New dye lab equipment shortens testing times, ensures more precise measurements for improved
quality control.As business conditions for the U.S. textile industry become more and more
competitive, the stresses on the industry’s manufacturing processes and methodologies become
correspondingly more demanding.
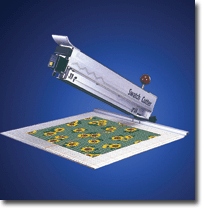
New dye lab equipment shortens testing times, ensures more precise measurement for improved
quality control.Today’s environment places a premium not just on price and quality, but on delivery
as well. Quick response is becoming the norm for those companies that want to grow or maintain
market share – and many U.S. textile companies are finding that their blue-chip customers will
accept nothing less. As a result, equipment and machinery manufacturers that supply the industry
are looking for innovative new ways to both cut production and testing time and ensure the
elimination of as much off-quality product as possible. Perhaps nowhere in the industry is that
more evident today than in testing and measurement equipment made for the dye lab.The modern dye
lab must be a sophisticated, scientific operation geared toward creating unparalleled consistency
and quality. From the manner in which shrinkage and elongation are measured, to the tolerance
specifications for color matches, there is little room for error. It is a well-known, if not
acknowledged, fact that inventory garners close scrutiny during lean economic times. Even the
suggestion or perception of variance from standards can send a perfectly good lot of yarn or fabric
back to the manufacturer as rejects.Therefore, one is more likely today to see rigorous testing
methods that drastically reduce both sampling and production time and labor; sophisticated
color-measurement devices that enable more exacting color matching; and state-of-the-art software
that does everything from evaluating samples, to monitoring production, to managing post-production
inspection and analysis.”Reducing testing time, eliminating redundancy and creating less
opportunity for off-quality goods – all of these factors can contribute significantly to the bottom
line of the manufacturers who are our customers,” said J. Mark Raiteri, president and CEO, Raitech
Inc., the Charlotte, N.C., manufacturer of textile control and measurement systems. “Our mission at
Raitech has been to provide these customers with relatively inexpensive equipment that creates the
opportunity for a rapid return on investment.” Shrinkage TestsAmong the company’s flagship products
is its Quickwash Plusª system. Originally developed in 1997 by Raitech and Cotton Incorporated,
Cary, N.C., an enhanced version, model EC300, was made available last year. Essentially, the
Quickwash Plus system radically reduces the time it takes to test for dimensional stability and
other fabric properties that require a washing and drying process. “The system reduces shrinkage
testing to about 15 minutes for most fabrics instead of up to 8 hours,” Raiteri said. “The
Quickwash Plus system uses a patented method for inducing the relaxation and shrinkage behavior of
textile fabrics. The process is one where a sample or samples are separately submitted to a short,
but complete, washing cycle in a whirling, oscillating hot-water bath followed by short rinse
cycles. Afterwards, the samples are subjected to a very short hydroextraction cycle and then
submitted to drying in a hot air stream. This method of drying induces constant motion of the yarns
at crossover points and flexing of the yarns in the fabric structure.” The Quickwash Plus system is
composed of a perforated vertical drum that contains up to five radially arranged partitions that
divide the space into an equal number of chambers capable of bi-directional rotation, he said. The
drum is enclosed in a thermally insulated protective casing covered by a lid and connected
mechanically to a shaft that can provide alternately a rotational or oscillating motion. The drum
has connections to a pressure air inlet from an air heater, a common water inlet for regulated
heated water and a water outlet for drainage. In addition to shrinkage, the Quickwash Plus system
can be used to evaluate a fabric’s tendency to spiral, twist or change in appearance. As well,
Raiteri said, it can be useful in reducing both time and effort in the determination of
colorfastness.”The overall benefit of the product is, of course, that it reduces the time it takes
to ensure the production of a quality product,” Raiteri said. “But also important is the fact that
the time and fabric savings alone can pay for the product in six months or less. The system only
uses one-fifth the fabric other testing methods require.”More than 300 Quickwash Plus units have
been sold, 100 of which have been to U.S. companies. “Currently, there is at least one Quickwash
Plus system in every country in the Americas,” Raiteri said. Customers include Cotton Incorporated,
National Textiles, Russell Athletics, Cone Mills, GaleyandLord, Guilford Mills and others, he
said.The latest offering from Raitech is a product called Quickviewª, an optical measurement device
for fabric shrinkage. “Quickview will do in a minute what it takes 15-30 minutes to do by hand,”
Raiteri said. “It eliminates up to 18 separate hand measurements.”Raitech also has available its
Quickcircleª fabric sample cutter; Quickcutª fabric cutter; Quickdryª fabric sample dryers; and
Quicktempª water temperature controller system. Testing ColorfastnessWhile the primary mission of
the Quickwash Plus system is to test for fabric shrinkage, United Kingdom-based James H. Heal –
represented in the United States by Advanced Testing Instruments Corp. (ATI), Greer, S.C. – focuses
on colorfastness with its Gyrowash machine. The latest incarnations of the Gyrowash range of
machines are used to investigate the fastness to washing, dry cleaning and chlorinated water of
colored textiles and leather.
