ATMI Presidents D.Y. Cooper, 1910-1911, was president of Henderson Cotton Mills and Harriett Cotton
Mills, Henderson, N.C. He was born in Granville County, N.C., April 21, 1847 and died in Henderson
on December 20, 1920. As ACMA president, he stressed development of a sounder foreign trade.Captain
Ellison A. Smyth, 1911-1912, was associated with Francis J. Pelzer in establishing Pelzer
Manufacturing Company at Pelzer, S.C. and was a founder, officer or director of a number of other
mills in South and North Carolina. He is credited with installing the first incandescent lighting
system in an American cotton mill in f1882: the first electric drives used in cotton mill in 1895;
and the purchase of the first Draper automatic looms. He also was involved in banking, in the
newspaper business, and in the electric power industry. As president of the South Carolina Cotton
Manufacturers Association, he was the first to sponsor a state child labor law. Captain Smyth was
born in Charleston on October 25, 1847 and died August 3, 1942 at the age of 94.W. A. Erwin,
1912-1913, began his textile career in 1882 and for some 11 years served as general manager and
treasurer of E. M. Holt Plaid Mills in Alamance County, N.C. He established Erwin Cotton Mills Co.
a West Durham, N.C., and, at the time of his death, also controlled the Durham Cotton Manufacturing
Company, the Pearl Cotton Mills, Oxford Cotton Milles, Locke Cotton Mills Co. and Erwin Yarn Co. He
was born July 15, 1856 and died February 28, 1932.Scott Maxwell, 1915-1916, began his career at
Androscoggin Bag Mill, Lewiston, Me., and worked in mills in New England, South Carolina and
Alabama before becoming mill agent at Indian Head Mills, Cordova, Ala. in 1903, a post he held
until his death in 1916. He was born at Webster, Me., July 8, 1855, and died November 4, 1916 at
Dover, N.H.John A. Law, 1916-1917, worked actively for a closer relationshop between Southern and
New England manufacturers. He was a member of the committee that organized the Cotton-Textile
Institute, and was an original member of the National Industrial Conference Board. He served for
many years as president of Saxon Mills, Spartanburg, S.C.Fuller E. Callaway, 1917-1918, organized
and directed anumber of cotton mills in Georgia, the best known being Callaway Mills at LaGrange.
He served as ACMA president during the difficult first year of World War I, then became chairman of
the Commission on European Representation at the World Cotton Conference, which he served as vice
president. He was born at LaGrange, Ga., on lJuly 15, 1870 and died February 12, 1928. A son, Cason
J. Callaway, served as Association president 1931-1932, and another son, Fuller E. Callaway, Jr.,
was first vice president.Arthur J. Draper, 1918-1919, president of Chadwick-Hoskins Co., Charlotte,
also served as president of the North Carolina Cotton Manufacturers Association. He was born on
April 28, 1875 and died April 26, 1932.James D. Hammett, 1919-1920, was born March 16, 1868 at
Greenville, son of Colonel Henry Pinckney Hammett, one of the South’s pioneer cotton manufacturers.
He began work at the bottom of the mill in 1890, because assistant treasurer of Orr Cotton Mills,
Anderson, S.C. in 1900 and went on to organize Chiquola Manufacturing Co., Honea Path, S.C. and to
serve as president of Chiquola, Anderson Cotton Mills, Brogan Mills and Orr Cotton Mills, all at
Anderson and Watts Mills, Laurens, S.C. He was a director of Piedmoont and Northern Railway and
active in banking. A son, L.O. Hammett, became president of the South Carolina Cotton Manufacturers
Association.Stuart W. Cramer, 1913-1914, is credited with having planned or equipped one-third of
the cotton mills operating in the South at the time of World War I. An inventor of note, he was
granted more than 60 patents. He was president of the National Council of American Cotton
Manufacturers in 1917-1918 and again from 1920 to 1927. He was a vice president of the
Cotton-Textile Institure, and a director and treasurer of the Textile Foundation. The National
Association of Cotton Manufacturers awarded him a medal in 1913 for his work on the protective
tariff.T. I. Hickman, 1914-1915, was second president of The Graniteville Co., 1889-1915. As
Association president, he campaigned energetically for more extesive use of cotton goods, even
attempting to get railroads to replace the traditional blue serge of conductors with cotton khaki.
He was born April 14, 1866 an died in Augusta, Ga., on March 21, 1941.
ATMI Presidents 1910-1920
Sara Lee Acquires National Textiles, DFK Trading Corp
Sara Lee Branded Apparel, Winston-Salem, N.C., has acquired National Textiles LLC, a
Winston-Salem-based vertically integrated yarn and textiles manufacturer; and DFK Trading Corp.
Ltd., a sourcing company based in Hong Kong. The acquisitions are part of Sara Lee’s strategy to
establish a global supply chain.
National Textiles manufactures open-end and ring-spun cotton and blended yarns, as well as
finished tubular knit fabrics. The company employs approximately 2,900 people at facilities located
in Georgia, Tennessee and Virginia, in addition to North Carolina. Operating as DFK International
Ltd., a wholly owned subsidiary of Sara Lee Branded Apparel, DFK will source raw materials in Asia.
Sara Lee Branded Apparel is in the process of separating from Chicago-based Sara Lee Corp.
The spin-off is expected to be completed by September 2006.
October 2005
The Country And The Industry Pull Out Of The Depression
The Country AndThe Industry PullOut Of The DepressionThe Depression lasted 42 months, reaching a
low point in March, 1933, according to the technical definition of economists. For most people, the
Depression lasted until the onset of World War 11.In human terms, the 42 months were devastating:
industrial output cut almost in half; one in four without jobs; one-third of the railroad mileage
held by bankrupt companies; foreclosures on farm mortgages so widespread that gangsters robbing
banks were folk-heroes; banks themselves threatened by runs and unpaid loans. The Commodity Price
Index (1910-14 = 100) fell to 86.4 in 1930; to 73 in 1931; to 64.8 in 1932. The Census Bureau index
of all stocks 11926-100) went from 149.8 in 1930 to 48.6 in 1932.In July, 1930, The Reporter was
talking of “conservative optimism”; the official line from Washington was that “prosperity is just
around the comer.”But, said The Reporter, “unless large gains in consumption are chalked up,
production this year is going to be a considerable extent below the estimates that were made at the
beginning of the year.” Mill production was then estimated at barely 50% of capacity.Mills Start
ClosingCotton consumption in the U. S. and overseas in May was the lowest since September 1924;
wool consumption for the first four months was the lowest since 1920. Mills were able to sell in
May only 66.9% of production and at the lowest prices in 15 years. Inventories piled up. Cash and
credit ran low. Mills began closing.The Reporter, realistic but positive, sought silver linings in
the clouds: Why is the textile industry singled out as one that is suffering What other industry is
in better shape Isn’t the whole industrial and business structure of the country depressed “Last
year (1929), something more than 500 state and national banks failed. The other day, the Hamilton
Brown Shoe Co., one of the biggest in the country, went into receivership. Anyone who knows Lynn,
Brockton and Haverhill, the great shoe centers of the country, is aware of the fact that the shoe
business is very quiet.”Last year, the Fisk Rubber Co. Lost $7 million; the United States Rubber
Co. Lost $3 million; the Hood Rubber Co. was taken over by a stronger organization; so was the
Miller Rubber Co. and previously the Apsley Rubber Co. “One radio company after another has folded
up. The automobile business isn’t good. Dodge Brothers was taken over by Chrysler; Pierce Arrow
taken over by Studebaker; the Jordan people asked their stockholders to put up more moneyand that
is only a small part of the story. Packard has just slashed prices. Chrysler announces a big cut.
