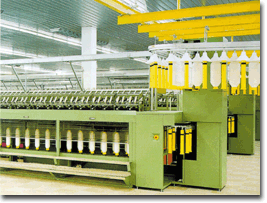
The Crisis in U.S. Textiles is, of course, the topic on everyones mind, and some may wonder
why we should be looking at technological advances when all eyes focus on Washington. Yet, in the
past, it was the tinkering of technologists and engineers, the vision of entrepreneurs and the
investments of textile managers in better equipment and processes that guided this industry through
unsteady waters.Textiles is not a dot.com business, but a long-term manufacturing industry.
Spinning does not produce virtual products, but real yarns that are used in many different
applications. And for this, spinners use equipment that is being steadily improved. These steady
improvements ensure the long-term vitality of yarn producers. Following is a look at some of the
improvements, with special consideration given to spinning man-made staple
fibers. CardingGermany-based Truetzschlers chute-feed system to the DK 903 card is produced
entirely from stainless steel to avoid finish build-up. The DK 903 carding system itself can be
adapted to run synthetic fibers through changes in the licker-in and cleaning units, and by
increasing the number of stationary carding segments of the Twin Top System TTS.Of course,
Switzerland-based Rieters reputation for processing 100-percent synthetic materials and blends on
the C-51 card is well-known. John D. Hollingsworth on Wheels, Green-ville, S.C., continues to
demonstrate its dedication to enhancing metallic wire performance through the development of the
Enhanced Point Wire that allows better transfer of fibers at the increased production speeds.
Continuously increasing throughput and production speeds is, of course, found with all equipment
producers. DrawingIncreased production and improved quality and efficiency remain the goals of
any incremental improvements in drafting. The technological level of short-staple drafting is best
seen in machines such as Rieters RSB-D30, or in the integration of carding in drafting, as shown in
Truetzschlers DK 903 and IDF. Such integration of traditionally separate manufacturing steps is
becoming more important with increased demands on quality, zero-error tolerances and, of course,
increasing labor-cost sensitivities.In the long-staple sector, France-based Schlumberger has found
a way to reduce fuzz in carpet yarns through high-speed gilling and spinning, which sounds like a
promising route to regain some of the carpet market share that has gone to
BCF-filament. SpinningWhile in many industries, market share is the primary reason for mergers
and acquisitions, in the spinning-machinery industry, one major focus of mergers is the potential
of the acquired technologies. Rieters purchase of parts of Suessen, Germany, is clearly motivated
by a quest for know-how. Technological leadership in ring spinning is demonstrated by the companys
entry into the Guinness Book of Records with the finest yarn count spun on ring-spinning equipment
(Nm 500 or 300 cc), spun from 100-percent PES on the G-33 ring-spinning frame. Rieters R-20
rotor-spinning machines are making a major impact in the U.S. market.Schlafhorst and Zinser, both
based in Germany, cover the range of rotor and ring spinning for synthetic yarns and blends.
Outside the United States, Zinser has commercial installations of the RM 350 spinning machine with
up to 1,488 spindles running. Increased efficiency and quality is achieved by linking the RO-WE-MAT
670 roving frame directly to spinning through integrated doffer and transfer stations. This direct
link avoids damage of the bobbins, as well as any human errors.Drafting systems in roving, as well
as spinning, show pneumatic loading for consistent pressure over time and for the entire machine.
The PK series from Germany-based TEXParts shows such approaches for new machines, as well as for
after-market improvements. Also state-of-the-art is the servo-drive or multi-motor drive approach
in the drafting system.Delivery speeds in rotor spinning are increasing, especially for blended
yarns with lower twist levels. For example, Schlafhorsts Autocoro 312 can produce at delivery
speeds of up to 250 meters per minute (m/min) with up to 240 spindle units at more than 100,000
revolutions per minute (rpm). Producing 100-percent synthetic yarns is more speed-sensitive, with
rotor speeds typically under 90,000 rpm.Notable improvements are being made in the suction systems,
providing a constant vacuum pressure in the spinbox. The constant pressure results in fewer ends
down and higher efficiencies, while at the same time providing consistent quality. Italy-based
Savios FRS spinning unit produces low-twist yarns at rotor speeds of up to 107,500 rpm and take-up
speeds of up to 200 m/min from a range of synthetic fibers.Charlotte, N.C.-based Murata of America
Inc.s MJS 802HR jet spinner is capable of producing a wide variety of yarns from blends and
100-percent synthetic materials. The new drafting system offers draft ratios of up to 300, allowing
the production of very fine yarn numbers. At the same time, the air-jet process allows the
production of core yarns or special blended yarn structures. Muratas MVS vortex spinner is not yet
used for synthetic yarns.When looking at coarser yarn counts, one must mention Austria-based
Fehrers DREF 2000 friction-spinning machine. As shown at ITMA 99 in Paris, the yarn count now goes
up to Nm 25 (14.5 cc), and the operation of the machine has been simplified for the operator while
its cost efficiency has improved. Last February, Fehrer opened a new demonstration center in Linz,
Austria, and the company indicated that a new DREF 3000 demonstration machine with three heads will
be available for testing at that location. Winding
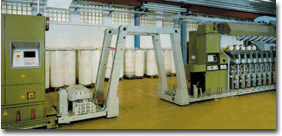
Winding is often treated as an afterthought to spinning, yet it is an extremely critical
step. Winding provides the final inspection of a yarn and the presentation of the final product to
a customer or the next processing step. With higher production speeds and increasing quality
requirements, producing a yarn package has more complex technical requirements than before,
especially when processing synthetic yarns. For todays winders, it is (or soon will be)
state-of-the-art to have computers at each position controlling the individual motors and sensors.
Intelligent winders focus on efficient motions rather than speed; fine tuning reduces unnecessary
clearing and improves efficiency; tension is more closely controlled and corrected through
closed-loop approaches, as they are known in autolevelers in carding or drafting. An example of
this approach is the Autotense yarn-tension control in Schlafhorsts Autoconer 338. Uniform tension
and package density is critical for processing downstream.Links between spinning and winding are
also becoming more important. Direct linking can prevent yarn damage during transport and,
especially for mills running many different products, can also prevent mix-ups of yarn due to human
error. The Autoconer 338 comes with up to 60 spindles on each link machine. In most cases, however,
mills link approximately 1,000 to 1,200 ring-spinning spindles with 26 to 36 winding positions.
Times are not easy for spinners these days, nor for anyone in textiles, for that matter.
State-of-the-art technology, sufficient tenacity, and some twist is needed to keep the numbers
right, in the yarn as well as in the books. Good technology is available, and spinners have
tenacity or they would be doing something else. Lets find the necessary twist.
Editors Note: Helmut H.A. Hergeth, Ph.D., is an associate professor in textile and apparel
technology and management at North Carolina State Universitys College of Textiles, Raleigh,
N.C.
October 2001