Burlington Industries Williamsburg Plant, Caswell County, N.C., part of the Burlington House
Division, recently renovated its fabric inspection room by installing 15 custom-designed machines
built by McCOYandDUKE Inc., Greenville, S.C.The Williamsburg Plant was built in 1966 and was
originally setup to weave drapery fabrics. It now produces mattress ticking, both fancy Jacquard
and dobby upholstery; drapery styling and bedding.Over the years, Burlington has updated the
equipment at the Williamsburg plant. In this latest modernization, the decision was made to improve
the material handling portion of production. In order to improve cost and safety conditions, the
company decided to renovate the approximately 11,000-square-foot area that housed its fabric
inspection room.We wanted to get our inspection department onto the same level of world-class
manufacturing as our weaving operation, said Joe Hatzopoulos, plant manager of the Williamsburg
Plant.Burlingtons approach was to involve both management and associates in selecting and
developing the system for automating the plants cloth room.This project is an excellent example of
how textile companies and vendors can work together to streamline production and improve workplace
conditions.
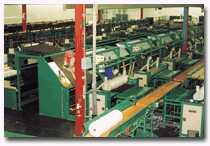
Burlington’s recent cloth room renovation has drastically reduced the manual handling of its
fabric. The Williamsburg Plant, which employs approximately 600 people, produces 1 million
yards of fabric per week. The company wanted to improve its time in/time out and the overall
quality of its fabric. It determined the best way this could be done was by reducing the handling
of the fabric.We wanted to get away from the manual handling of our fabrics to eliminate several
processes. One in particular was batching and shearing. We wanted to reduce not just the manual
handling but reduce the overall handling of all our fabrics, said Hatzopoulos.Burlington has always
been a corporation willing to seek out state-of-the-art equipment, and this plant has been one of
the flag ships of the division as far as capital investments. Beginning The ChangeAfter
looking at several solutions and companies, Burlington chose to work with McCOY/HOUSTON (as the
company was called at the time) because of the companys ability to create custom-built inspection
equipment that fit Burlingtons needs.From the beginning, the two companies worked in tandem to
redesign the cloth room. Burlington wanted as many of its cloth room associates to be involved in
the design and layout of the area as possible. Burlington believed that its employees some of whom
had been with the company since the plant opened could provide valuable insight.I have been in the
textile sales business for probably 25 years and this is one of the first times that I have seen
this many people be involved in the decision, said Ron McCoy, McCOYandDUKE.Some members of the
production team were sent to McCOYandDUKE to get an in-person look at the design process.We sent a
second shift supervisor and two or three other employees to Greenville to find out more information
about the equipment, to serve as our experts, said Hatzopoulos. Benefits Of Installation
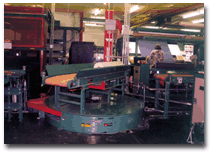
As expected, the new machines have dramatically reduced downtime while also reducing cost.
The new system allows for a flow of fabric rolls from the weave room to the inspection area. The
rolls are moved via conveyors from the weave room to the inspection floor. As the rolls come down
the conveyor they are directed to the next available inspection station. These dump stations are
fully automated.When the fabrics come from the weave room they are not even touched by an employee
in the inspection department until they are actually in the cradle of the inspection frame,
Hatzopoulos said. At that part of the frame, the inspector has to thread up the fabric.This new
system of delivering the fabric rolls eliminates a 25-year-old process known as the Eagle system.
The Eagle system used a claw-like mechanism to carry rolls of fabric to the sort location. Because
the system moved overhead, and had problems with misplaced sorting and mis-drops caused by
mechanical failure, it was the number one safety concern in the facility. The new system not only
eliminates the safety problems, but it also eliminates delays that occur from inaccurate fabric
roll placement.The biggest improvement occurred at the inspection stations. A full roll of fabric
can move down to the station from the conveyor system to await inspection. When the in-use roll is
out of fabric, the empty core automatically disengages from the work station and is sent to the
return conveyor system located directly below the main conveyor system. The cores are then returned
for use on the production floor.No longer is he or she having to lift a center mandrel, pull it
out, push the roll of cloth on the conveyor system, put a whole new tube on the air mandrel, put it
back, insert it, position it, Hatzopoulos said.Now it is just a simple procedure of laying a
three-inch paper tube onto two rollers to start-up.Eliminating the manual removal of these cores
not only reduces downtime, but also improves safety. The empty cores are heavy, some weighing up to
50 pounds. In the past, the inspectors, a large percentage of which are women, had to manually
remove and disengage the empty cores. The new system reduced the handling of these cores, allowing
for vastly improved workplace ergonomics.What we wanted to get away from was a lot of the lifting,
a lot of the pushing and pulling and handling of our fabrics,said Hatzopoulos. The number one
reason is for the safety of our employees, and number two is the reduced amount of handling of our
fabrics is going to ensure a more quality product.The core return system eliminated the need for
having associates walk around the area collecting, setting up and taking off cores. Avoiding
DelaysThroughout the entire renovation process, the Williamsburg Plant maintained full production
by using a satellite inspection area for several months. While this required an increase in manual
labor, there were no accidents during the transition stage, a point Burlington proudly points
out.For as big as this cloth room was, and for the work that had to be done, and what was brought
in it probably could not have been any better than the way it was handled, said McCoy. They lost
very little downtime compared to what it could have been. Steps To The FutureThese
improvements have allowed Burlington to continue to compete in this ever changing and high
competitive market. In todays market, there are more and more shorter runs and more and more style
changes, said Hatzopoulos. Our division is very fashion- and speed-oriented, and they are two of
the major factors within Burlington House. McCoyandDukeMcCOYandDUKE Inc., Greenville, S.C., began
operation in 1995 as McCOYandHOUSTON. The companys principals, Ronald J. McCoy and Charles E. Duke
along with project engineer John Malone together have 75 years combined experience in the textile
industry. The company can produce custom-built machinery for many areas of the textile industry.
These included greige mills, dye and print ranges, nonwovens, process lines to carpet, paper,
plastic and fiberglass machinery and material handling requirements.
November 1999