Speed Weaving
Multiple weft insertion, advanced drives propel weaving machines to new heights of productivity
and efficiency. It wasnt so long ago that uniformly green, clacking, creaking,
fly-shuttle looms lined the weave rooms of American textile mills in seemingly endless columns,
pounding out yard upon yard of fabric in a laborious, raucous process that substituted sheer volume
for efficiency. The United States can credit these looms, along with the furnaces of Pittsburgh and
the assembly lines of Detroit, for its ascendancy to the pinnacle of world economic power.Those
were days of high adventure in American textiles. Every now and again, a shuttle deviated from its
assigned mission of weft insertion, escaped the shed and was launched on an uncontrolled flight
across the weave room, providing perhaps the first definition of projectile weaving. Those also
were the days when Americas staple product was borne from the take-up rolls on the backs of
broad-shouldered cloth doffers, and loom fixers resembled automotive mechanics more than computer
technicians. Quiet, relatively vibration-free machines, automated processes, and speeds in excess
of 1,000 picks per minute might well have been the subjects of science fiction novels.Then, some
bright engineer decided to take a look at the method of weft insertion and well, suffice it to say
that things changed. A weaver transported from a 1960s greige mill wouldnt recognize the smooth,
svelte machines at modern plants today. But, more to the point, a weaver from an early 1990s
environment might find himself equally as lost in the weave room of 2001.A number of companies have
new offerings in weaving machines, and most claim their products herald the dawn of a new era in
fabric production. Somets Mythos was reviewed in these pages several months ago (See Vision,
Innovation Are Keys To Viability, ATI, August 2000), and the products of other manufacturers will
be the subjects of future articles. In this issue, ATI provides a look at new concepts from two
leading manufacturers in Europe.The process of weft insertion provided the first major stumbling
block to increases in weaving speed. The fly-shuttle looms of the previous era could run only so
fast with any semblance of control over the process. Then came the first projectile looms, rapiers
and air-jets.Multi-Phase Weaving With Sulzer’s M8300Sulzer Textil, Switzerland, has taken the
concept of high-speed weft insertion a step further with the introduction of its multi-phase
weaving machine, the M8300.Single-phase weaving, traditional projectiles, rapiers and air-jets have
pushed the envelope, both in textile and technical limits, in what we can do, explained Louie
Dejonckheere, vice president, marketing, for Sulzer Textile Inc., the Spartanburg, S.C., unit of
Sulzer Textil. Improvements in insertion rates are limited by textile and technological factors,
particularly when processing spun staple yarns, he said. These limits are caused, in part, by
incompatible stressing of the threads and by uncontrollable physical conditions. When Sulzer began
looking at new technologies to improve efficiency and performance, we began exploring the
possibilities of multiple weft insertions.The concept of multiple insertions is not new. Research
dates back more than four decades to 1955, but finding a practical method of bringing concept to
reality proved a daunting task. Multiple shed formation can be accomplished with two basic
techniques, wave-shed and multi-linear. In wave-shed, the sheds are formed in the direction of the
weft, while multi-linear insertions require the sheds to be formed in the direction of the warp.
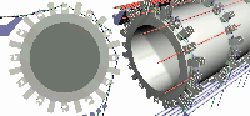
Initial concentration was on the wave-shed technique. At ITMA 75, four manufacturers
including Ruti (which had not yet been integrated into the Sulzer group), presented developments in
wave-shed techniques. By ITMA 83, three manufacturers were still demonstrating this technique, but
technological obstacles prevented the concept from achieving market success.On the basis of
experience drawn from our long-standing research, the wave-shed development failed because of
several inherent shortcomings, Dejonckheere said. Among those were: the impossibility of repairing
mispicks; differing weft-thread tensions as a consequence of several weft-yarn carriers being
activated at the same time; the requirement of an additional rewinding process caused by the
special make-up of the weft carriers; restriction to output-limited mechanical weft carriers; and
the failure to achieve the required beat-up necessary to obtain uniform insertion across the entire
weaving length.As a logical conclusion, arrived at with the experience we collected, Sulzer began
considering the multi-linear shed strategy for implementing multi-phase weaving, Dejonckheere said.
