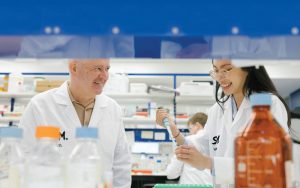
Scaling Samsara Eco’s technology enables infinite recycling without quality degradation and eliminates the need for creating new plastics from fossil fuels.
TW Special Report
Recycling textiles and plastic waste has been top-of-mind among many leaders in the textile industry under the guise of sustainability for some time now.
Thought leaders have led the charge, conferences have been held, and no shortage of articles have been written on this very hot topic. And in time, real investments, innovations, and products have come to market. But there is still much work to be done to achieve a serious level of circularity in the textile industry.
Mixed waste often consists of various plastics, contaminants, dyes and other components presenting a conventional recycling nightmare that necessitates sorting and often some degree of cleaning prior to further processing.
There is something to be said for a more efficient recycling process but regrettably, meeting the challenge is no simple task.
Enter Samsara Eco
Founded in 2021, Australia-based Samsara Eco has made strides in mixed waste recycling with a continuous enzymatic approach that alleviates waste sorting, breaks both polyester and nylon 6,6 waste down to their respective monomer building blocks, and doesn’t gobble up a lot of energy in the process.
By engineering plastic degrading enzymes that can break down plastics to their most basic building blocks —from polymers to monomers — the Samsara platform streamlines the mixed waste recycling process.
The very definition of samsara is the “cyclicity of all life, matter, and existence.”
A Breakthrough
As Ph.D. students at the Australian National University (ANU), Matthew Spence and Vanessa Vongsouthi focused on engineering plastic-degrading enzymes. Their work formed the foundation of Samsara Eco’s infinite plastic recycling technology platform.
Paul Riley, who saw the technology’s potential, founded Samsara Eco to address global plastic pollution and put his 30 years of experience in venture capital and private equity business development to work. Commercializing Co-Founders Spence and Vongsouthi’s research would allow for infinite recycling without quality degradation and eliminate the need for creating new plastics from fossil fuels or plants.
Samsara Eco was launched with the backing of Main Sequence —Australia’s “deep tech” investment fund — and Woolworths Group, and in partnership with ANU, all drawn to Samsara’s mission to “decouple fossil fuels from plastics manufacturing, by delivering new plastics comprised of 100-percent recycled material — with no virgin plastics supplementation needed.”
Riley, founder and CEO of Samsara Eco, explained: “I had been searching for a solution to the plastic crisis for nearly a year when a serendipitous moment led me to the research at ANU. The moment I saw it, I knew it could change everything. It had the potential to tackle both the waste and carbon problems associated with plastics.
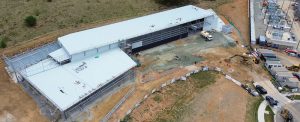
“As we’ve scaled the technology and run trials with brands and partners, we’ve witnessed how this potential can become a reality. And, while there’s still a long way to go in solving the plastic crisis, our progress over the past four years — advancing the ability to recycle even the most challenging plastics, including mixed plastics and textile blends — offers real hope for a fossil-fuel, waste-free future.”
The Basics
Samsara’s enzyme platform has broad capabilities that can depolymerize polyethylene terephthalate (PET) and polyester plastics; nylon 6,6, including dyed and spandex blended textiles; and hard-to-recycle plastics.
EosEco™ Technology
Moving the technology forward, the Samsara team created the brand EosEco™ to signify its patented recycling technology and the combination of biophysics, chemistry, biology, and computer science, including AI, used in creating its plastic-eating enzymes.
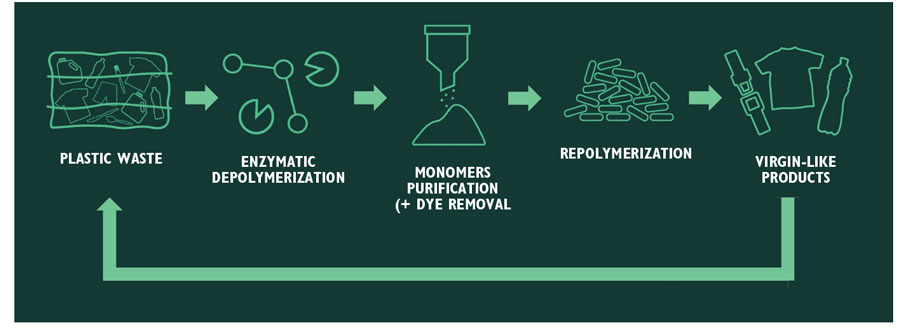
More Than Bench Chemistry
The Samsara Eco team has taken scaling enzymatic recycling seriously from the get-go.
Starting with a lab scale model in 2021, it created a pilot line in 2022 followed by a prototype of two batch lines — for polyester and nylon 6,6 — in 2023 and 2024 respectively.
Two, larger scale commercial proof of concept R&D lines will come online during 2025, and the team has sights set on delivering a 20-kiloton commercial plant in 2027.
“Textile-to-textile recycling is becoming increasingly important as minimum recycled content mandates and extender producer responsibility regulations come into force in the EU and elsewhere around the world,” said Samsara Eco Chief Commercial Officer and COO Sarah Cook.
“Brands are having to rethink their entire global supply chains with these regulations in mind, and it’s placing a greater need for solutions like ours.
“We help brands take control of the entire lifecycle of their products, while also helping reduce scope emissions. That’s a really appealing proposition for companies,” Cook added.
