By Lukas Lechthaler, Christoph Peiner, Marie-Isabel Popzyk, Thomas Gries
In Germany, approximately 10 percent of the workforce is exposed to high temperatures in the workplace — including workers in metal, glass, ceramics and steel production, as well as forges, foundries, fire brigades [TÜV16]. At these workplaces, employees are subjected to extreme heat stress because of working and environmental conditions. In addition to heavy physical exertion, an increased ambient temperature can lead to an increase in body temperature from a normal 37°C ± 0.5°C/98.5°F ± 1°F to life-threatening heat shocks above 40°C/104°F. This danger can be countered with the use of suitable protective clothing. [Ate15; KSC+07; NN15]
In conventional protective clothing, protection mainly is provided by the outer layers of the clothing. In contrast, a current research project named “Development of heat-exposed textiles for occupational safety” known as HEATex, focuses on the deeper layers of clothing. Usually, conventional cotton underwear is used here to absorb moisture, while the outer layers protect against heat radiation and burns. The cotton lies directly on the skin and can absorb and store large amounts of moisture from the body because of its good absorption behaviour. The stored moisture can be warmed up by external heating, which is not absorbed by the outer layer of the protective clothing. This can lead to scalding and overheating due to the body’s own perspiration. Pressure-loaded areas, in particular, are critical, as they impede air circulation and thus a possible cooling effect. If the clothing layers are compressed due to the pressure load, the skin comes into direct contact with the underwear so that moisture is prevented from being transported away and scalding occurs more frequently.
Functionalized 3D Textile With Load-Suitable Reinforcement Structures
The proportion of all accidents at work caused by overheating and scalding is about 50 percent for heat-exposed workplaces in Germany. The aim is to reduce this proportion to 10 percent by using a new type of functionalized 3D underwear. The solution to this problem is to apply underwear specially designed and developed for high temperatures. A locally reinforced 3D spacer fabric is used. On the one hand, scalding is prevented by avoiding direct skin contact and on the other hand, moisture is removed to protect against overheating. Pressure-loaded areas in particular are locally reinforced in order to reliably prevent contact between the skin and the layer of protective clothing above it.
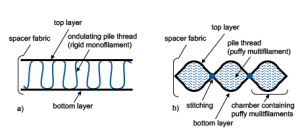
The layers of 3D spacer fabric are designed, manufactured and validated. Spacer fabrics generally consist of two parallel fabric layers which are kept at a distance by a third layer of thread. The distance is caused by a so called pile thread. Pile threads are usually rigid monofilaments, that ondule between the two parallel layers of the spacer fabric to maintain the distance. As an alternative, puffy multifilaments can be used, which cause the distance between the two parallel layers by puffing. The multifilaments are fixated by chambers that are stitched through the whole spacer fabric. Figure 1 shows the cross section of a spacer fabric using rigid monofilaments (a) as a pile thread as well as puffy multifilaments (b).
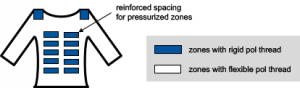
The inclusion of air between the top and the bottom layer of the spacer fabric creates an insulating layer. In order to counteract scalding, this insulating layer must be maintained throughout the entire service life. In highly stressed areas such as knees, elbows, shoulders or the back, local reinforcements must therefore be used (See Figure 2). The reinforcement is achieved by using either stiffer monofilament as a pile yarn or a puffier multifilament to keep the distance. According to the current state of research, there is no possibility of changing the stiffness of the pile yarn during the ongoing process.
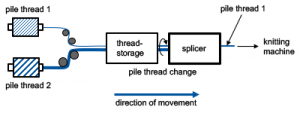
For this purpose, a splicer was developed within the scope of this project. Using the splicer, different yarns can be connected online and during the knitting process in order to change the pile yarn material. Splicing is a permanent and non-detachable connection of two yarn ends and is mainly used to repair a yarn breakage. Depending on the splicing concept, different yarns can also be connected to each other, for example to change the functionality of a textile. Various basic principles can be used for this purpose. The pile yarn is changed in the running process via the splicing system and thus the distance stiffness of the structure is specifically adjusted (See Figure 3).
The challenge developing this splicing system is to ensure the proper knitting process, which must not be interrupted or disturbed during pile yarn change. On the one hand, the connection of different pile yarns must take place within a few seconds without yarn breakage. On the other hand, the change between the pile yarns must be coordinated in such a way that the correct pile yarn is used at the correct position in the knitted fabric. For example, the stiffer or puffier pile yarn should be used at the location of the local reinforcement. The yarn infeed quantity and pattern must also be matched to each other. Therefore, a communication between the splicing unit and the knitting machine is necessary.
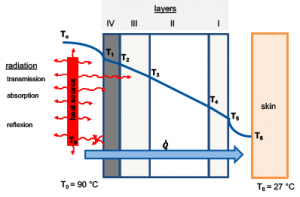
Approaches
The basic concept chosen is a four-layer structure consisting of a spacer fabric, a latent heat accumulator and a reflective layer. An exemplary concept is shown in Figure 4, where the spacer fabric is used within the layers I and II, the latent heat accumulator is layer III and layer IV is used as a reflective layer.
