Roll-A-Reel PresentsPortable Handling DeviceCincinnati-based Roll-A-Reel Co. has added a new portable space-saving model, Style C, to its line of Roll-A-Reel devices for pay-out or take-up of reeled materials. The new model is load-rated per CEMA standards at 3,000 pounds and will accommodate reels of any width.Style C requires only one operator. It consists of two platforms that are placed individually behind the reel flanges for roll-on reel loading. The built-in steel loading ramp and spring-loaded front roller lock eliminate the need for jacks, cranes or other tools.February 2002
Unifi Jassin-O39 Rourke Seminars Show CBI At Work
Unifi, Jassin-O’RourkeSeminars Show CBI At WorkA series of seminars hosted by Unifi Inc.,
Greensboro, N.C., and New York City-based Jassin-ORourke Group LLC, and designed to help companies
understand how to profitably market the Caribbean Basin Initiative (CBI), recently took place in
Greensboro, New York City, the Dominican Republic, Honduras, El Salvador and Guatemala. U.S.
knitters, weavers and converters of polyester- and nylon-content fabrics, and CBI apparel
manufacturers learned how to better leverage CBI advantages through the supply chain.Michael
Delaney, senior vice president, Unifi, noted that 60,000 textile jobs have been lost due to a
consumption slowdown and import growth. However, U.S. textile market potential is getting bigger,
not smaller. The increase was 7 percent in 2001. Asias market share dropped 70 percent, while
market share from Mexico and CBI countries increased between 30 and 40 percent.Stewart Little,
senior vice president, Unifi, said apparel manufacturers and retailers have no conception of the
CBI advantages in cost and quick turnaround. Mary ORourke, managing director, Jassin-ORourke, said
the CBI can drive growth for companies through elimination of tariffs on textile apparel imports
that contain U.S.-manufactured fabrics and yarns. U.S. companies that leverage CBI advantages
through the supply chain can demonstrate to customers down stream an edge over Asian prices and
time-to-market.Turnaround time is faster from Honduras, ORourke pointed out. Retailers and
manufacturers can eliminate up to six weeks of lead time. With shorter order cycles and quick
replenishment of stock and reorder options, companies can carry decreased inventories.ORourke
stated the view that the domestic textile industry is commodity-oriented, requires large minimums
and long lead times is no longer true. There is also a misconception that Asian fabrics are
cheaper.Eight Caribbean countries represent 95 percent of the apparel business, each having its
special niche. Today, the experts agree, manufacturers and retailers must be shown how a
full-package apparel program is an economic advantage and a cost saver.
February 2002
Malden Mills Receives Funding
Malden Mills Receives FundingLawrence, Mass.-based Malden Mills Industries Inc., which recently
filed for reorganization under Chapter 11 of the U.S. Bankruptcy Code, has received $20 million in
funding from its lenders to enable it to continue operating during the reorganization process.This
reorganization allows Malden Mills to emerge from the challenges we have faced since the
catastrophic fire that nearly destroyed our company in late 1995, said Aaron Feuerstein, president
and CEO, anticipating that the 95-year-old company will emerge as a stronger, more highly focused
and profitable company.Following the fire, Feuerstein immediately rebuilt the companys facilities
in Lawrence, continuing to pay his employees during the reconstruction. The new Polartec® building
was the first mill built in New England in more than a century.The company filed for reorganization
due to the cost of servicing bank debt, a sluggish retail market, high reconstruction costs and the
closing of its upholstery division following the fire. Maldens patented Polartec fabrics are used
for all outdoor activities and are the sole fabrics used in cold-weather gear for the U.S. Army,
Marine Corps and Special Operations Command.
January 2002
January 2002
Peter Hegarty has assumed responsibilities for the company’s global marketing and
sales efforts.
Atlas Electric Devices Co., Chicago, has appointed
Larry W. Masters president and CEO; and
Jack L. Martin president, Atlas Weathering Services Group.

