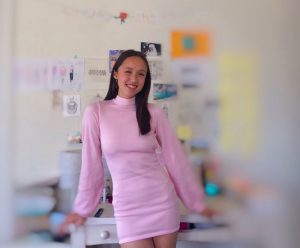
BELMONT, N.C. — April 30, 2021 — In 2019, Lauren Choi, then an innovative senior majoring in Material Science and Engineering at Johns Hopkins University, was sent a Los Angeles Times article by her mom about China banning imported U.S. recyclables. The article described how plastics shipped abroad could not be recycled because they are dyed, contaminated, or mixed with other non-recyclable waste.
Distraught to see no compulsory bilateral environmental agreements between the two countries, the story made a profound impact on Choi. She started a project, The New Norm, to find a way to use plastic waste to produce sustainably made textiles that would not harm the environment.
“At an early age, I had a strong interest and desire to work with sustainable products that would not damage but protect our planet,” Choi said. “While in college my interest focused on creating sustainable textiles for the fashion industry. After reading this article, I saw it as an opportunity to step up and do something.”
Choi began The New Norm’s search for a plastic product that was easily accessible and inexpensive. She selected red Solo cups, a popular brand of cups used at parties, picnics and many social gatherings. The cups are made of polystyrene (#6 plastic). It is estimated that the approximately 7.4 billion Solo cups, lids and containers that are produced each year end up in landfills or oceans.
“Over time, I received grants and other funding to build a small extruder in my garage that enabled me to test the concept,” said Choi. “The long-term goal is to operate as a B2B wholesale fabric company, targeting higher-end womenswear brands, but I needed to first produce fiber and clothing on a larger scale.”
To inquire about blending the Solo cups into a suitable fiber-grade polymer, Choi contacted Gaston College’s Textile Technology Center (TTC) and the Catawba Valley Community College Manufacturing Solutions Center (MSC). Together, they worked with The Polymer Center of Excellence, a polymer lab in Charlotte, N.C., to conduct testing and determine the polymer blending and pellet extrusion process. Through this network of polymer engineers and textile specialists, Choi got in contact with Dart Container, the makers of Solo cups, and is now working in collaborative efforts with its recycling initiative.
In 2020, the TTC and the MSC formed a partnership creating the Manufacturing & Textile Innovation Network (MTIN), to work together to develop a regional workforce focused on advanced materials and textile testing development.
“When Lauren initially reached out to the Textile Technology Center for assistance with her research, I was extremely excited to help,” said Jasmine Cox, process coordinator at the TTC at Gaston College. “Sustainability is such an important concept that directly impacts the textile and apparel industry. Being able to transform a common household item like a Solo cup into a garment is amazing. I knew that the TTC and partner organizations would be able to help The New Norm produce a great product,” Cox said.
The process included grinding recycled Solo cups into a pellet size suitable for the melt extrusion. Then the polymer pellets were melted through a combination of applied heat and friction, after which the molten polymer was forced under pressure through a small “shower head” opening, called a spinneret, on the TTC One Shot Extruder. This produced a prototype filament. The TTC Physical Testing laboratory then ran initial tensile, or tension, tests to determine ultimate strength and durability of a product.
Watching every stage of the testing process, Choi learned it was necessary to start small and work her way up to achieve successful fiber blends that could be turned into yarn and then a knit and woven fabric samples.
“Both the TTC and MSC have introduced me to experts in the industry,” Choi said. “I’m very grateful for this pool of advisors who helped me while working on this project. You need to seek advice and listen so that you can make the proper decisions. Stay on your feet but be flexible to change. Don’t give up and keep going.”
“These centers are wonderful tight knit facilities with good one-on-one communication,” Choi continued. “They were able to do multiple fiber tests and stay on budget until they could extrude a yarn successfully. You can’t create something so unique without building a relationship of trust. I don’t believe we would have accomplished these projects in the same timeline otherwise.”
Although Choi graduated from Johns Hopkins in 2020, she elected to pursue The New Norm for a year to continue with the project. “Everything we’ve done so far would not have been possible without both centers. I’ve personally learned so much and as I look back to see what we’ve achieved in one year, I know we wouldn’t be here if it wasn’t for the centers,” said Choi.
Posted April 29, 2021
Source: Gaston College Textile Technology Center