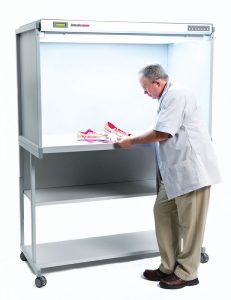
Getting color right the first time reduces waste, saves time and offers value to customers.
By Basto Wong
To improve the value they provide to their customers, some industry-leading brands and major retail chains now require their suppliers to follow tighter quality and sustainability guidelines. These include mandates to use color specification and quality control (QC) technologies throughout their supply chains.
Companies hope to achieve multiple goals by specifying these technologies. First, they reduce the environmental impact caused by waste-producing color mistakes that can occur during manufacturing. In addition, they help provide universal color consistency — a benefit at every stage of the supply chain and to customers as well.
Although many brands have been utilizing color management technology in their own facilities for years, these requirements are now being extended to current and would-be suppliers. The reasons are well justified. Color management systems can help reduce waste, save time, provide consistent color QC across multiple locations, and improve communication between brands and their suppliers.
Implementing the necessary hardware and software tools isn’t enough, however. To ensure supply chain consistency and transparency, many vendors are also being required to prove they can meet color standards by participating in a color management verification program.
Verifying The Supply Chain
Quality-conscious brands take color consistency seriously. To ensure that their suppliers’ color programs and processes meet specified standards, many are increasingly turning to verification and certification processes. Experts recommend that each supplier be assessed by a third-party authority such as Data-color Certify, a color assessment and lab audit program that also provides training services.
The auditor will check for conditions within the manufacturing process that can affect color quality, such as:
- Operator expertise, skill, knowledge, and ability to use color management software and technology properly;
- Overall equipment performance, condition and calibration; and
- Humidity, temperature and other environmental factors.
Assessments typically involve a combination of off-site and on-site inspections designed to ensure that the supplier is qualified and capable of meeting a brand’s color quality expectations. Inspections should ideally be performed annually to ensure that proper color develop-mental procedures are followed consistently over time.
Achieving Objectives
By implementing regular color management assessments like this across their supply chains, brands can achieve multiple goals, including:
- Reducing the overall number of lab dips or samples;
- Reducing or eliminating shipments of physical color samples for approval;
- Easing the environmental impact of repeat production by minimizing color matching and formulation errors;
- Increasing speed to market;
- Verifying the color capabilities of suppliers;
- Empowering vendors to make decisions locally, eliminating delays waiting for guidance — especially from customers in distant time zones; and
- Ensuring consistent quality for end customers.
Benefits Of A Color Program
Although verification is typically required by brands or retailers, suppliers are often the primary beneficiaries when it comes to cost savings. For those in the apparel sector, for example, color approval processes that used to involve as many as six lab dip submissions can potentially be streamlined to only one or two. Those kinds of savings add up quickly because a single lab dip can cost more than $100. Lab dip samples also must be ferried back and forth between brands and suppliers, incurring additional costs and creating unnecessary carbon emissions. The savings in time, money and resources from these two benefits alone can easily justify the effort of verifying a color program, both for brands and suppliers.
Certification can empower qualified suppliers in other ways. Being able to self-approve samples that meet measurable specifications delivers increased production efficiency and opportunities to optimize the color developmental process. Suppliers can also reach more brands by showcasing their capabilities. A universal accreditation program is especially advantageous, because a single annual certification can satisfy the requirements of multiple brands.
Suppliers often become validated in response to mandates from their customers, but they can also benefit by seeking certification proactively. Certified suppliers are automatically more attractive to brands because they’ve already proven their color management capabilities; the brand doesn’t have to worry about training or lag time. In addition, some certification providers maintain databases that brands can search when looking for suppliers to work with.
Brands benefit from the capability to respond to market demands faster, with the confidence that color quality from all their suppliers will meet their expectations.
Implementation across an entire supply chain can shave several weeks off color developmental and production processes while providing greater transparency. In cases where the same color is being utilized by multiple suppliers, brands can expect much greater consistency and fewer rejections. Partnership with a third-party validation authority also eliminates the time, administrative and travel costs needed to send knowledgeable team members overseas to certify suppliers.
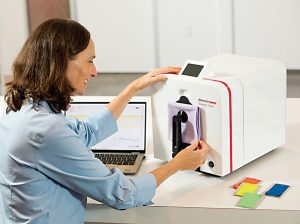
Improving Supply Chain Sustainability
In addition to improving the consistency and quality of products, partnership with a verification service can help support more sustainable supply chains. Wasted time, money, labor, materials and resources are significant issues for all industries. Minimizing the unnecessary carbon emissions associated with shipping samples or transporting team members across continents are also relevant concerns.
Getting color right the first time is the best way to reduce all of these things. This commitment to sustainability aligns with broader corporate responsibility goals established by many organizations, whether for their own sake or in response to regulations.
What To Look For In A Color Certification Partner
An expert verification service can help a company achieve more ambitious color formulation, measurement and QC goals. Here are some key factors to consider when evaluating potential partners.
Start by looking for a vendor that also makes high-quality measurement tools themselves, rather than relying on hardware from a third party. Its instruments should be capable of adhering to the industry’s tightest color tolerance ranges and have high inter-instrument agreement. With proper usage, good instruments can prevent suppliers from accidentally shipping products with off shades.
It’s important to also make sure instruments have 100-percent backward compatibility. This will ensure that any valuable color data curated over the years won’t be lost because of incompatibility with newer instruments when it’s time to upgrade.
In addition to trusted and reliable products, look for a partner with an even more valuable asset — people. Hardware and software should be supported by experts who have experience working in the industries they serve — ideally, for many years. This will ensure that they’re not only proficient in their company’s products and services, but have a deep under-standing of your industry’s unique needs and challenges.
Finally, make sure any investment in a solution is backed by a global team capable of providing guidance every step of the way, from choosing the right solutions through final installation and continued support thereafter. A partner should have a dedicated local sup-port team that speaks regional languages and is ready to help should problems arise.
Elements of a Complete Color Solution
Many well-known brands utilize color management technologies to bring end-to-end color solutions to their supply chains. Common packages include:
- Spectrophotometers: High-precision benchtop instruments used for close-tolerance color measurement, ensuring uniform assessment of materials across
the supply chain. - Performance monitoring: A predictive measurement monitoring system that assists with the calibration of spectrophotometers and correlates to master instruments to ensure performance meets a brand’s requirements.
- Formulation software: Amplifies the accuracy of color development, improving QC and productivity. This can significantly reduce the need for physical matches and improve first-shot match rates, shortening formulation time.
- QC software: Enables objective analysis, reporting, communication and visualization of accurate color results.
- Industry-specific applications: Specialized software is available to meet the unique needs of certain industries, including textiles, apparel, home furnishings, paint and coatings, plastics, and other applications.
- Light booths: Viewing stations that simulate a variety of lighting conditions, including daylight, common light sources used in retail stores, typical home and office lighting, LED, ultraviolet, and more. This enables visual color assessments of inks, paints, plastics, textiles, paper, colorants and other materials. Calibrated light booths across the supply chain promote consistency in color decisions by ensuring that everyone evaluating samples views them under similar lighting conditions.
- Operator training: Remote or hands-on instruction provided by experts fluent in the operator’s local language.
Editor’s Note: Basto Wong is the Service Project manager and head of Assessments at Lawrenceville, N.J.-based Datacolor.
2025 Quarterly Issue I