N95 masks.“We have focused our development and manufacturing processes to help fight the battle against COVID-19,” said Halsey M. Cook, Milliken & Company’s president and CEO. “We began by engineering our existing textiles into medical-grade fabrics for PPE, and we will continue to seek critical solutions as we navigate this uncharted territory as a company, a nation and a world.”
Burlington, Greensboro, N.C., also has increased production of its reusable medical fabrics (See, “Quality Fabric of the Month: Time-Honored Protection,” TW, this issue).
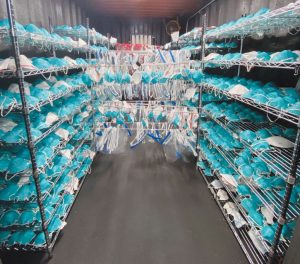
Instead of making PPE to combat the shortage, Battelle — a Columbus, Ohio-based global research and development organization committed to science and technology for the greater good — has brought to the industry a way to extend the life of disposable PPE through its Critical Care Decontamination System™ (CCDS™). The system is capable of rapidly decontaminating N95 respirator masks by exposing the used respirators to a concentrated vapor phase hydrogen peroxide (VPHP) for two-and-a-half hours to remove biological contaminates including SARS-CoV-2. CCDS was the result of a 2016 research project conducted by Battelle on behalf of the U.S. Food and Drug Administration (FDA). This year, further testing showed the CCDS rendered SARS-CoV-2 and other pathogens non-infectious on N95 respirators.
The FDA recently granted Battelle an Emergency Use Authorization (EUA) to decontaminate used N95 respirators up to 20 times — a number of cleanings through which the filter material has been shown to remain intact, exhibiting no degradation and therefore remaining safe for reuse.
The EUA allowed Battelle to begin a collection process whereby the company collects worn masks from enrolled healthcare systems, transports them to an active Battelle CCDS site, decontaminates the masks and returns them. A barcoded serial number tracks the mask through the process ensuring it is returned to the same hospital system. Each mask is also marked to denote the number of times it has been cleaned for reuse. According to Battelle, including shipping times and depending on the number of masks received for processing, hospitals can expect to receive their cleaned masks back in 7 to 10 days.
“The response has been overwhelmingly good, and now Battelle has been awarded a $415 million contract by the Defense Logistics Agency on behalf of the U.S. Department of Health and Human Services to support development, deployment and operation of some 100 systems across the United States,” said Dr. Vicki A. Barbur, senior director, Partnerships and Technology Commercialization, Battelle.
A Need For Meltblown, Spunbond Nonwovens
Nonwovens are the optimal material for the N95 masks that are most needed by the front-line medical workers who are treating patients with COVID-19. However, prior to the pandemic, the United States relied on Asia for some 80 percent of its nonwovens-based N95 masks, according to INDA President Dave Rousse.
“There are now several key policy makers and administrators in our military and our government who have a new knowledge and appreciation for the role that nonwovens play in personal protective equipment,” Rousse said. “We have worked with folks at FEMA, the Department of Defense, the White House, EPA, FDA, NIOSH, and more, to connect producers of various nonwovens with converters of PPE.” Rousse reports INDA has also been able to connect some nonwovens producers with sources of funding for new meltblown equipment to make the filter media required for N95 respirators.
Rousse’s big concern for the future is will the nonwovens supply chain for masks revert back to Asia with its low pricing as soon as the situation abates? “Or will policy makers develop some kind of ‘Buy American’ plan or National Stockpile or both to provide some continuity of demand for the new investments?” Rousse questioned. He also mentioned that liability protection concerns need to be addressed so the country can be better prepared for possible future pandemics.
The Nonwovens Institute (NWI) is a global partnership among industry, government and academia dedicated to the development of engineered fabrics located on the Centennial Campus of NC State University in Raleigh, N.C. With full support of the university, “NWI is dedicating its meltblown and spunbond nonwoven making facilities and expertise” to manufacture both of these nonwoven materials commonly used to make N95 respirator and surgical face masks.
