The modern textile industry finds itself at a curious crossroads: On one hand, there is a diminishing pool of inexpensive labor; and on the other, the client base is interested in flat margins and assurances of responsible manufacturing practices — which can sometimes require significant financial investment. The second Great Ideas in Cotton conference — hosted in Hong Kong by Cary, N.C.-based Cotton Incorporated on May 22 — showcased a range of new technologies and process optimization research to help cotton textile businesses meet current industry expectations.
“This conference is a thoughtfully curated collection of responsible technologies and processing efficiencies,” explained Mark Messura, senior vice president, Global Supply Chain Marketing, Cotton Incorporated. “As a resource for the global cotton industry, we are pleased to convene this forum, so that manufacturers can be aware of the many options available for their businesses,” he added.
The day-long conference began with an overview of Cotton LEADS™ by Adam Kay, CEO, Cotton Australia; and Berrye Worsham, president and CEO, Cotton Incorporated. Cotton LEADS, a joint program with Australian and U.S. cotton producers, calls attention to the national regulatory environment, responsible growing practices and significant environmental gains achieved by the founding countries.
“The self-investment by Australian and U.S. growers in research and development, combined with the well-established national regulatory environments in Cotton LEADS founding countries, enables us to make significant environmental gains at a national level,” Kay explained.
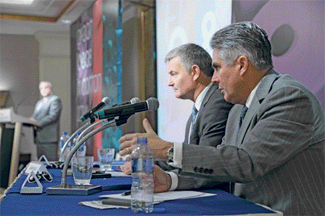
Left to right: Cotton Australia CEO Adam Kay and Cotton Incorporated President and CEO Berrye Worsham discuss the Cotton LEADS™ program with attendees at the Great Ideas in Cotton Conference held in Hong Kong earlier this year.
During the question-and-answer session, Worsham and Kay pointed out that Cotton LEADS is a complement, not a competitor, to identity cotton programs, which rely on farm-by-farm certification. A day ahead of the conference, representatives from founding cotton organizations in Australia and the United States met with local manufacturing partners of the Cotton LEADS program. Simon Corish and Lyndon Mulligan, chairman and deputy chairman, respectively, of Cotton Australia; and Jimmy Dodson, past National Cotton Council chairman, detailed growing practices on their cotton farms, as well the use of third-party verifications to measure environmental impact in the founding countries. Since the program’s launch last October, 179 manufacturers and brands have acknowledged Cotton LEADS cotton as meeting their sustainable fiber sourcing criteria.
Great Ideas For Denim
The technical portion of the program included a host of great ideas for denim, a key cotton category.
Cotton Incorporated shared research pinpointing optimal levels of indigo, water and energy for traditional processing, as well as gains that can be achieved through the use of enzymatic processing.
Soko Chimica S.r.l., Italy, presented its Soko Eco Stonewash process for producing stonewashed effects. The process can reduce water usage from the typical 30 liters or more to less than 3 liters.
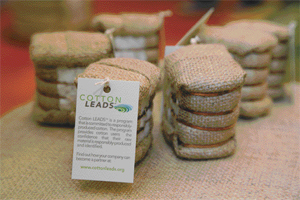
Cotton LEADS™, a joint program with Australian and U.S. cotton producers, highlights the national regulatory environment, responsible growing practices and significant environmental gains achieved by the founding countries.
Tonello S.r.l., Italy, presented four technologies: EcoFree, an ozone wash system capable of producing a pure indigo, as well as stonewashed looks, with a 50- to 80-percent reduction in water and chemical consumption; Laser Blaze™, a versatile machine that can laser-treat denim and dyed garments on a table, a double table or a mannequin; a Jet System that uses sulfur dyes in a nitrogen atmosphere and achieves a 70-percent reduction in water, chemical and energy consumption; and Kit Batik, an automatic machine process that can apply stain in varying degrees using 96-percent less water than traditional processes.
Jeanologia, Spain, presented two new machine systems. The company’s Dynamic Laser is a continuous laser engraving system capable of engraving denim at the rate of 1 to 6 meters per minute (m/min), depending on design and definition, without chemicals, water or discharge. The Dynamic G2 is a continuous ozone system for creating a wide range of finishing effects at the rate of 2 to 12 m/min, again without chemicals, water or discharge.
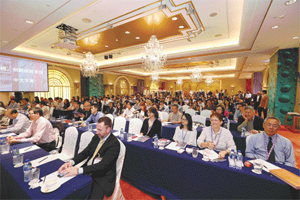
More than 300 representatives from 123 companies and eight countries in the Asia-Pacific region attended the Great Ideas in Cotton Conference.
Switzerland-based Archroma, better known as a textile chemical supplier, presented its innovative ONE WAY Methodology and Toolbox. The measurement tool helps manufacturers and brands meet sustainability targets through a highly systematic approach to chemical and production process selection. The three-step process belies the complexity of the system, which draws upon a database of 15 textile eco-standards and other criteria. The system also assesses the cost, performance and environmental impact of evaluated products and processes.
Amid growing concerns over formaldehyde use in textile finishes, Germany-based BASF SE presented a formaldehyde-free resin option for achieving no-iron performance in cotton and cotton-rich blends.
Korea High Tech Textile Research Institute (KOTERI) presented new research on the advantages of cold pad batch processing on knits. Process recommendations have resulted in reduced water and energy expenditures, as well as reduced wastewater and reduced levels of dye and electrolytes in the wastewater.
More than 300 representatives from 123 companies and eight countries in the Asia-Pacific region attended the conference, which also included a panel discussion on marketing cotton textiles, a vendor exhibition area, concurrent trend presentations by Cotton Incorporated trend forecasters, and displays of innovative cotton apparel by design school students from Hong Kong universities.
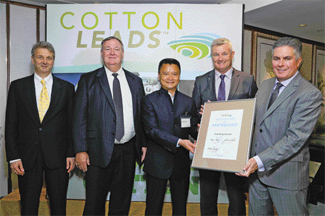
Samuel Choi (center) accepts the Cotton LEADS partner certificate on behalf of Ford Glory, a Hong Kong-based garment manufacturing and trading company, from Cotton Australia Deputy Chairman Lyndon Mulligan, Chairman Simon Corish and CEO Adam Kay; and Cotton Incorporated President and CEO Berrye Worsham.
July/August 2014