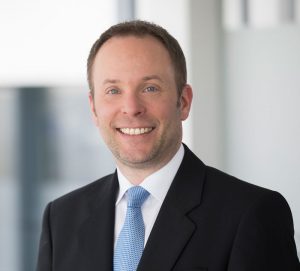
TW Special Report
Digitization is more important than ever. As more designers work online and our industry strives to reduce waste and save resources 3D technologies for technical prototyping promise great benefits. While the designs are digital, most apparel is still designed for real people, not avatars. So, realistic visualization is important for designers, manufacturers and consumers.
Digital material parameters are an often-undervalued pillar of 3D design. Brands are building digital material libraries, increasing the incentive for suppliers to offer digitized materials. But, suppliers want their materials represented realistically across all 3D platforms.
To help both suppliers and designers, textile testing and research partner Hohenstein created the Universal Translator Approach for digital material parameters. Dr. Virgilio L. González, correspondent for Textile World‘s sister publication Textiles Panamericanos, recently had the opportunity to interview Dr. Jan Beringer, Hohenstein’s senior scientific expert.
González: What exactly are digital materials and why are they important?
Beringer: Material parameters are measurements of the physical textile (or accessory) that are needed by a software system to make a digital simulation. These can include elasticity, mass, density, stiffness, friction, strain strength and many more. The program’s algorithm turns this data into a 3D object on your screen that is meant to be a digital twin of the material. Ideally, it should look and behave the same as the real material. This accuracy affects not only the appearance, but also the fit, comfort, quality and manufacturing process of the garment. You need to know how a material will behave on a body or interact with other materials, especially if the wearer is planning to move.
González: What is the current state of digital materials?
Beringer: The lack of standardization around digitizing materials is a real challenge to our industry.
To digitize a material for the most popular 3D simulation systems, material suppliers or digital designers must test many distinct parameters for each fabric. Each software has its own requirements for what and how to test. Even the required units differ. For example, the bending parameter is entered as ‘µNm’ for one system, ‘Bend W/L (𝒅𝒚𝒏/𝐜𝐦²)’, for another and ‘Bending weft/warp ((g∗mm²)/(s^2∗rad))’ for a third system.
The problem for material suppliers is that their brand customers may be using different 3D systems. Not only is it unrealistic to test for up to 35 parameters on each material, after following the various test procedures for each, differences in the algorithms result in different visualization and behavior across platforms. And suppliers want their materials represented accurately in every 3D system, wouldn’t you?
It’s no wonder that designers have resigned to using default material libraries or buying parameters from sources that differ in accuracy and methods. Worse, these materials don’t match the current collection.
González: What is the problem with default or inaccurate material parameters?
Beringer: Imagine a designer using different materials in the physical design and prototyping stages than they plan for the finished garment. Everyone knows this does not work for traditional designing. So, why would it work for digital designing?
Digital materials have impacts beyond development, to the physical products that customers buy. Unrealistic designs affect manufacturing, where clear communication and material accuracy are important for production efficiency, repeatability and profitability. Designing with imprecise digital materials can reduce product quality, lowering consumer satisfaction, increasing return rates and hurting the bottom line — not to mention the negative impact on a brand sustainability strategy.
González: How did Hohenstein get involved with this area?
Beringer: Hohenstein garment engineers have conducted applied research and size studies for over 60 years. We’ve always studied new technologies as they develop, such as 3D and 4D scanning, fit in motion and avatars. The Hohenstein Digital Fitting Lab takes the essential knowledge of traditional fitting and helps partners adopt the new 3D technologies.
Given the importance of accurate materials, we wanted to remove the barriers for brands and suppliers. In an extensive research project, we examined the major 3D systems in terms of requirements, formats, units and simulation outcomes. We narrowed it down to five essential parameters with standard test methods: weight, thickness, bending, elongation and fold volume and shape. Then, we developed the Hohenstein Universal Translator Approach, a conversion that assures consistent visualization and behavior across all major 3D platforms.
González: How does the Hohenstein Universal Translator Approach help the industry?
Beringer: First, we reduce time and cost. Only five standard tests are required per material, down from more than 30. We export the data in the file formats required by each software. We can also generate drape images and create physical swatch books with matching digital parameters. It’s straight forward and designer friendly.
With accurate test results and the Hohenstein conversion, the materials match reality, no matter which software is used. Suppliers guarantee that their materials are correctly represented, regardless of the platform used by the designer — ensuring reproducible designs. Designers can access digital materials that correspond to their current collections. Manufacturers receive clear instructions. Finally, consumers get products that match the image they saw online.
González: What other digitization challenges does the industry face?
Beringer: There is no industry standard for material digitization. A standard will allow more businesses to adopt the technology without reducing quality and efficiency and at the same time becoming more sustainable. In fact, Hohenstein is part of an ISO standard working group to develop one. Despite delays with the Covid-19 pandemic, we hope to make an announcement by 2022.
Training is also important. Anyone can purchase 3D software, but you must learn how to use it. Software does not eliminate the need for fitting and pattern-making skills. The Hohenstein Academy offers training on digital and physical garment engineering.
González: What is your next development for improving 3D visualization and technical fit prototyping?
Beringer: We are focusing on next generation avatars — with accurate shapes and movements (rigging). We need accurate simulations of how clothes would fit and move in real life – something that hasn’t been done before. Garments must be created for actual humans in motion, while most default avatars look more like stiff aliens. We are continuing to develop realistic avatars based on sizing surveys and research. We’re also working on rigged avatars that realistically perform movements like walking and raising arms. Realistic avatars, along with high quality digital patterns and materials, are crucial to successful adoption in our industry.
September 23, 2021