The non-essentials are getting it just as much as the staple industries.”The machine tool business
is bad. The newsprint producers are suffering. The Canadian government itself has interceded in the
newsprint situation endeavoring to raise prices. It isn’t only textiles.”In the cotton goods
industry, the line of demarcation between the North and the South has been obliterated. The
situation in the South is no better than in the East, if as good.”The Maginnis Cotton Mills of New
Orleans has been shut down since January first. The 50-50 plan of curtailment to better market
conditions is to help the southern mills. The F. W. Poe Mfg. Company shares sold the other day at
$28, and this has been one of the most successful print cloth mills in the country for a great many
years, and, for the last half dozen years, on fancy goods from print cloth numbers. Victor Monaghan
is cutting the dividend. “The condition of the textile industry parallels the condition of every
other industry in the country. It isn’t only textile shares that are selling low. Obviously, then,
selected mill shares offer Just as good opportunities for a long term investment as do the
securities of any other industry.”Bennett’s SuggestionsAs the Depression deepened, Editor Bennett
inveighed against inefficiency and the differing job assignments in unionized and non- union mills.
In July, 1930:”In one big worsted mill here in Massachusetts, there are 60 clerks in the efficiency
department with a payroll in that one department of at least $90,000 a year, equal to 6 percent on
$1,500,000. If the mill is profitable, it is in spite of this so-called efficiency work,” he wrote,
declaring that a firm of consulting engineers could lay out an efficiency program for a fraction of
the cost of the clerks, 4but a whole litter of efficiency clerks 60 of themare a dead weight.”And,
in September:”The full-fashioned hosiery branch of the textile industry exemplifies the effect of
complete unionization. Full-fashioned operatives in unionized millsand these are mill workers, not
presidents and treasurersaverage $100 a week wages, and, in some mills, earn $150 a week wages.
These operatives tend only one full-fashioned knitting machine. They are very arbitrary about
apprentices. The owner of a full-fashioned mill can’t put his own son into the mill to learn the
business unless the union lets him. The unionized operatives, not the owners, run the mill.”The
operatives in the non-union full-fashioned hosiery mills in North Carolina, for instance, earn $40
a week and tend two machines.”And he cited another example in September:”Nearly two years ago, the
cotton mill operatives of the Newmarket Manufacturing Company were induced by the board of
officials of the United Textile Workers to go out on strike. For more than 19 months, now the
Newmarket cotton division has been shut down, and today the machines are being sold and the mill is
to be given up. But, as of July 30th, the official report of the United Textile Workers of America
reads as follows:’The Newmarket strikers were very cheerful at their meeting I attended Tuesday,
July 15th. Much credit is due these people for the manner in which they have fought the New- market
Manufacturing Company. After 18 months of struggle, they are still determined to see the strike to
the bitter end, and their morale is in splendid shape.’But, the cotton mill is shut down, all the
operatives have lost their jobs and the town is to be abandoned.More Work AssignedThe Reporter gave
an example of how to properly apply an increase in job assignment, called by workers “the
stretch-out”:In a Southern mill, a woman weaver tended 24 looms. The superintendent thought she
could handle more and suggested she try 60. She did, but found the work too much. The
superintendent then suggested she try 55, which she found she could handle. By agreement, half the
savings went to the weaver, half to the company. The weaver was told not to talk about her pay
increase, but word got around and other weavers applied to tend more looms. “Now,” said the
Reporter, “a thousand looms are operated with less than half the weavers.”Despite the sharp
downturn, some business was good. The Goodyear tire fabric plants were being expanded while many
mills were closing. Goodyear then had mills at St. Hyacinthe, Quebec; Atco, Cedartown and Rockart,
Ga.; New Bedford, Mass.; Killingly, Conn.; Los Angeles, Calif.; and in England, Australia and
Brazil.And, complained Editor Bennett, people owning “toy golf courses” were getting rich overnight
while real business suffered. The miniature golf courses were springing up everywhere, in vacant
lots and empty stores, a craze that peaked and quickly slumped.By October, The Reporter said the
textile business was “much improved” with employment up 18%. At the Southern Textile Exposition
that month, exhibitors filled all permanent space plus that in a steel annex and temporary wooden
annex 130 x 40. Some 40,000 visitors jammed the aisles, and sales were said to be good. The
Southern Textile Association and the textile section of the American Society of Mechanical
Engineers met concurrently. A hit of the show was Draper’s new looms for rayon and silk, and a new
high-speed warper.Four million spindles had been junked by that time. Of the 20 million spindles in
the Southern states, 10 million were on 24-hour operation. The Cotton Textile Institute called for
an end to night operations by March 1, 1931.False DawnBut, the upturn was a false dawn. By
mid-1932, American industry was operating at less than half of the 1929 production rate.Spindles in
the textile industry had peaked in the Twenties, and the decline was to continue over the years as
improved machinery and methods increased the output per spindle. For woolen and worsted machinery
the figures were not spindles and looms as well as those in Mass. R.I., and Pa., the main woolen
and worsted producing states.The dominant company, American Woolen, was operating 744,737 spindles
and 8,437 looms. As an aside, Howard Bennett was responsible in 1936 for continuing the annual
meeting of the American Woolen Co. for three days and two nights, without adjournment, to force
through a change in management. Time Magazine referred to the event as the rowdiest, longest annual
stockholders meeting ever held. The Reporter participated in the fight, conducted it, paid for the
proxy solicitation and the lawyers’ fees, and ended up eliminating the incumbent president and
chairman.All Business SuffersThe total amount of wages paid in all business and industry in all of
1932 was only 40% of the 1929 total.Business suffered a net loss for the year of more than $5
billion, and that was when a billion dollars was BIG money. Total dividends were cut by 57%. Stock
values, followed the over-the-clifftrend: U. S. Steel from 261 3/4 in 1929, to 21 174; General
Motors from 72 ¾ to 7 5/8. Cotton sold for five cents a pound, sometimes less.President Hoover