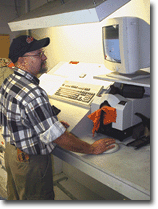
Steven Webb, National Textile, checks color and quality of fabric prior to cutting with
ColorTools¨ software from Datacolor.Softrol, Acworth, Ga., manufactures a catalyst system,
ChemPulse, that includes a redundancy feature that continues chemical delivery to all washers when
one unit is taken out of service for maintenance or repair. Each catalyst, according the company,
can work in a preferred network range of machines to ensure equal utilization of
equipment.SpectrophotometersSpectrophotometers measure light reflected from an object at each
wavelength in the color spectrum. New developments in this arena include the LCS+ Liquid Color
Spectrophotometer from Mahlo America Inc., Spartanburg, S.C., and the CM-2600d portable from
Minolta, Japan.The LCS+ is a highly precise transmission spectrophotometer that spectrally measures
the color of transparent liquids, according to Udo Skarke, executive vice president, Mahlo America
Inc. “It makes sure the pigment in the dyes is the same,” he said. The LCS+ is designed for use
with disposable plastic cells, high-precision optical cuvettes or 11-millimeter (mm) tube cells.The
CM-2600d from Minolta is the first portable spectrophotometer on the market with instantaneous
ultraviolet (UV) adjustment, according to Norm Demers, technical support manager for Minolta’s
Light and Color Applications Center Instrument Systems Division.The product is lightweight and
compact and features dual apertures of 3 mm and 8 mm, Demers said. The CM-2600d performs like a
bench-top spectrophotometer and is suited for measuring fluorescents, paper, textiles or any
product with optical brighteners. Also from Minolta is the CM-3600d benchtop spectrophotometer for
reflectance and transmittance color measurement. This product, according to Demers, performs faster
and more accurate measurements of samples with gloss differences and offers instantaneous numerical
UV adjustment for samples that contain a UV-absorbing light component, such as fluorescing dyes,
pigments and optical brighteners.As well, Minolta offers the CL-200 Light Source Chroma Measurement
System, which can perform measurements of tristimulus colorimetrics, chromaticity, color
difference, correlated color temperature and illuminance of light sources. The CL-200 System
features an expandable modular design that uses compact and lightweight interchangeable components,
according to Demers. The system can be used for such applications as research and development of
light sources; color adjustment of cathode ray tubes (CRTs); flat panel displays and other display
devices; color evaluation and control of light boxes and booths; and optimum installation of
projection systems and presentation lighting.An ongoing argument for some concerns exactly when a
fabric should be tested for color consistency and quality. Should the greige fabric be tested for
consistency and dyeability before production is finished – or should the final product be tested to
measure conformity to specifications Mahlo’s Skarke told Textile Industries that U.S. manufacturers
in general produce dyed fabric and then use off-line testing as a quality control feature. “What we
are finding, however, is that a number of European companies are beginning to test fabric in-line
in order to be able to make quality decisions on the production floor. To this end, Mahlo has
developed its Colorscan CIS-10 offering, an on-line sensor that runs back and forth across the
fabric during production. The CIS-10 logs any variations in shade, both across and along the length
of the fabric.”The CIS-10 can measure properties on-line and at high speed after mercerizing, after
the range, at just about any step in the process, and can cull bad greige goods. That way, the
textile manufacturer knows very quickly that the products being manufactured are top quality. This
is faster, provides less waste and increases efficiency,” said Skarke.Testing Light Stability And
WeatheringOf course, color consistency, colorfastness and dimensional stability are not the only
factors that determine the quality and marketability of a particular yarn or fabric. Resistance to
the deteriorating effects of sunlight and other harsh lighting systems, for example, is critical to
the performance of many products today, particularly activewear. The Q-Sun Xenon Test Chamber,
manufactured by Q-Panel Lab Products, Cleveland, uses full-spectrum xenon arc lamps to reproduce
the damaging wavelengths of light encountered in a multitude of environments, according to Ronald
L. Roberts, U.S. sales manager. The Q-Sun can be used to simulate and accelerate these conditions
for both research and development and quality-control applications. The Q-Sun is used for the
selection of new materials, the improvement of existing materials or the evaluation of how changes
in formulations affect product durability. In addition to photodegradation, Roberts said, the Q-Sun
can also be operated as a weathering tester.From SDL America Inc., Charlotte, N.C., the M237 Light
Fastness Tester determines colorfastness and sunlight degradation through the use of a 500-watt
mercury-blended tungsten lamp. The machine includes a presettable timer and time-elapsed counter.