“NWI was eager to help join the fight against the novel coronavirus and given that NWI has been working in the field of filtration and separation for many years and using that know-how, very quickly developed several alternative facemask materials,” said NWI’s Executive Director Dr. Behnam Pourdeyhimi, who is also the NC State Wilson College of Textiles’ associate dean for industry research and extension, and William A. Klopman distinguished professor.
However, running production-level amounts of nonwovens requires raw materials that the institute did not have on hand. Enter NatureWorks and ExxonMobil — both long-time partners of the Nonwovens Institute (NWI) that are contributing to the institute’s PPE efforts by donating raw materials.
Minnetonka, Minn.-based NatureWorks donated Ingeo™ resin, a polylactic acid biopolymer, that NWI is using to produce spunbond nonwovens for N95 surgical masks. “… We took the spunbond technology and created a new generation of unique filters that have excellent filtering capability without needing to be charged, meaning they can potentially be reused after cleaning with peroxide, or an alcohol solution,” Dr. Pourdeyhimi said. “Because these materials are also strong, they can be cut and sewn by traditional techniques.”
ExxonMobil, Irving, Texas, has donated a total of 146,000 pounds of its ExxonMobil™ PP3155, Achieve™ Advanced PP6926G2 and Vistamaxx™ 8880 performance polymers to NWI through LINC, a non-profit NWI affiliate. Channel Prime Alliance handled delivery of the product. NWI is using the polymers to produce spunbond and meltblown nonwovens, which are being used as the outer and inner layers of the face masks respectively.
“There is a global shortage of materials and securing supply is a key factor in NWI’s ability to create nonwoven filter media,” Dr. Pourdeyhimi noted. “Natureworks and ExxonMobil are long time partners of NWI and not only secured the supply for NWI, they also donated significant amounts of the polymer to help NWI in its fight against the novel coronavirus. Without their partnership, we would not be able to do what we are doing today.”
According to Dr. Pourdeyhimi, there are two critical shortages in the United States for nonwovens manufacturing. “The first is capacity for base nonwoven materials — especially meltblown filters; and the second is converting machinery to form masks.”
NWI also has invested in mask-making equipment that will soon arrive at the institute. Dr. Pourdeyhimi observed that the ability to make masks also gives the institute the opportunity to develop new structures not previously used for masks. “Our machines will be used to manufacture classical masks,” he said. “However, NWI also will create new structures that will serve as a platform to redefine the future of how masks are made.
“It will take several years before we see the impact of the current crisis on new, innovative solutions,” Dr. Pourdeyhimi said. “I am certain we will see a surge in patents being filed on various forms of masks from the classical styles, to 3D printed, and beyond!”
The Future For The Industry And U.S.-Made PPE
No-one yet knows the full impact of the virus on the supply chain and what the textile industry looks like when the immediate need for massive quantities of PPE abates. But the general outlook seems positive.
“I do think the U.S. textile industry has proven that we have some of the most creative minds in the world,” Contempora’s Roach said. “The collaboration between companies, competitors and organizations has been incredible. It is also apparent to all of us that the reliance on Asia is not a good position to be in. The role that NCTO [National Council of Textile Organizations] has played in securing business here in the United States has been outstanding.”
Parkdale’s Warlick said he thinks the government’s understanding of the relevance of the U.S. textile industry has changed as a result of the pandemic. Speaking of NCTO he said: “I think NCTO’s President and CEO Kim Glas has done a good job of making sure that Washington sees what the textile industry is doing. And I do think there’s more interest and more talk on the Hill about legislation that quite frankly wouldn’t be happening if the industry hadn’t stepped up. I do believe the industry’s recent collective efforts have helped the textile industry.
“Individually, I hope a lot of textile companies go into the PPE business because it’s good for the textile industry,” Warlick added. “It’s just another way companies can survive, and I hope we thrive!”
May/June 2020