worked hard at trying to organize optimism. He summoned the big bankers, the top industrialists and
businessmen to Washington where they conferred and issued statements saying that conditions were
fundamentally sound and that prosperity really was just around the corner. But nothing
changed.Then, Hoover declared a moratorium on reparations from Germany and on war debts due from
the Allies, hoping to stimulate foreign trade. The world only went deeper into depression.Despite
pleas from around the country, the president refused to entertain the idea of any federal action to
relieve the distress of the millions of unemployed; that was a matter for individual charity and
local government.Then he set up the Reconstruction Finance Corporation to provide federal aid to
banks and businesses. Banks continued to fail, businesses continued to close.Washington was greatly
alarmed that summer when World War I veterans including a few who talked revolution, marched into
the city to demonstrate for war-service pay bonuses. The 17,000-man “bonus army camped for weeks,
then was driven out by troops headed by Army Chief of Staff, Douglas MacArthur. Roosevelt
Elected,More Banks CrashAnd so Franklin Delano Roosevelt easily won election over Mr. Hoover in
November, but Mr. Hoover’s tribulations had yet to reach their depth. That winter, the banks
crashed. By March 2, 1933, two days before the inauguration of the new president, 5,504 banks had
closed, and 23 states had suspended or drastically restricted banking operations. By Inauguration
Day, nearly every bank in the United States was closed or under restriction.President Roosevelt
sparked hope with his inaugural address, the famous “we have nothing to fear but fear itself,” and
immediately took action. He declared a four-day national bank holiday to allow bankers time to
reorganize. Within three days, 4,507 banks reopened, and within two weeks, stock prices rose 15%.
He called for a special session of Congress to convene March 9th.The importance to morale of
Roosevelt’s words and actions was deeply impressed on this writer’s mind the following Sunday when
he heard J. W. Arrington, president of Union Bleachery, Greenville, S. C., say to “the Dunean
crowd” as he joined them in front of Christ Church: “Gentlemen, we have just escaped
revolution.”100 DaysIn 100 days of legislative action, that special session of the Congress changed
life in these United States. Among the acts that emerged from frenetic sessions of the House and
Senate:
- The Emergency Banking Relief Act.
- The Economy Act, cutting government pay and veterans pensions 15% to help balance the
budget. - The act creating the Civilian Conservation Corps that put 250,000 jobless young males to work
in the forests and national parks. More than 500,000 were on the rolls at peak point, and, by 1941,
some 2,000,000 had passed through the CCC ranks. - The Beer-Wine Revenue Act legalizing beer and wine with up to 3.2 per cent alcoholic
content. - The Federal Emergency Relief Act providing $500 million in grants to states and municipalities
for work relief projects. - The Agricultural Adjustment Act providing subsidies to farmers for reducing crops.
- The act creating the Tennessee Valley Authority to build dams and power plants and develop a
vast area involving Tennessee, North Carolina, Kentucky, Virginia, Mississippi, Georgia and
Alabama. - The Federal Securities Act.
- The National Employment System Act, establishing the U. S. Employment Service.
- The act creating the Home Owners Loan Corporation to refinance home mortgages.
- The act creating the Federal Deposit Insurance Corporation, guaranteeing deposits up to
$5,000. - The Farm Credit Act.
- The Emergency Railroad Transportation Act.
- The act creating the Commodity Credit Corporation to lend to farmers on their crops; in the
early years, loans primarily to cotton farmers, bolstering cotton prices. - The act creating the Public Works Administration which spent $4.25 billion on 34,000 public
works projects, mostly road and public buildings. - And, most important of all, the National Industrial Recovery Act, providing for industry
self-regulation through “fair competition” codes governing operating conditions; participating
industry was exempt from the anti-trust laws.
Section 7a of the Act guaranteed the right of labor “to organize and bargain collectively
through representatives of their own choosing,” applying to 22 million workers in 500 industries or
areas of business. A National Labor Relations Board was set up to enforce the right of collective
bargaining.In a few brief months, the Congress had enacted into law nearly all the planks in the
socialist platform of the 1890’s and l900’s.Yet, business and industry welcomed the NRA at first,
principally because it promised stability. In those days, state legislatures were continually
considering legislation on hours, wages and other matters affecting business and many executives
claimed they spent more time on political matters than in running their business.Spread The
Work;Spread The Jobs!In the spirit of the times spread the work, spread the jobsThe Cotton Textile
Institute that spring recommended to the textile industry that the work week in cotton mills not
exceed 40 hours, and that production machinery not be operated more than two 40-hour shifts per
week.The original members of the Cotton Textile Industry Committee which negotiated with the
National Recovery Administration on the NRA code for the mills were: George A. Sloan, president of
the Cotton Textile Institute; Thomas M. Marchant, president of the American Cotton Manufacturers
Association; Ernest N. Hood, president of the National Association of Cotton Manufacturers; William
D. Anderson, Robert Amory, Harry L. Bailey, Bertram H. Borden, G. Edward Buxton, Cason L. Callaway,
Charles A.Cannon, A. E. Colby, Donald Comer, Stuart W. Cramer, B. B. Gossett, R. E. Henry, Gerrish
H. Milliken, Frank I. Neild, H. Nelson Slater, Robert T. Stevens and Robert R. West. They dealt
with General Hugh (lronpants) Johnson, NRA administrator.Pick-up In ’33The Reporter noted that “the
cotton textile industry has advanced from 51% of capacity in July, 1932 to 129. 1% of capacity in
June, 1933, and some textile machinery firms are sold ahead for many months.”The industry’s former
over-capacity was being drastically reduced: “Never before has there been such a liquidation and
junking of textile equipment as has been carried out in New England during the last few years,” The
Reporter said in commenting on the reduction in New England from 20 million to 12 million spindles,
a loss of 6 million spindles in Massachusetts alone.By spring of 1934, disenchantment with NRA and
its codes and multitude of regulations was growing. The Reporter said it received seven and a half
pounds of mail from NRA in one day.”Manufacturers generally seem to be afraid to tell the whole
truth about how the NRA affects their business. Some of them have government contractsperhaps they