Layer I must transport water absorbed by the body, sweat, to the outside (high diffusibility) without absorbing water itself or conducting too much heat to the skin (low heat conductivity). Here, there is a conflict of objectives between a high contact surface textile/skin — better moisture removal, but also higher heat conduction — and a lower contact surface — better insulation effect, but lower moisture absorption. Layer II must have a large cross-section and an open mesh structure for good ventilation and diffusion properties. In addition, the high resilience of the spacer fabric reliably suppresses contact between layer II and the skin. Layer III provides shielding of layers I and II from the heat radiation of the heat source via a low degree of transmission and a high degree of reflection. Also, a latent heat accumulator based on a phase-change material (PCM) can be installed in layer III to compensate the heat input into the deeper layers I and II. Layer IV is an additional reflective layer which reflects heat radiation and thus absorbs less heat overall. The optimum layer structure is determined using heat conduction simulation software. Only the optimum layer structure will be tested on a heat conducting test bench, using different types of spacer fabrics and investigate on the effect of different amounts of absorbed humidity on heat conductivity.
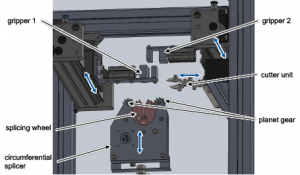
As possible process variants of splicing to change the pile thread in the process, bonding, welding and circumferential splicing are investigated. The most important parameters on the basis of which the decision for one of these processes is made are the spliceable material spectrum, the investment costs, the splice duration as well as the mechanical properties of the splice site. Since all processes have similar investment costs and the achievable mechanical properties differ only slightly, the focus when selecting a process is on the material spectrum that can be processed and the process time required for splicing. In contrast to adhesive bonding and welding, circumferential splicing can also be used to splice foreign materials together. In addition, there is a temporal advantage over gluing and welding in the case of downwind splicing due to the lack of curing and cooling times. In the further course of the project, therefore, circumferential splicing is favoured. Within the scope of this project a circumferential splicing unit was designed and constructed (See Figure 5).
The splicer unit consists of the circumferential splicer itself, two grippers and a cutter unit. The circumferential splicer is driven by a gearwheel and synchronized by planet gears for defined positioning of the splicing wheel. This is necessary to ensure the gap of the splicing wheel is at the top when the pile yarns are inserted. The pile yarns are moved by the grippers, while the insertion of the pile yarn is achieved by moving the splicer up. After splicing the yarn is cut off by the cutter unit and the splicer is moved down again.
Conclusion
As part of the HEATex research project, a functionalized, 3D undergarment is being developed that can be worn under conventional protective clothing at workstations exposed to heat. The protective clothing consists of a four-layer structure, with each layer performing a separate function. Layers I and II are spacer fabrics. The protective effect of this spacer fabric is based on the one hand on the avoidance of skin contact with the layers of protective clothing lying above it, in order to prevent scalding caused by one’s own body sweat. On the other hand, a cooling effect is created by moisture removal. Both effects are achieved using a spacer fabric which has locally different spacer stiffness. The spacing stiffness is achieved using pile yarns of different stiffness, which can be changed flexibly during the process. The flexible changing of the pile yarns is carried out via a circumferential splicer module, with which also pile yarns of other types can be connected in a few seconds. In addition to the spacer fabric of layers I and II, a lateral heat accumulator is installed in layer III, which prevents and delays the heat input into layers I and II. Layer III as well as layer IV are additionally reflective layers which can reflect the heat radiation.
References
[Ate15]
Atemschutzunfälle:
URL: http://www.atemschutzunfaelle.de/unfaelle/eu/
Zugriff am 01.09.2015
[KSC+07]
Kales, S. N.; Soteriades, E. S.; Christophi, C. A., Christiani, D. C.:
Emergency Duties and Deaths from Heart Disease among Firefighters in the
United States
The New England Journal of Medicine, Vol. 356, no. 12; 22. März 2007
[NN15]
NN:
Unfallstatistik der Feuerwehr-Unfallkassen FUK Mitte und HFUK Nord
Der Sicherheitsbrief, 37, H.1/2015, S. 6-8
[TÜV16]
TÜV Rheinland:
Hitze-Check am Arbeitsplatz H.E.A.T Analyse – Objective Klimamessung nach DIN EN
27243 und Beurteilung der Hitzebelastung am Arbeitsplatz
URL: http://www.presseportal.de/pm/31385/2279470
Zugriff am 24.11.2016
Editor’s Note: Lukas Lechthaler, Christoph Peiner, Marie-Isabel Popzyk, Thomas Gries are based at the Institut für Textiltechnik of RWTH Aachen University, Aachen, Germany. The research project is funded by the German Federal Ministry of Economics and Energy (BMWi) within the framework of the Central Innovation Programme for SMEs (ZIM) on the basis of a resolution of the German Bundestag. Within the framework of this project, the ITA thanks its research partner STS Textiles GmbH, Grünbach, for their constructive cooperation.
December 14, 2018