The M8300 is the result.The M8300, designed exclusively to be a single-warp machine, is earmarked
for mass-production commodity fabrics. Technological design at this point does not yet allow for
multiple-color, patterned insertions. The machine is installed in production capacity in several
locations throughout the world, including the United States. The M8300 has four sheds open at all
times, resulting in a machine that is technically capable of running from three to four times as
fast as a typical air-jet machine, Dejonckheere said. Weft insertion rates of up to 6,000 meters
per minute are possible, as Sulzer demonstrated at ITMA 99 in Paris. This concept truly extends the
boundaries of fabric production, he said.The M8300 has a complete modular design for ease of
installation, operation and maintenance, according to Dejonckheere. The machine is divided into a
weaving module, warp module, shedding module, cloth-winding module and yarn-feeding module. This
arrangement guarantees warp and cloth run-off optimized for ergonomics and facilitates a quick warp
change. The machine accommodates warp beams of up to 1,600 millimeters, which allows processing of
large batch lengths.Shed Formation And Weft InsertionThe multi-linear shed formation opens four
sheds across the entire weaving length. The parallel sheds are opened in the warp direction, one
behind the other. One thread is inserted into each shed to allow the simultaneous weaving of four
picks. Unlike the wave-shed method, every missed pick can be detected and repaired, Dejonckheere
said.The individual sheds are form-fit across the circumference of a weaving rotor, anchored by
shed-holding elements arranged in a line. Spreading the warp threads on the shed-holding elements
is achieved with the aid of warp positioners similar to the needle bars of knitting machines. The
quantity of required warp positioners depends upon warp density.
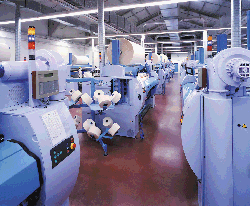
Weft insertion is accomplished with a low-pressure blast of air through a weft channel formed
by the shed-holding elements. Additional relay nozzles are placed within the shed-holding elements.
The weft threads are continuously unwound through metering rollers from four stationary packages.
Constant thread velocity can be controlled according to weaving width, insertion rate and the speed
of the metering rollers. Thread velocity amounts to only 20 meters per second at an insertion rate
of 5,000 meters per minute. Weft threads are fed to a weft-processing unit, which controls
distribution. The weft-processing unit consists of two concentrically arranged disks in a
multi-channel system. The threads leave these guiding channels in a synchronized sequence and enter
the appropriate weft channel. Between the weft-processing unit and the weft channels are a thread
clamp and the main cutter. The four weft yarns are then transported very gently through their
respective sheds in a staggered sequence by a compressed air stream of only 25-30 psi.On the
receiving side, arrival of the weft thread is electronically detected, and combs positioned on the
circumference of the weaving rotor accomplish weft beat-up. These combs are located between two
rows of shed-holding elements and replace the function of conventional weaving reeds.Single-Motor
ControlThe M8300s individual motor control allows optimum support of the modular weaving system,
according to Dejonckheere. All motions are freely programmable to ensure adaptation to weaving
requirements. The actuating concept of the M8300 features an electronic guiding shaft with no
moving parts. The guiding shaft position is transmitted to all drives via a tact bus. Each drive
has an electronically controlled coupling and gearbox with programmable transmission ratios and can
be operated either synchronously or asynchronously in any direction of rotation. This allows for
absolute freedom in the spatial arrangement of drive shafts, he said, and provides for the
programmability of all motions via software. Ultimately, one has the possibility of optimizing
operability and weaving automation without either conversions or additional hardware.Because of the
low velocity of weft insertion, weft-thread stress is considerably lower than in single-phase
air-jet machines, even though ultimate insertion rate is substantially higher. Despite
two-and-a-half times higher production rates, this weft-insertion system reduces the maximum weft
velocity by approximately 75 percent, compared to single-phase air-jet weaving machines, he said.In
addition to much higher insertion rates, Dejonckheere said the M8300 reduces noise levels by up to
50 percent over conventional air-jet machines and consumes less power. Self-contained
air-conditioning reduces heat build-up, waste and airborne particulate matter.The M8300 multi-phase
weaving machine is a milestone in technology, he said. For standard fabrics, we believe it is the
most economical weaving system currently available. Picanol Focuses On Production
FlexibilityWhile Sulzer has been focusing on multi-phase weaving for large runs of commodity
fabrics, Belgium-based Picanol NV continues to optimize its line of air-jet machines for smaller
production runs.Just under a decade ago, Picanol introduced its revolutionary Omni air-jet weaving
machine based on the fast-response philosophy, said James C. Thomas, president, Picanol of America
Inc., Greenville, S.C., the U.S. subsidiary of Picanol NV. Weve been working to enhance economical
production of relatively small batches at high speed, with the capability to make frequent style or
warp changes. We consider this to be the textile industrys answer to lean, flexible
manufacturing.Earlier this year, Picanol expanded upon this concept with the launch of the OMNIplus
machine (see New Products, ATI, September 2000).