are afraid the government will cancel the orders. The present government does cancel contracts and
does go back on its word. It does make the profoundest promises worthless.”They may be afraid of
labor troubles initiated by someone outside the mill. There are authorities in political office who
could start a strike in any mill. The whole country is intimidated. Business has been bad for so
long a period that the hope of a quick profit, perhaps a phantom profit, and the opportunities for
speculative advance in raw materials seem to have destroyed the old time insistence on the part of
American businessmen that the truth and sound practices are more important than a temporary
advantage.”Labor Unrest GrowsIn mid-April, Bennett reported: “A Fall River mill operating executive
writes us that the labor leadership in that town is dominated by aggressive people. Tuesday, April
10th, the employees in a very large plant in that city walked out. The labor leaders presented a
long list of alleged grievances, one of the most serious being that overseers within the mill
favored with the work certain operatives who were undeserving of it and that the favoritism was for
ulterior purposes. Thursday, April 12th, the labor leadership presented the management with a list
of 35 persons who must be discharged before the strike can be settled. Who is running the mill”Mill
workers had grown bolder about union membership since the Government placed its stamp of approval
on unions with Section 7a of the National Industrial Recovery Act guaranteeing the right to
organize. For many, the stigma formerly attached to unions was removed. Many new locals were
organized. In mid-August, the United Textile Workers’ board voted to call a general strike in the
textile industry on or by September 1st, demanding a 30-hour maximum work week, six hours for five
days, at the same pay as for the current 40-hour week; industry-wide recognition of the union as
representative of all industry workers, and the adoption of specified work loads (described by
management as “ridiculous”).The strike was on, but not all workers struck.Newspapers reported that
as of September 6th, 73% of the industry’s 410,000 operatives were at work. In the North, 32,000 of
100,000 workers walked out; in the South, 60,000 of 154,000. The percentage of strikers varied
widely by locality. And not all who walked out stayed out. There were hotbeds of union fervor, such
as Gastonia in North Carolina and Spartanburg in South Carolina.Union ViolenceThe hotbeds spawned
“flying squadrons”caravans of trucks and cars loaded with strikers moving from mill to mill,
rushing into plants, cutting off machinery, flourishing clubs (and an occasional pistol) and
intimidating those at work. Half the mills in the Carolinas closed, but only briefly, for the
National Guard was called out to protect mill property and those who wanted to work.Tempers flared
when strikers attempted to block men trying to enter the mills to work. Deputies were guarding the
main entrance and strikers were gathered in front when first shift workers appeared at Chiquola
Manufacturing in Honea Path, S. C. Angry words were exchanged, gunfire erupted. Six strikers died
and 13 were wounded.Reaction To ViolenceReaction to the flying squadrons resulted in stories still
told today, some of them surely apocryphal. They tell of:
- The dyehouse worker at Cliffside, N. C., who climbed to the mill tower and aimed a stream of
sulfuric acid at the squadron below. - The workers at a Greenville mill who had walked out a few days earlier in a dispute with
management, had returned, asked for, and received an issue of picker sticks with which to greet the
squadron. - Col. Elliott White Springs, a World War I fighter pilot, flying out from the mill to scout the
approach of a squadron reported moving in from Gastonia and, so goes one version, rolling his
plane’s wheels on the cab of the lead truck, causing the group to turn back lest the Colonel “get
real mad.” To protect his workers, Col. Springs did close several plants until the National Guard
could arrive to protect them.
A presidential commission brought an end to the strike, a failure for the UTW whose memory has
lingered for decades, often thwarting the efforts of other organizers. Not long afterward, the
ClO’s Textile Workers Organizing Committee (TWOC) moved in to salvage what they could of the UTW
faithful and work just as unsuccessfully on their own. The organizing group included Miss Lucy
Randolph Macon (of the Virginia Randolphs) who served as publicity director.A side effect of the
UTW strike was the postponement of the October, 1934 Southern Textile Exposition to the spring of
1935 because Textile Hall was commandeered for use as barracks for the National Guardsmen called to
the Greenville area.Peace Restored:Technology RevivedWith labor peace restored, interest in new
machinery was mounting by the time of that Spring 1935 show. The Reporter had commented earlier
that “big package spinning is very interesting to the worsted industry….the changeover from cap
spinning with one-ounce packages to ring frames with 4-oz. packages is being generally
considered.”President Roosevelt NRA was declared unconstitutional by the Supreme Court in 193S, but
FDR succeeded in getting Congress, to pass a National Labor Relations Act to continue government
backing for unions. Also passed then was the Social Security Act. In 1937, the president became a
cropper when he tried to pack the Supreme Court; the Southern Democrats defected from his cause.
But, he staged a comeback in 1938 with the wages and hours law setting a minimum wage of 40 cents
an hour within eight years, beginning the stairstep with a 25 cents an hour minimum, and a maximum
work week of 40 hours within three years, beginning with a 44 hour maximum. The act also mandated
time-and-a-half pay for over 40 hours, and forbade labor by children under 16.Improved Rayon
ThrivesThe 10- and 12-hour work day and the six-and-a-half day week were to become memories, as
were the days when the natural fibers were sole rulers of the textile roost.Consumption of rayon
had outpaced that of silk in the late 1920’s. Now, in the late 1930’s, the first resin finish for
rayon was available, substantially improving the hand of rayon fabrics, and the first rayon tire
cord was being produced.The Reporter was running weekly sections on rayon, and commented that “a
very large percentage of the growth and profits of the textile industry is going to come from the
cotton goods industry going into rayon work. The rayon weaving is going to be in the old,
established cotton mills, rather than in the silk mills, because cotton manufacturing has always
been a more economical, more efficient industry than silk manufacturing. Cotton mill methods are
far ahead of silk mill methods.”The domain of the natural fibers was also being invaded by other
fibers besides rayon. Commercially useful glass fiber was produced by Owens-Corning Fiberglas Corp.
