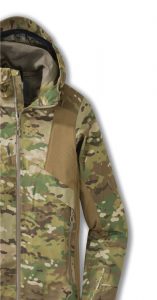
available from Seattle-based Outdoor
Research® features
GORE-TEX® fabric
with stretch technology.
TW Special Report
American armed forces are tasked with defending our country in the air, on land and at sea no matter how challenging the environment.
Because of the unique and global nature of this mission, the Department of Defense (DOD) must buy an estimated 8,000 different U.S.-made textile products annually to satisfy its various operational needs. When different sizes are factored into the item mix, there are some 31,000 line items sourced from the textile industry by the military each year.
Fortunately for America, manufacturers like Newark, Delaware-based W.L. Gore & Associates Inc. (Gore) and New Bedford, Massachusetts-based Brittany Global Technologies (Brittany) are up to the job of helping to make textile-based defense products that are the most technically advanced in the world.
Innovations For All Environments, Situations
Famous for its GORE-TEX®-branded consumer products, Gore also is a high-level innovator that manufactures military textiles, including those used in protective gear.
Jason Rodriguez, marketing communications manager, Military Fabrics, W.L. Gore, notes that the environment and a warfighters protection and comfort in that environment are of prime importance to Gore as the company conducts research and development on innovative fabrics for the armed forces.
“Our protective fabrics are designed essentially to help warfighters improve their mission effectiveness by staying alert, staying comfortable, staying dry, and remaining protected no matter what their environment is,” said Rodriguez. “Those are very important elements when developing high-tech fabrics within our business.”
Gore was founded in 1958 by Wilbert “Bill” Lee Gore and his wife Genevieve Walton Gore, initially serving the electronics market. In 1969 when Wilbert’s son Robert “Bob” Gore discovered expanded polytetrafluoroethylene (ePTFE), the company launched GORE-TEX and went on to become a leader in fluoropolymer technologies that apply to many different industries. The first GORE-TEX customer used the fabric in a tent application.
“GORE-TEX is our signature fabric within the Fabrics Division,” Rodriguez said. “It is our legacy product. However, we’re continuing to develop new fabric technologies around that — lighter weight and thinner products within the GORE-TEX portfolio — to continue improving mission effectiveness and assist with lightening the overall load for the warfighter. We are also developing innovations in new areas such as chemical and biological protection; uniforms that leverage ePTFE fiber; and self-extinguishing, flame resistant products.”
Some of Gore’s latest protective technologies for military applications include GORE® CHEMPAK® fabrics— used for chembio uniform applications that feature a stretch technology — and GORE® Katana fabric — a blend of ePTFE, nylon and cotton fibers specifically engineered for hot weather and tropical operations. According to Gore, uniform-specific fabrics optimize air-permeability, dry time and strength-to-weight ratio and can exhibit no melt or drip during flash-fire incidents.
GORE-TEX® PYRAD® is a weatherproof, breathable fabric that was designed to also offer a unique blend of flame resistance (FR), thermal insulation and thermal properties. Gore reports PYRAD® fabrics also are lightweight, fast drying and abrasion resistant. “GORE® PYRAD® is an engineered flame-resistant technology that can be integrated into waterproof and non-waterproof technologies,” Rodriguez said. “The technology has also been leveraged in tent applications.”
“Gore continues to expand our technical fabrics portfolio into areas that are providing enhanced protection against weather, contaminants or flash-fire incidents that the military is faced with,” Rodriguez said. “We focus on delivering this performance in garments, footwear and gloves. It’s a system level approach where Gore can provide a solution that can protect warfighters in the field.”
“In addition to having a rain chamber and various testing labs, Gore recently invested in a state-of-the-art heat and flame lab and comfort chamber,” said Donald C. Vavala, director, Military Government Affairs, Gore. “The heat and flame lab can simulate various test methods traditionally conducted by a third party. The comfort chamber was designed to replicate climates from across the world. Gore keeps investing in assets to ensure we can continue to provide great products now for the warfighter, but also meet the future needs of the warfighter.
“One thing I think helps Gore stand apart from other fabric providers is our comprehensive and robust understanding of our customers’ needs and the end-use application,” Vavala added. “Our commitment to fitness for end use is paramount. Our products undergo rigorous testing both in our facility and in the field to ensure they do what we say they will do first time and every time. We adhere to high standards of quality and product integrity. We want to make sure that our warfighters have an advantage when they are on the battlefield. Their protection is paramount in our minds — their ability to execute the mission and come back from the mission — and anything we can do to help that is hugely important to Gore.”
Expertise Required
Once a high-tech fabric is specified by the military, it must then be fine-tuned with camouflage and other special protective technologies to maximize its effectiveness for warfighters in the field. Brittany Global Technologies specializes in adding these enhancements through dyeing, printing and finishing.
Dyeing and printing are the two most common processing methods to color textiles. While dyeing produces only one color, printing is a more complex process whereby various colored designs are imparted on a fabric surface. Finishing refers to subsequent processes that turn a dyed or printed textile into a more useable product by improving its look, performance and feel.
“The specs are very numerous” said Ken Joblon, president, Brittany Global Technologies. “That’s one of the most challenging aspects of working for the U.S. military — being consistent with the specs as well as matching the colors accurately. They are extremely exacting.”
“The military needs stringent specs because they want the fabric to perform at its very best,” said John Kenyon, COO and vice president, Brittany Global Technologies. “Brittany has state-of-the-art equipment, a lot of technology developed over the years, and the military really looks to us now as someone that can provide the very best fabrics. It’s very proprietary in nature, but we do use special dyes, chemicals and formulations of course,” Kenyon added. “The soldier’s uniform just continues to get better and better. The soldier’s uniform needs to stand up to harsh conditions and needs to fulfill a lot of different functions.”
Brittany maintains a government certified lab with all the necessary testing equipment to be sure it meets the military’s specifications for each product. Every lot is certified with an official government report.
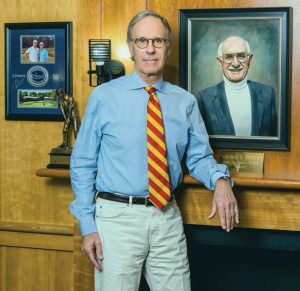
Brittany, founded in 1939, is a second-generation family business with a long history in textile printing and dyeing. In the early 2000s, the company — feeling pressure from low-cost imports — began investigating new markets to strengthen its business. The company’s willingness to innovate and diversify rather than stand still, led them to the military business.
“I feel gratified to play a part in equipping our military,” Joblon said. “I know our military has the best equipment available. We are all proud of what we do here, and it’s a fast-moving business. We have to be very nimble as things happen fast, and we must respond very quickly. In order to respond, many pieces must be in place, a few of which include having raw materials on hand, to having the right machinery, and having trained people to take care of whatever needs the government may have. That’s our culture.”
Editor’s Note: This article appears in Textile World courtesy of the National Council of Textile Organizations (NCTO) as part of the “American Textiles: We Make Amazing™” campaign. NCTO is a trade association representing U.S. textile manufacturing. Please visit ncto.org to learn more about NCTO, the industry and the campaign.
July/August 2018