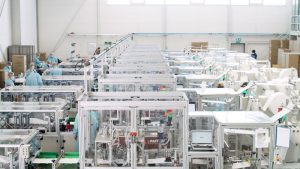
Autefa and Emerson contribute technology to respirator production line installed by Univent Medical.
By Didier Perret
The COVID-19 pandemic hit simultaneously around the world in early 2020, putting tremendous pressure on governments, industries, healthcare organizations and others to find ways to protect the public.
On April 9, 2020, Germany’s federal government established a task force, under the direction of the Federal Ministry for Economic Affairs and Energy (BMWi), to coordinate expanded production of personal protective equipment, tests and testing equipment, and active ingredients for COVID-19 testing in Germany and the European Union (E.U.). In short order, the BMWi task force developed an estimate that Germany would need annual production of 750 million FFP2 and FFP3 filtering respirators and 1,750 million medical face masks to meet the added level of demand.
Soon thereafter, the German federal government sought to contract with mask and respirator manufacturers to meet its ambitious goals. Univent Medical of Schwenningen, Germany, a maker of high-quality respiratory masks, received a contract that required it to dramatically increase production of its Atemious Pro FFP2 respirator.
At the time of the government’s huge request, Univent looked for new automated manufacturing lines to produce 1 million FFP2 respirators per week. Autefa Solutions Switzerland AG, Frauenfeld, Switzerland, a global machine builder, took an existing production machine concept and transformed it to comply with European safety regulations. This concept initially used ultrasonic welders, sourced in Asia, that were of entry-level quality. While these welders could support ordinary production rates in the mask-making machines, they lacked the features required to deliver and sustain superior quality at maximum rates of production. Of particular concern was their consistency and repeatability in bonding the four-layer mask laminate with the required strength at increased production speeds (see sidebar).
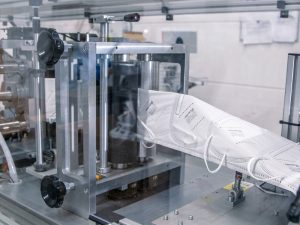
Autefa contacted Emerson, the maker of Branson™ ultrasonic plastic welding equipment, to recommend welders that could deliver the power, quality and speed that Univent required. Emerson recommended retrofitting the four ultrasonic welding stations with high-performance Branson DCX Series ultrasonic power supplies and newly optimized ultrasonic production tooling. Weld tooling included new converters, boosters and weld sonotrodes specialized to each welding task. The tooling was fabricated and maintained by the local Emerson representative Pascal Baechtiger in Switzerland.
Accepting Autefa’s advice, Univent approved the equipment retrofits. Emerson filled the order — for 32 ultrasonic welding power supplies and the needed tooling — in less than six weeks. Upon delivery of the welders, Emerson representatives offered on-site technical support as Autefa personnel completed the welder retrofits. “The experience and responsiveness of Emerson’s Branson ultrasonic welding team enabled Autefa to start the equipment rebuilding program quickly, without a long learning curve,” said André Imhof, Autefa’s CEO Autefa Solutions Switzerland AG.
When the revamped mask-making machines resumed production, Univent felt the impact right away. Thomas Vosseler, director and co-owner of Univent, stated, “Due to the reliability and performance of the new Branson power supplies and weld tooling, each of our eight production machines have increased their speed and output with high reliability, enabling us to increase production to 4.5 million Atemious Pro FFP 2 respirators each month.”
When it comes to improved production speed and quality, every detail counts. For example, two of the four ultrasonic welding stations on each mask-making machine are dedicated to attaching the elastic earloops, which are essential to ensuring a comfortable, airtight fit. The new Branson technology affixes the left and right earloops simultaneously and in less than a quarter of a second. And, using the “energy mode” of the Branson DCX welding power supply, the welds are made perfectly reliable — a substantial increase in both quality and speed over any entry-level welding system.
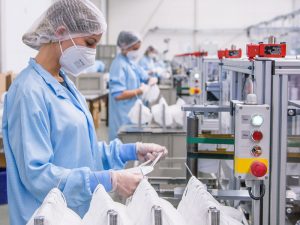
Completed Atemious Pro FFP2 respirators are removed from the production line, inspected and readied for packaging. Photograph courtesy of Univent.
Vosseler estimated that using high-end Branson welding equipment “enabled 95-percent efficiency of the existing automated lines, compared to less than 60-percent production efficiency generally observed with the entry-level ultrasonic welding equipment.” He defined production line efficiency as the ratio between how long the machine is producing good parts at full speed, compared to the time the machine slows down or stops due to technical issues, alarms or maintenance.
Based on the improved production and quality figures for the revamped production lines, Univent asked Autefa to build and deliver an additional 20 mask-production machines in 2021. Upon installation and startup of the last of these new machines, Univent estimates that it will be producing 3.5 to 4 million Atemious Pro FFP2 respirators per week, making it one of Europe’s largest FFP2 respirator producers.
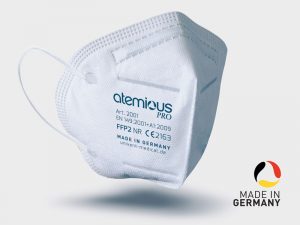
The Atemious Pro FFP2 Respirator
The Atemious Pro filtering respirator is built to exceed Conformité Européenne (CE) FFP2 testing standards and has been demonstrated in testing to capture more than 98% of the tiny solid and liquid particles that can spread COVID-19. Like the N95 respirator to which its performance may be compared (N95 is a respirator standard for the U.S. National Institute for Occupational Safety and Health [NIOSH]), Univent’s Atemious Pro respirator forms an airtight seal with the wearer’s face, so its design must not only balance excellent particle filtration with wearer comfort but also minimize any added exhalation resistance that can cause wearer fatigue over hours of use.
While many surgical masks and filtering respirators utilize a laminate of three layers of nonwoven fabric, the Atemious Pro respirator utilizes four layers, which are bonded together using ultrasonic welding. Closest to the skin is a layer of moisture-absorbing derma fleece. Then inside this are two special layers that perform the fine-particle filtration. They are made of an extremely tight web of meltblown polyethylene fibers. This is topped by a protective outer covering of polyethylene fleece providing the structural strength. To ensure a tight, yet comfortable fit, the laminated fabrics in the respirator incorporate an adjustable nose bridge and upper/lower attachment points for a soft, stretchable ear band and are also available with head loops.
Editor’s Note: Didier Perret is Medical Business Development manager, Branson Welding and Assembly at Emerson
March/April 2021