in 1938, used first as a filter medium for air conditioning and as insulation. By the end of the
decade, glass yams and fabrics were established in a number of industrial uses and in draperies,
curtains and tablecloths.Cotton responded to the challenge. The National Cotton Council was
organized November 21, 1938 at the Peabody Hotel in Memphis, Tenn., by cotton producers, ginners,
seed crushers, warehousemen, and merchants. The Council’s major thrust at the beginning was
research and promotion, but it quickly became involved in government affairs. Textile Manufacturers
joined the Council a few years later. Cotton co-operatives, which had been part of other interests
from the beginning, became a separate interest in the Sixties. Observers say the Council has held
together for nearly 50 years because of a key bylaw provision that no position is taken without at
least majority approval of the delegates from each interest voting separately DuPont’s nylon fiber,
on which Wallace Carothers had begun research back in 1928, went into commercial production at
Seaford, Del., in 1939. The first nylon stocking would captivate the nation’s women in 1940.In the
summer of 1939, The Reporter was commenting that the “worsted business, particularly on
lightweights and tropicals for men’s wear, is already feeling the effect of Southern competition,
and cut worsted staple and cut rayon staple blended yarns, are generally made in the South, and
much of it woven in the South. Riverside and Dan River have 500 looms on woolen mixture men’s wear,
a big cotton mill. A weaver in New Hampshire has purchased a lot of cut worsted and rayon blended
yarns for weaving men’s wear fabrics, the yarn coming from Cannon and from Textiles, Inc. in
Gastonia and from other Southern mills. There isn’t any status quo in any branch of the textile
industry.”Rising Tide Of WarNor was there any status quo in the world. Hitler’s Germans and
Mussolini’s Italians had successfully dueled with Russia in the Spanish civil war, and had won.
Then, Hitler brow-beat the British and French into appeasement at Munich in 1938 and Czechoslovakia
died. In April, 1939, Italy invaded Albania, and, in May, signed a military alliance with
Germany.On August 2, 1939, Albert Einstein wrote President Roosevelt alerting him that recent
research made possible an explosive device based on splitting the atom.On August 23rd, the Russians
and Germans signed a non-aggression pact.On August 31st, The Reporter commented on “a sense of
foreboding” in the textile industry: markets uncertain, woolens withdrawn by large producers and
the wool auction at Sydney postponed.On September 1st, Germany invaded Poland.World War 11 had
begun. The atomic bomb had been conceived. Vast changes lay ahead.
Haggar Enters Into Acquisition Agreement
Dallas-based Haggar Corp. parent company of Haggar Clothing Co., which markets and licenses men’s
casual and dress apparel and womens sportswear has entered into an agreement with Infinity
Associates LLC; Perseus LLC, Washington (through an affiliate); and Symphony Holdings Ltd., Hong
Kong; whereby Infinity, Perseus and Symphony would acquire Haggar for $212 million. Haggar
stockholders would receive $29 in cash for each share of common stock held.
“This transaction provides
outstanding shareholder value and represents an endorsement of the excellent performance of our
entire team,” said J.M. Haggar III, chairman of the board and CEO, Haggar Corp. “With the new
ownership team and our ability to utilize their respective capabilities, we will be able to
accelerate our strategy of world-class sourcing and will strengthen the marketing power of our
owned and licensed brands, as well as our service to the private-label market. The net result will
be a stronger, more nimble company that is better suited for growth in the global apparel market.”
The merger agreement has been approved by Haggar’s Board of Directors.
The transaction, expected to close by the end of this year, is contingent upon approval by
Haggar stockholders, regulatory review and funding of debt to complete the acquisition.
October 2005
Material World New York Debut Exceeds Expectations
2005 at the Jacob K. Javits Convention Center, Material World New York exceeded show management
attendance expectations and generated solid business results for exhibiting companies. Urban
Expositions and the American Apparel & Footwear Association (AAFA) plan to build on the
momentum of this inaugural edition to firmly establish Material World New York as the city’s
premier global fabric, sourcing and trend exhibition for fall.
“Based on the strong attendance numbers and positive feedback we’ve received from many of
our exhibitors, we think we’re off to a great start with Material World New York,” says Tim von
Gal, executive vice president, Urban Expositions, producers and managers of Material World. “As
pleased as we are, we know we have not yet begun to fully tap the potential of this New York
exposition. Looking forward, we plan to continue building on our attendee marketing efforts to
fully penetrate the local New York market, as well as the domestic and international audiences.”
“The premier of Material World New York was an outstanding showcase bringing together a
balanced presentation of sourcing, fabric, and technology,” offers Kevin M. Burke, President and
CEO, AAFA. “Coupled with the educational programming, the expanding international presence, and the
New York venue, it is fast becoming a must-attend industry event.”
Featuring 325 exhibiting companies, Material World New York showcased the latest
introductions and innovations from leading companies from around the world in every sector,
including fabric, trim, yarn, components, technology, color/trend forecasting and more. With a
broad international scope, Material World’s exhibitor base represented 22 countries. Further
expanding the global exhibitor participation, the New York edition also featured the ASAP Global
Pavilion, which showcased products and services from countries, including Bangladesh, India, Japan,
Korea, Pakistan and South Africa.
The exhibition attracted key decision-makers from branded apparel companies, private label
retailers, sourcing executives and other key categories. “There has been a strong mix of attendees,
especially at our trend presentations. We’ve met sourcing executives and designers from both large
and small companies,” said Abby Klanecky, global communications manager, Dow Fiber Solutions.
“We were impressed with the quality of attendees, finding it significantly better than that
of other apparel shows,” adds Lawrence Serbin, president, Hemp Traders. “I’m also impressed with
the show’s diversity – besides apparel, we’ve also seen more textile and footwear manufacturers.”
Responding to the city’s position as an international fashion and retail leader, Material
World New York also featured a number of trend and educational resources. In addition to a dramatic
trend pavilion in the center of the exhibit hall highlighting fall/winter 2007, Material World New
York offered a number of trend forecast presentations from leaders like Trend Union, Pantone and
Cotton Incorporated. The educational program also touched on key industry topics through the AAFA
line-up, including The Next Frontier in Fabric, Fiber & Thread; New and Different Ways to
Finance International Transactions, and Do’s and Don’t’s in the New Trade Era. Putting the
spotlight on technology, the AAFA’s Supplier & Resource Division program, Technologies That
Enable Today’s Global Apparel Industry, was followed up by a number of presentations from
exhibiting technology vendors and leaders, including [TC]2, QuestaWeb, New Generation Computing and
Geac Apparel North America.
Based on exhibitor feedback, the 2006 edition of Material World New York will shift from a
Wednesday to Friday date pattern, to a Tuesday to Thursday schedule, September 26-28, 2006.
The spring edition of Material World Miami Beach is scheduled for April 4-6, 2006. In
addition to offering a spring/summer fabric and sourcing opportunity, Material World Miami Beach
also puts the spotlight on Technology Solutions, the exposition and educational conference for
information technology enabling the sewn products industry. Both events run concurrently at the
Miami Beach Convention Center.