Masters
The West Conshohocken, Pa.-based
American Society of Testing and Materials (ASTM), Committee E18 on Sensory
Evaluation of Materials and Products has presented its David R. Peryam Award to
Gail Vance Civille, president, Sensory Spectrum. The award recognizes outstanding
professionals in applied sensory science.
The Hosiery Association (THA), Charlotte, N.C., has elected
Sally Kay president, following the retirement of
Sid Smith.
Fairlawn, Ohio-based
OMNOVA Solutions has elected
James J. Hohman vice president of the company. Hohman also serves as president of
the company’s Paper & Carpet Chemicals Division.
Woolrich®, Woolrich, Pa., has promoted
David Becker to operations manager, retail; and
Mike McCarter to general merchandising manager, retail. In addition, the company
has named
Valerie Beggs designer, women’s sportswear; and
Phoebe Hogeland designer, outerwear and sporting group.
TSG Inc., North Wales, Pa., has named
Robert M. Beaty vice president, sales. He will oversee both the SynFin Industries
and Synthetic Finishing Divisions.
The
Synthetic Organic Chemical Manufacturers Association (SOCMA), Washington, has made
the following appointments:
Cedric Calhoun, director, marketing;
Charlena Patterson, director, human resources; and
Robert Dickinson, controller.
The Washington-based
American Fiber Manufacturers Association (AFMA) has elected
Bradley Hill, Solutia, chairman; and
Geoff Schofield, Drake Extrusion, vice chairman and chairman of the Executive
Committee.
Walter W. Hubbard, BASF Corp., was elected treasurer.
Springs Industries Inc., Fort Mill, S.C., has named
R. Dean Riggs executive vice president, home furnishings operations. Riggs is
responsible for Springs’ bed and bath manufacturing operations, overseeing approximately 30 plants
and 11,000 employees in eight states.
Sara Lee Activewear, Winston-Salem, N.C., has named
Kim E. McAleer senior vice president, operations. McAleer previously served as a
vice president of Anvil Knitwear.

McAleer
Germany-based
Mayer & Cie. announced the following management changes: co-owner
Rainer Mayer, along with his brother
Peter Mayer, will focus attention on Group functions; Rainer Mayer has
relinquished responsibility for operative sales management to
Oliver Scharf, sales manager;
Reiner Plankenhorn, purchasing manager, has been appointed general power of
commercial representation as sole signatory;
Rolf Willmer continues as development manager; and
Rainer Müller as production and operations manager.
WestPoint Stevens, West Point, Ga., has named
John Cafaro vice president, sales, Bed and Bath Division, for Kmart, Sears and
regional mass retailers.
New York City-based
Kellwood Co., has appointed
Kathy White president, EMME® Division; and
Stephen L. Ruzow president, womenswear.
Mount Vernon Mills Inc., Greenville, S.C., announced the promotion of
Charles L. Little Jr. to president, Yarn Sales Division and LaFrance Division.
Teijin Ltd., Japan, has appointed
Toru Nagashima president and COO. Nagashima assumes the presidency from
Shosaku Yasui, who retains his position as CEO and has assumed the position of
chairman of the company.
Appleton, Wis.-based
Rollguard® Products, a subsidiary of Great Northern Corp., has named
Mike Cattanach account manager for the Southeastern United States.

Cattanach
The
Industrial Fabrics Association International (IFAI), Roseville, Minn., has electedDonald M. Reinbolt chairman of its Board of Directors. Reinbolt has served on the
Board since 1991.