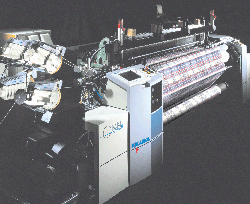
The two starting points for development of the OMNIplus were the fabrics to be produced and
the weavers job, Thomas said. On one hand, the machine had to be able to produce high-quality
fabrics in a very wide application range and at competitive prices. On the other hand, it had to
enable the weaver to meet varying market demands in a flexible, user-friendly way. These, then, are
the key features of the OMNIplus: higher quality at lower cost coupled with production flexibility
and user-friendliness.The OMNIplus weaves spun, filament and a wide range of fancy yarns
high-twist, stretch, chenille and textured yarns in up to six colors and yarn types. For the weave
pattern, there is a choice of positive cam, positive dobby or jacquard motion. Available reed
widths include 190, 220, 250, 280, 340, 380, and 400 centimeters. The OMNIplus can produce cloth
rolls of up to 720 millimeters or 1,500 millimeters with the Picanol Batching Motion. Sumo
Drive MotorPerhaps the biggest innovation associated with the introduction of the OMNIplus is
Picanols Sumo drive motor, which is based on switched reluctance technology. Sumo derives its name
not from the famed Japanese wrestlers although Picanol uses the image in its marketing efforts but
from the first two letters in the words super and motor.The Sumo motor drives the weaving machine
directly, Thomas said, without the clutch-and-brake units. This is an enormous contribution to
reliability, he said. Moreover, the extremely fast response time its on the order of milliseconds
makes it possible to automatically vary the speed of the motor during the weaving cycle to suit
each and every pick. The variable speed of the Sumo is set electronically. The Flexispeed version
of the motor, which is standard on the OMNIplus, enables the speed variation to be set in
distinctive steps when the machine is stopped. The optional Multispeed version permits continuous
speed adjustment during weaving. A third option, the Optispeed version, allows automatic variation
according to color and weave pattern.
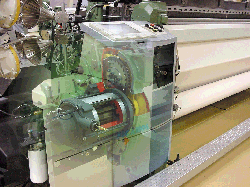
The principle of the switched reluctance motor, according to Picanol, dates back more than a
century to the early days of electromagnetic technology. The rotor is merely a lump of iron, with
no permanent magnets or windings. The stator consists of slots containing a series of coil
windings, which are energized by electronic switching to generate a moving magnetic field.While the
basic concept is extremely simple, Thomas said, the switching necessary to obtain top performance
at an acceptable price has been, previous to this development, too complex.In addition to the Sumo
motor, the OMNIplus features a flexible insertion system that enables the speed to be
electronically controlled to suit the filling material and the weave pattern, he said. With
Picanols Quick Style Change system, a style change can be carried out in less than 30
minutes.Yarn-friendly insertion is achieved with separate controls of both the fixed and movable
main nozzle, the low-friction presentation of the yarn, the filling tensioner and the motion of the
sley, Thomas said.Energy consumption is estimated to be 15 to 20 percent less than comparable
machines, and air consumption is lower because of a reduced pressure drop in the air distribution
system. Productivity Enhanced By Technological InnovationsThese offerings, in combination
with advanced weaving machines and systems from other manufacturers that will be explored in
upcoming issues of ATI, are poised to have significant impact on the productivity of American
textile plants, as well as those throughout the rest of the world. What has been a steady evolution
in single-phase technology is becoming, with the advent of multi-phase insertion, a revolution,
according to Sulzers Dejonckheere.We began working on multi-phase technology many years ago, he
said. And we are constantly looking at pushing the edge of the envelope of applications as far as
it will go.Its all about meeting the customers needs, says Picanols Thomas. Its about close
collaboration, advanced production methods and extensive test programs. These are the factors that
have led to the advanced Picanol machines of today and will lead to even more advancements
tomorrow.
November 2000