Yarn ConditioningBy Eric Vonwiller, Senior Technical Editor Steamy Conditions
U.S. yarn manufacturers share their practical experiences with Xorella yarn-conditioning
equipment.
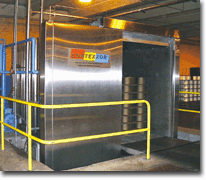
This LTC-S compact unit installed at Four Leaf Textiles, Spindale, N.C. is the
latest-generation Xorella Contexxor yarn-conditioning system. Yarn conditioning is one of
those subjects like flu shots or dental visits that do not elicit a great deal of excitement in
general conversation. Perhaps much of the reason has to do with the fact that a number of textile
people are dubious about the benefits of some systems they say the machines just dont work as
advertised.There is no doubt, however, that the proper yarn-conditioning technology properly
applied can make a big difference in the processability of yarns in weaving and knitting
operations. Such processes as vacuum steam or cold steam yarn conditioning can have significant
benefits for knitters and weavers.The first vacuum steam machines were installed in U.S. mills
about seven or eight years ago and have since become indispensible components of the manufacturing
process. But it was an uphill battle, not only to get textile manufacturers to consider the
technology, but also to get the machinery manufacturers to develop it.Freddy Wanger, founder and
managing director of Xorella AG, discovered this reluctance the hard way. His idea for a vacuum
steam yarn-conditioning process ran against the grain with a former employer. Rather than battle an
established corporate structure, Wanger decided to set up his own business. He founded Xorella AG
in 1971 in Wettingen, Switzerland.The textile mills around the world have finally realized what
great production improvements this system can provide, Wanger told Textile Industries at a
recent textile exhibition, but it took us 20 years to convince them!His painful and patient
persistence, though, has paid off handsomely. Today, the Xorella system is considered to be among
the most effective and consistent yarn-conditioning systems on the market. Years In The Race
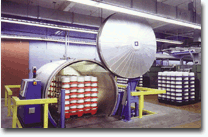
To get a good handle on the evolution of Xorella yarn-conditioning equipment, TI visited
two yarn manufacturers that have the system in place. R.L. Stowe, Belmont, N.C., has the first
generation of the Xorella machinery running at several plants, while Four Leaf Textiles, Shelby,
N.C., operates the latest incarnation of the equipment.The first Xorella Contexxor® LT-O machines
were sold to R.L. Stowes National and Helms plants in the early 1990s and are still in operation.
Age has added some appearance wear, but the machines still function without problems and fulfill
their tasks to full satisfaction everyday. Verner E. Stanley, Jr., executive vice president and
COO, said Xorellas yarn-conditioning process enhances the runability and presentation of the yarn
to weavers and knitters.When asked why Stowe selected Xorella, Stanley explained: Conditioning
cotton yarn in a vacuum at a relatively low temperature has all the attributes of success. This is
achieved by full penetration of the packages and at a condition that does not change the dye index.
Mechanically, the machine is extremely reliable, has excellent electronic controls and is built
with substantial structure.Both Stowe plant managers were positive about the impact of the
Contexxor LT-O machines, which have run continuously with few problems. Stowe conditions all of its
cotton yarns, specifically, plied and twisted yarns, for knitting and weaving customers. Only a few
of the companys hosiery customers request unconditioned yarns.The latest technology from Xorella,
the Contexxor LTC-S, is installed at the Four Leaf Textiles plant in Spindale, N.C. The
space-saving cubical unit was presented for the first time at ITMA 99 in Paris. Xorella received
TIs Innovation Award in 1999 for this technological development.Terry Lee, vice president,
operations, said, Xorella maximizes the yarn conditioning with this machine. Because Four Leaf also
has earlier designs of the Xorella machines in its plants, Lee is able to make a direct comparison
between the older machinery and the LTC-S unit. He pointed out that energy, time and water savings
are significant, especially when compared with conventional machinery on the market. He also
praised the consistency of conditioning the new unit produces. He and his staff consider the effort
for maintenance quite reasonable, as it is basically limited to cleaning door seals and draining
the water every two weeks.At the Spindale plant, Four Leaf produces mainly plied and twisted
man-made yarns from polypropylene/olefin fibers blended with acrylic and some rayon. The majority
of these yarns are conditioned to reduce loops and kinks, set the twist, and enhance knitability
and weaveability. Some single yarns are waxed and conditioned, depending on specific customer
request.Like the executives and managers from Stowe, those from Four Leaf were positive about the
impact of Xorellas Contexxor system. Lee said customer feedback has been very positive. Once
customers have seen the benefits of yarn conditioning, they dont want to be without it.
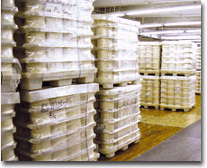
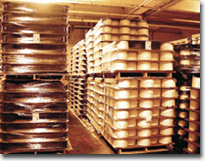
Both R.L. Stowe (left) and Four Leaf Textiles (right) shrink-wrap their yarns immediately after
the conditioning process, retaining moisture and helping fight fiber fly typical of cotton
yarns. Technology With SuccessThe Contexxor vacuum yarn-steaming and conditioning system is
the primary product line of Xorella, which is represented in the United States by PSP Marketing
Inc., Charlotte, N.C. The vacuum and pressure vessels are built according to strictest safety
specifications and are manufactured to conform to each countrys regulations. A process of steam and
vacuum prevents loops in the yarn, sets the twist, humidifies and improves the efficiency of the
machines in the subsequent processes (spooling, winding, knitting, weaving, etc.).Additionally, it
improves yarn strength and elongation of cotton yarns. During a process that takes from 35 to 45
minutes, the initial and intermediate vacuum stages ensure accelerated penetration of the saturated
steam and 100-percent humidity without condensation from a temperature as low as 50ºC (122°F). At
the same time, air and atmospheric oxygen are removed. This saturated steam also penetrates paper
tubes and cardboard boxes without destroying them. A newly developed ECO-System achieves low energy
cost.Xorella offers the more conventionally based Contexxor LT-O with the ECO-System and the
patented overhead door. Its latest technology is the Contexxor Compact LTC-S unit that is designed
to treat especially high pallets up to 13 layers. The new cubical design offers even greater energy
savings, easier maintenance, a water bath cover against fiber fly, shorter processing times, and
full automation. One and two-door versions are available. According to Xorella, the system can be
offered with significant price advantages when compared with other conventional systems on the
market.Many companies in Italy and China use the Xorella equipment for treating silk yarns. Plants
in Europe, South America, Mexico, the United States, Pakistan and Taiwan use it for cotton. Mills
in Australia, England, Germany, Korea and Switzerland use it for wool. The Xorella system is used
for man-made spun and filament yarns in the United States, Russia and the Far East.
November 2001