January 2002
KoSa Restructures Textile Fibers Business
KoSa RestructuresTextile Fibers BusinessKoSa, Charlotte, N.C, has restructured its textile fibers business. Three distinct business segments have been created nonwovens, filament and fine-denier staple.Directed by Paul Latten, the nonwovens segment will join KoSas other specialty industrial fibers businesses in the technical fibers business group, which is led by Thomas Kehl, vice president and general manager.To create vertical integration benefits and leveraged sales opportunities for commodity and specialty polymers and filaments, the filament segment now reports to Thomas Fahnemann, vice president and general manager, intermediates and polymers and filament. Mario Fonseca manages the filament segment.The fine-denier staple segment, managed by Marco Espinosa, now reports to Carlos Sierra, business director, packaging resins and fine-denier staple.January 2002
Magnetic Technologies Offers New Payoff Brake
Magnetic TechnologiesOffers New Payoff Brake
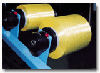
Magnetic Technologies Ltd., Oxford, Mass., has developed a magnetic payoff brake for use in winding composite material, yarn, film and wire. The brake includes shaft, adaptor and locking system to hold the payoff material and has a torque range of 1/2 to 12 inch pounds. A new calibration system provides improved reading and adjustment.January 2002
Aprion Digital Establishes Ink Plant In Israel
Aprion DigitalEstablishes Ink Plant In IsraelIsrael-based Aprion Digital has opened its third plant. The newest plant in Be`er Tuvya, Israel, will produce ink for its patented MAGIC (Multiple Array Inkjet Color) drop-on-demand piezo ink-jet technology. An ink-jet-head production plant and an industrial digital press assembly line were opened previously.The new plant has the capacity to produce up to 3,000 metric tons of ink annually for application on packaging, outdoor signage and home furnishing applications, according to Eyal Ben-Amram, vice president of operations. This plant will enable Aprion to provide its advanced, environmentally friendly ink to its customers worldwide, Ben-Amram said.The ink plant will be operated in association with Israel-based Tzah, an ink manufacturer for the traditional printing industry.January 2002
National Spinning Acquires Two Glen Raven Facilities
National Spinning AcquiresTwo Glen Raven FacilitiesNational Spinning Co. Inc., Washington, N.C.,
has acquired the open-end spinning and package-dyeing business of Glen Raven, N.C.-based Glen Raven
Inc. The acquisition includes two plants located in Alamance County, N.C., which are now integrated
into Nationals operations as Alamance Spinning Plant and Alamance Dyeing Plant of National
Spinning. More than 200 associates at the plants are now among Nationals base of 1,600
owner-associates.Despite being in an environment that has not favored domestic textile producers,
National is fortunate to be in a position to expand its core business, said Jim Chestnutt,
president and CEO, National. This move will emphasize our commitment to U.S.-based manufacturing
and North American/Caribbean markets. We will continue to support our customers with the highest
quality products and service, to assure their success in difficult markets.
January 2002
Unifi Completes Refinancing Enters Into New Facility
Unifi Completes Refinancing, Enters Into New FacilityUnifi Inc., Greensboro, N.C., has completed
refinancing of its existing credit facilities and has entered into a new $150-million facility with
Bank of America N.A.Unifi has used the facility to refinance its existing $150-million revolving
credit facility and a $100-million accounts receivable securitization, as well as to finance
working capital and investment needs.From December 31, 2000, to the date of the refinancing, we
have reduced our borrowings by approximately $155 million, said Billy Moore, executive vice
president and CFO. We will remain focused on strengthening our balance sheet by maximizing cash
flows generated from sales growth, reducing operating costs, controlling capital expenditures and
lowering working capital levels.
January 2002
Bayer Signs Agreement For China Investment
Bayer SignsAgreement For China InvestmentGermany-based Bayer has signed an agreement with the Shanghai Chemical Industry Park Co. Ltd. for a production site in China. Bayer plans to invest $3.1 billion in the site.Asia continues to show high long-term potential despite a possible short-term slowdown as a result of the economic weakness in the U.S., said Bayers CEO, Dr. Manfred Schneider. To expand business in the region, Bayer will therefore continue to commit substantial funds to establish facilities for production and product development in China.Construction began on the new production site which will combine several individual production facilities into a network-sharing infrastructure in November 2001.The three core projects include operations to manufacture colorants and coatings systems, thermoplastics (Bayers polycarbonate Makrolon®) and polyurethane raw materials.In addition to these primary projects, Bayer has further plans for high-performance plastics facilities, as well as plants for additional precursor products and basic chemicals.According to Schneider, the total value of Bayers investment program in Asia, initiated in 1994, will reach approximately $6 billion by the year 2010.January 2002