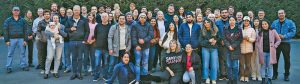
The Nylon Difference
Regarding the company’s ability to recycle nylon 6,6 and its recently announced enzyme capable of recycling nylon 6, Cook said: “There are really limited solutions for recycling nylon so our ability to recycle nylon 6,6, nylon 6 and polyester is a significant advantage. The broader industry’s recent focus tends to be on recycling pure polyester textiles largely because polyester accounts for approximately 57 percent of global fiber production.
However, for a huge segment of the market, particularly sports and outdoor wear, athleisure, intimates, hosiery and even automotives, nylon is widely used, and they need a solve to handle their waste and excess. We are uniquely positioned to help them fill this gap.
“We are working with a range of potential feedstock partners including the brands, mills, existing collectors and other potential sources within the nylon 6,6 supply chain,” Cook continued. “The feedstock will be both post-industrial and post-consumer waste that will go through our enzymatic recycling technology.”
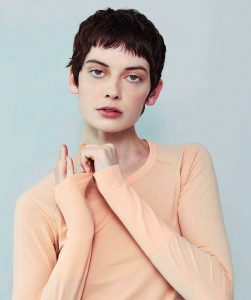
Collaboration Is Key
Developing a process from bench chemistry to a full-blown plant is one thing, but developing industry partnerships and gaining acceptance takes significant effort as well.
In February 2024 Vancouver, British Columbia-based brand lululemon announced: “Using recycled nylon 6,6 made with Samsara Eco’s technology, lululemon has created samples of its iconic Swiftly Tech Long-Sleeve Top, representing the first time this type of nylon has been recycled in this way.”
Riley said at the time: “Our work with lululemon represents a ground-breaking step forward in tackling the challenge of textile waste and demonstrates the potential to create a fully circular ecosystem for apparel.
“We’ve started with nylon 6,6, but this sets the trajectory of what’s possible for recycling across a range of industries as we continue expanding our library of plastic-eating enzymes.This is an incredibly significant moment for the future of sustainable fashion and circularity.”
lululemon also noted that, “This milestone in lululemon’s multi-year collaboration with Samsara Eco is one way lululemon is advancing its goal to make 100 percent of products with preferred materials and end of use solutions by 2030.”
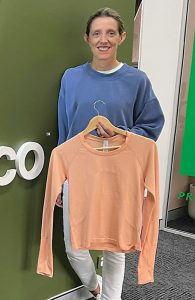
NILIT MoU
In August 2024, Samsara signed a memorandum of understanding (MoU) for apparel with Israel-based nylon 6,6 producer NILIT. Regarding the MoU, Ilana Melamed, NILIT general manager, explained: “NILIT’s partnership with Samsara Eco is a critical step in our multi-pronged strategy to provide the apparel market with premium nylon 6,6 products that have lower environmental impact.
“Implementing textile-to-textile recycling solutions will substantially decrease global carbon emissions and reduce the 92 million tons of textile waste added to landfills annually. Together, NILIT and Samsara Eco have the potential to produce infinitely recycled nylon 6,6 that delivers outstanding fabric quality and performance while benefiting the planet.”
Industry Recognition
In September 2024, Samsara Eco received an “ITMF Sustainability & Innovation Award” presented by the Zurich-based International Textile Manufacturers Federation (ITMF) at its annual conference held in Samarkand, Uzbekistan.
ITMF Awards recognize outstanding achievements by actors in the global textile industry in two categories — Sustainability & Innovation and International Cooperation. According to ITMF, these awards highlight the textile industry’s commitment to sustainability and global cooperation, showcasing innovation and collaborative efforts that are driving progress towards a more sustainable future.
The ITMF Sustainability & Innovation Award was presented in honor of Samsara’s development described as, “Endless Plastic Recycling: A Solution for Textiles Out of Use.”
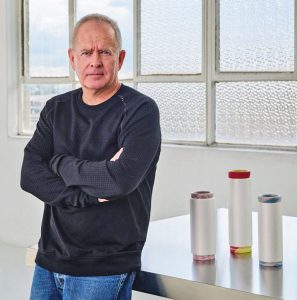
Investing In The Future
In June 2024, Samsara Eco raised $100 million Australian dollars ($65 million) in a Series A+ funding round. According to ESG Today — a website dedicated to covering environmental, social and governance (ESG) issues for investors — the funding was led by Temasek and Main Sequence, with participation from investors including Wollemi Capital, lululemon, Hitachi Ventures, Titanium Ventures and DCVC.
It has also been reported that the funding will be used for facilities across Southeast Asia.
Regarding the investment, Cook stated: “Our latest funding will facilitate the development of two major recycling facilities — one for nylon and another for polyester. We expect these facilities to commence commercial operations during 2027 and will be established as joint ventures with leading plastic polymerization companies.”
Building Towards A Sustainable Future
Vongsouthi serves as head of Science Operations & Research founder and is focused on optimization of the company’s enzymes. She has often stated: “All the plastic we’ll ever need has already been produced. With infinite plastic recycling, we can view waste as a valuable resource and put a ‘full stop’ to the production of virgin plastic from fossil fuels.”
Accomplishing the company’s mission to divert plastic from landfills and oceans while creating a truly circular economy for plastics has become more than Riley’s vision for Samsara Eco — it’s reality.
2025 Quarterly Issue I