Press Release Courtesy of Urban Expositions
October 2005
ATMI Presidents 1950-1960
ATMI Presidents 1950-1960George P. Swift, III, 1950-1951, grandson of the founder of Muscogee
Manufacturing Co., Columbus, Ga., was born April 9, 1888; graduated from the University of Ga.;
joined Muscogee in 1909, became vice president in 1942; and chairman of the board in 1962. He
became chairman of the board of Columbus Fiber Mills when the firm was founded in 1946. His
business affiliations included chairmanship of Fourth National Bank, Columbus; founding director of
Georgia International Life Insurance Company; director of Tom Huston Peanut Co.; and director of
Swift Spinning Mills, Columbus. He was a founder of Archer Mills, Columbus, which merged in 1940
with Wayne Knitting Mills, Fort Wayne, Ind.C. C. Hertwig, 1951-1952, a native of Macon, Ga., joined
Bibb Manufacturing Co. after service in France with the 33rd Division. He was named progressively
assistant treasurer, treasurer, vice president, and, in October 1947, president of The Bibb. He
retired in October, 1956. He served as president of the Cotton Manufacturers Association of
Georgia; vice president of the Cotton Textile Institute; trustee of the Institute of Textile
Technology; and director of the National Cotton Council.W. A. L. Sibley, 1952-1953, began his
textile career as superintendent of the Whitney Manufacturing Co. and the Ware Shoals Manufacturing
Co., later becoming associated with the Milliken interests. He attended the U.S. Naval Academy and
the Georgia Institute of Technology. He served as a director of the Federal Reserve Bank of
Richmond and the Charlotte branch of the FRB.H. K. Hallett, 1953-1954, a native of Reading, Mass.,
made his textile career in the South after graduation from Dartmouth College, working with Langley
Mills, Langley, S.C.; Draper Corp.; Graniteville Co.; Wateree Mill, Camden, S.C.; Thrift Mill, Paw
Creek, N.C.; rising to president of Pelzer Mills, Pelzer, S.C., 1948-1953; and vice president of
Kendall Mills, Cotton Mill Division in 1956.J. Craig Smith, 1954-1955, a graduate of Virginia
Military Institute, led the 1956-1957 fight that spotlighted the increasing burdens imposed on
American industry by low-wage foreign countries. A native of Birmingham, Ala., he joined Avondale
Mills, rose to president of Avondale and a number of trade associations.Arthur Knox Winget,
1955-1956, born in Mecklenburg County, N.C., on October 26, 1882, entered the textile business in
1909 with Colonel C. B. Armstrong of the Armstrong group of mills, becoming secretary/treasurer a
few years later. The Armstrong group merged with Textile-Incorporated in 1931. He became president
and treasurer with American YarnandProcessing Co. in 1952 to become AmericanandEfird Mills Inc., he
then became chairman of the board. He was a director of ACMI for 17 years and also served as
president of the North Carolina Assocation.F. E. Grier, 1956-1957, was serving as president of the
South Carolina Textile Manufacturers Association when he became president of ACMI. At the time of
his death, he was president and treasurer of Abney Mills, Anderson, S.C.; and chairman of the board
of Erwin Mills, Durham, N.C. Born on November 17, 1899 in Due West, S.C., he began his career in
banking and became president of the Bank of Greenwood in 1933, holding that post until 1942.L. G.
Hardman Jr., 1957-1958, son of a physician who served as Governor of Georgia, graduated from the
University of Georgia in 1950 and went on to a varied career including the presidency of Harmony
Grove Mills, Commerce, Ga.; presidency of First National Bank of Commerce,; and of Frozen Food
Lockers, Inc. He served as president of the Cotton Manufacturers Association of Georgia; president
of the Textile Education Foundation at Georgia Tech.Halbert M. Jones, 1958-1959, a 1929 Phi Beta
Kappa graduate of the University of North Carolina and of the Harvard Business School, joined
Waverly Mills, Laurinburg, N.C., in 1931, became president and treasurer in 1935. He was an
organizer, vice president and treasurer of Scotland Mills Inc., Laurinburg, treasurer of Morgan
Jones Inc.; New York, and treasurer of Aileen Mills Co., Biscoe, N.C. He served as president of the
North Carolina Textile Manufacturers Association and of the Carded Yarn Association.James A.
Chapman, 1959-1960, holds the distinction of being the first man to have served as president of the
Southern Textile Association, the South Carolina Textile Manufacturers Association and ACMI. He
joined the family firm, Inman Mills, in 1916, and succeeded his father as president in 1936. A
graduate of Wofford College, he served his alma mater as trustee for many years and was awarded an
honorary doctor of laws degree. He also served as a trustee of Presbyterian College, Clinton, S.C.,
and was a founding trustee of the Spartanburg County Foundation.
ShanghaiTex To Be Held Annually Starting In 2006
To fulfill the strong requests of many of its exhibitors and China textile enterprises visitors,
the famous International Exhibition on Textile Industry in Shanghai (ShanghaiTex), will be changed
into an annual event starting 2006 from its original cycle of once every two years. ShanghaiTex is
sponsored by the Shanghai Textile Holding (Group) Corporation, China Council for the Promotion of
International Trade Shanghai Sub-Council and China Chamber of International Commerce Shanghai
Chamber of Commerce. The Fair is organized by Shanghai Textile Technology Service and Exhibition
Centre, Adsale Exhibition Services Ltd. and Shanghai International Exhibition Co. Ltd. Since the
inception of the Fair in 1984, the organizers of ShanghaiTex have been working consistently in
enlarging the scale of the Fair and maintaining an international standard for the exhibiting
services.
“We are pleased to see that ShanghaiTex is now the largest textile machinery fair in Asia and
one of the World’s most professional and authoritative textile events. ShanghaiTex 2005 (The 11th
International Exhibition on Textile Industry in Shanghai), held from June 3 to 7, 2005 at the
Shanghai New International Expo Centre, gathered over 1,400 worldwide renowned suppliers from 23
countries and regions (including the participation of 10 country/ group pavilions). A visitor flow
of 121,516 trade buyers from over 60 countries and regions were attracted to this mega show, which
occupied an exhibition area of 100,660 square meters. However, due to the limited exhibiting area
of the venue in Shanghai, about 100 companies did not get space allocation to their applications to
the show while several hundreds of exhibitors had to exhibit in 25,000 square meters of temporary
halls, which undermined the safety and effectiveness of their participations.East China is one of
the most prosperous textile production bases in China. The textile industry in East China has
gradually developed into a blooming stage with Shanghai as the dragon-head, complemented by
Zhejiang and Jiangsu Provinces. This results in a very high expectation on ShanghaiTex as a
platform to showcase advanced textile technology and equipment.