The SDL M237 can be fitted with type C, D or E sample holders within which humidity can be
controlled using saturated salts. The company also has available a rapid fade model fitted with a
400-watt mercury tungsten high-powered lamp.Software For Control, EfficiencyNot all of the
improvements in quality measurement and production efficiency are related to manufacturing
equipment. A number of software offerings are on the market that assist companies in formulation
and dispersement of dyes and chemicals, as well as product testing and sorting.SheLyn Inc.,
Greensboro, N.C., has its SLI-Form¨ package that can interface with a wide variety of
spectrophotometers. In addition to formulation, SLI-Form can evaluate dyeings to ensure accuracy in
formulations and can correct or fine-tune formulas in production, according to Ann C. Laidlaw,
manager, color applications.DCIMatch from Datacolor International, Lawrenceville, N.J., provides
for the matching of any shade on any substrate or blend. DCIMatch features the company’s Smart
Match¨ Expert System, which “learns” the behavior of dyestuffs, processes and substrates in order
to match color theory to real world practices.GretagMacbeth, New Windsor, N.Y., offers its
ProPalette Textile Formulation software, a complete quality control program that measures color
difference, plots variations in color and features pass/fail tolerancing for all major color spaces
and illuminants. As well, ProPalette offers dyestuff calibration and performance
monitoring.National Textiles – Committed to CustomersIf there is one thing management at the
National Textiles LLC plant in Forest City, N.C., has learned in an era of extreme competitive
pressure, it’s that quality is a process-by-process measurement.”Today, we’re driving quality into
the process, instead of waiting until the end,” said Bonnie Davis, the plant’s quality manager.
“Two years ago, we would do quality audits on the finished product. Now more than 90 percent of our
quality is checked in process from the very beginning.”
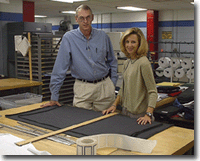
Plant Manager Ken Warren and Quality Manager Bonnie Davis inspect dyed knits at National
Textiles’ Forest City TextilesAs a result, the plant has reduced its lead time and increased
production efficiency – while continuing to manufacture highly respected dyed knit fabrics.National
Textiles is a vertically integrated company, encompassing everything from yarn to cut fabrics. At
the Forest City Plant, yarn is brought in from sister facilities, knitted, dyed and finished. The
plant ships about 1.3 million pounds of finished fabric per year and cuts about 200,000 dozen
samples per week.Like many other companies in the U.S. textile industry, National Textiles feels
the mounting pressure from the expanding influx of low-cost foreign textiles, particularly from the
Far East. The company, however, is committed to a strategy it believes will keep National
competitive through the rollback of quotas in 2005 and beyond.”We key in on things that are really
important to our customers,” Davis said. “We identify those things they are really looking for and
focus on them.”That commitment runs through the company, from top to bottom, Plant Manager Ken
Warren said. “Our basic philosophy is simple. We give our customers what they want when they want
it. We’re working with lead times we wouldn’t even have thought about a few years ago. The
commitment runs not only to processes but also to equipment purchases. National’s Forest City Plant
was among the first facilities, for example, to embrace the Quickwash Plus system offered by
Raitech Inc. Armed with the potential of saving time and simultaneously increasing quality, Warren
saw the opportunity to serve both his customers and the company.”The Quickwash Plus machine has
really taken our fabric performance to a new level. It gives us a much quicker view of what the
fabric will be like after the compaction process,” Warren said.”To meet our objectives today, we
can’t hold up a product for a lab test that might take six hours or more before we can begin
cutting fabric,” Davis said.National uses other state-of-the-art systems, such as ColorTools¨
software by Datacolor International, to ensure dyed fabric is within customer specifications. The
company has a reputation of being among the lowest-cost manufacturers of knitted fabrics in the
United States. But that is only part of the reason behind the company success, according to
Davis.”People usually come to us because of price,” she said. “But they stay because of the quality
and service they receive.”Today, our focus, instead of on mass production, is on the individual
lots that we ship to our customers. On-time performance is measured on a weekly basis. Our quality
process has enabled us to move product through the plant without getting stopped along the way.
And, if for any reason the flow does stop, we know how to address and correct the situation
quickly.”In an era in which competition has made quick response the norm, on-time performance is
especially critical if a company is to keep its customers. “If a product doesn’t ship within our
specified lead time, it’s late,” Warren said. “And being late gets a lot of attention around here.
But we believe that – if we continue to deliver a high-quality product that exactly meets our
customers’ wants and needs and deliver it on time – then we will continue to grow. I truly believe
that if you focus on service and quality, you will not lose customers.”Prospects for continued
success for National are good, Warren said. The company is comfortable without being complacent.
Indeed, there are many challenges looming on the horizon, but both Warren and Davis believe
National’s commitment to customer service will be more than enough to keep the company at the top
of supplier lists for many of its customers.
December 2001