I
n thermal nonwovens processes, most medium- and long-term costs are not caused by
machinery purchases, but by the thermal energy generated. The most important measures are initial
moisture reduction, exhaust-air flow optimization and heat utilization, and a highly efficient
dryer. The Eco-Heat heat-recovery and Eco-Air exhaust-air cleaning systems from Brückner
Trockentechnik GmbH & Co. KG, Germany, allow considerable cost cutting and are compatible with
all dryer makes.
Production line operating costs have a decisive influence on the total costs of articles
produced. Even nonwovens and technical textiles producers face ever more decreasing profits. One
reason is tough competition due to globalization. Another is that more and more producers want to
share in these segments by diversifying their existing portfolios. In parallel, operating costs
have increased rapidly in recent years, caused mainly by rising energy costs. If nonwovens
producers want to save these costs, they must consider measures resulting directly in lower
specific energy consumption and measures indirectly but positively affecting energy consumption.
Three Production Steps
The nonwovens process comprises mainly three steps: First, a web is formed from individual
fibers. This web, still sensitive to pressure and traction, eventually is treated using bonding
processes to get the required dimensional stability. In the last step, the nonwovens are finished
using different methods to give the requested end-product characteristics.
The complete process requires a corresponding amount of energy, mainly electrical or
thermal. Depending on the process step and the applied methods, the portion of required electric
and thermal power and the relevant energy carrier’s absolute consumption differ very much.
While nonwovens formation requires electric power almost exclusively, the portion of thermal
energy increases significantly for bonding and finishing. Particularly energy-demanding are all
bonding methods, such as spray bonding, hydroentanglement, full bath or foam impregnation. And
nonwovens finishing technologies such as coating, printing, dyeing and others require the
evaporation of water or solvent.
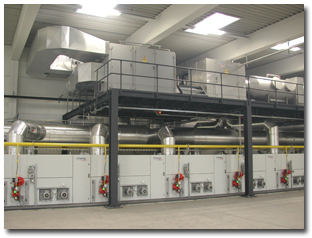
Brückner’s Eco-Heat heat-recovery and Eco-Air exhaust-air cleaning systems are shown
installed on a nonwovens finishing line.
Electrokinetic Energy
Apart from thermal energy, it also is possible to save electrokinetic energy. Electrical
energy needs are determined by motor size and efficiency, a drive system that is optimally designed
and fine-tuned for the complete line, and the consequent use of highly efficient gears and motors,
which offers a big savings potential.
Brückner has calculated possible annual savings in a five-digit-euro range for production
lines. In addition, the use of suitable raw materials and high-capacity materials and thus
achievable weight savings also contributes to cost savings.
Thermal Energy
In nonwovens production, thermal energy is required almost solely for bonding and finishing.
Heat transfer from machine components onto the nonwovens is made by heated roller contact, infrared
radiation or convection. However, there is a difference between direct and indirect heating: With
direct heating, the heat generated by the energy carrier comes directly in contact with the
substrate. Indirect systems generate the primary heat basically in the same way, but the thermal
energy is first transferred to a carrier medium and then by means of a heat exchanger onto the
nonwoven
(See Table 1).
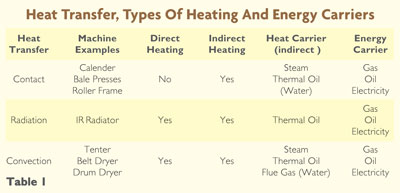
In this connection, two aspects are of particular importance regarding thermal energy cost.
Direct heating systems are approximately 92- to 96-percent efficient, while indirect systems
provide only 60 to 85 percent of the primary energy. Also, basic prices for the elementary energy
carriers’ power can differ considerably and thus directly affect the cost per generated kilowatt of
thermal energy.
Surprising Results
Some years ago, Brückner completed a study regarding life cycle costs, focusing on how a
machine’s operating and energy consumption costs are distributed over time for a convective heat
transfer process. The expenses for heating energy and power represent more than 50 percent of the
total costs
(See Table 2). However, most of the customers participating in the study overestimated
heavily the share of the machinery price, with an average estimate at 40 to 50 percent, whereas
energy costs were predicted only at 30 to 40 percent.
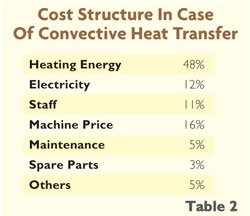
To reduce thermal energy costs in nonwovens bonding and finishing, it is a prerequisite to
know the parameters involved in the process and the corresponding energy inflow and outflow.
Thermal energy is required to heat the web to the desired temperature, evaporate moisture adhering
to the textile, and heat the exhaust air and/or the corresponding quantity of fresh air to remove
the evaporated water.
The evaporation of water and the heat removed with the exhaust air and the heating of fresh
air require most of the consumed thermal energy. The portions for fabric heating and heat losses
due to the transport system and machinery components are rather low in comparison. Heat losses in
modern convection machines are not more than 3 percent of the total heat required. Therefore,
machinery producers focus optimizing efforts mainly on cost drivers where possible savings are
higher. In practice, heat losses are often discussed, and it is correct to strive for improvements
here, too. However, as the use of high-capacity materials leads also to considerable cost increases
for the complete machine, the achievable benefit must be critically analyzed.
Energy Savings
The decisive saving potential is in the energy required for water evaporation, exhaust air
flow and fresh air heating. The first step is to provide for the best mechanical dewatering of the
web, as lower initial moisture leads to lower energy consumption.
The second step is to reduce exhaust-air volume. Drying requires air that is able to absorb
moisture. Lower exhaust-air flow means higher saturation of the circulating air with steam, but
absorptive capacity decreases with increasing humidity, and the dew point sets a physical limit.
The moisture in the dryer interior or in the exhaust-air ducts condenses when maximum saturation of
the circulating air is exceeded. Exhaust-air-flow reduction is always connected to dryer
performance and is thus a problem for optimization. According to Brückner, the optimization is
between 80 and 140 grams of moisture in the exhaust air per kilogram of exhaust air. A control
system allows setting this optimum for each drying process by automatically adapting exhaust-air
volume flow independent of exhaust-air moisture.
Control of exhaust-air volume flow and recovery of exhaust-air heat make up the third step.
It is possible to recover efficiently most of the heat discharged with the exhaust air by means of
heat-recovery systems. A possibility is to heat fresh air, which is then supplied to the convection
machine. In this context, there is a considerable difference in the heat-setting process: The use
of exhaust-air heat is also important because there is no measurand for the exhaust-air flow
control. Also, here, the exhaust-air flow should be as low as possible. However, condensation of
finishing vapors must be avoided. The only possibility for such processes is manually controlled
exhaustion.
Heat Recovery
Brückner provides two systems for exhaust-heat recovery: air-to-air; and air-to-water. Both
can be combined and varied and adapted to any convection machine or to customer specifications.
Also, when combined with an electrostatic precipitator, this efficient method of economic energy
utilization can be enlarged to be used as a high-capacity exhaust-air purification system. This
heat-recovery system can be used with a range of dryers, ovens and heat-treatment chambers.
Using an air-to-air system, process heat can be reduced by 12 to 15 percent; and using
heat-setting processes, by 33 to 36 percent. Another possibility is to use the hot fresh air to
air-condition the factory. With an air-to-water system, water can be heated to 90°C. These are
excellent savings possibilities regarding the overall energy balance of a plant for nonwovens
producers that use hot water for their wet-finishing.
Editor’s Note: Stefan Müller is sales director, Nonwovens, at Brückner Trockentechnik GmbH
& Co. KG.
May/June 2010