After the successful completion of ShanghaiTex 2005, there were numerous requests from
textile enterprises which expressed their strong wishes in having an annual ShanghaiTex to enable
them to have a timely review of the latest and innovative textile technology and equipment close to
their production base. In response to the pressing demand of the textile industry and the request
for better exhibiting environment from a few hundred exhibitors, ShanghaiTex will be held annually
starting from 2006. ShanghaiTex will continue to focus on setting a high international standard for
the Fair and to help in speeding up the brand building of Chinas textile industries.ShanghaiTex
2006, the 12th International Exhibition on Textile Industry, will be staged from July 5 to 8, 2006
at the Shanghai New International Expo Centre, PR China. As less than 50,000 square meters of
exhibiting space will only be available, ShanghaiTex 2006 will emphasis on the most advanced
textile technologies from local and overseas. It is expected that the show will help the local
textile enterprises to accelerate the modernization of their equipment.ShanghaiTex 2007 will
continue to be held in June 2007 with a forecast exhibition area of 120,000 square meters, and it
will be the 13th edition of the Event.
Press Release Courtesy of Adsale Exhibitions Services Ltd.
October 2005
Foam Products Corporation: Silence Is Golden
S
erving
major laminate flooring
manufacturers, specialty textile companies and label printers, Foam Products Corp. (FPC), Calhoun,
Ga., has an interesting history that exemplifies the flexibility necessary to remain competitive.
With 50 employees and approximately $15 million to $25 million in annual revenues, FPC stays busy
making more than 10 million yards of coated fabrics annually. Ninety percent of its business is
domestic, with the majority of exports slated for Canada.
Ken Garner, vice president and general manager, said the company was started in 1978 by
entrepreneurs James Shook, Jerry Arnold and Jerry Kassel as a manufacturer of latex foams on fabric
for the footwear industry. FPC began as the sole source of insole material for Dr. Scholl’s® and
developed additional sales of product to other footwear companies.
“In the early ‘80s, Dr. Scholl’s built its own foam plant in Georgia and began supplying
most of its needs,” said Garner. “FPC was established with domestic footwear companies and enjoyed
strong sales. However, [after losing the Scholl‘s account] a new division was started, producing
hot-melt-coated fine papers for carpet and mattress labels. This business was well-suited to our
proximity to the carpet industry, and it has grown steadily over the years.
“In the late ‘80s,” Garner continued, ”the demise of the US footwear industry was in full
force. Manufacturers were leaving in droves for Asia, especially China. By the early ‘90s, it was
obvious that companies like FPC would have to shift emphasis in order to survive. Manufacturing
facilities were added to allow the production of frothed polyurethane foams. Although the target
markets were still hazy at the time, they soon became clear. A small trade show in the mid-’90s
brought to our attention a new product. European producers of laminate flooring were making their
debut in the United States. Believing that there was an opportunity for a better acoustical
underlayment than they were offering, we went to work on it as a polyurethane project.”
The result of that work was The Silencer™. “It is still our flagship product and the most
popular wood underlayment brand in North America,” Garner said.
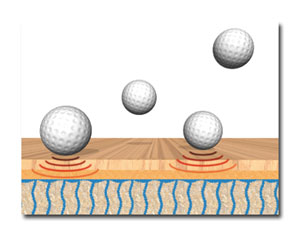
reflected sound and sound transmission.
Expanding The Business
“Shortly after The Silencer’s
introduction, we expanded our Calhoun facility to 100,000 square feet,” Garner said. “We have
continued to develop and promote our acoustical underlayments, which are sold under our brand as
well as those of major laminate manufacturers.”
Like most aspects of manufacturing, looking for and responding to a changing marketplace is
essential.
“We continue to look at opportunities to grow with shifting market demands,” Garner said. “
Where it is possible, we stay with our core competency — foaming and narrow web coating. Beyond
underlayments, we see plenty of opportunity. It was very rewarding to be the first entry into a
booming market, and we would like to go there again.”
When asked about the challenges in the marketplace, Garner responded: “It is not imports. We
need to generate the right ideas for growth and work immediately to become better and more
efficient than potential competitors. Sometimes that means filtering out products where we can’t be
a leader. We have been flexible enough to make dramatic changes in order to accommodate significant
new business. We do it quickly. We have people who are bright and well trained and have great
attitudes. This gives us the confidence to take on difficult projects.”
Investing Where It Counts
With 2 to 3 percent of revenues
reinvested in research and development, FPC strives to place those investments strategically in
order to maximize return.
“Recently, we have modified one of our coaters significantly in order to perform some unique
coatings on difficult-to-handle fabrics,” Garner said. “We have partnered with companies that we
believe are going to be very successful in producing barrier fabrics. We needed to upgrade our
web-handling capability. A lot of our machinery had not changed significantly since the ‘80s.”
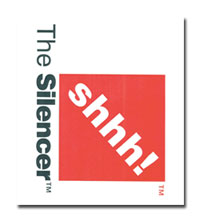
Quality Matters
“There are many challenges relative
to manufacturing and quality when producing such a versatile array of products on a single
production line,” said Perry Muse, plant manager. “At FPC, we use the production equipment for
research and development (R&D) of new products, the benefit being accurate analysis of line
capability and constraints. There are numerous components that work in conjunction with one
another. Consequently, adjustments to any component will oftentimes create a domino effect.
“From a quality perspective, it is an enormous undertaking to define the processing
parameters required to meet the customer’s product specifications. We find it recurrent that
finished product specifications need to be redefined, or tweaked, in order to satisfy downstream
processing or product testing. The learning curve is often precipitous, but far more beneficial
than the imprecise approach of transferring data from a lab environment to a production
environment.”
Home Run
“We feel like the industry has hit an
old-fashioned home run in this instance, with an American machinery manufacturer working with an
American specialty textiles supplier,” said Lucy Hooper, vice president, marketing, Tandematic.
Hooper’s first contact with FPC was during an FPC visit by Garner to the Tandematic showroom and
R&D facility in Spartanburg in early 2005. Garner had in mind one or two specific Tandematic
products he wanted to see in operation. He also carried back to Calhoun a sense of how many more of
FPC’s manufacturing problems Tandematic could solve.
“Our showroom is one of our most powerful selling tools,” Hooper said. “Tandematic equipment
is in demand wherever fabric is made. Most of our business is overseas, and while technology
unavailable 10 years ago — e-mailed digital photos, CAD [computer-aided design] and pdf drawings —
allow us to work with a customer halfway across the globe on an ‘almost-like-being-there’ basis,
the experience of doing business with a company down the road was pleasant and refreshing.
