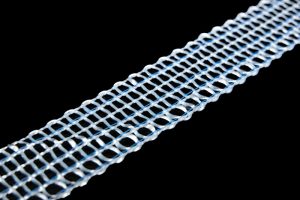
Offerings include advanced woven webbings used in parachutes, safety harnesses, and protective equipment.
TW Special Report
Bally Ribbon Mills — a company specializing in the design, development, and manufacture of highly specialized engineered woven fabrics — announced its newest line of advanced textile products to increase part functionality and utility. As companies demand higher durability and product differentiation, BRM has innovated with its E-WEBBINGS® and TPCM™ thermoplastic materials. Both products offer superior features, including lighter weight, specific strength, durability, stability, abrasion resistance, and sustainability, according to the company.
BRM’s advanced textile products are ideal for electronic transmission data, energy storage, and manufacturing automation. Working with companies that include NASA, Tier 1 Defense suppliers, as well as directly with the Department of Defense (Army, Air Force), BRM has developed advanced textiles used in parachutes, safety harnesses, personal protective equipment, and chemically resistant webbing. BRM is in accordance with safety standards, specifications and certifications, including ISO9001, AS9100, ISO13485, ISO14000, NFPA, ASTM, ANSI, *UL, and CSA.
E-WEBBINGS are conductive narrow fabrics, enabling the electronic transmission of data sensations — including light, noise, vibrations and heat — and power that can be stored or used to actuate/transform objects. Unique conductive fibers can be woven in conjunction with other fibers and can be used in embedded sensors in both wearable and integral technology, including the Internet of Things.
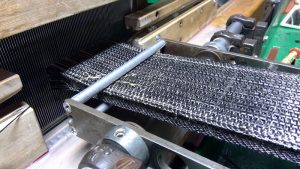
TPCM thermoplastic composite materials are 2D or 3D-woven, thermoplastic structures for incorporation into composite parts produced within varied, continually-evolving molding processes. The woven structural shapes are used in hybrid composite structures used in numerous industries, including aerospace/aviation, automotive/transportation, defense, architecture/infrastructure, marine and sports/recreation.
BRM customizes weave designs to modify performance properties, offering expert capabilities for custom options and configurations to optimize designs. BRM’s laboratories consider application details, width, tensile strength, elongation, color, quantity, and other special requirement with customized advanced textile products.
November 2020