“Foam Products started out with several models of Tandematic decurlers, added a fabric
guiding machine, and then our tenter rail guidance system. Virtually all important Tandematic
products can now be found on the FPC floor except our selvage trim system, in which they have
expressed interest for the future,” Hooper added.
Keith McCollum, sales/service manager, Tandematic, was in charge of the showroom
demonstrations for Garner and Muse when they visited the plant, and also handled the installation
of Tandematic equipment at FPC. McCollum said he knew early on that FPC would be a good match with
Tandematic, and he quickly grew to appreciate the competence of their personnel during the
installations.
“Foam Products came to us for help in upgrading their line in order to be able to process
difficult types of fabric easily and efficiently, and we were all pleased with the results,” said
McCollum. “As a last step in the current project, we have equipped our fabric guiding machine with
sensors that will allow the system to automatically ‘see’ an unusual open-weave fabric. At this
point, everything FPC makes is handled successfully with Tandematic equipment.”
Going Forward
According to Garner, investing has
made a difference. “The improved equipment in combination with what our people have learned and the
strong position of our partners has us in a very capable position now,” he said. “We expect to grow
in our existing businesses, but we are also working on some innovative approaches that we expect
will keep us busy. We have worked to become a versatile narrow web coater, able to apply a variety
of foams or coatings to any type fabric or substrate.”
And the work and search for new opportunities continues.
October 2005
Quality Fabric Of The Month: Walls Of Earthtex™
screens and other commercial and residential interior products — has developed Earthtex™, its first polyvinyl chloride (PVC)-free woven wall covering and the next generation of its Hardwear™ collection of upholstery and wall covering fabrics. For Designtex and its parent company, Grand Rapids, Mich.-based office environments manufacturer Steelcase Inc., Earthtex represents one step
toward their goal to remove PVC from all products by 2012 — part of an overall, ongoing strategy to make their operations and products as environmentally sustainable as possible.According to Carol Derby, director of research and development, Designtex, the traditional Hardwear wall coverings are made using a PVC-coated polyester fill and a polyester warp. By comparison, Earthtex wall coverings are made using EarthTex™ solution-dyed 100-percent thermoplastic olefin (TPO) fill yarn, which has a polypropylene (PP) core and is coated with a blend of PP and polyethylene olefins, and an olefin warp. Because there is no contamination of one olefin by the other, Earthtex product manufacturing trimmings and waste can be recycled into new product. The end-product also has been designed to be recyclable once a reclamation program for such products is in place.
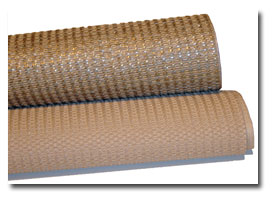
and an olefin warp, are designed to be recyclable once a reclamation program is in place to receive
them.
In addition to being PVC-free, the company notes, Earthtex also contains no heavy metals or plasticizers, is inert and therefore nontoxic in a landfill, and requires much lower temperatures for processing than PVC. With all these environmental advantages, the product offers durability comparable to that of the traditional
Hardwear wall coverings. In addition, because Earthtex is solution-dyed — the other Hardwear products are not — it offers improved cleanability, Derby said.
The standard Earthtex fabric has an acrylic backing that typically is knife-coated in a liquid state onto the fabric, which then is dried in an industrial dryer or oven. As an alternative, more environmentally sustainable solution, Derby said the company will apply a polylactide (PLA) backing when it is specified. She noted PLA is water-soluble, adding that the company plans to make PLA its standard backing as the cost comes down.
Designtex is marketing its Earthtex line especially for health care applications, but the products also are suitable for hospitality and corporate environments.
The first two Earthtex wall covering styles are being made available this fall, and other styles are planned using EarthTex in combination with other olefins.
“Interesting textures can be achieved by combining EarthTex with other olefin yarns,” Derby said, noting there also are opportunities going forward to use it in upholstery. “It’s a soft, supple yarn. A lot of work went into making it that way.”
For more information about E47, contact Bob Parker or Bill Douglas, ARC Outdoors (918)
258-8788; www.e47nano.com.
October 2005
From The Editor: Trust – Supply Chain’s Weakest Link
A
s all sectors of the textile industry search for new ways to compete, new markets to
enter and innovation to obtain a competitive edge, one parameter that rarely makes the paper is
trust. Today, companies rely on speed, quality and delivery in ever tighter time frames across the
supply chain. They share the growing need to work together in truly innovative product development.
Each must develop relationships that go beyond a contract and embrace real partnership as a
critical ingredient. Growing interdependence of companies isn’t new, but collaboration is the
buzzword for Western Hemisphere companies trying to establish a framework to counter increasing
Asian competition.
For a US business person, this is a
nice idea, but competition, the drive to win and no team structure in the linked businesses of the
supply chain make trust seem naive. The stakes have never been higher, and the chain can easily
break, damaging a customer relationship with one failed promise, missed delivery or misrepresented
capability.
At the recent American Apparel
Producers’ Network (AAPN) meeting in Savannah, Ga. — an event that gathered 75 companies from fiber
to apparel brands and finance to logistics — it was amazing to see so many different companies
searching for ways to establish new, trusting relationships. Old friends were apparent, but the new
demands of the apparel supply chain can test even those relationships. Innovation and collaboration
are a recipe for success for the Western Hemisphere in supplying apparel. Several AAPN members
expressed interest in forming a cooperative, a partnership of companies to remove excess capacity
from existing facilities and pool those resources to add capacity in Central America where there is
a perceived need. As you can imagine, an interesting dialogue ensued — but that is the point. Those
not willing to come together in the form of a cooperative are forced to develop a solution that can
perform at the level of a cooperative — finding partners with common ideals, identifying a need in
the market and developing a supply chain solution to solve it, gaining ground on foreign
competition by leveraging every aspect of the chain. Use finance, use logistics, leverage core
competencies and bring fresh product to the table — simple? No, but these steps are absolutely
necessary.
Some companies are doing this. They have developed and continue to develop new products and
processes. Some spinners have developed strong relationships with brands, and when they succeed,
members of the chain with which they have shared success in the past are in line to share new-found
success — they earn trust each time.
Jeff Streader, VF Imagewear, was clear at the AAPN meeting in his call for innovation,
saying: “Bring it to me. If I can use it, and you don’t have a chain, I’ll plug you into my chain —
but bring it to me.” Streader said he expects VF — now with roughly $6 billion in annual revenues —
to continue to source 50 percent in the Western Hemisphere — that is the opportunity and also the
challenge.
Building trusting partnerships that emphasize collaboration and innovation will establish a
clear competitive framework for the Western Hemisphere — trust may just be the weakest
link.
October 2005